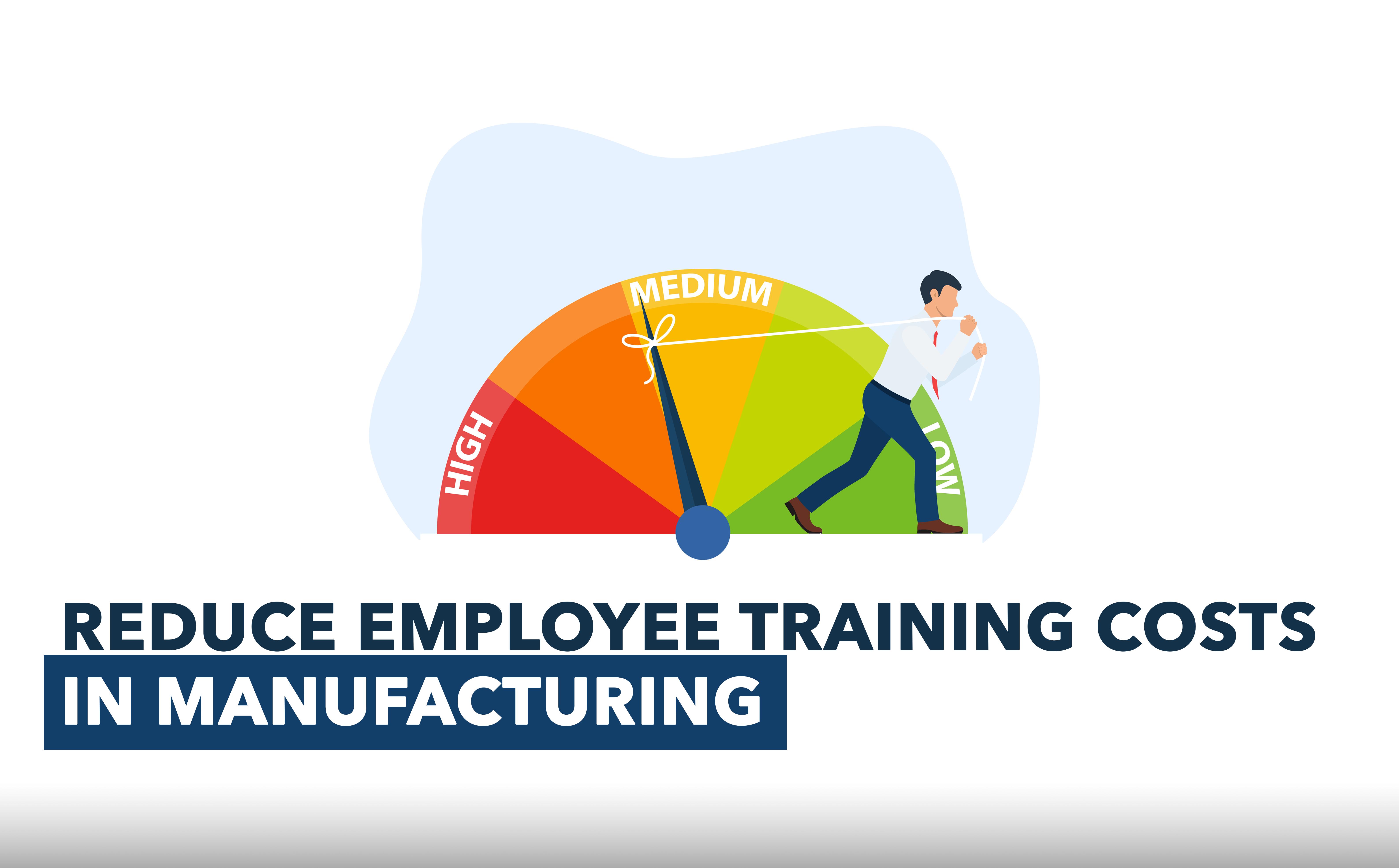
General managers are responsible to formulate strategy, hire functional leaders, and communicate with all stakeholders. This article will discuss the responsibilities and skills required to excel in this position. Read on to see a complete description of the duties of a general manger. To be a successful general manager, you'll need strong communication and presentation skills. A mastery of financial management is also required. Your success is ultimately dependent on your ability to be persistent and manage your company's processes and performance within a budget. You must be a great leader and build trust with customers.
GMs are responsible for strategy formulation
Although it is true that GMs are responsible for strategy formulation, the process can be subject to certain risks. A GM who is motivated by their own motivations or is a member a leadership team might overplay his role in strategy formulation. Managers are subjected primarily to their own motivations.
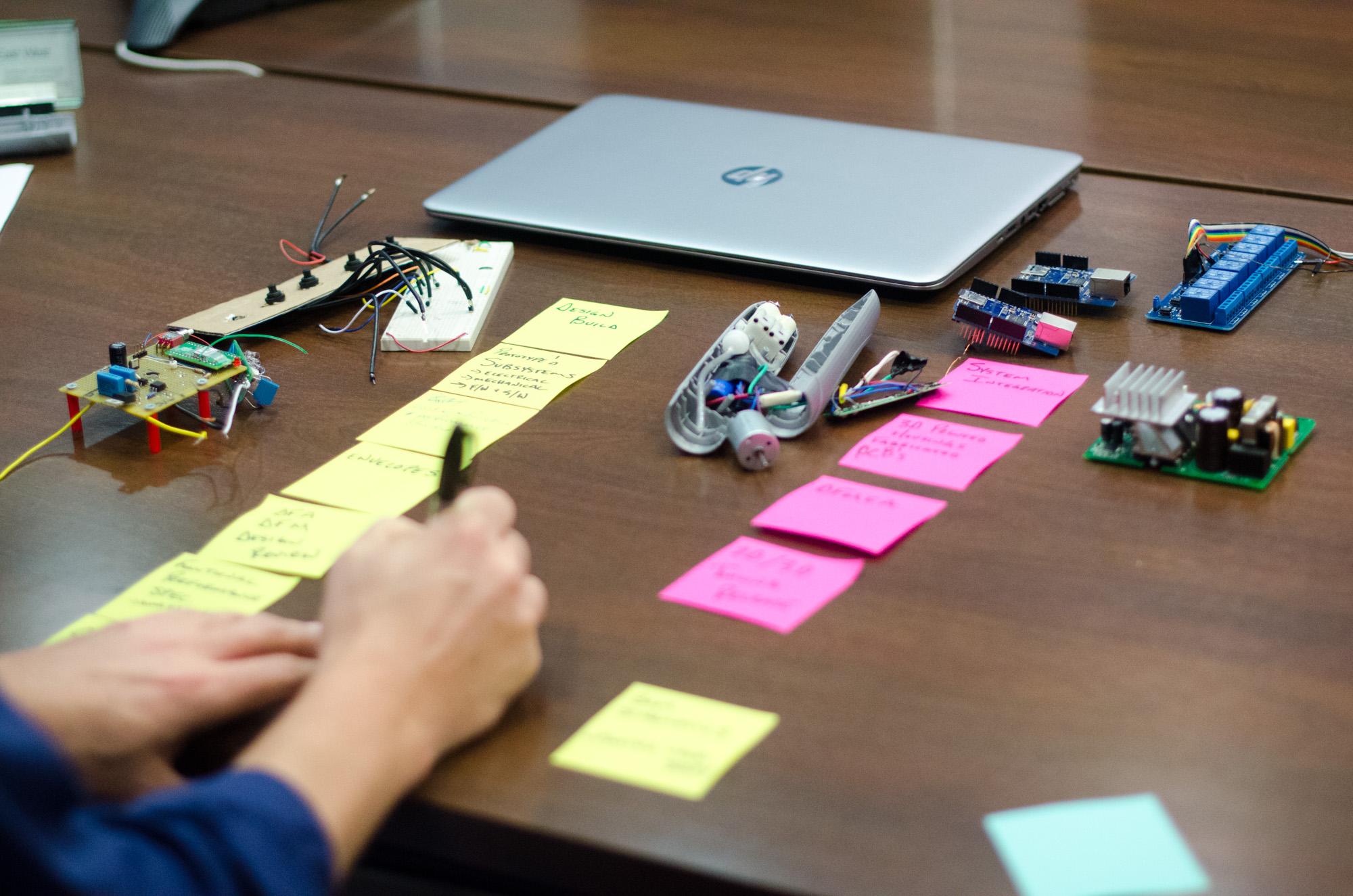
They employ functional leaders
The organization and its business units are under the general manager's control. They have to manage the entire business from strategy to structure to budgets and people. They are also responsible to manage the daily operations and coordinate key performance indicators for all business units. In order to succeed in this role, they will need to understand the language of finance and human resources. The role of general manager is complex and essential for the overall success of an organisation.
They collaborate closely with their subordinates
General managers are responsible for understanding the organisation's internal workings and communicating with all departments. They must also have strong analytical skills in order to recognize problems and come up with appropriate solutions. It is expected that general managers will be strong leaders and be able to delegate work and ensure that employees perform to their potential. General managers also need to be able to work closely with other departments and provide clear directives for subordinates.
They communicate with them
Many general manager tasks require good communication skills. General managers can help employees listen by hosting training sessions, or coaching them in effective communication techniques. To encourage better communication, general managers can host more team events and meetings. These are some tips for improving general manager communication skills. All good managers should make themselves accessible to employees to help them succeed. This is a critical part of their job. They should be available to answer any questions or provide guidance if necessary.

They are motivating
Top GMs can motivate staff. They are willing work long hours, demonstrate dedication to the business, and set an example for their employees. They reinforce their high standards by small acts. Here are some of the ways top managers motivate their staff:
FAQ
Can we automate some parts of manufacturing?
Yes! Since ancient times, automation has been in existence. The Egyptians discovered the wheel thousands and years ago. To help us build assembly lines, we now have robots.
There are many uses of robotics today in manufacturing. These include:
-
Assembly line robots
-
Robot welding
-
Robot painting
-
Robotics inspection
-
Robots that produce products
Automation can be applied to manufacturing in many other ways. For example, 3D printing allows us to make custom products without having to wait for weeks or months to get them manufactured.
Are there any Manufacturing Processes that we should know before we can learn about Logistics?
No. It doesn't matter if you don't know anything about manufacturing before you learn about logistics. But, being familiar with manufacturing processes will give you a better understanding about how logistics works.
Why is logistics important for manufacturing?
Logistics is an integral part of every business. They help you achieve great results by helping you manage all aspects of product flow, from raw materials to finished goods.
Logistics plays a significant role in reducing cost and increasing efficiency.
Statistics
- [54][55] These are the top 50 countries by the total value of manufacturing output in US dollars for its noted year according to World Bank.[56] (en.wikipedia.org)
- In 2021, an estimated 12.1 million Americans work in the manufacturing sector.6 (investopedia.com)
- It's estimated that 10.8% of the U.S. GDP in 2020 was contributed to manufacturing. (investopedia.com)
- In the United States, for example, manufacturing makes up 15% of the economic output. (twi-global.com)
- According to the United Nations Industrial Development Organization (UNIDO), China is the top manufacturer worldwide by 2019 output, producing 28.7% of the total global manufacturing output, followed by the United States, Japan, Germany, and India.[52][53] (en.wikipedia.org)
External Links
How To
How to use the Just-In Time Method in Production
Just-in time (JIT), is a process that reduces costs and increases efficiency in business operations. It allows you to get the right amount resources at the right time. This means that only what you use is charged to your account. The term was first coined by Frederick Taylor, who developed his theory while working as a foreman in the early 1900s. He noticed that workers were often paid overtime when they had to work late. He realized that workers should have enough time to complete their jobs before they begin work. This would help increase productivity.
The idea behind JIT is that you should plan ahead and have everything ready so you don't waste money. You should also look at the entire project from start to finish and make sure that you have sufficient resources available to deal with any problems that arise during the course of your project. If you anticipate that there might be problems, you'll have enough people and equipment to fix them. This will ensure that you don't spend more money on things that aren't necessary.
There are many JIT methods.
-
Demand-driven: This JIT is where you place regular orders for the parts/materials that are needed for your project. This will allow you to track how much material you have left over after using it. It will also allow you to predict how long it takes to produce more.
-
Inventory-based: This type allows you to stock the materials needed for your projects ahead of time. This allows you predict the amount you can expect to sell.
-
Project-driven: This means that you have enough money to pay for your project. If you know the amount you require, you can buy the materials you need.
-
Resource-based JIT: This type of JIT is most commonly used. You allocate resources based on the demand. You might assign more people to help with orders if there are many. If you don’t have many orders you will assign less people to the work.
-
Cost-based : This is similar in concept to resource-based. But here, you aren't concerned about how many people your company has but how much each individual costs.
-
Price-based pricing: This is similar in concept to cost-based but instead you look at how much each worker costs, it looks at the overall company's price.
-
Material-based is an alternative to cost-based. Instead of looking at the total cost in the company, this method focuses on the average amount of raw materials that you consume.
-
Time-based JIT: This is another variant of resource-based JIT. Instead of focusing solely on the amount each employee costs, focus on how long it takes for the project to be completed.
-
Quality-based JIT: Another variation on resource-based JIT. Instead of worrying about the costs of each employee or how long it takes for something to be made, you should think about how quality your product is.
-
Value-based JIT: One of the most recent forms of JIT. This is where you don't care about how the products perform or whether they meet customers' expectations. Instead, your focus is on the value you bring to the market.
-
Stock-based: This inventory-based approach focuses on how many items are being produced at any one time. It's useful when you want maximum production and minimal inventory.
-
Just-intime (JIT), planning is a combination JIT management and supply chain management. This refers to the scheduling of the delivery of components as soon after they are ordered. This is important as it reduces lead time and increases throughput.