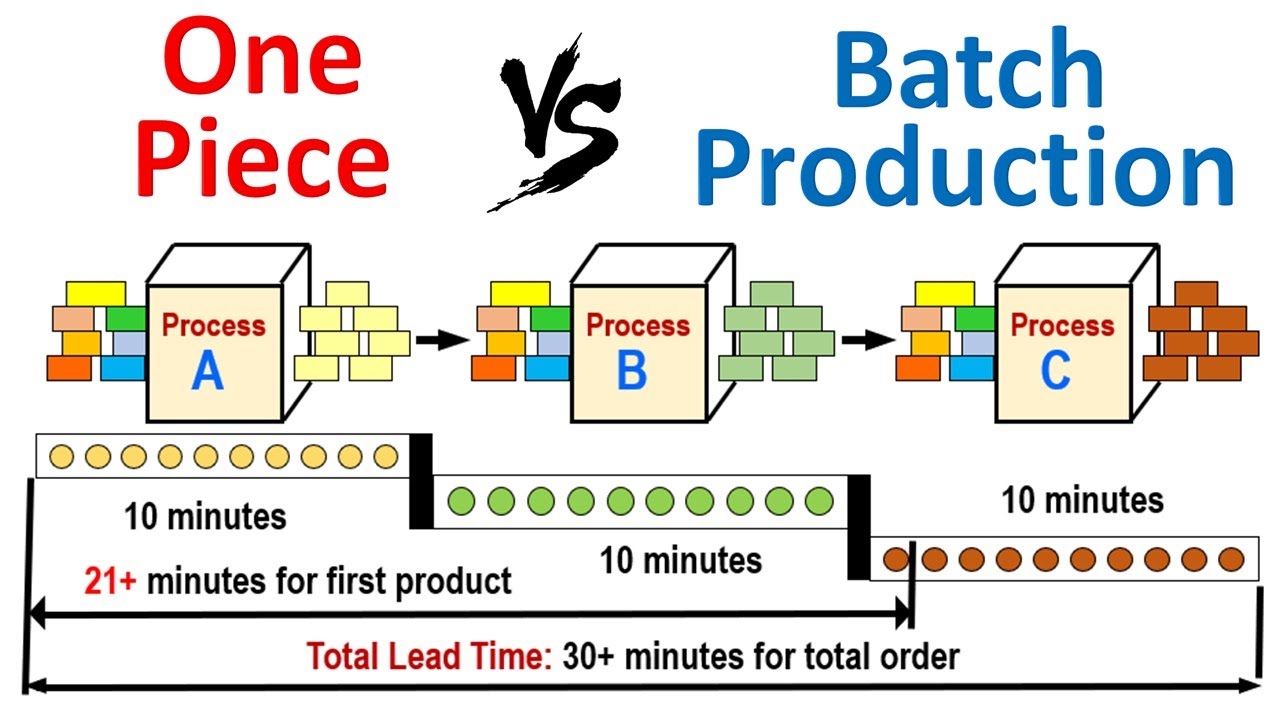
OSHA compliance and experience are equally important for food manufacturers. Three things to look at when looking for a company to automate the production process.
Food manufacturers need to have experience
A high level of industry experience is often required for a position in a food manufacturer. However, there are also opportunities for those with little or no experience. Many food manufacturers prefer to hire within their own ranks. High school education can be beneficial but not essential. Entry-level employees start out as assistants to more experienced workers. They then learn on their own. Some entry-level jobs are straightforward and can be completed in a few days. Common entry-level jobs include operating bread slicers and washing vegetables before processing. In every aspect of food manufacturing, experience is essential.
OSHA regulations must be followed
OSHA regulations governing food manufacturers require that an inspection be conducted. This inspection is either triggered through an incident, complaint or "programmed inspection". OSHA enforcement visits to yogurt manufacturing facilities are, for instance, triggered by a complaint. They were preceded by a plan inspection. Many cases include multiple violations for the process safety management system, standards on hazard communication (guarding machinery), stairs and platforms as well emergency egress, forklift operator, hearing protection, and others.
Develop a plan for food safety
While federal regulations govern most companies, some businesses are exempt from certain requirements. It is impossible to predict every possible food safety problem, but there are ways to manage and prevent them. Food safety is a serious problem that can not only affect the health of the consumer but also impact the business. Recalls have the potential to affect both operations and other parts of the supply chain. These recalls can happen for many reasons, including adulteration or misbranding and violative products. Food recalls can pose health risks and can be expensive for food manufacturers.
Automation Costs
The cost of automation for food manufacturers is increasing as utility costs increase, and some regions are forced to import ingredients to compete with local producers. The suppliers also have a decreasing profit margin as they pass on the cost to consumers. Automation can help reduce costs and increase efficiency. In this article, we'll discuss how automation can help improve the overall efficiency for food manufacturers. You can also reach out to us for our industry knowledge.
Competition with major food companies: Challenges
To maintain their market dominance and prevent unwelcome competition, dominant food companies employ three strategies. These strategies include acquiring and developing intangible assets, controlling the supply chain, marketing efficiency, and enforcing production and market efficiencies. These strategies are essentially barriers to entry. Here are some of the most important challenges faced by emerging food and beverage companies. Let's talk more about each strategy.
FAQ
What does manufacturing mean?
Manufacturing Industries refers to businesses that manufacture products. Consumers are people who purchase these goods. These companies use a variety processes such as distribution, retailing and management to accomplish their purpose. They create goods from raw materials, using machines and various other equipment. This includes all types of manufactured goods, including food items, clothing, building supplies, furniture, toys, electronics, tools, machinery, vehicles, pharmaceuticals, medical devices, chemicals, and many others.
Is there anything we should know about Manufacturing Processes prior to learning about Logistics.
No. It doesn't matter if you don't know anything about manufacturing before you learn about logistics. But, being familiar with manufacturing processes will give you a better understanding about how logistics works.
What is the role of a production manager?
Production planners make sure that every aspect of the project is delivered on-time, within budget, and within schedule. They also ensure the quality of the product and service meets the client's requirements.
Why is logistics important for manufacturing?
Logistics are an essential part of any business. They enable you to achieve outstanding results by helping manage product flow from raw materials through to finished goods.
Logistics are also important in reducing costs and improving efficiency.
Why automate your warehouse?
Modern warehouses are increasingly dependent on automation. The rise of e-commerce has led to increased demand for faster delivery times and more efficient processes.
Warehouses have to be flexible to meet changing requirements. They must invest heavily in technology to do this. Automating warehouses is a great way to save money. Here are some of the reasons automation is worth your investment:
-
Increases throughput/productivity
-
Reduces errors
-
Increases accuracy
-
Safety enhancements
-
Eliminates bottlenecks
-
This allows companies to scale easily
-
It makes workers more efficient
-
Provides visibility into everything that happens in the warehouse
-
Enhances customer experience
-
Improves employee satisfaction
-
It reduces downtime, and increases uptime
-
Quality products delivered on time
-
Removing human error
-
It ensures compliance with regulations
Statistics
- Job #1 is delivering the ordered product according to specifications: color, size, brand, and quantity. (netsuite.com)
- According to the United Nations Industrial Development Organization (UNIDO), China is the top manufacturer worldwide by 2019 output, producing 28.7% of the total global manufacturing output, followed by the United States, Japan, Germany, and India.[52][53] (en.wikipedia.org)
- In the United States, for example, manufacturing makes up 15% of the economic output. (twi-global.com)
- [54][55] These are the top 50 countries by the total value of manufacturing output in US dollars for its noted year according to World Bank.[56] (en.wikipedia.org)
- Many factories witnessed a 30% increase in output due to the shift to electric motors. (en.wikipedia.org)
External Links
How To
How to Use Just-In-Time Production
Just-intime (JIT), a method used to lower costs and improve efficiency in business processes, is called just-in-time. It allows you to get the right amount resources at the right time. This means that only what you use is charged to your account. Frederick Taylor developed the concept while working as foreman in early 1900s. He saw how overtime was paid to workers for work that was delayed. He then concluded that if he could ensure that workers had enough time to do their job before starting to work, this would improve productivity.
The idea behind JIT is that you should plan ahead and have everything ready so you don't waste money. Also, you should look at the whole project from start-to-finish and make sure you have the resources necessary to address any issues. If you anticipate that there might be problems, you'll have enough people and equipment to fix them. This way, you won't end up paying extra money for things that weren't really necessary.
There are different types of JIT methods:
-
Demand-driven JIT: This is a JIT that allows you to regularly order the parts/materials necessary for your project. This will let you track the amount of material left over after you've used it. This will allow you to calculate how long it will take to make more.
-
Inventory-based: This allows you to store the materials necessary for your projects in advance. This allows you predict the amount you can expect to sell.
-
Project-driven: This method allows you to set aside enough funds for your project. You will be able to purchase the right amount of materials if you know what you need.
-
Resource-based JIT : This is probably the most popular type of JIT. This is where you assign resources based upon demand. For example, if there is a lot of work coming in, you will have more people assigned to them. If you don't have many orders, you'll assign fewer people to handle the workload.
-
Cost-based : This is similar in concept to resource-based. But here, you aren't concerned about how many people your company has but how much each individual costs.
-
Price-based: This is very similar to cost-based, except that instead of looking at how much each individual worker costs, you look at the overall price of the company.
-
Material-based: This is very similar to cost-based but instead of looking at total costs of the company you are concerned with how many raw materials you use on an average.
-
Time-based JIT is another form of resource-based JIT. Instead of focusing on how much each employee costs, you focus on how long it takes to complete the project.
-
Quality-based JIT: Another variation on resource-based JIT. Instead of thinking about the cost of each employee or the time it takes to produce something, you focus on how good your product quality.
-
Value-based: This is one of the newest forms of JIT. In this scenario, you're not concerned about how products perform or whether customers expect them to meet their expectations. Instead, your focus is on the value you bring to the market.
-
Stock-based: This stock-based method focuses on the actual quantity of products being made at any given time. It's used when you want to maximize production while minimizing inventory.
-
Just-in-time (JIT) planning: This is a combination of JIT and supply chain management. It refers to the process of scheduling the delivery of components as soon as they are ordered. It is essential because it reduces lead-times and increases throughput.