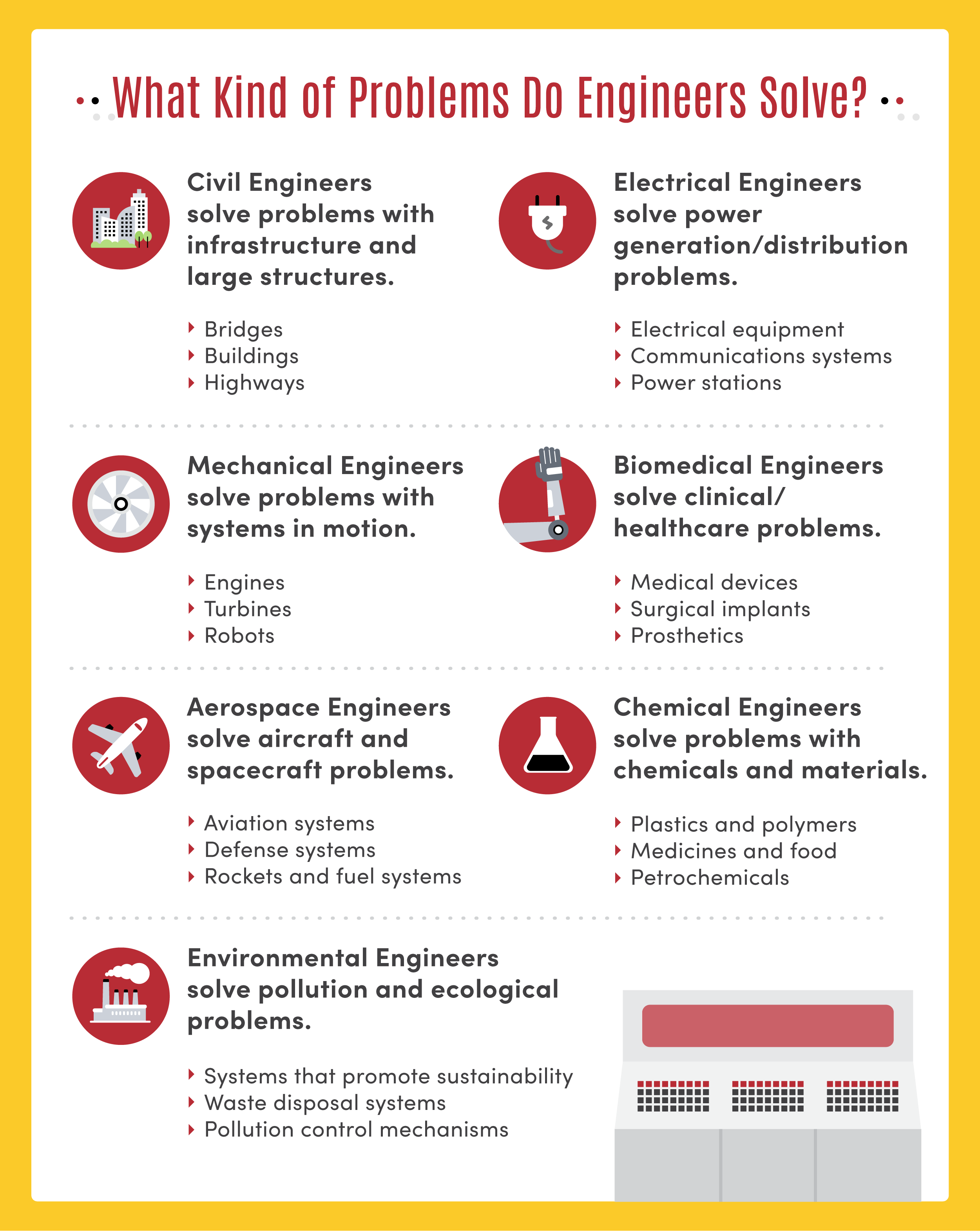
Toyota Production System, originally called Just-in-Time production was an integrated sociotechnical and technological system used to eliminate waste from processes and improve them. It is used to organize manufacturing, logistics, as well as customer interaction. It drives continuous improvement as well as employee development. It is also the foundation for Lean Manufacturing. Numerous manufacturing facilities, both in the United States of America and overseas, have adopted the Toyota Production System.
SakichiToyoda was the creator of Toyota's Production System. Sakichi Toyoda studied each production stage of his company and eliminated unnecessary parts. This resulted in a 20% decrease in build time. Toyota could also produce a vehicle in half of the time as GM. Toyota was however on the verge to go bankrupt in the 1950s.
Taiichi Okno, Toyota's executive in the mid-1940s observed the stocking process at a supermarket. He realized that using Just-in-Time methods in vehicle production could save time. He collaborated with EijiToyoda, Toyota's president, to develop the Toyota Production System in 1948-1975.
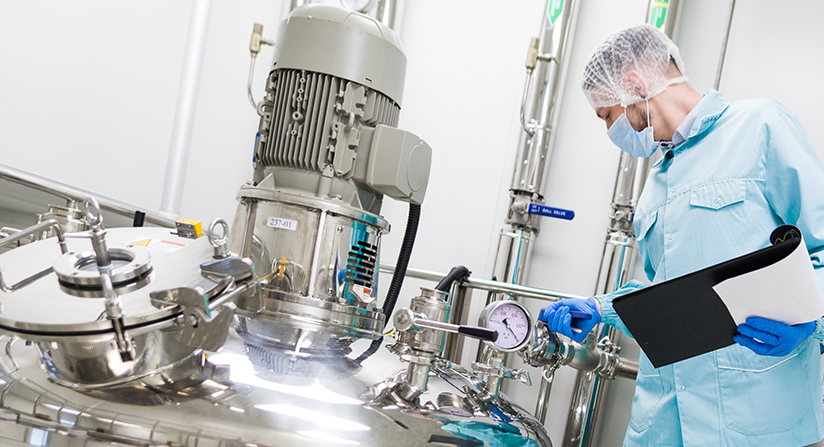
The Toyota Production System was designed to eliminate waste and inconsistency. Kaizen, the Japanese word for continuous improvement, was the underlying philosophy of the Toyota Production System. Toyota's Production System is continually improved to meet company needs. It is a learning system that drives the company's progress. It uses low-tech, yet efficient tools and advanced production techniques. It also employs advanced information technology, as well as unique social/management methods.
Six core principles are the basis of Toyota Production System. It has been used by many companies such as Boeing, Porsche, Honda, and others. These companies have reengineered their processes to replicate Toyota's production process.
Toyota Production System includes activities for team building. These activities include weekly safety rounds for local leaders that assess staff performance in key safety initiatives. Everyone is encouraged to contribute ideas and identify opportunities for improvement. This has changed the culture of the company.
Jidoka refers to the automation of processes with a human touch. Jidoka encourages workers and managers to review their work and stop making changes when they see problems. Jidoka stresses the importance of correcting mistakes and not ignoring them.
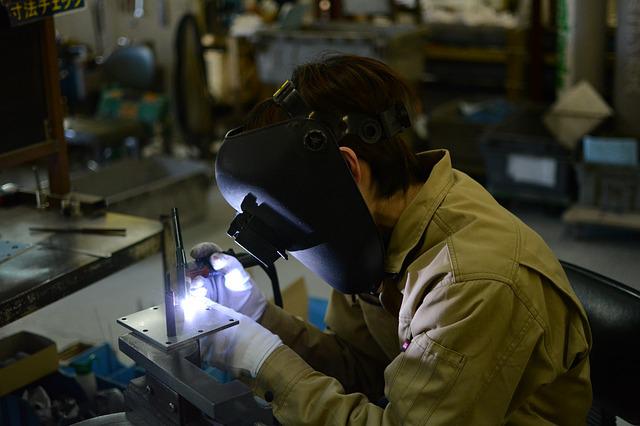
Visual control is an integral part of the Toyota Production System. It makes work instructions visible on the factory floor. This helps workers follow instructions precisely. The company also uses poka-yoke devices to verify quality standards. These devices can also be used for identifying red rabbits.
Toyota Production System does not just apply to manufacturing, but also to health care. It can be used by patients to improve their satisfaction. It can be used in critical care and the operating rooms.
Using the Toyota Production System, it is possible to improve patient satisfaction and health care delivery. In 2003, the EPA published a case report that highlighted the EPA's interest in Toyota's achievements in waste reduction. This led to several partnerships with companies including the St. Bernard Project, which employs military vets.
FAQ
Is automation important in manufacturing?
Automation is essential for both manufacturers and service providers. It allows them to offer services faster and more efficiently. They can also reduce their costs by reducing human error and improving productivity.
What are the 4 types of manufacturing?
Manufacturing refers to the transformation of raw materials into useful products by using machines and processes. It includes many different activities like designing, building and testing, packaging, shipping and selling, as well as servicing.
What is the role of a manager in manufacturing?
Manufacturing managers must ensure that manufacturing processes are efficient, effective, and cost-effective. They should also be aware and responsive to any company problems.
They should also learn how to communicate effectively with other departments, including sales and marketing.
They should also be aware of the latest trends in their industry and be able to use this information to help improve productivity and efficiency.
What does it take for a logistics enterprise to succeed?
You need to have a lot of knowledge and skills to manage a successful logistic business. To communicate effectively with clients and suppliers, you must be able to communicate well. You need to understand how to analyze data and draw conclusions from it. You need to be able work under pressure and manage stressful situations. You need to be innovative and creative to come up with new ways to increase efficiency. Strong leadership qualities are essential to motivate your team and help them achieve their organizational goals.
It is important to be organized and efficient in order to meet tight deadlines.
What does the term manufacturing industries mean?
Manufacturing Industries is a group of businesses that produce goods for sale. Consumers are those who purchase these products. These companies use a variety processes such as distribution, retailing and management to accomplish their purpose. These companies produce goods using raw materials and other equipment. This covers all types of manufactured goods including clothing, food, building supplies and furniture, as well as electronics, tools, machinery, vehicles and pharmaceuticals.
Statistics
- According to a Statista study, U.S. businesses spent $1.63 trillion on logistics in 2019, moving goods from origin to end user through various supply chain network segments. (netsuite.com)
- Many factories witnessed a 30% increase in output due to the shift to electric motors. (en.wikipedia.org)
- In the United States, for example, manufacturing makes up 15% of the economic output. (twi-global.com)
- In 2021, an estimated 12.1 million Americans work in the manufacturing sector.6 (investopedia.com)
- According to the United Nations Industrial Development Organization (UNIDO), China is the top manufacturer worldwide by 2019 output, producing 28.7% of the total global manufacturing output, followed by the United States, Japan, Germany, and India.[52][53] (en.wikipedia.org)
External Links
How To
How to Use the Just-In-Time Method in Production
Just-in-time is a way to cut costs and increase efficiency in business processes. It is a process where you get the right amount of resources at the right moment when they are needed. This means that only what you use is charged to your account. Frederick Taylor developed the concept while working as foreman in early 1900s. He observed how workers were paid overtime if there were delays in their work. He realized that workers should have enough time to complete their jobs before they begin work. This would help increase productivity.
JIT is a way to plan ahead and make sure you don't waste any money. Look at your entire project, from start to end. Make sure you have enough resources in place to deal with any unexpected problems. You can anticipate problems and have enough equipment and people available to fix them. This way you won't be spending more on things that aren’t really needed.
There are many JIT methods.
-
Demand-driven: This JIT is where you place regular orders for the parts/materials that are needed for your project. This will allow to track how much material has been used up. You'll also be able to estimate how long it will take to produce more.
-
Inventory-based: You stock materials in advance to make your projects easier. This allows one to predict how much they will sell.
-
Project-driven: This method allows you to set aside enough funds for your project. You will be able to purchase the right amount of materials if you know what you need.
-
Resource-based: This is the most common form of JIT. You allocate resources based on the demand. You will, for example, assign more staff to deal with large orders. If you don't have many orders, you'll assign fewer people to handle the workload.
-
Cost-based: This is similar to resource-based, except that here you're not just concerned about how many people you have but how much each person costs.
-
Price-based: This is very similar to cost-based, except that instead of looking at how much each individual worker costs, you look at the overall price of the company.
-
Material-based: This approach is similar to cost-based. However, instead of looking at the total cost for the company, you look at how much you spend on average on raw materials.
-
Time-based: This is another variation of resource-based JIT. Instead of focusing on the cost of each employee, you will focus on the time it takes to complete a project.
-
Quality-based JIT - This is another form of resource-based JIT. Instead of focusing on the cost of each worker or how long it takes, think about how high quality your product is.
-
Value-based JIT : This is the newest type of JIT. You don't worry about whether the products work or if they meet customer expectations. Instead, you're focused on how much value you add to the market.
-
Stock-based: This stock-based method focuses on the actual quantity of products being made at any given time. It's used when you want to maximize production while minimizing inventory.
-
Just-in-time planning (JIT): This is a combination JIT and supply-chain management. It's the process of scheduling delivery of components immediately after they are ordered. This is important as it reduces lead time and increases throughput.