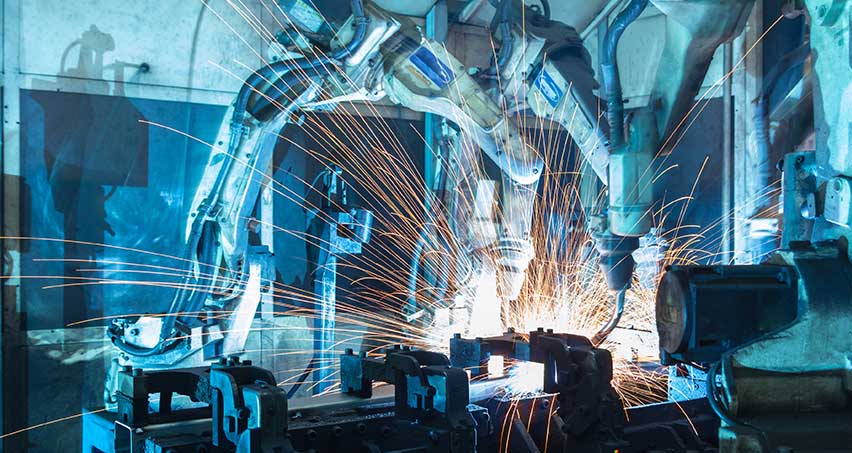
Lean thinking can help improve an organization's performance. It's about eliminating wastes and unvalued tasks from your process. It is also a way of creating a lean environment within your organization. A lean culture is a set of values, principles, and practices that promote employee morale, improve quality, and increase productivity. It creates a more sustainable work environment.
Lean thinking starts with identifying value for your customers. This requires understanding your customer's needs and the entire value chain. Once you have identified this, you can determine the steps in your processes. This will allow you to identify inefficiencies in your current processes. To see how your business is operating, you can also use value streaming mapping. The value stream mapping shows how your business works and the value that each process creates.
Lean thinking relies on flow. It's the ability to swiftly switch between one activity and another. This is crucial when responding to customer needs. This reduces inventory and backlogs. It also makes it possible for workers to quickly switch jobs.
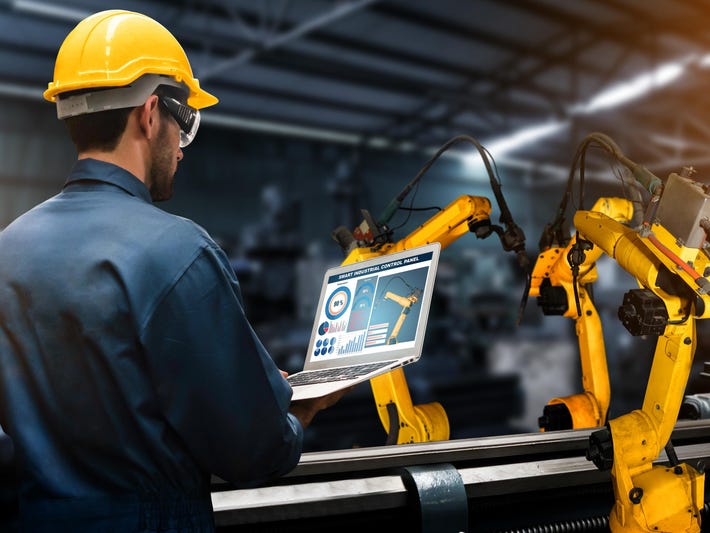
Lean organizations have a similar approach to managing output. They encourage communication and collaboration. They encourage quality assurance and celebrate success. They reduce unnecessary costs to customers and suppliers.
Lean thinking refers to a continuous process. It can be applied in any kind of work. It can help to reduce environmental damage, reduce the waste, and improve employee motivation. Although lean thinking is often used in manufacturing, it can be used in all areas of business.
A culture that encourages lean thinking and collaboration is key to implementing lean production techniques. The culture should be based on a clear definition of value, constant improvement, and employee motivation. You must also be willing to make small, incremental improvements on a regular basis. This is called kaizen.
Lean thinking involves continuous improvement and requires a kaizen spirit. To improve the quality of your product you have to be open to small improvements each day. This can be achieved by either implementing organizational changes or using standardized tasks. Standardized work is a visual representation of the flow of work. Everything is clearly located. It also helps people to see how to overcome obstacles to smooth work.
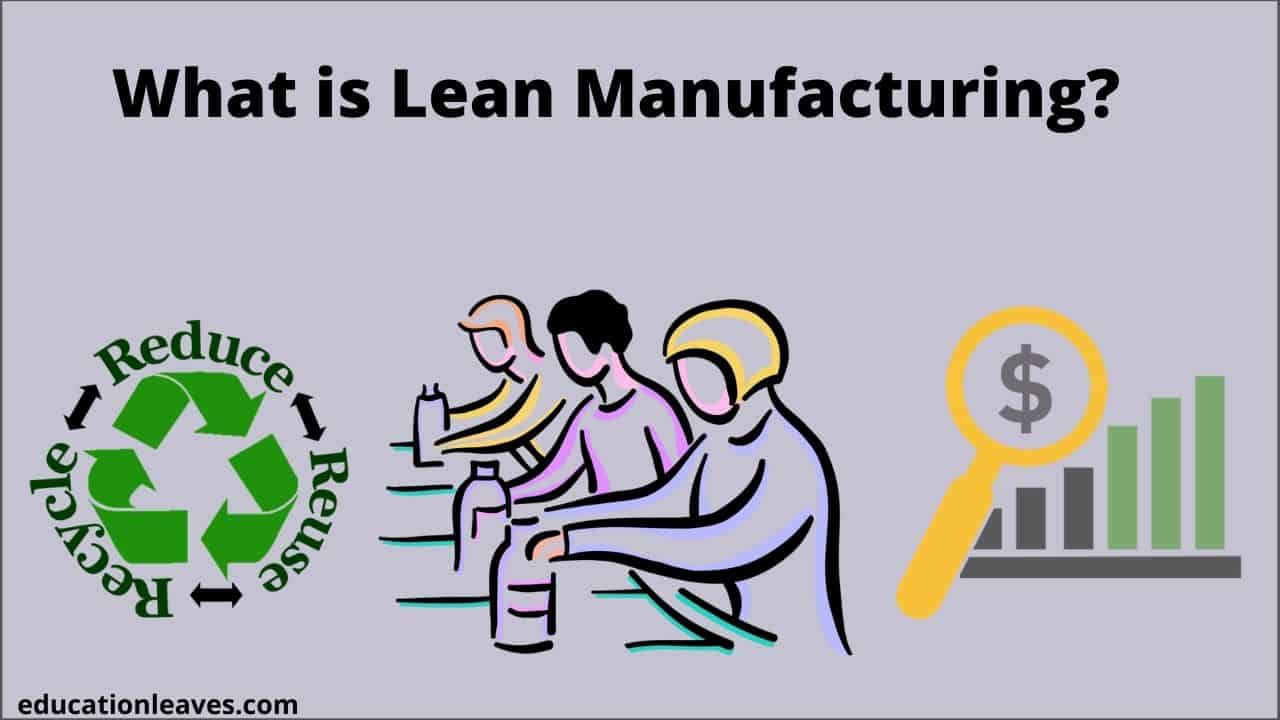
Other production metrics should also be considered when you implement lean production techniques. For example, the ratio of downtime to running time shows how often an asset is available for production. It also shows how often planned maintenance is required. It is an indicator of the supplier's ability to deliver quality products.
You should also be aware of the potential risks associated with the "Just In Time” principle. This principle ensures that supplies can be delivered promptly. It helps focus and concentrate the mind to the task at hand. It can also cause problems in your industry.
FAQ
What skills are required to be a production manager?
Being a production planner is not easy. You need to be organized and flexible. Also, you must be able and willing to communicate with clients and coworkers.
How does a Production Planner differ from a Project Manager?
The difference between a product planner and project manager is that a planer is typically the one who organizes and plans the entire project. A production planner, however, is mostly involved in the planning stages.
What does it take to run a logistics business?
To be a successful businessman in logistics, you will need many skills and knowledge. You must have good communication skills to interact effectively with your clients and suppliers. You will need to know how to interpret data and draw conclusions. You must be able and able to handle stress situations and work under pressure. In order to innovate and create new ways to improve efficiency, creativity is essential. You need to have strong leadership qualities to motivate team members and direct them towards achieving organizational goals.
It is important to be organized and efficient in order to meet tight deadlines.
What is the best way to learn about manufacturing?
Experience is the best way for you to learn about manufacturing. You can read books, or watch instructional videos if you don't have the opportunity to do so.
What are manufacturing & logistics?
Manufacturing is the process of creating goods from raw materials by using machines and processes. Logistics is the management of all aspects of supply chain activities, including procurement, production planning, distribution, warehousing, inventory control, transportation, and customer service. Logistics and manufacturing are often referred to as one thing. It encompasses both the creation of products and their delivery to customers.
What is the responsibility for a logistics manager
Logistics managers make sure all goods are delivered on schedule and without damage. This is done by using his/her experience and knowledge of the company's products. He/she should also ensure enough stock is available to meet demand.
Statistics
- Job #1 is delivering the ordered product according to specifications: color, size, brand, and quantity. (netsuite.com)
- [54][55] These are the top 50 countries by the total value of manufacturing output in US dollars for its noted year according to World Bank.[56] (en.wikipedia.org)
- In the United States, for example, manufacturing makes up 15% of the economic output. (twi-global.com)
- (2:04) MTO is a production technique wherein products are customized according to customer specifications, and production only starts after an order is received. (oracle.com)
- According to the United Nations Industrial Development Organization (UNIDO), China is the top manufacturer worldwide by 2019 output, producing 28.7% of the total global manufacturing output, followed by the United States, Japan, Germany, and India.[52][53] (en.wikipedia.org)
External Links
How To
How to use lean manufacturing in the production of goods
Lean manufacturing is a management style that aims to increase efficiency and reduce waste through continuous improvement. It was first developed in Japan in the 1970s/80s by Taiichi Ahno, who was awarded the Toyota Production System (TPS), award from KanjiToyoda, the founder of TPS. Michael L. Watkins published the original book on lean manufacturing, "The Machine That Changed the World," in 1990.
Lean manufacturing, often described as a set and practice of principles, is aimed at improving the quality, speed, cost, and efficiency of products, services, and other activities. It emphasizes the elimination of defects and waste throughout the value stream. The five-steps of Lean Manufacturing are just-in time (JIT), zero defect and total productive maintenance (TPM), as well as 5S. Lean manufacturing emphasizes reducing non-value-added activities like inspection, rework and waiting.
Lean manufacturing is a way for companies to achieve their goals faster, improve product quality, and lower costs. Lean manufacturing can be used to manage all aspects of the value chain. Customers, suppliers, distributors, retailers and employees are all included. Lean manufacturing is widely used in many industries. Toyota's philosophy is a great example of this. It has helped to create success in automobiles as well electronics, appliances and healthcare.
Five principles are the basis of lean manufacturing:
-
Define Value - Identify the value your business adds to society and what makes you different from competitors.
-
Reduce Waste – Eliminate all activities that don't add value throughout the supply chain.
-
Create Flow - Ensure work moves smoothly through the process without interruption.
-
Standardize and Simplify – Make processes as consistent, repeatable, and as simple as possible.
-
Build Relationships - Establish personal relationships with both internal and external stakeholders.
Although lean manufacturing isn't a new concept in business, it has gained popularity due to renewed interest in the economy after the 2008 global financial crisis. To increase their competitiveness, many businesses have turned to lean manufacturing. In fact, some economists believe that lean manufacturing will be an important factor in economic recovery.
With many benefits, lean manufacturing is becoming more common in the automotive industry. These include higher customer satisfaction levels, reduced inventory levels as well as lower operating costs.
Any aspect of an enterprise can benefit from Lean manufacturing. Because it makes sure that all value chains are efficient and effectively managed, Lean Manufacturing is particularly helpful for organizations.
There are three main types:
-
Just-in Time Manufacturing, (JIT): This kind of lean manufacturing is also commonly known as "pull-systems." JIT is a method in which components are assembled right at the moment of use, rather than being manufactured ahead of time. This approach is designed to reduce lead times and increase the availability of components. It also reduces inventory.
-
Zero Defects Manufacturing - ZDM: ZDM focuses its efforts on making sure that no defective units leave a manufacturing facility. If a part is required to be repaired on the assembly line, it should not be scrapped. This is true even for finished products that only require minor repairs prior to shipping.
-
Continuous Improvement: Continuous Improvement aims to improve efficiency by continually identifying problems and making adjustments to eliminate or minimize waste. Continuous improvement refers to continuous improvement of processes as well people and tools.