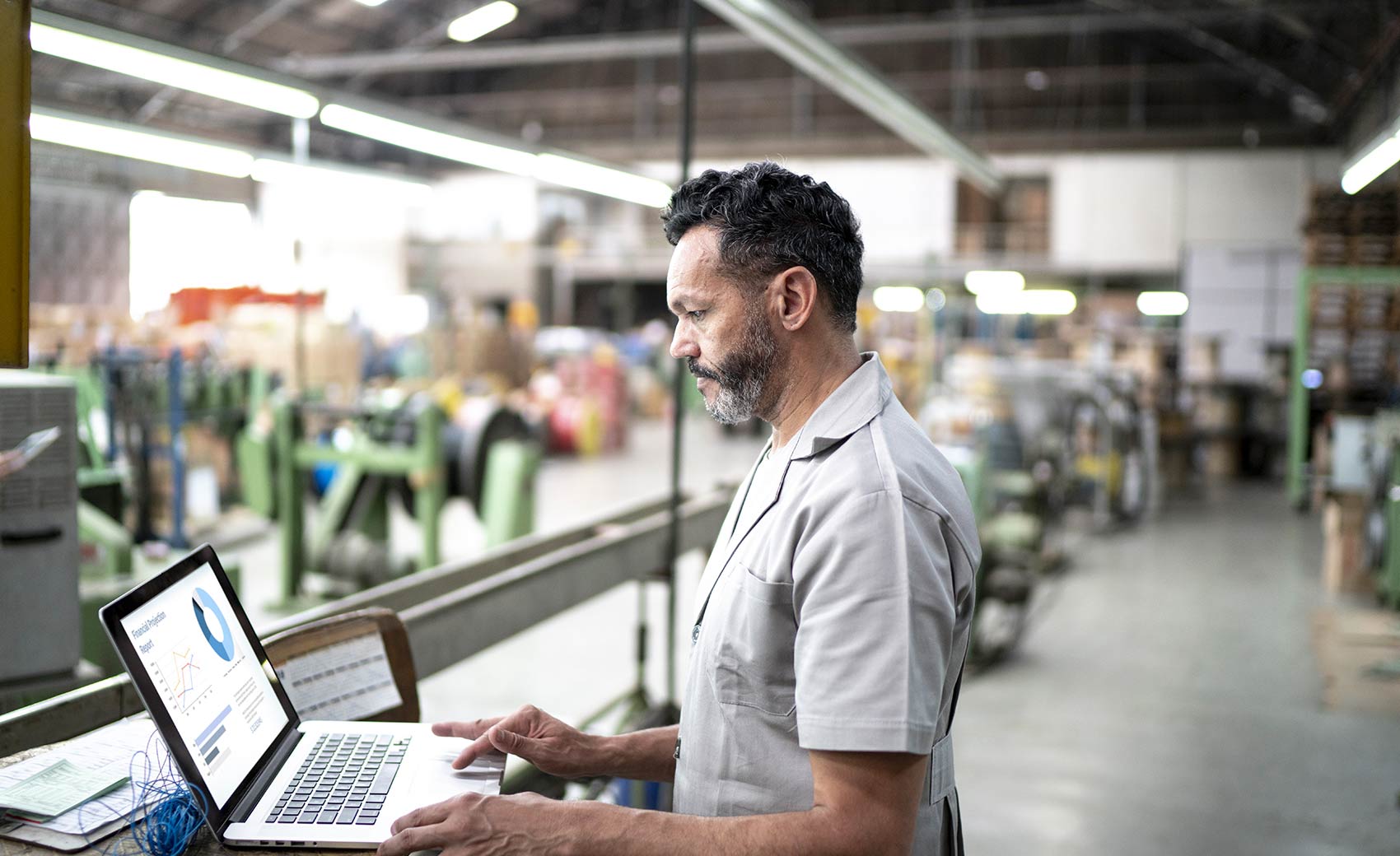
Several factors have caused a massive chip shortage in recent years. These include transportation issues and manufacturing problems. Many disasters have resulted in the closing of chip plant facilities. This has affected consumer electronics such as gaming consoles and data centers. The Chinese government has made many efforts to promote the manufacturing of semiconductors in China. The Chinese government has created an investment fund to aid chip manufacturers.
China's chip manufacturing industry has made great strides over the past few decades as a result. According to IC Insights, chip production in China is projected to grow by 19.4% by 2025. But the industry has a long way ahead of it before it reaches its former status. Despite these achievements, the number domestic chip companies remains small. Many of these companies have not yet become independent.
Huawei, Oppo (and Midea) are just a few of the top chip companies in China. Chinese companies are also increasing their market share in mobile processors. They are also creating their own chips, which allows them to increase their chip making capabilities. This has made them more attractive in the industry.
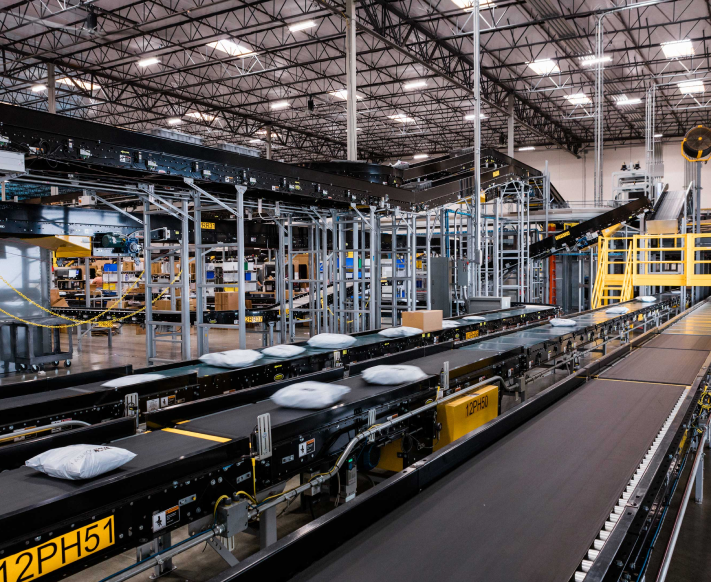
China is rapidly becoming a key chip manufacturing center, but there are still some limitations. Chinese companies have limited resources and are not able to mass-produce high end microchips. These chips are used in servers, smartphones, and wearable devices. Additionally, the country cannot yet produce its own raw materials for chip manufacturing. These include enriched isotopes, tantalum, and neon. These raw materials are processed chemically.
The Chinese government is also keen to decrease its dependence upon imported chips. China plans to produce 70% by 2025 of its chip production there. This will be difficult to achieve, however. China currently has 32 registered chip companies, many of which are still waiting for IPOs. The government actively markets its industrial policies. It hopes to encourage chip-producing companies to increase production, which is a challenging task considering the scarce resources.
The US semiconductor market is experiencing an unprecedented shortage. In addition, Washington recently passed new rules that restrict the ability of US persons to support chip production.
TSMC is one of the most important chipmakers in the world. However, it has not made any announcements yet about a new plant in Europe. But it has not ruled out building an older-generation chip plant there. To purchase lower-end chips, the company also partners with European automakers. The idea was largely rejected by European automakers. A European plant would expand the supply chain. However, chips would still need to be shipped to Asia for processing. This could prolong the life of the chip by several more years.
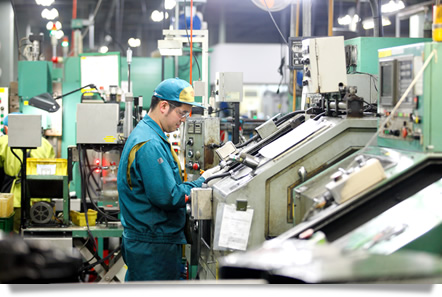
A report from the US Commerce Department states that the chip shortage could become severe in 2021. This has resulted in long delays for customers. The shortage also has impacted transportation, healthcare, gaming consoles, and other areas. However, the government's investments in reshoring chip production will help create hundreds of thousands of jobs in the US, and ensure a more resilient chip supply chain.
FAQ
Why should you automate your warehouse?
Modern warehouses have become more dependent on automation. E-commerce has brought increased demand for more efficient and quicker delivery times.
Warehouses must be able to quickly adapt to changing demands. Technology is essential for warehouses to be able to adapt quickly to changing needs. Automating warehouses is a great way to save money. Here are some of the reasons automation is worth your investment:
-
Increases throughput/productivity
-
Reduces errors
-
Improves accuracy
-
Safety increases
-
Eliminates bottlenecks
-
Companies can scale more easily
-
Increases efficiency of workers
-
Provides visibility into everything that happens in the warehouse
-
Enhances customer experience
-
Improves employee satisfaction
-
Reduces downtime and improves uptime
-
Ensures quality products are delivered on time
-
Eliminates human error
-
This helps to ensure compliance with regulations
What does "warehouse" mean?
A warehouse or storage facility is where goods are stored before they are sold. It can be an outdoor or indoor area. In some cases, it may be a combination of both.
What is the importance of logistics in manufacturing?
Logistics are an integral part any business. They can help you achieve great success by helping you manage product flow from raw material to finished goods.
Logistics play a key role in reducing expenses and increasing efficiency.
What are manufacturing & logistics?
Manufacturing is the act of producing goods from raw materials using machines and processes. Logistics encompasses the management of all aspects associated with supply chain activities such as procurement, production planning, distribution and inventory control. It also includes customer service. Logistics and manufacturing are often referred to as one thing. It encompasses both the creation of products and their delivery to customers.
How does a Production Planner differ from a Project Manager?
The primary difference between a producer planner and a manager of a project is that the manager usually plans and organizes the whole project, while a production planner is only involved in the planning stage.
What is the difference in Production Planning and Scheduling, you ask?
Production Planning (PP) is the process of determining what needs to be produced at any given point in time. Forecasting demand is one way to do this.
Scheduling refers the process by which tasks are assigned dates so that they can all be completed within the given timeframe.
What is the job of a manufacturer manager?
Manufacturing managers must ensure that manufacturing processes are efficient, effective, and cost-effective. They should be aware of any issues within the company and respond accordingly.
They should also know how to communicate with other departments such as sales and marketing.
They should be up to date on the latest trends and be able apply this knowledge to increase productivity and efficiency.
Statistics
- According to the United Nations Industrial Development Organization (UNIDO), China is the top manufacturer worldwide by 2019 output, producing 28.7% of the total global manufacturing output, followed by the United States, Japan, Germany, and India.[52][53] (en.wikipedia.org)
- Job #1 is delivering the ordered product according to specifications: color, size, brand, and quantity. (netsuite.com)
- It's estimated that 10.8% of the U.S. GDP in 2020 was contributed to manufacturing. (investopedia.com)
- Many factories witnessed a 30% increase in output due to the shift to electric motors. (en.wikipedia.org)
- In 2021, an estimated 12.1 million Americans work in the manufacturing sector.6 (investopedia.com)
External Links
How To
How to use Lean Manufacturing in the production of goods
Lean manufacturing is a management system that aims at increasing efficiency and reducing waste. It was developed in Japan between 1970 and 1980 by Taiichi Ohno. TPS founder Kanji Tyoda gave him the Toyota Production System, or TPS award. Michael L. Watkins published the "The Machine That Changed the World", the first book about lean manufacturing. It was published in 1990.
Lean manufacturing is often defined as a set of principles used to improve the quality, speed, and cost of products and services. It emphasizes the elimination of defects and waste throughout the value stream. Lean manufacturing is also known as just in time (JIT), zero defect total productive maintenance(TPM), and five-star (S). Lean manufacturing seeks to eliminate non-value added activities, such as inspection, work, waiting, and rework.
Lean manufacturing not only improves product quality but also reduces costs. Companies can also achieve their goals faster by reducing employee turnover. Lean manufacturing can be used to manage all aspects of the value chain. Customers, suppliers, distributors, retailers and employees are all included. Lean manufacturing can be found in many industries. Toyota's philosophy has been a key driver of success in many industries, including automobiles and electronics.
Five basic principles of Lean Manufacturing are included in lean manufacturing
-
Define Value: Identify the social value of your business and what sets you apart.
-
Reduce waste - Get rid of any activity that does not add value to the supply chain.
-
Create Flow – Ensure that work flows smoothly throughout the process.
-
Standardize & simplify - Make processes consistent and repeatable.
-
Build Relationships- Develop personal relationships with both internal as well as external stakeholders.
Although lean manufacturing has always been around, it is gaining popularity in recent years because of a renewed interest for the economy after 2008's global financial crisis. Many businesses are now using lean manufacturing to improve their competitiveness. Economists think that lean manufacturing is a crucial factor in economic recovery.
With many benefits, lean manufacturing is becoming more common in the automotive industry. These include improved customer satisfaction, reduced inventory levels, lower operating costs, increased productivity, and better overall safety.
It can be applied to any aspect of an organisation. It is especially useful for the production aspect of an organization, as it ensures that every step in the value chain is efficient and effective.
There are three main types in lean manufacturing
-
Just-in Time Manufacturing (JIT), also known as "pull system": This form of lean manufacturing is often referred to simply as "pull". JIT is a process in which components can be assembled at the point they are needed, instead of being made ahead of time. This strategy aims to decrease lead times, increase availability of parts and reduce inventory.
-
Zero Defects Manufacturing: ZDM ensures that no defective units leave the manufacturing plant. Repairing a part that is damaged during assembly should be done, not scrapping. This applies to finished goods that may require minor repairs before shipment.
-
Continuous Improvement (CI): CI aims to improve the efficiency of operations by continuously identifying problems and making changes in order to eliminate or minimize waste. Continuous Improvement (CI) involves continuous improvement in processes, people, tools, and infrastructure.