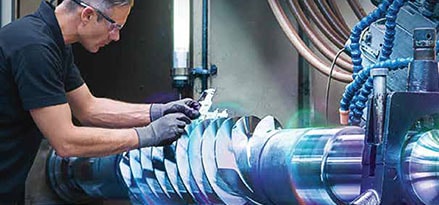
It may be more difficult than you think to introduce kaizen to manufacturing processes. The process is slow, requires time to procure inventory and ensure that all hands are on deck. The time required for this improvement process varies with the firm, problem area and level of participation. Be sure to follow the right methods of implementation and gather the necessary resources in order to make your manufacturing improvement initiative a success. For this strategy to be successful, it is important to establish a strong company culture encouraging continuous improvement.
A company culture that focuses on improvement
Gallup polls indicate that only 32% American workers are engaged in their jobs. 17.2% of these employees were actively disengaged. Kaizen culture can be implemented to encourage employee engagement. This will lead to improved processes, lower turnover, and more innovation. Engaged employees will be more open to new ideas and innovative thinking, which leads to increased productivity and customer satisfaction. The benefits of a Kaizen culture go beyond reducing waste and boosting productivity.
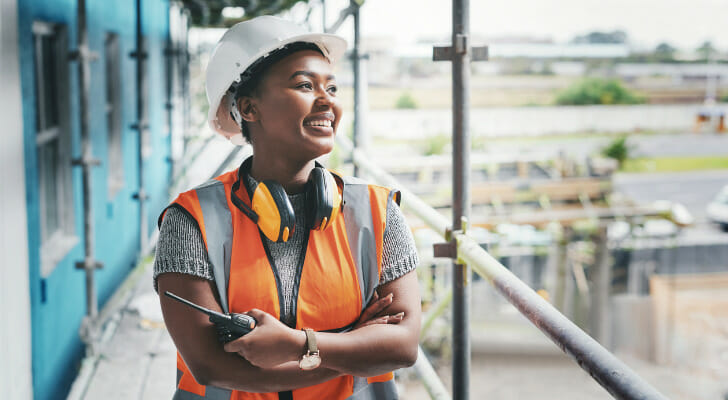
Kaizen stands for continuous improvement in all aspects of a company's business. Kaizen is not about making large-scale changes that aren't beneficial, but incremental improvements. Kaizen is a process that can improve customer satisfaction, productivity, quality, and costs. The philosophy is also effective in improving employee morale and communication.
There are many obstacles to implementing Kaizen in manufacturing
While the benefits of implementing kaizen are many, they also have some disadvantages. First, the implementation of kaizen can require major changes to a business's managerial system. It may be difficult to reverse changes once they are made. Second, it is often difficult for businesses to make changes to their work processes, which could be a barrier to kaizen implementation.
Another common obstacle is that many manufacturers operate on a "feast or famine" cycle. A machine shop could run into difficulties if there isn't enough demand for the products they produce or enough qualified people to fill their positions. In such a situation, they'll have to lay off employees and close their doors. Implementing kaizen (continuous improvement) will keep these machine shops from falling into the "feast or feast" cycle. Kaizen is a way to increase efficiency in a shop and produce more products.
Kaizen implementation success rate in manufacturing
Statistics show that Kaizen implementation is not very successful in the manufacturing sector. Only 10% manufacturing firms reported positive Kaizen results. However, that does not make the Kaizen implementation useless. Implementing kaizen is an essential component of the lean manufacturing process. Here are some tips to increase your manufacturing business's success rate:
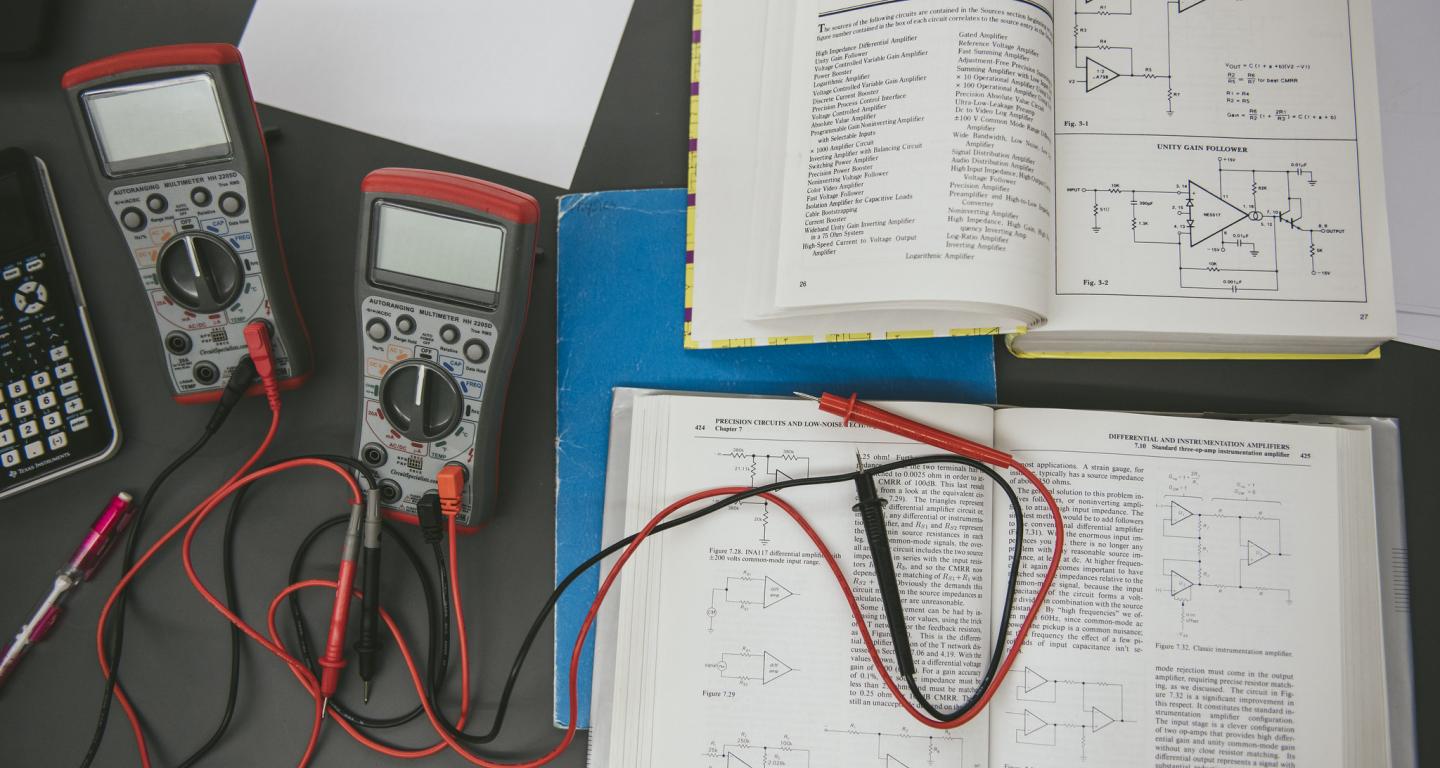
First, the process of kaizen must start with an understanding of current state processes. In the first step, data are collected and analyzed to identify high priority areas. Then, improvements are tested and verified by doing a before-and-after comparison. You can also use benefit-to cost analysis to assess the impact on a particular improvement or the entire kaizen cycle. To assess the program's effectiveness, it is crucial to monitor the results for 60 to 90 days.
FAQ
What is the job of a manufacturer manager?
A manufacturing manager must ensure that all manufacturing processes are efficient and effective. They should be aware of any issues within the company and respond accordingly.
They should also be able and comfortable communicating with other departments like sales and marketing.
They should also be knowledgeable about the latest trends in the industry so they can use this information for productivity and efficiency improvements.
What can I do to learn more about manufacturing?
Practical experience is the best way of learning about manufacturing. If that is not possible, you could always read books or view educational videos.
What are manufacturing & logistics?
Manufacturing is the process of creating goods from raw materials by using machines and processes. Logistics manages all aspects of the supply chain, including procurement, production planning and distribution, inventory control, transportation, customer service, and transport. Manufacturing and logistics are often considered together as a broader term that encompasses both the process of creating products and delivering them to customers.
Statistics
- It's estimated that 10.8% of the U.S. GDP in 2020 was contributed to manufacturing. (investopedia.com)
- In 2021, an estimated 12.1 million Americans work in the manufacturing sector.6 (investopedia.com)
- [54][55] These are the top 50 countries by the total value of manufacturing output in US dollars for its noted year according to World Bank.[56] (en.wikipedia.org)
- According to a Statista study, U.S. businesses spent $1.63 trillion on logistics in 2019, moving goods from origin to end user through various supply chain network segments. (netsuite.com)
- In the United States, for example, manufacturing makes up 15% of the economic output. (twi-global.com)
External Links
How To
Six Sigma: How to Use it in Manufacturing
Six Sigma is "the application statistical process control (SPC), techniques for continuous improvement." Motorola's Quality Improvement Department in Tokyo, Japan developed Six Sigma in 1986. The basic idea behind Six Sigma is to improve quality by improving processes through standardization and eliminating defects. This method has been adopted by many companies in recent years as they believe there are no perfect products or services. Six Sigma aims to reduce variation in the production's mean value. This means that if you take a sample of your product, then measure its performance against the average, you can find out what percentage of the time the process deviates from the norm. If the deviation is excessive, it's likely that something needs to be fixed.
Understanding the dynamics of variability within your business is the first step in Six Sigma. Once you have a good understanding of the basics, you can identify potential sources of variation. Also, you will need to identify the sources of variation. Random variations occur when people make mistakes; systematic ones are caused by factors outside the process itself. For example, if you're making widgets, and some of them fall off the assembly line, those would be considered random variations. It would be considered a systematic problem if every widget that you build falls apart at the same location each time.
After identifying the problem areas, you will need to devise solutions. It might mean changing the way you do business or redesigning it entirely. You should then test the changes again after they have been implemented. If they didn't work, then you'll need to go back to the drawing board and come up with another plan.