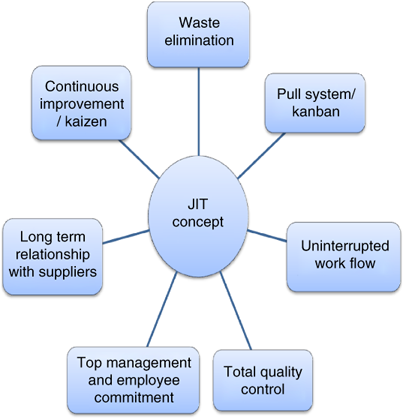
Japanese factories make high-quality products at affordable prices. They account for five percent of the country’s total GDP. However, they have struggled with tighter standards, growing competition and the cost pressures of the recent recession.
One example is the last-year government white paper that found Japanese firms unprepared for a cutoff in parts procurement. The recession had a devastating effect on the Japanese auto industry. The supply chain is a critical part of the car manufacturing business. It relies on approximately 30,000 parts. This can lead to production being stopped. Some parts don't have substitutes.
Japanese manufacturers closely work with suppliers to address problems and improve efficiency, in order not to compromise the quality of their products. They are also encouraging feedback from workers, salesmen and quality inspectors.
Japanese manufacturers have been worried about the rising number of factory accidents. There have been many safety scandals throughout the country's production sector. This has increased scrutiny over the quality of work in factories.
Non-regular labor has also been a problem for Japanese goods production. Companies can reduce labor costs by hiring non-regular workers, but they also increase the chance of accidents and lower the skill level on the production floor. To train their regular workers, companies have been focusing on making them more reliable and safer.
Japan's increasing labor shortage is due to its declining birthrate. The proportion of companies complaining about a labor shortage has reached a 25-year peak. Japanese companies will face increased challenges if the workforce shrinks.
Despite the shortage of skilled workers, a large percentage of factories have been cutting costs. A growing number of so-called "factries" employ fewer than ten people. Many of these small workshops create the finest equipment in the entire world.
China and South Korea are increasingly challenging the Japanese manufacturing sector. Many factories are now trying to increase productivity and reduce costs. The Japanese government warns that the industry could lose its competitive edge on overseas markets.
Japan is confronted with increased competition from Asia as well as abroad and it is questioning whether its ability to adapt and adjust its processes to meet this demand. It is not likely that it will be able to, as the demand for skilled workers continues to grow.
Japanese factories are a significant source of components to the global market. They are also a source of advanced materials, such as silicon chips, that are used in computers and smart phones. They rely on Japan for crucial components, whereas Chinese factories focus on low-cost assembly.
Despite having worked hard to improve their product quality and productivity, Japanese have had to face increased competition from the outside. Due to the economic downturn, their products were less valued in the domestic markets. This has forced them to cut costs. Despite these challenges the Japanese have managed to maintain a high level production standard.
FAQ
What are the four types of manufacturing?
Manufacturing is the process of transforming raw materials into useful products using machines and processes. It involves many different activities such as designing, building, testing, packaging, shipping, selling, servicing, etc.
What does it mean to be a manufacturer?
Manufacturing Industries are businesses that produce products for sale. Consumers are people who purchase these goods. To accomplish this goal, these companies employ a range of processes including distribution, sales, management, and production. They produce goods from raw materials by using machines and other machinery. This includes all types and varieties of manufactured goods, such as food items, clothings, building supplies, furnitures, toys, electronics tools, machinery vehicles, pharmaceuticals medical devices, chemicals, among others.
How does a Production Planner differ from a Project Manager?
The main difference between a production planner and a project manager is that a project manager is usually the person who plans and organizes the entire project, whereas a production planner is mainly involved in the planning stage of the project.
How can we reduce manufacturing overproduction?
In order to reduce excess production, you need to develop better inventory management methods. This would reduce the time spent on unproductive activities like purchasing, storing and maintaining excess stock. This would allow us to use our resources for more productive tasks.
One way to do this is to adopt a Kanban system. A Kanban board, a visual display to show the progress of work, is called a Kanban board. Kanban systems allow work items to move through different states until they reach their final destination. Each state represents an individual priority level.
If work is moving from one stage to the other, then the current task can be completed and moved on to the next. But if a task remains in the beginning stages it will stay that way until it reaches its end.
This allows work to move forward and ensures that no work is missed. With a Kanban board, managers can see exactly how much work is being done at any given moment. This data allows them adjust their workflow based upon real-time data.
Lean manufacturing, another method to control inventory levels, is also an option. Lean manufacturing seeks to eliminate waste from every step of the production cycle. Anything that does not contribute to the product's value is considered waste. Some common types of waste include:
-
Overproduction
-
Inventory
-
Unnecessary packaging
-
Excess materials
By implementing these ideas, manufacturers can improve efficiency and cut costs.
Why automate your warehouse?
Modern warehousing is becoming more automated. With the rise of ecommerce, there is a greater demand for faster delivery times as well as more efficient processes.
Warehouses have to be flexible to meet changing requirements. Technology is essential for warehouses to be able to adapt quickly to changing needs. Automating warehouses has many benefits. Here are some reasons why it's worth investing in automation:
-
Increases throughput/productivity
-
Reduces errors
-
Improves accuracy
-
Safety is boosted
-
Eliminates bottlenecks
-
Companies can scale more easily
-
Increases efficiency of workers
-
It gives visibility to everything that happens inside the warehouse
-
Enhances customer experience
-
Improves employee satisfaction
-
Reduces downtime and improves uptime
-
Ensures quality products are delivered on time
-
Eliminates human error
-
This helps to ensure compliance with regulations
What are the 7 Rs of logistics?
The acronym 7Rs of Logistics refers to the seven core principles of logistics management. It was published in 2004 by the International Association of Business Logisticians as part of their "Seven Principles of Logistics Management" series.
The following letters make up the acronym:
-
Responsible - to ensure that all actions are within the legal requirements and are not detrimental to others.
-
Reliable - Have confidence in your ability to fulfill all of your commitments.
-
Reasonable - make sure you use your resources well and don't waste them.
-
Realistic - consider all aspects of operations, including cost-effectiveness and environmental impact.
-
Respectful: Treat others with fairness and equity
-
Be resourceful: Look for opportunities to save money or increase productivity.
-
Recognizable: Provide customers with value-added service
What are the responsibilities of a logistic manager?
A logistics manager makes sure that all goods are delivered on-time and in good condition. This is accomplished by using the experience and knowledge gained from working with company products. He/she should make sure that enough stock is on hand to meet the demands.
Statistics
- (2:04) MTO is a production technique wherein products are customized according to customer specifications, and production only starts after an order is received. (oracle.com)
- In 2021, an estimated 12.1 million Americans work in the manufacturing sector.6 (investopedia.com)
- It's estimated that 10.8% of the U.S. GDP in 2020 was contributed to manufacturing. (investopedia.com)
- According to the United Nations Industrial Development Organization (UNIDO), China is the top manufacturer worldwide by 2019 output, producing 28.7% of the total global manufacturing output, followed by the United States, Japan, Germany, and India.[52][53] (en.wikipedia.org)
- [54][55] These are the top 50 countries by the total value of manufacturing output in US dollars for its noted year according to World Bank.[56] (en.wikipedia.org)
External Links
How To
How to Use Six Sigma in Manufacturing
Six Sigma can be described as "the use of statistical process control (SPC), techniques to achieve continuous improvement." Motorola's Quality Improvement Department in Tokyo, Japan developed Six Sigma in 1986. Six Sigma's core idea is to improve the quality of processes by standardizing and eliminating defects. This method has been adopted by many companies in recent years as they believe there are no perfect products or services. Six Sigma aims to reduce variation in the production's mean value. This means that if you take a sample of your product, then measure its performance against the average, you can find out what percentage of the time the process deviates from the norm. If you notice a large deviation, then it is time to fix it.
Understanding how variability works in your company is the first step to Six Sigma. Once you understand that, it is time to identify the sources of variation. It is important to identify whether the variations are random or systemic. Random variations occur when people do mistakes. Symmetrical variations are caused due to factors beyond the process. Random variations would include, for example, the failure of some widgets to fall from the assembly line. It would be considered a systematic problem if every widget that you build falls apart at the same location each time.
Once you've identified the problem areas you need to find solutions. You might need to change the way you work or completely redesign the process. Test them again once you've implemented the changes. If they didn't work, then you'll need to go back to the drawing board and come up with another plan.