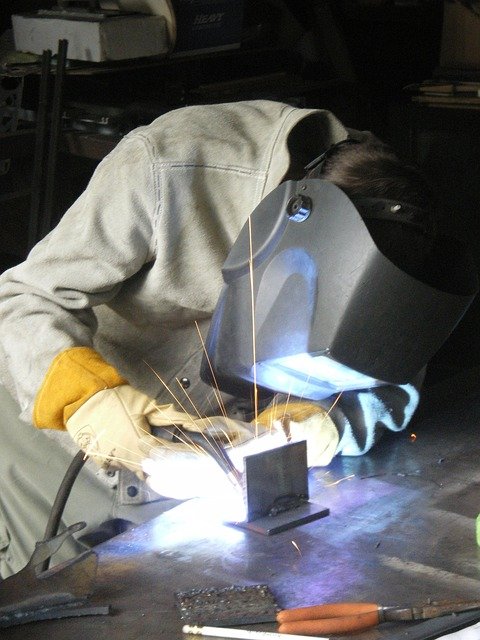
Structural engineers have one of the highest salaries, compared to other professions. The demand for structural engineering professionals is a major factor in the salaries. A bachelor's degree is usually required for structural engineers. They should also have at least one year of experience in this field. They could work for a utility company, engineering consulting firm, or construction company. Some structural engineers may even set up their own company.
Structural Engineers design structures that can withstand severe stresses. They need to be familiar with the properties and limitations of various materials. They may also be asked to participate in competitive bidding. They need to have project management and communication skills. They will also need to be proficient in computer programming. Sometimes they may have to work extra hours to meet deadlines. They may also be able to travel for clients projects that are not in their immediate area.
Most structural engineers work full time. But they can also work nights and weekends. Employees who work for companies will have access to company cars and extended health care benefits. They might also be eligible to participate in an employee share-ownership plan. An engineer who is a structural engineer may be able to increase his or her income by switching employers or getting an advanced degree. The annual salary range for structural engineers is $59,000 to $108,000.
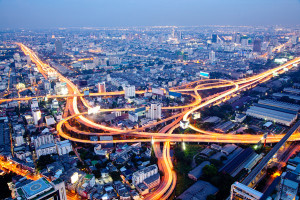
The salaries of structural engineers in the United States vary from one city to another. In San Francisco, structural engineers make a total of $147,822 a year. The second highest salary is in District of Columbia, where the average salary is $146,683. The third highest salary is in Deer Park, CA, where the average salary is $111,562.
Norway's average structure engineer salary is kr 755206. However, the average salary for structural engineers in Oslo is 8% less than in Norway. The cost of living also influences the salary of structural engineer.
From Monday to Friday, structural engineers typically work between 9:00 and 5:00. They can also work nights, weekends, and holidays. Sometimes they may visit construction sites to inspect the work. They will need the ability to communicate their designs with clients. They will also need to know how to use computer-aided modeling (CAD) software to visualize the final parts.
A structural engineer can also work as an assistant to an experienced engineer. They will need to go through supervised training before being able to work independently. You can also get certified as a structural engineer through an apprenticeship program. They must have at minimum four years experience in the field. Once they have acquired sufficient experience, they can begin applying directly to employers.

As a rule, structural engineers earn $42 an hour. As a structural engineer your salary may increase if the work you do is hard and you get more experience. Senior structural engineers make the most of their positions. The Institution of StructE recognizes excellence in this field and you can become a member.
The total compensation of a structural engineer includes his or her salary, bonus, and profit sharing. The average bonus is $3179
FAQ
What is meant by manufacturing industries?
Manufacturing Industries is a group of businesses that produce goods for sale. These products are sold to consumers. These companies employ many processes to achieve this purpose, such as production and distribution, retailing, management and so on. They create goods from raw materials, using machines and various other equipment. This includes all types if manufactured goods.
Why should you automate your warehouse?
Modern warehouses are increasingly dependent on automation. E-commerce has brought increased demand for more efficient and quicker delivery times.
Warehouses must be able to quickly adapt to changing demands. They must invest heavily in technology to do this. Automating warehouses is a great way to save money. Here are some benefits of investing in automation
-
Increases throughput/productivity
-
Reduces errors
-
Improves accuracy
-
Boosts safety
-
Eliminates bottlenecks
-
This allows companies to scale easily
-
Workers are more productive
-
It gives visibility to everything that happens inside the warehouse
-
Enhances customer experience
-
Improves employee satisfaction
-
Reducing downtime and increasing uptime
-
You can be sure that high-quality products will arrive on time
-
Human error can be eliminated
-
This helps to ensure compliance with regulations
Can some manufacturing processes be automated?
Yes! Yes! Automation has existed since ancient times. The Egyptians invented the wheel thousands of years ago. Robots are now used to assist us in assembly lines.
In fact, there are several applications of robotics in manufacturing today. These include:
-
Automation line robots
-
Robot welding
-
Robot painting
-
Robotics inspection
-
Robots that make products
Manufacturing can also be automated in many other ways. For instance, 3D printing allows us make custom products and not have to wait for months or even weeks to get them made.
Is automation necessary in manufacturing?
Automation is essential for both manufacturers and service providers. It allows them provide faster and more efficient services. It also helps to reduce costs and improve productivity.
What are the 7 Rs of logistics?
The 7R's of Logistics is an acronym for the seven basic principles of logistics management. It was developed and published by the International Association of Business Logisticians in 2004 as part of the "Seven Principles of Logistics Management".
The following letters make up the acronym:
-
Responsible - ensure that actions are in compliance with legal requirements and do not cause harm to others.
-
Reliable - You can have confidence that you will fulfill your promises.
-
Reasonable - make sure you use your resources well and don't waste them.
-
Realistic – Consider all aspects, including cost-effectiveness as well as environmental impact.
-
Respectful – Treat others fairly and equitably.
-
You are resourceful and look for ways to save money while increasing productivity.
-
Recognizable: Provide customers with value-added service
How can manufacturing efficiency be improved?
First, determine which factors have the greatest impact on production time. We must then find ways that we can improve these factors. You can start by identifying the most important factors that impact production time. Once you have identified the factors, then try to find solutions.
Statistics
- Many factories witnessed a 30% increase in output due to the shift to electric motors. (en.wikipedia.org)
- Job #1 is delivering the ordered product according to specifications: color, size, brand, and quantity. (netsuite.com)
- In 2021, an estimated 12.1 million Americans work in the manufacturing sector.6 (investopedia.com)
- You can multiply the result by 100 to get the total percent of monthly overhead. (investopedia.com)
- According to the United Nations Industrial Development Organization (UNIDO), China is the top manufacturer worldwide by 2019 output, producing 28.7% of the total global manufacturing output, followed by the United States, Japan, Germany, and India.[52][53] (en.wikipedia.org)
External Links
How To
How to Use Lean Manufacturing for the Production of Goods
Lean manufacturing is a management system that aims at increasing efficiency and reducing waste. It was first developed in Japan in the 1970s/80s by Taiichi Ahno, who was awarded the Toyota Production System (TPS), award from KanjiToyoda, the founder of TPS. The first book published on lean manufacturing was titled "The Machine That Changed the World" written by Michael L. Watkins and published in 1990.
Lean manufacturing, often described as a set and practice of principles, is aimed at improving the quality, speed, cost, and efficiency of products, services, and other activities. It emphasizes reducing defects and eliminating waste throughout the value chain. The five-steps of Lean Manufacturing are just-in time (JIT), zero defect and total productive maintenance (TPM), as well as 5S. Lean manufacturing emphasizes reducing non-value-added activities like inspection, rework and waiting.
Lean manufacturing not only improves product quality but also reduces costs. Companies can also achieve their goals faster by reducing employee turnover. Lean Manufacturing is one of the most efficient ways to manage the entire value chains, including suppliers and customers as well distributors and retailers. Lean manufacturing is widely practiced in many industries around the world. For example, Toyota's philosophy underpins its success in automobiles, electronics, appliances, healthcare, chemical engineering, aerospace, paper, food, etc.
Five fundamental principles underlie lean manufacturing.
-
Define Value- Identify the added value your company brings to society. What makes you stand out from your competitors?
-
Reduce Waste - Remove any activity which doesn't add value to your supply chain.
-
Create Flow – Ensure that work flows smoothly throughout the process.
-
Standardize & simplify - Make processes consistent and repeatable.
-
Develop Relationships: Establish personal relationships both with internal and external stakeholders.
Although lean manufacturing isn't a new concept in business, it has gained popularity due to renewed interest in the economy after the 2008 global financial crisis. Many businesses are now using lean manufacturing to improve their competitiveness. Economists think that lean manufacturing is a crucial factor in economic recovery.
With many benefits, lean manufacturing is becoming more common in the automotive industry. These include higher customer satisfaction, lower inventory levels, lower operating expenses, greater productivity, and improved overall safety.
Any aspect of an enterprise can benefit from Lean manufacturing. This is because it ensures efficiency and effectiveness in all stages of the value chain.
There are three main types of lean manufacturing:
-
Just-in Time Manufacturing: This lean manufacturing method is commonly called "pull systems." JIT stands for a system where components are assembled on the spot rather than being made in advance. This method reduces lead times, increases availability, and decreases inventory.
-
Zero Defects Manufacturing: ZDM ensures that no defective units leave the manufacturing plant. It is better to repair a part than have it removed from the production line if it needs to be fixed. This applies to finished products, which may need minor repairs before they are shipped.
-
Continuous Improvement (CI: Continuous improvement aims to increase the efficiency of operations by constantly identifying and making improvements to reduce or eliminate waste. Continuous improvement involves continuous improvement of processes and people as well as tools.