
A blue collar job is generally a manual labor job. These jobs can be found in construction, manufacturing or hospitality. While some may require some skills, such as electricians or plumbers, others may not. Blue collar jobs tend to pay decent salaries and offer good career growth.
The Fourth Industrial Revolution has the potential to transform the labour market for manual workers. This revolution involves artificial intelligence (AI), robotics, machine-learning, and 3D printing. It will require a new, more skilled workforce for companies to succeed. It will also require firms to shift away from transactional relationships, and toward more enduring ones.
Employers are therefore forced to recruit workers from the United States. In some cases, these workers can be hired per-item. Others might be paid by the project. It is encouraging to see the demand for blue collar work rising.
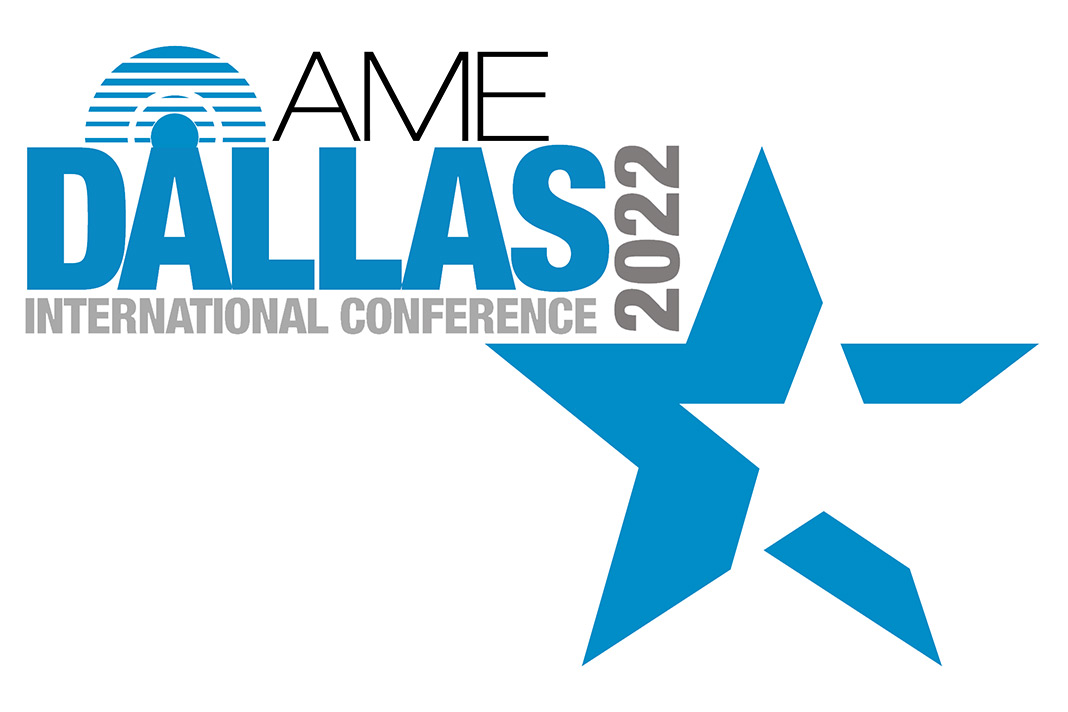
These jobs require some physical labor, but they are often better-paid than white collar work. Companies are willing to invest in their employees' training because these jobs can provide good income. Some examples of these jobs are signal and track switching repairers, nuclear power reactor operators, and electrical and electronics repairers. These jobs do not require a highschool diploma. However, some require on-thejob training.
The availability of blue collar jobs is also higher than that of white collar positions. The majority of Indian workforce is made up of blue collar workers. India has 210 million workers in the agricultural sector, and 290 million in the non-agricultural sector. The demand for blue-collar workers is increasing at an alarming rate.
Companies are also being transformed by the Fourth Industrial Revolution in how they manage their blue-collar workers. Not only are digital jobs replacing manual ones, but firms are also moving away form transactional relationships and toward lasting ones. Firms can create stronger relationships and better productivity by prioritizing their employees.
Although blue collar workers are highly in demand, they have to face competing realities. They might be concerned about their jobs' stability, or about retirement. Blue collar workers, despite these worries, tend to be optimistic about the future. In fact, the percentage of blue-collar workers saving for retirement is growing. As the economy recovers, blue-collar jobs are expected to rise in popularity.
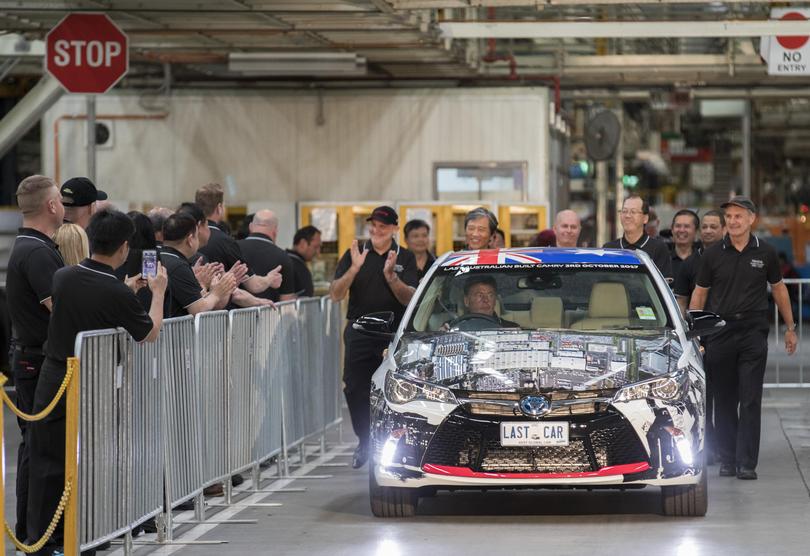
These jobs are also not threatened by automation. According to the Association for Manufacturing Technology, for every job that technology replaced, five new jobs were created. The biggest salary increase last year went to signal and track switch repairers, who earned $76,210 on average.
In addition to being more lucrative, blue collar positions are also becoming more popular. Many blue collar jobs have earnings that are higher than the national average. This makes it a great option for people looking for a good job. Additionally, blue collar jobs often require a high level in problem-solving skills. They are also likely to offer career growth.
FAQ
How can manufacturing avoid production bottlenecks
To avoid production bottlenecks, ensure that all processes run smoothly from the moment you receive your order to the time the product ships.
This includes both planning for capacity and quality control.
This can be done by using continuous improvement techniques, such as Six Sigma.
Six Sigma is a management method that helps to improve quality and reduce waste.
It's all about eliminating variation and creating consistency in work.
Why is logistics important for manufacturing?
Logistics are essential to any business. They enable you to achieve outstanding results by helping manage product flow from raw materials through to finished goods.
Logistics are also important in reducing costs and improving efficiency.
What is the role of a production manager?
Production planners ensure that all project aspects are completed on time, within budget and within the scope. They also ensure that the product/service meets the client’s needs.
Statistics
- According to a Statista study, U.S. businesses spent $1.63 trillion on logistics in 2019, moving goods from origin to end user through various supply chain network segments. (netsuite.com)
- Many factories witnessed a 30% increase in output due to the shift to electric motors. (en.wikipedia.org)
- In the United States, for example, manufacturing makes up 15% of the economic output. (twi-global.com)
- According to the United Nations Industrial Development Organization (UNIDO), China is the top manufacturer worldwide by 2019 output, producing 28.7% of the total global manufacturing output, followed by the United States, Japan, Germany, and India.[52][53] (en.wikipedia.org)
- You can multiply the result by 100 to get the total percent of monthly overhead. (investopedia.com)
External Links
How To
How to Use the Just In Time Method in Production
Just-in-time is a way to cut costs and increase efficiency in business processes. This is where you have the right resources at the right time. This means that you only pay for what you actually use. Frederick Taylor first coined this term while working in the early 1900s as a foreman. He saw how overtime was paid to workers for work that was delayed. He decided to ensure workers have enough time to do their jobs before starting work to improve productivity.
JIT teaches you to plan ahead and prepare everything so you don’t waste time. You should also look at the entire project from start to finish and make sure that you have sufficient resources available to deal with any problems that arise during the course of your project. You'll be prepared to handle any potential problems if you know in advance. You won't have to pay more for unnecessary items.
There are many types of JIT methods.
-
Demand-driven JIT: You order the parts and materials you need for your project every other day. This will enable you to keep track of how much material is left after you use it. This will let you know how long it will be to produce more.
-
Inventory-based: You stock materials in advance to make your projects easier. This allows you to forecast how much you will sell.
-
Project-driven: This approach involves setting aside sufficient funds to cover your project's costs. Once you have an idea of how much material you will need, you can purchase the necessary materials.
-
Resource-based JIT is the most widespread form. This is where you assign resources based upon demand. If you have many orders, you will assign more people to manage them. If you don't have many orders, you'll assign fewer people to handle the workload.
-
Cost-based: This is the same as resource-based except that you don't care how many people there are but how much each one of them costs.
-
Price-based: This is very similar to cost-based, except that instead of looking at how much each individual worker costs, you look at the overall price of the company.
-
Material-based - This is a variant of cost-based. But instead of looking at the total company cost, you focus on how much raw material you spend per year.
-
Time-based: Another variation of resource-based JIT. Instead of focusing solely on the amount each employee costs, focus on how long it takes for the project to be completed.
-
Quality-based JIT: This is another variation of resource based JIT. Instead of looking at the labor costs and time it takes to make a product, think about its quality.
-
Value-based JIT : This is the newest type of JIT. In this scenario, you're not concerned about how products perform or whether customers expect them to meet their expectations. Instead, your focus is on the value you bring to the market.
-
Stock-based. This method is inventory-based and focuses only on the actual production at any given point. This is used to increase production and minimize inventory.
-
Just-in-time (JIT) planning: This is a combination of JIT and supply chain management. It is the process that schedules the delivery of components within a short time of their order. It's important as it reduces leadtimes and increases throughput.