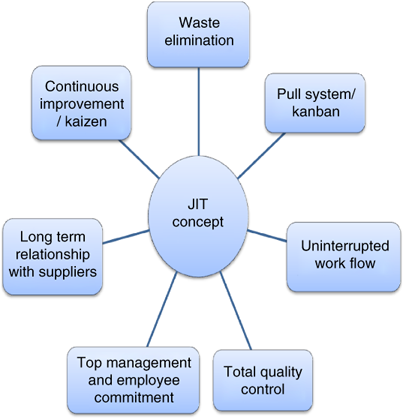
OEE stands for Overall Equipment Effectiveness. It is a method of evaluating the equipment's performance. This article will discuss the definition of OEE as well as how to calculate it. It is a best practice indicator that is based upon Availability, Performance and Quality. OEE helps improve manufacturing efficiency by decreasing downtime, increasing production, and reducing costs. It can also help manufacturers save money.
OEE is a labor efficiency metric
OEE is an indicator of overall production quality. It is based on an interaction of availability, quality, and performance. OEE losses are lost time due to inconsistency in production. These include time down, rate drops in the process and scrap.
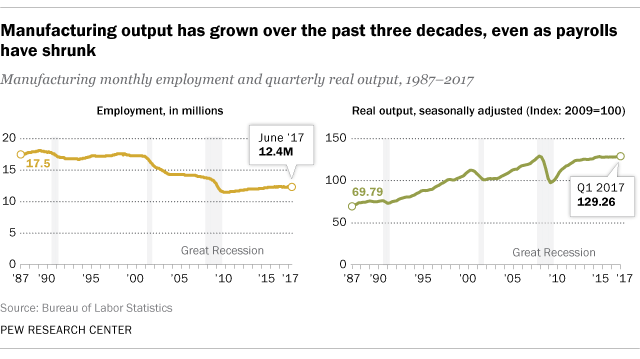
It is based on Availability, Performance and Quality
OEE (Optimum Equipment Efficiency) is a production management strategy that emphasizes quality, performance, and availability. Availability refers to the time that a product, service or other item is available for purchase or use. For example, it may be defined as the time between delivery to a customer and recovery, or the time in between scrapping and repair. Performance directly relates to the quality and performance of a business. Hiring a professional company to assess your business process and offer suggestions for improvement is an effective way to measure it.
It is a best practices measure
OEE can be used to improve and measure your operation. This metric allows you to analyze different levels of your operations, which can help you reduce waste and improve your operations. However, it is important to note that it cannot be used as an end-all-be-all metric. This means you shouldn't launch an OEE improvement programme without first piloting it.
It is a directional indicator
In addition to defining its exact definition, OEE is also a directional metric that is used to compare the performance of similar types of machines across a company. Companies can measure this metric consistently across all their machines to see if they are improving their machine efficiency.
It is a TPM measure
The overall equipment effectiveness (OEE) metric is a useful tool for analyzing production efficiency. It measures production inefficiencies and losses in three key areas: availability and performance. It can be used as a metric to track and identify areas for improvement.
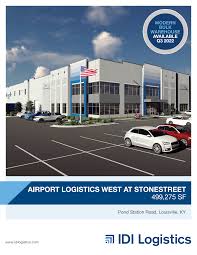
It is a best manufacturing practice
OEE is an acronym for overall equipment effectiveness. OEE is the ratio between what a machine/cell can produce in a certain time and how long it takes to actually produce that product. The goal is to maximize OEE and reduce downtime. As a result, manufacturing operations can improve quality and reduce costs.
FAQ
What does manufacturing industry mean?
Manufacturing Industries are those businesses that make products for sale. These products are sold to consumers. These companies use a variety processes such as distribution, retailing and management to accomplish their purpose. They manufacture goods from raw materials using machines and other equipment. This includes all types manufactured goods such as clothing, building materials, furniture, electronics, tools and machinery.
How can I find out more about manufacturing?
You can learn the most about manufacturing by getting involved in it. You can also read educational videos or take classes if this isn't possible.
What is the responsibility of a production planner?
A production planner makes sure all project elements are delivered on schedule, within budget, as well as within the agreed scope. They ensure that the product or service is of high quality and meets client requirements.
What jobs are available in logistics?
There are many kinds of jobs available within logistics. Some of them are:
-
Warehouse workers - They load trucks and pallets.
-
Transportation drivers: They drive trucks and trailers and deliver goods and make pick-ups.
-
Freight handlers, - They sort out and pack freight in warehouses.
-
Inventory managers – These people oversee inventory at warehouses.
-
Sales reps are people who sell products to customers.
-
Logistics coordinators - They plan and organize logistics operations.
-
Purchasing agents: They are responsible for purchasing goods and services to support company operations.
-
Customer service representatives – They answer emails and phone calls from customers.
-
Shippers clerks - They process shipping order and issue bills.
-
Order fillers - These people fill orders based on what has been ordered.
-
Quality control inspectors – They inspect incoming and outgoing products to ensure that there are no defects.
-
Others - There is a variety of other jobs in logistics. These include transportation supervisors and cargo specialists.
Statistics
- In 2021, an estimated 12.1 million Americans work in the manufacturing sector.6 (investopedia.com)
- It's estimated that 10.8% of the U.S. GDP in 2020 was contributed to manufacturing. (investopedia.com)
- (2:04) MTO is a production technique wherein products are customized according to customer specifications, and production only starts after an order is received. (oracle.com)
- According to a Statista study, U.S. businesses spent $1.63 trillion on logistics in 2019, moving goods from origin to end user through various supply chain network segments. (netsuite.com)
- Many factories witnessed a 30% increase in output due to the shift to electric motors. (en.wikipedia.org)
External Links
How To
Six Sigma and Manufacturing
Six Sigma refers to "the application and control of statistical processes (SPC) techniques in order to achieve continuous improvement." Motorola's Quality Improvement Department developed it at their Tokyo plant in Japan in 1986. Six Sigma's basic concept is to improve quality and eliminate defects through standardization. In recent years, many companies have adopted this method because they believe there is no such thing as perfect products or services. Six Sigma seeks to reduce variation between the mean production value. This means that you can take a sample from your product and then compare its performance to the average to find out how often the process differs from the norm. If you notice a large deviation, then it is time to fix it.
Understanding the dynamics of variability within your business is the first step in Six Sigma. Once you have this understanding, you will need to identify sources and causes of variation. These variations can also be classified as random or systematic. Random variations are caused by human errors. Systematic variations can be caused by outside factors. If you make widgets and some of them end up on the assembly line, then those are considered random variations. But if you notice that every widget you make falls apart at the exact same place each time, this would indicate that there is a problem.
Once you identify the problem areas, it is time to create solutions. That solution might involve changing the way you do things or redesigning the process altogether. To verify that the changes have worked, you need to test them again. If they don't work, you will need to go back to the drawing boards and create a new plan.