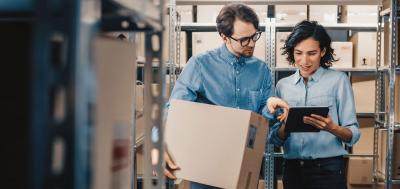
A blue collar job is generally a manual labor job. These jobs might be in the fields of agriculture, manufacturing, healthcare or hospitality. While some jobs may require some level of skill (e.g., plumbers or electricians), others may not. Blue collar jobs are good for career growth and pay decent salaries.
The Fourth Industrial Revolution has the potential to transform the labour market for manual workers. This revolution includes artificial intelligence, robotics, machine learning, and 3D printing. For companies to succeed, it will require a skilled workforce. It will also require that firms shift away from transactional relations and move towards more enduring relationships.
Therefore, many companies have to hire workers outside the United States. In certain cases, these workers may also be paid per-item. Others may be paid by the project. In any case, the rise in demand for blue collar jobs is encouraging.
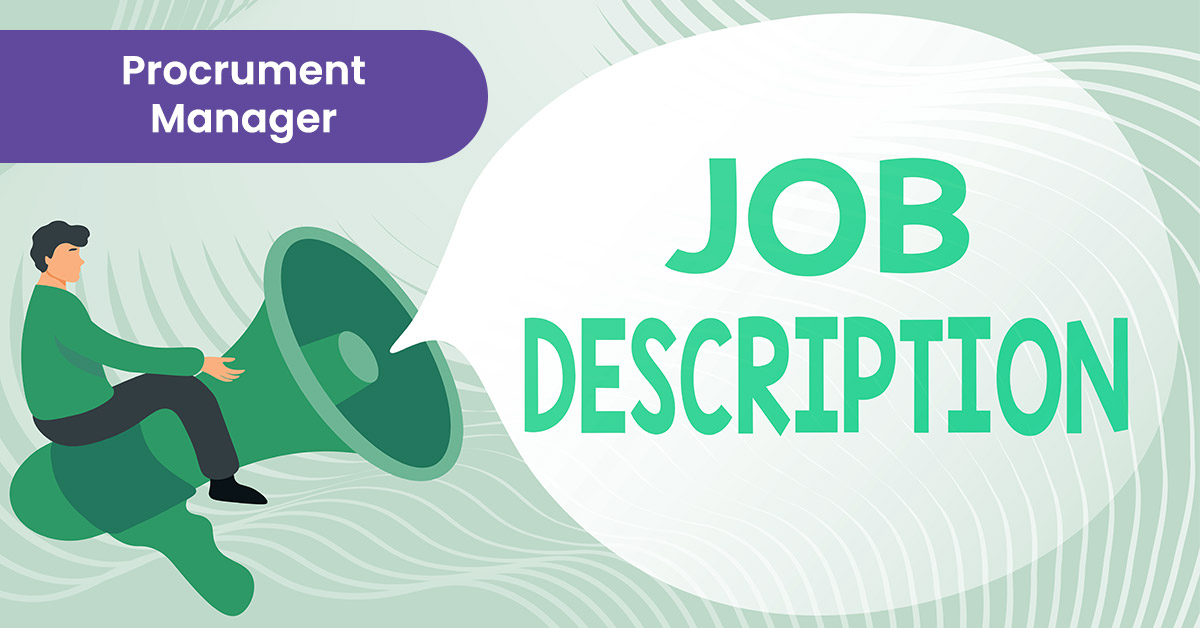
Although these jobs require some degree of physical labor, they are considered to be better paid than white collar jobs. These jobs provide a steady income source and companies are prepared to invest in training employees. There are many examples of these jobs, including signal and track switches repairers and nuclear power plant operators. These jobs can be done with a high school diploma. Others require additional training.
There are also more blue collar jobs than there are white collar ones. The majority of Indian workforce is made up of blue collar workers. India has 210 million workers in the agricultural sector, and 290 million in the non-agricultural sector. The demand for blue collar workers is growing at a rapid pace.
Companies are changing how they manage their blue collar workforce through the Fourth Industrial Revolution. Firms are not only replacing manual jobs with digital jobs, but they also shift away from transactional relationships towards lasting ones. Firms are better able to create stronger relationships and improve productivity by prioritizing the needs of employees.
While blue collar workers are in high demand, they also face other realities. They may be worried about the stability of their jobs, or about retiring. Blue collar workers are optimistic about their future, regardless of their concerns. The percentage of blue-collar workers who are saving for retirement is actually increasing. Blue collar jobs will continue to grow in popularity as the economy recovers.
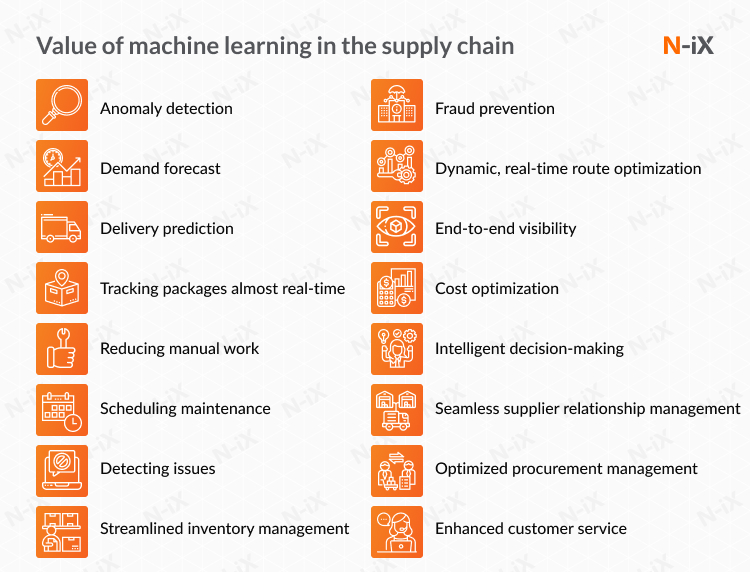
These jobs are also not in danger from automation. The Association for Manufacturing Technology has found that for every job that is replaced by technology there are five new jobs. Signal and track switch repairers earned $76,210 an average salary, which was the largest increase in salaries.
In addition to being more lucrative, blue collar positions are also becoming more popular. Many blue collar jobs earn much more than the national average. This makes them an attractive option for anyone looking for a high-paying job. In addition, many blue collar jobs require a high degree of problem-solving skills, and are more than likely to provide good career growth.
FAQ
What is the difference between Production Planning and Scheduling?
Production Planning (PP) is the process of determining what needs to be produced at any given point in time. This can be done by forecasting demand and identifying production capabilities.
Scheduling refers the process by which tasks are assigned dates so that they can all be completed within the given timeframe.
What are manufacturing and logistics?
Manufacturing is the production of goods using raw materials. Logistics includes all aspects related to supply chain management, such as procurement, distribution planning, inventory control and transportation. Manufacturing and logistics are often considered together as a broader term that encompasses both the process of creating products and delivering them to customers.
Why should you automate your warehouse?
Automation has become increasingly important in modern warehousing. E-commerce has increased the demand for quicker delivery times and more efficient processes.
Warehouses should be able adapt quickly to new needs. To do so, they must invest heavily in technology. Automation warehouses can bring many benefits. These are some of the benefits that automation can bring to warehouses:
-
Increases throughput/productivity
-
Reduces errors
-
Accuracy is improved
-
Safety increases
-
Eliminates bottlenecks
-
Allows companies scale more easily
-
It makes workers more efficient
-
It gives visibility to everything that happens inside the warehouse
-
Enhances customer experience
-
Improves employee satisfaction
-
Reduces downtime and improves uptime
-
High quality products delivered on-time
-
Removing human error
-
Helps ensure compliance with regulations
Statistics
- Job #1 is delivering the ordered product according to specifications: color, size, brand, and quantity. (netsuite.com)
- In the United States, for example, manufacturing makes up 15% of the economic output. (twi-global.com)
- [54][55] These are the top 50 countries by the total value of manufacturing output in US dollars for its noted year according to World Bank.[56] (en.wikipedia.org)
- (2:04) MTO is a production technique wherein products are customized according to customer specifications, and production only starts after an order is received. (oracle.com)
- It's estimated that 10.8% of the U.S. GDP in 2020 was contributed to manufacturing. (investopedia.com)
External Links
How To
Six Sigma: How to Use it in Manufacturing
Six Sigma is defined as "the application of statistical process control (SPC) techniques to achieve continuous improvement." Motorola's Quality Improvement Department in Tokyo, Japan developed Six Sigma in 1986. The basic idea behind Six Sigma is to improve quality by improving processes through standardization and eliminating defects. In recent years, many companies have adopted this method because they believe there is no such thing as perfect products or services. The main goal of Six Sigma is to reduce variation from the mean value of production. You can calculate the percentage of deviation from the norm by taking a sample of your product and comparing it to the average. If you notice a large deviation, then it is time to fix it.
Understanding how variability works in your company is the first step to Six Sigma. Once you understand that, it is time to identify the sources of variation. It is important to identify whether the variations are random or systemic. Random variations occur when people make mistakes; systematic ones are caused by factors outside the process itself. Random variations would include, for example, the failure of some widgets to fall from the assembly line. However, if you notice that every time you assemble a widget, it always falls apart at exactly the same place, then that would be a systematic problem.
Once you've identified where the problems lie, you'll want to design solutions to eliminate those problems. It might mean changing the way you do business or redesigning it entirely. Once you have implemented the changes, it is important to test them again to ensure they work. If they don’t work, you’ll need to go back and rework the plan.