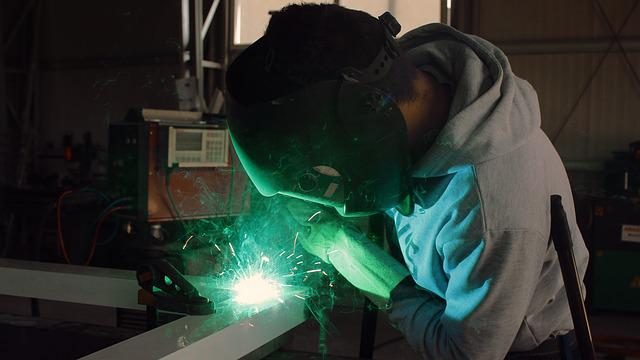
General managers have the responsibility of developing strategy, identifying and hiring functional leaders, as well as communicating with company stakeholders. This article covers the skills and responsibilities required to succeed in this role. You can read the following to get a comprehensive overview of general manager duties. Strong communication skills and presentation skills are key to being a successful manager. You must also be proficient in financial management. Ultimately, your success depends on your persistence and ability to manage your company's performance and processes within a budget. To succeed in this role, you must be an excellent team leader and able to build trust with customers and suppliers.
Strategy formulation is the responsibility and responsibility of GMs
While strategy formulation is a key responsibility of GMs, it can also be fraught with risks. A GM who is motivated or a member a a leadership team could overplay their role. This is because managers are subjected to their own motivations and biases. They may make decisions based on personal interpretations and assumptions, rather than objective data.
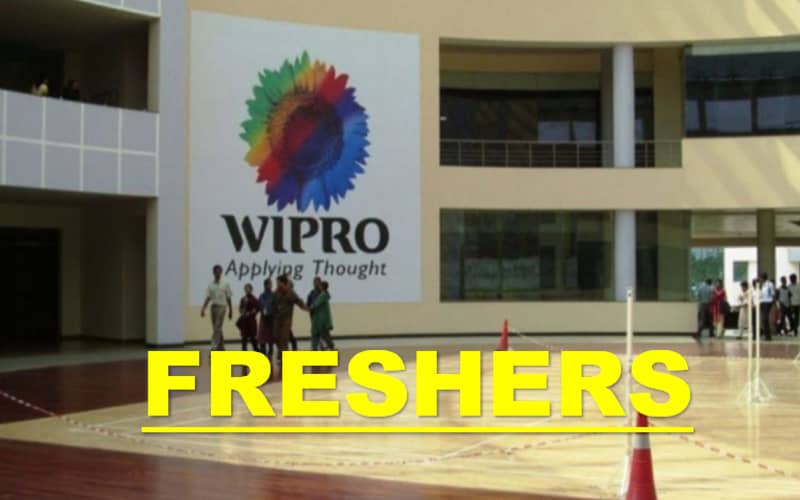
They recruit functional leaders
General managers are responsible for all aspects of the organization and its business units. They have to manage the entire business from strategy to structure to budgets and people. They are also responsible to manage the daily operations and coordinate key performance indicators for all business units. They must be fluent in finance, sales and human resource management to effectively execute the strategy. The general manager role is complex, as it involves ensuring the success and growth of the entire organization.
They work closely alongside their subordinates
A general manager's job requires them to understand the internal workings of the organization and communicate with all the departments. They need to be analytically able to spot problems and provide solutions. The role of the general manager is to manage tasks and ensure employees do their best. It is also important for general managers to communicate clearly with subordinates and work in close collaboration with other departments.
They communicate with each other
Communication skills are crucial in many general manager roles. By hosting training sessions and coaching employees in effective communication skills, general managers can learn to listen to employees' concerns. You can host more team meetings and social events in order to encourage greater communication. Here are some tips to improve manager communication skills. Every manager should be available to their employees in order to make them successful. This is a crucial part of their job description. They should also be available to answer questions and provide guidance when necessary.
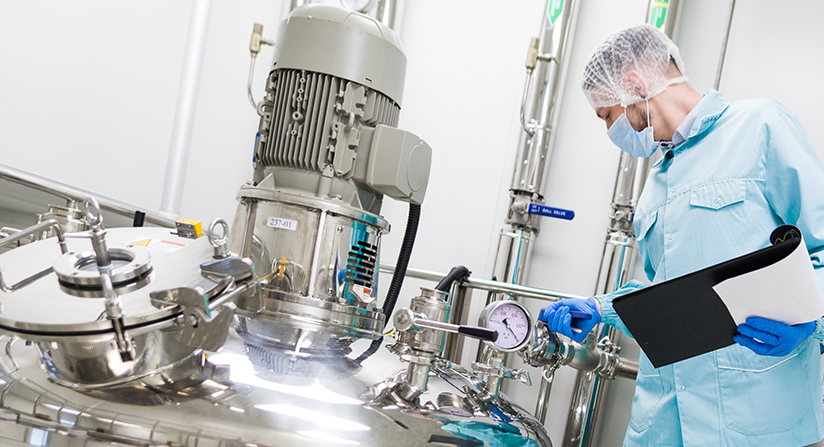
They motivate
The best GMs are able to motivate their staff. They are willing, able and able work hard for the business. They also demonstrate their high standards in small ways. Here are some examples of how top managers motivate staff.
FAQ
What is production planning?
Production Planning refers to the development of a plan for every aspect of production. This document is designed to make sure everything is ready for when you're ready to shoot. This document should include information about how to achieve the best results on-set. This includes information on shooting times, locations, cast lists and crew details.
The first step is to decide what you want. You may have already chosen the location you want, or there are locations or sets you prefer. Once you have identified the scenes and locations, you can start to determine which elements are required for each scene. If you decide you need a car and don't know what model to choose, this could be an example. You could look online for cars to see what options are available, and then narrow down your choices by selecting between different makes or models.
After you have chosen the right car, you will be able to begin thinking about accessories. What about additional seating? Or maybe you just need someone to push the car around. You might want to change your interior color from black and white. These questions will help determine the look and feel you want for your car. The type of shots that you are looking for is another thing to consider. What type of shots will you choose? Maybe you want the engine or the steering wheels to be shown. These factors will help you determine which car style you want to film.
Once you have determined all of the above, you can move on to creating a schedule. You can create a schedule that will outline when you must start and finish your shoots. Each day will include the time when you need to arrive at the location, when you need to leave and when you need to return home. It will help everyone know exactly what they have to do and when. If you need to hire extra staff, you can make sure you book them in advance. You should not hire anyone who doesn't show up because of your inaction.
It is important to calculate the amount of filming days when you are creating your schedule. Some projects are quick and easy, while others take weeks. When creating your schedule, be aware of whether you need more shots per day. Multiplying takes in the same area will result both in increased costs and a longer time. If you are unsure if you need multiple takes, it is better to err on the side of caution and shoot fewer takes rather than risk wasting money.
Budget setting is an important part of production planning. You will be able to manage your resources if you have a realistic budget. If you have to reduce your budget due to unexpected circumstances, you can always lower it later. However, it is important not to overestimate the amount that you will spend. If you underestimate the cost of something, you will have less money left after paying for other items.
Planning production is a tedious process. Once you have a good understanding of how everything works together, planning future projects becomes easy.
How is a production manager different from a producer planner?
A production planner is more involved in the planning phase of the project than a project manger.
What does it take to run a logistics business?
You need to have a lot of knowledge and skills to manage a successful logistic business. You must have good communication skills to interact effectively with your clients and suppliers. It is important to be able to analyse data and draw conclusions. You must be able and able to handle stress situations and work under pressure. You must be creative and innovative to develop new ideas to improve efficiency. Strong leadership qualities are essential to motivate your team and help them achieve their organizational goals.
To meet tight deadlines, you must also be efficient and organized.
What skills are required to be a production manager?
Being a production planner is not easy. You need to be organized and flexible. It is also important to be able communicate with colleagues and clients.
Statistics
- In 2021, an estimated 12.1 million Americans work in the manufacturing sector.6 (investopedia.com)
- In the United States, for example, manufacturing makes up 15% of the economic output. (twi-global.com)
- (2:04) MTO is a production technique wherein products are customized according to customer specifications, and production only starts after an order is received. (oracle.com)
- According to a Statista study, U.S. businesses spent $1.63 trillion on logistics in 2019, moving goods from origin to end user through various supply chain network segments. (netsuite.com)
- [54][55] These are the top 50 countries by the total value of manufacturing output in US dollars for its noted year according to World Bank.[56] (en.wikipedia.org)
External Links
How To
Six Sigma in Manufacturing
Six Sigma refers to "the application and control of statistical processes (SPC) techniques in order to achieve continuous improvement." Motorola's Quality Improvement Department created Six Sigma at their Tokyo plant, Japan in 1986. The basic idea behind Six Sigma is to improve quality by improving processes through standardization and eliminating defects. Many companies have adopted this method in recent years. They believe there is no such thing a perfect product or service. Six Sigma aims to reduce variation in the production's mean value. If you take a sample and compare it with the average, you will be able to determine how much of the production process is different from the norm. If this deviation is too big, you know something needs fixing.
Understanding the dynamics of variability within your business is the first step in Six Sigma. Once you understand this, you can then identify the causes of variation. Also, you will need to identify the sources of variation. Random variations are caused when people make mistakes. While systematic variations are caused outside of the process, they can occur. These are, for instance, random variations that occur when widgets are made and some fall off the production line. You might notice that your widgets always fall apart at the same place every time you put them together.
After identifying the problem areas, you will need to devise solutions. That solution might involve changing the way you do things or redesigning the process altogether. Once you have implemented the changes, it is important to test them again to ensure they work. If they don’t work, you’ll need to go back and rework the plan.