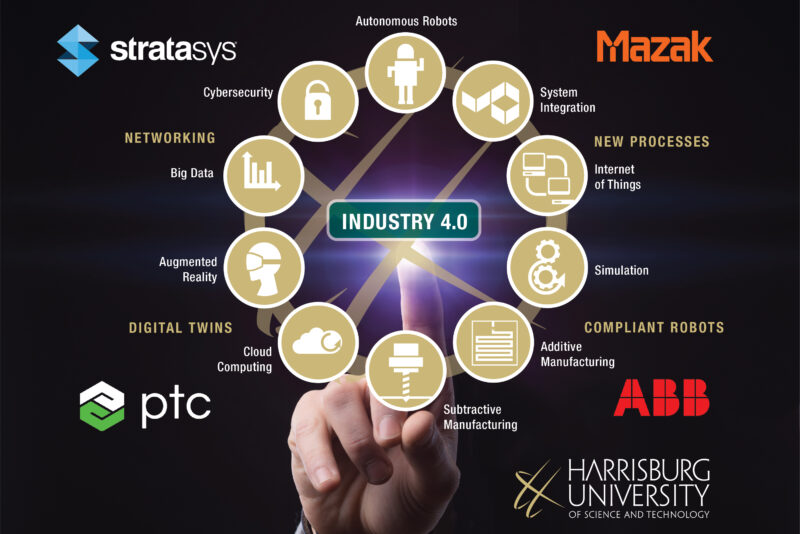
There are many types of manufacturers, but which one is best for your business? Learn about discrete manufacturing, continuous manufacturing, job shop manufacturing, or process manufacturing. Each type has its own advantages and disadvantages. This article will show you how the four types of manufacturing differ. The best model for you business will depend on your industry and location. Once you have determined which type is best, you need to take into account your sales, production and quality control.
Discrete manufacturing
Discrete manufacturing refers to a process where different products are made. Examples of such products are toys, automobiles and aeroplanes. Discrete manufacturing allows companies the freedom to concentrate on specific products rather than mass production. For example, discrete manufacturing makes it possible to create unique parts for an aeroplane by integrating several manufacturing processes. High-tech products can be made by discrete manufacturing.
Discrete manufacturing produces distinct items. Instead of making many identical products, discrete production produces unique items that can be easily identified with serial numbers, labels and other numerical attributes. A smartphone might be made up of parts from different factories located in different states. The individual pieces are only assembled once the product is sold. The same is true for the smartphone's case. It might contain different parts of several plants, including the Missouri plant and headquarters.
Process manufacturing
The idea of process manufacturing is a sub-field of manufacturing that includes formulas and recipes. The term process manufacturing contrasts with discrete manufacturing, which is concerned with individual units, bills of materials, and the assembly of components. Both manufacturing methods have different goals. But each one is an important part of the manufacturing process. Here are three methods to distinguish between discrete and process manufacturing. Let's take a look at each of them.
Batch process manufacturing is similar to continuous process manufacturing, but it uses larger batches of raw materials and runs around the clock. Batch process manufacturing is used in many industries, including pharmaceuticals, paper production and bookbinding. This process is not the best for every industry. For smaller businesses, it can be too expensive and complex. This is why most companies resort to this method when producing large quantities of the same product.
Factory job shop
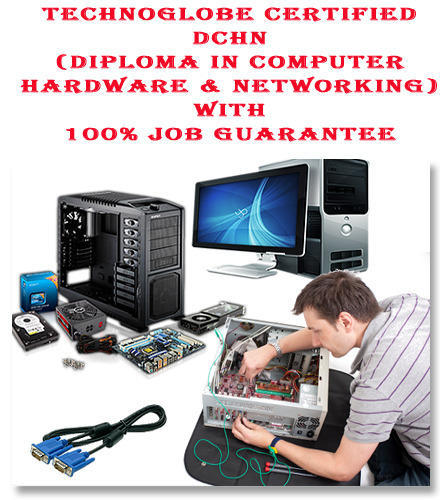
Job shop manufacturing is small-scale manufacturing that specializes in custom, semi-custom, and batch manufacturing. After each job is complete, job shop systems can move to the next. This method of production, also known as lean manufacture, is more efficient than any other. Here are some benefits of job shop manufacturing. This manufacturing process is described in detail below. It might be a good option for your business if you need to manufacture products or services.
First, job shops have to be more efficient. A critical factor in achieving a lean manufacturing system is incorporating new manufacturing principles. These principles focus on quality control and justin-time production and are especially relevant for high-volume operations. A job shop can improve productivity and reduce costs by adopting new manufacturing principles. Additionally, jobs should proceed through each process one at a time, so there should be no queues.
Continuous manufacturing
Continuous manufacturing offers many benefits, including the flexibility of tracking. This is especially beneficial when it concerns product failure. Since the production line's time stamp and the raw material quantity can help identify when a batch has gone wrong, continuous manufacturing allows for more flexible tracking. This allows the manufacturer to reduce waste and minimize the possibility of a product shortage by allowing for better tracking. In the pharmaceutical industry, continuous manufacturing is also gaining popularity.
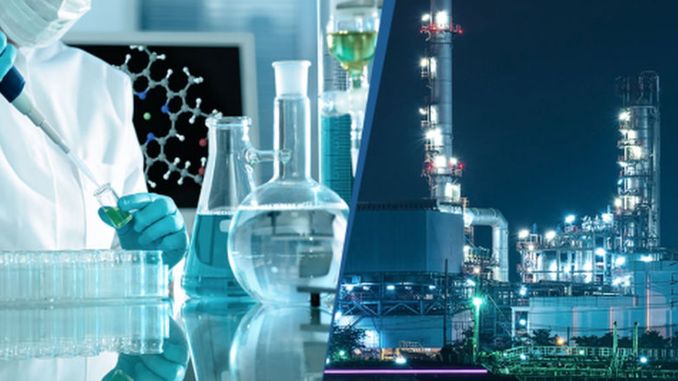
Although continuous manufacturing has many benefits, implementation can be difficult. Implementation can be difficult because the process is not fully integrated within the company. Continuous manufacturing, despite its potential benefits, has the potential for a major shift in the pharmaceutical industry. The process must be seamless and integrate with continuous flow and end to end integration for it to be effective. While the benefits of continuous manufacturing have been well-known in the pharmaceutical sector, implementation has been slow.
FAQ
What is manufacturing and logistics?
Manufacturing refers the process of producing goods from raw materials through machines and processes. Logistics manages all aspects of the supply chain, including procurement, production planning and distribution, inventory control, transportation, customer service, and transport. Manufacturing and logistics are often considered together as a broader term that encompasses both the process of creating products and delivering them to customers.
How important is automation in manufacturing?
Automation is essential for both manufacturers and service providers. It enables them to provide services faster and more efficiently. It helps them to lower costs by reducing human errors, and improving productivity.
How is a production manager different from a producer planner?
The difference between a product planner and project manager is that a planer is typically the one who organizes and plans the entire project. A production planner, however, is mostly involved in the planning stages.
What are the 4 types manufacturing?
Manufacturing is the process by which raw materials are transformed into useful products through machines and processes. It involves many different activities such as designing, building, testing, packaging, shipping, selling, servicing, etc.
Statistics
- According to the United Nations Industrial Development Organization (UNIDO), China is the top manufacturer worldwide by 2019 output, producing 28.7% of the total global manufacturing output, followed by the United States, Japan, Germany, and India.[52][53] (en.wikipedia.org)
- In the United States, for example, manufacturing makes up 15% of the economic output. (twi-global.com)
- It's estimated that 10.8% of the U.S. GDP in 2020 was contributed to manufacturing. (investopedia.com)
- Many factories witnessed a 30% increase in output due to the shift to electric motors. (en.wikipedia.org)
- [54][55] These are the top 50 countries by the total value of manufacturing output in US dollars for its noted year according to World Bank.[56] (en.wikipedia.org)
External Links
How To
How to Use lean manufacturing in the Production of Goods
Lean manufacturing is a management system that aims at increasing efficiency and reducing waste. It was developed by Taiichi Okono in Japan, during the 1970s & 1980s. TPS founder Kanji Takoda awarded him the Toyota Production System Award (TPS). The first book published on lean manufacturing was titled "The Machine That Changed the World" written by Michael L. Watkins and published in 1990.
Lean manufacturing is often defined as a set of principles used to improve the quality, speed, and cost of products and services. It emphasizes the elimination and minimization of waste in the value stream. Just-in-time (JIT), zero defect (TPM), and 5S are all examples of lean manufacturing. Lean manufacturing seeks to eliminate non-value added activities, such as inspection, work, waiting, and rework.
In addition to improving product quality and reducing costs, lean manufacturing helps companies achieve their goals faster and reduces employee turnover. Lean manufacturing has been deemed one of the best ways to manage the entire value-chain, including customers, distributors as well retailers and employees. Many industries worldwide use lean manufacturing. Toyota's philosophy is the foundation of its success in automotives, electronics and appliances, healthcare, chemical engineers, aerospace, paper and food, among other industries.
Five principles are the basis of lean manufacturing:
-
Define value - Find out what your business contributes to society, and what makes it different from other competitors.
-
Reduce Waste - Remove any activity which doesn't add value to your supply chain.
-
Create Flow - Make sure work runs smoothly without interruptions.
-
Standardize and simplify - Make your processes as consistent as possible.
-
Build relationships - Develop and maintain personal relationships with both your internal and external stakeholders.
Lean manufacturing, although not new, has seen renewed interest in the economic sector since 2008. Many businesses have adopted lean manufacturing techniques to help them become more competitive. Some economists even believe that lean manufacturing can be a key factor in economic recovery.
Lean manufacturing is now becoming a common practice in the automotive industry, with many benefits. These include higher customer satisfaction levels, reduced inventory levels as well as lower operating costs.
Lean manufacturing can be applied to almost every aspect of an organization. This is because it ensures efficiency and effectiveness in all stages of the value chain.
There are three main types:
-
Just-in-Time Manufacturing (JIT): This type of lean manufacturing is commonly referred to as "pull systems." JIT is a process in which components can be assembled at the point they are needed, instead of being made ahead of time. This approach is designed to reduce lead times and increase the availability of components. It also reduces inventory.
-
Zero Defects Manufacturing, (ZDM): ZDM is focused on ensuring that no defective products leave the manufacturing facility. If a part is required to be repaired on the assembly line, it should not be scrapped. This is true even for finished products that only require minor repairs prior to shipping.
-
Continuous Improvement: Continuous Improvement aims to improve efficiency by continually identifying problems and making adjustments to eliminate or minimize waste. It involves continuous improvement of processes, people, and tools.