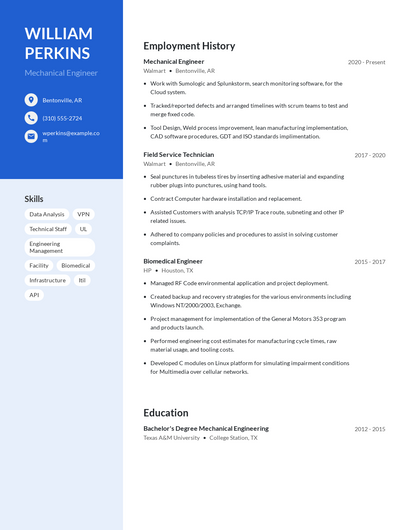
The sourcing and coordination of all purchasing activities is the responsibility of Purchasing Managers (also known as Materials Managers). They interact with suppliers, vendors, and other purchasing agents. They need to be familiar with the company's buying process and how they can improve it. They must also know how to negotiate the best deal for the company.
A purchasing manager also needs to have accurate and current records regarding purchases. They evaluate the price trends, analyze financial reports, and analyze customer needs. They coordinate purchasing activities with other departments. If the company requires supplies from foreign markets, they may have to work overtime.
As well as managing inventory and logistics, purchasing managers coordinate and manage them. They determine the best method of purchasing and ensure that purchased items are in compliance with company quality standards. They also manage budgets, and collaborate with their staff in order to ensure that purchases are made for the best price. They are also able to negotiate contracts and find the best suppliers.
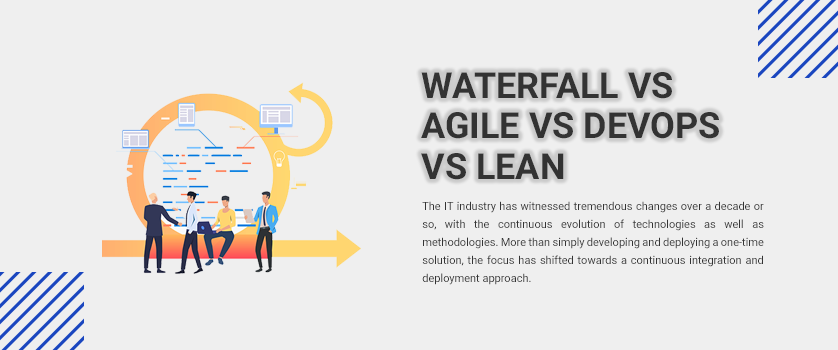
All purchasing employees are monitored and managed by Purchasing Managers. They evaluate the quality, speed, and cost of all purchased goods. They meet with suppliers and buyers and visit their distribution facilities. They ensure that all suppliers adhere to the contract terms. They may also need to handle disciplinary issues and team-building.
The Purchasing Manager must be able to communicate effectively, use analytical skills and think strategically. They must be able and able to analyse the effect of different products on a company. They must have the ability to manage suppliers, and their relationships. They should also be able take business decisions and increase sales. They must be able deal with complicated purchases. They must be capable of evaluating new vendors and analyzing their capabilities in order to select the best vendor.
A bachelor's degree in business is required for purchasing managers. It is also helpful if they have experience in inventory management and supply chain management. They must also have a knowledge of Microsoft Office, as well as other computer software programs.
The best purchasing manager should be able to find the best deals and negotiate the most favorable contracts. They must be able manage inventory, coordinate purchasing activities and monitor supplier and vendor performance. They should also possess the ability to manage a small team of purchasing agents.
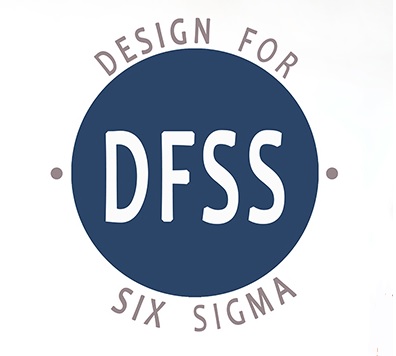
The purchase manager job description should also be able to mention how purchasing is essential to the company's success. It should also highlight how important it for the company's to be ahead of the game. It should also describe how the company values work-life balance. It should include a call for action to encourage applicants.
If the company requires equipment or materials to be purchased for an international market, purchasing managers may work overtime. They may also be required to interact with vendors and attendees at trade shows.
FAQ
What is the role and responsibility of a Production Planner?
Production planners ensure that all project aspects are completed on time, within budget and within the scope. They make sure that the product and services meet client expectations.
What are the 7 Rs of logistics?
The 7R's of Logistics is an acronym for the seven basic principles of logistics management. It was created by the International Association of Business Logisticians and published in 2004 under its "Seven Principles of Logistics Management".
The following letters form the acronym:
-
Responsible – ensure that all actions are legal and don't cause harm to anyone else.
-
Reliable – have faith in your ability and capability to keep promises.
-
Reasonable - use resources efficiently and don't waste them.
-
Realistic - Take into consideration all aspects of operations including cost-effectiveness, environmental impact, and other factors.
-
Respectful - Treat people fairly and equitably
-
Responsive - Look for ways to save time and increase productivity.
-
Recognizable - Provide value-added services to customers
How can we increase manufacturing efficiency?
The first step is to determine the key factors that impact production time. We then need to figure out how to improve these variables. If you don’t know where to begin, consider which factors have the largest impact on production times. Once you have identified the factors, then try to find solutions.
What is the difference between manufacturing and logistics
Manufacturing refers to the process of making goods using raw materials and machines. Logistics includes all aspects related to supply chain management, such as procurement, distribution planning, inventory control and transportation. Manufacturing and logistics can often be grouped together to describe a larger term that covers both the creation of products, and the delivery of them to customers.
Statistics
- According to the United Nations Industrial Development Organization (UNIDO), China is the top manufacturer worldwide by 2019 output, producing 28.7% of the total global manufacturing output, followed by the United States, Japan, Germany, and India.[52][53] (en.wikipedia.org)
- In the United States, for example, manufacturing makes up 15% of the economic output. (twi-global.com)
- In 2021, an estimated 12.1 million Americans work in the manufacturing sector.6 (investopedia.com)
- According to a Statista study, U.S. businesses spent $1.63 trillion on logistics in 2019, moving goods from origin to end user through various supply chain network segments. (netsuite.com)
- You can multiply the result by 100 to get the total percent of monthly overhead. (investopedia.com)
External Links
How To
Six Sigma and Manufacturing
Six Sigma is defined as "the application of statistical process control (SPC) techniques to achieve continuous improvement." It was developed by Motorola's Quality Improvement Department at their plant in Tokyo, Japan, in 1986. The basic idea behind Six Sigma is to improve quality by improving processes through standardization and eliminating defects. This method has been adopted by many companies in recent years as they believe there are no perfect products or services. Six Sigma's main objective is to reduce variations from the production average. This means that if you take a sample of your product, then measure its performance against the average, you can find out what percentage of the time the process deviates from the norm. If there is a significant deviation from the norm, you will know that something needs to change.
The first step toward implementing Six Sigma is understanding how variability works in your business. Once you have a good understanding of the basics, you can identify potential sources of variation. Also, you will need to identify the sources of variation. Random variations are caused when people make mistakes. While systematic variations are caused outside of the process, they can occur. You could consider random variations if some widgets fall off the assembly lines. You might notice that your widgets always fall apart at the same place every time you put them together.
Once you have identified the problem, you can design solutions. The solution could involve changing how you do things, or redesigning your entire process. To verify that the changes have worked, you need to test them again. If they don't work you need to rework them and come up a better plan.