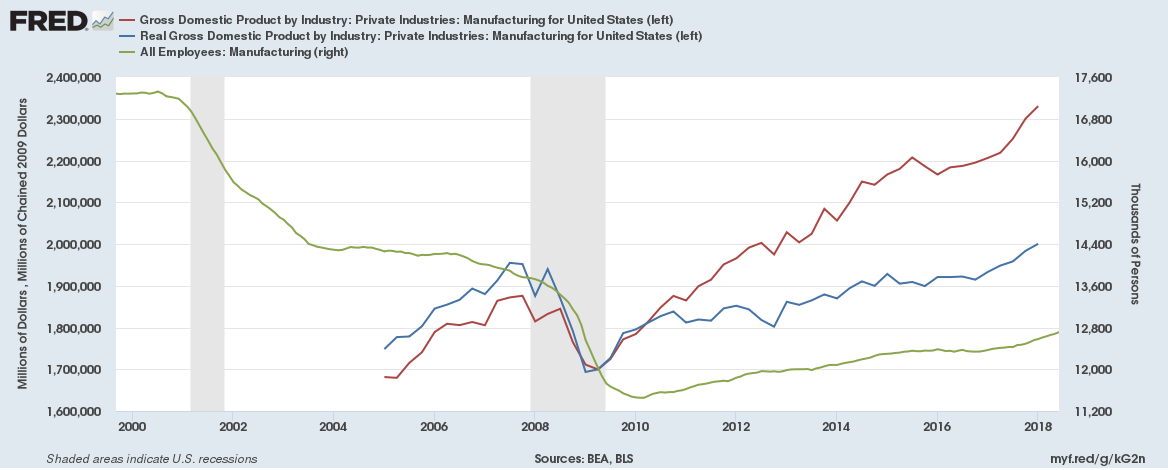
A director in manufacturing is responsible to manage the company's production processes. They are responsible for overseeing all aspects of manufacturing, from design through to production. This role requires a lot of experience in manufacturing, as well as a good knowledge of new technologies. Some examples of such technologies include robotics and 3D printing. A director who keeps up with these technologies is an asset to his company. As the manufacturing sector continues to develop, the director will find his or her role more complicated as he/she must coordinate with both engineering and operations. Quality control will also be a key focus.
Director of manufacturing salary
A Director of Manufacturing's salary can vary greatly, depending on the region they work in. Many directors get a salary in the low six figures, but some earn more than others. A Director of Manufacturing's salary can vary depending on education and years of experience. These are the factors that will impact how much you can earn in your particular area.
The salary for a director of manufacturing varies but it's generally higher if you have more work experience. The cost of living and the location can also impact salary. If you live in a big city, expect to earn higher salaries, but be aware that your salary may not match the cost of living. When the opportunity presents itself, it is important to be open to negotiations to obtain a higher wage.
A Director in Manufacturing Operations earns between $181,000.500 and $66,000 per year. The salary for a director of manufacturing operations is variable. It can vary up to 8% from one city to the next. Fremont's director of manufacturing operations can make between $128,493 - $164,500. This salary is much higher than the national median. However, salaries for Director of Manufacturing Operations vary depending on location, experience, and company.
Education necessary
Director of manufacturing is responsible to manage a manufacturing facility and supervise the production process. Some of the duties of this position include hiring new employees, overseeing quality assurance, collaborating with designers, and meeting operations standards. The director of manufacturing reports to the senior management team. They execute policy and sales initiatives. Candidates must have some manufacturing experience and be able communicate well. There are different educational requirements to become a director in manufacturing.
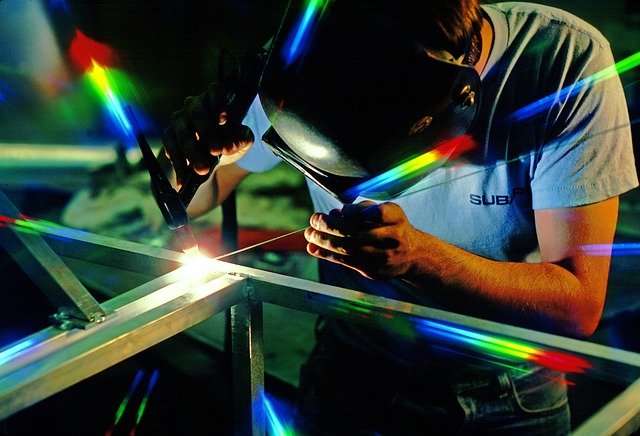
A graduate degree in engineering may not be required to become a director of manufacturing, but a post-secondary education will enhance your skills and knowledge. This position is well-suited for candidates who are interested in learning about business, management and economics. Ultimately, you will be responsible for managing a diverse group of people.
You will be working closely with engineers and designers during product development. This stage is where you will evaluate new manufacturing processes and ensure high quality standards. As well as overseeing production, directors can also serve as coaches to employees. They mentor their employees in risk mitigation and best practices. A manufacturing director must not only oversee the production process but also be able to solve problems.
Experience required
For this position, a bachelor's Degree in a relevant subject and 5-10 years of progressive experience are usually required. Generally, manufacturing companies prefer to hire internal employees for this role. The ideal candidate will have a thorough understanding of the manufacturing process and business objectives. However, a graduate degree may also be desired by some employers. In addition to these requirements, candidates may have additional training in their chosen field or industry.
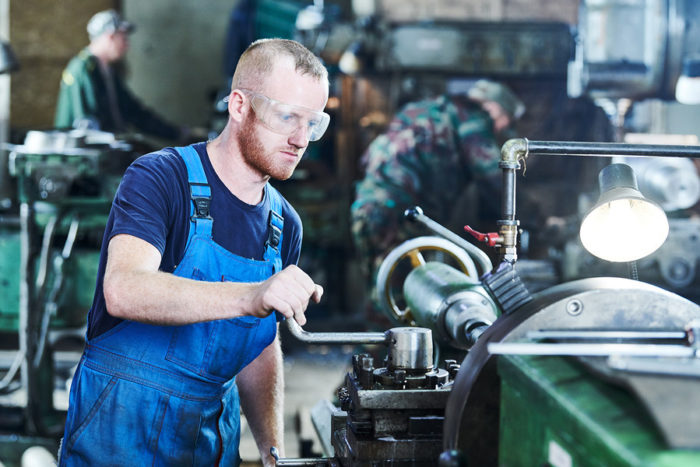
A director of manufacturing oversees the production process, including engineers, supervisors, and workers. They may be responsible for solving problems and developing a solution for them. A director of manufacturing may not only oversee production but also develop and implement quality-control programs. Directly reports to the top management of the manufacturing organization, the director of manufacturing. Manufacturing experience is a must. This position can be made more successful if you have experience in manufacturing management.
Experience as a manufacturing director will be an asset. Directors should have at least 10 years' experience in a manufacturing setting. They might have begun their careers as technicians or manufacturing supervisors. Strong communication skills are also required. The director of manufacturing must also be able to understand business strategy. A director of Manufacturing must also be able to communicate effectively with other departments. As such, the director is responsible for overseeing the production process and ensuring that it meets all quality standards.
FAQ
What are the responsibilities of a logistic manager?
A logistics manager makes sure that all goods are delivered on-time and in good condition. This is done through his/her expertise and knowledge about the company's product range. He/she should make sure that enough stock is on hand to meet the demands.
What does warehouse mean?
A warehouse is a place where goods are stored until they are sold. You can have it indoors or outdoors. Sometimes, it can be both an indoor and outdoor space.
Why automate your factory?
Automation has become increasingly important in modern warehousing. E-commerce has increased the demand for quicker delivery times and more efficient processes.
Warehouses need to adapt quickly to meet changing needs. To do so, they must invest heavily in technology. Automation warehouses can bring many benefits. These are some of the benefits that automation can bring to warehouses:
-
Increases throughput/productivity
-
Reduces errors
-
Improves accuracy
-
Boosts safety
-
Eliminates bottlenecks
-
Allows companies scale more easily
-
Workers are more productive
-
It gives visibility to everything that happens inside the warehouse
-
Enhances customer experience
-
Improves employee satisfaction
-
This reduces downtime while increasing uptime
-
Quality products delivered on time
-
Eliminates human error
-
Helps ensure compliance with regulations
What does it take to run a logistics business?
To run a successful logistics company, you need a lot knowledge and skills. Effective communication skills are necessary to work with suppliers and clients. It is important to be able to analyse data and draw conclusions. You will need to be able handle pressure well and work in stressful situations. To increase efficiency and creativity, you need to be creative. You need to have strong leadership qualities to motivate team members and direct them towards achieving organizational goals.
It is important to be organized and efficient in order to meet tight deadlines.
What is the importance of automation in manufacturing?
Automating is not just important for manufacturers, but also for service providers. It allows them provide faster and more efficient services. They can also reduce their costs by reducing human error and improving productivity.
What types of jobs can you find in logistics
Logistics can offer many different jobs. Here are some examples:
-
Warehouse workers – They load and unload pallets and trucks.
-
Transportation drivers – They drive trucks or trailers to transport goods and perform pick-ups.
-
Freight handlers: They sort and package freight in warehouses.
-
Inventory managers – They manage the inventory in warehouses.
-
Sales representatives - They sell products to customers.
-
Logistics coordinators are responsible for organizing and planning logistics operations.
-
Purchasing agents are those who purchase goods and services for the company.
-
Customer service representatives - They answer calls and emails from customers.
-
Shipping clerks - They process shipping orders and issue bills.
-
Order fillers: They fill orders based off what has been ordered and shipped.
-
Quality control inspectors – They inspect incoming and outgoing products to ensure that there are no defects.
-
Others - There are many other types of jobs available in logistics, such as transportation supervisors, cargo specialists, etc.
Statistics
- According to the United Nations Industrial Development Organization (UNIDO), China is the top manufacturer worldwide by 2019 output, producing 28.7% of the total global manufacturing output, followed by the United States, Japan, Germany, and India.[52][53] (en.wikipedia.org)
- It's estimated that 10.8% of the U.S. GDP in 2020 was contributed to manufacturing. (investopedia.com)
- Job #1 is delivering the ordered product according to specifications: color, size, brand, and quantity. (netsuite.com)
- In 2021, an estimated 12.1 million Americans work in the manufacturing sector.6 (investopedia.com)
- [54][55] These are the top 50 countries by the total value of manufacturing output in US dollars for its noted year according to World Bank.[56] (en.wikipedia.org)
External Links
How To
How to Use Six Sigma in Manufacturing
Six Sigma is "the application statistical process control (SPC), techniques for continuous improvement." Motorola's Quality Improvement Department developed it at their Tokyo plant in Japan in 1986. Six Sigma is a method to improve quality through standardization and elimination of defects. Many companies have adopted Six Sigma in recent years because they believe that there are no perfect products and services. Six Sigma's primary goal is to reduce variation from the average value of production. This means that if you take a sample of your product, then measure its performance against the average, you can find out what percentage of the time the process deviates from the norm. If the deviation is excessive, it's likely that something needs to be fixed.
Understanding how your business' variability is a key step towards Six Sigma implementation is the first. Once you have a good understanding of the basics, you can identify potential sources of variation. This will allow you to decide if these variations are random and systematic. Random variations occur when people do mistakes. Symmetrical variations are caused due to factors beyond the process. These are, for instance, random variations that occur when widgets are made and some fall off the production line. You might notice that your widgets always fall apart at the same place every time you put them together.
Once you identify the problem areas, it is time to create solutions. This could mean changing your approach or redesigning the entire process. Once you have implemented the changes, it is important to test them again to ensure they work. If they fail, you can go back to the drawing board to come up with a different plan.