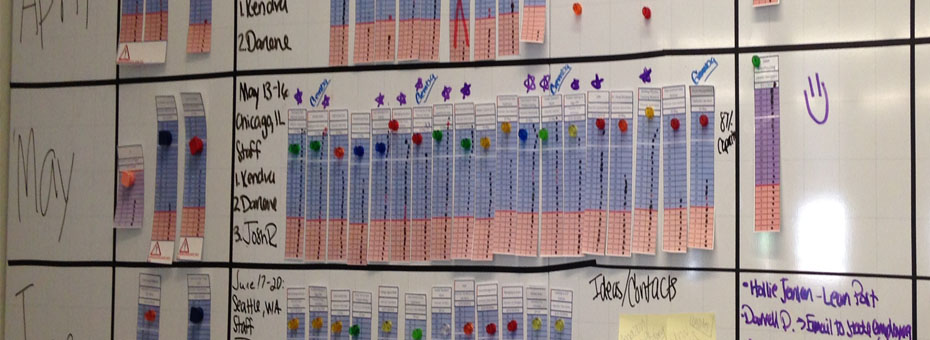
Historically, manufacturing has been driven by consumer demand. But this is changing. The manufacturing industry is also being transformed by technology. This is due in part to advances in predictive analytics, which enable manufacturers to move production closer to consumers. However, there are still risks to manufacturing, such as supply and demand. Manufacturers who fail to meet consumer demand could lose their customers. Also, too much production can lead to oversupply in the market. To protect their brand image, manufacturers must adhere to quality control standards.
Manufacturers can use a variety of manufacturing methods, but they all have similar characteristics. The most commonly used processes are batch manufacturing, repetitive manufacturing, and manufacturing by process. These processes can be used on large scales to allow manufacturers to make products in bulk.
Repetitive production is where dedicated production lines produce identical or similar products year-round. Repetitive Manufacturing production lines do not require any setup or changeover. This makes it ideal for production runs that require little capital investment. They can run 24-hours per day.
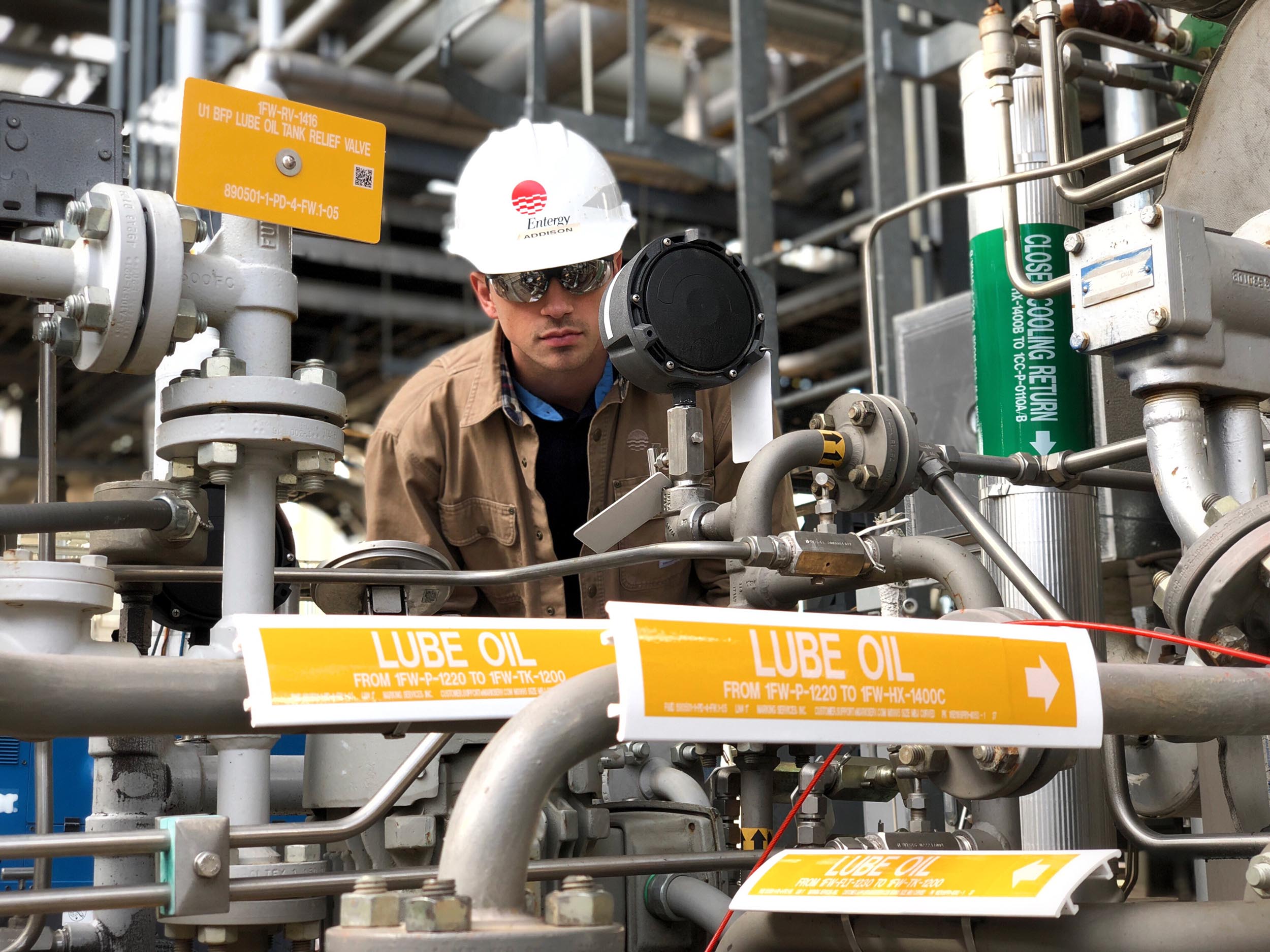
Batch manufacturing is similar in concept to repetitive manufacturing but works in smaller, more precise batches. The process is usually faster and requires less automation. It is not suitable, however, for all types production. This is an option for products that need frequent changeovers. It can also be used for custom-made products. It is suitable to manufacture goods made from materials that are difficult to break down.
Discrete production is the opposite from process manufacturing. It requires a bill of materials, as well as instructions to produce finished goods. It can also include toys and automobiles. It can also involve the use of software and computers. The main difference is the fact that process manufacturing has fewer interruptions while maintaining a higher level of quality control.
Injection molding is the most popular method for mass-producing plastic parts. Small plastic pellets are first melted and then injected in a mold. The mold is then cooled, and mechanically ejected. To ensure uniform coating, the mold is also heated and rotated. This method can be used to create a wide range of products, from pipes and straws to name a few.
A third type of manufacturing process is atomic manufacturing. This process is also called "bottom up" manufacturing. This process allows components to interrelate spontaneously. It is also possible to produce products from biological materials in this manner. You can add parts manually or automatically in certain cases.
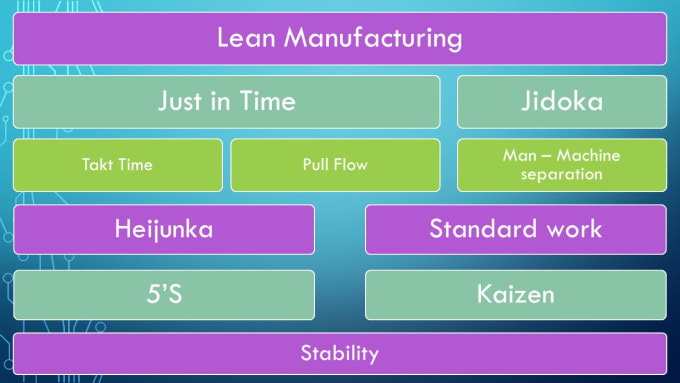
Intermittent Manufacturing is another form. This method can produce many identical items simultaneously, making it especially useful for small-volume production runs. This method is not customizable and may not be suitable for all products.
Process manufacturing also includes the production of items that cannot be broken down, such as ceramics or glass. Process manufacturing's main advantage is its ability to produce a wide variety of products and maintain high quality. Additionally, process manufacturing is less prone to defects and has fewer interruptions.
FAQ
Do we need to know about Manufacturing Processes before learning about Logistics?
No. No. But, being familiar with manufacturing processes will give you a better understanding about how logistics works.
What are the essential elements of running a logistics firm?
To be a successful businessman in logistics, you will need many skills and knowledge. To communicate effectively with clients and suppliers, you must be able to communicate well. You should be able analyse data and draw inferences. You must be able and able to handle stress situations and work under pressure. To improve efficiency, you must be innovative and creative. To motivate and guide your team towards reaching organizational goals, you must have strong leadership skills.
To meet tight deadlines, you must also be efficient and organized.
Why is logistics important in manufacturing
Logistics are an essential part of any business. They enable you to achieve outstanding results by helping manage product flow from raw materials through to finished goods.
Logistics plays a significant role in reducing cost and increasing efficiency.
How can overproduction in manufacturing be reduced?
The key to reducing overproduction lies in developing better ways to manage inventory. This would reduce the time needed to manage inventory. By doing this, we could free up resources for other productive tasks.
A Kanban system is one way to achieve this. A Kanbanboard is a visual tool that allows you to keep track of the work being done. A Kanban system allows work items to move through several states before reaching their final destination. Each state is assigned a different priority.
For instance, when work moves from one stage to another, the current task is complete enough to be moved to the next stage. It is possible to keep a task in the beginning stages until it gets to the end.
This keeps work moving and ensures no work is lost. Managers can view the Kanban board to see how much work they have done. This information allows them to adjust their workflow based on real-time data.
Lean manufacturing can also be used to reduce inventory levels. Lean manufacturing works to eliminate waste throughout every stage of the production chain. Anything that does nothing to add value to a product is waste. The following are examples of common waste types:
-
Overproduction
-
Inventory
-
Packaging that is not necessary
-
Materials in excess
Manufacturers can increase efficiency and decrease costs by implementing these ideas.
What are the responsibilities for a manufacturing manager
Manufacturing managers must ensure that manufacturing processes are efficient, effective, and cost-effective. They should be aware of any issues within the company and respond accordingly.
They should also know how to communicate with other departments such as sales and marketing.
They should be informed about industry trends and be able make use of this information to improve their productivity and efficiency.
How can manufacturing efficiency improved?
The first step is to determine the key factors that impact production time. Next, we must find ways to improve those factors. If you aren't sure where to begin, think about the factors that have the greatest impact on production time. Once you've identified them, try to find solutions for each of those factors.
What is the difference between Production Planning and Scheduling?
Production Planning (PP), or production planning, is the process by which you determine what products are needed at any given time. This is done through forecasting demand and identifying production capacities.
Scheduling involves the assignment of dates and times to tasks in order to complete them within the timeframe.
Statistics
- Many factories witnessed a 30% increase in output due to the shift to electric motors. (en.wikipedia.org)
- [54][55] These are the top 50 countries by the total value of manufacturing output in US dollars for its noted year according to World Bank.[56] (en.wikipedia.org)
- In 2021, an estimated 12.1 million Americans work in the manufacturing sector.6 (investopedia.com)
- (2:04) MTO is a production technique wherein products are customized according to customer specifications, and production only starts after an order is received. (oracle.com)
- According to the United Nations Industrial Development Organization (UNIDO), China is the top manufacturer worldwide by 2019 output, producing 28.7% of the total global manufacturing output, followed by the United States, Japan, Germany, and India.[52][53] (en.wikipedia.org)
External Links
How To
How to Use Lean Manufacturing in the Production of Goods
Lean manufacturing is a management style that aims to increase efficiency and reduce waste through continuous improvement. It was first developed in Japan in the 1970s/80s by Taiichi Ahno, who was awarded the Toyota Production System (TPS), award from KanjiToyoda, the founder of TPS. Michael L. Watkins published the book "The Machine That Changed the World", which was the first to be published about lean manufacturing.
Lean manufacturing is often described as a set if principles that help improve the quality and speed of products and services. It is about eliminating defects and waste from all stages of the value stream. Lean manufacturing is called just-in-time (JIT), zero defect, total productive maintenance (TPM), or 5S. Lean manufacturing is about eliminating activities that do not add value, such as inspection, rework, and waiting.
Lean manufacturing not only improves product quality but also reduces costs. Companies can also achieve their goals faster by reducing employee turnover. Lean Manufacturing is one of the most efficient ways to manage the entire value chains, including suppliers and customers as well distributors and retailers. Lean manufacturing is widely practiced in many industries around the world. Toyota's philosophy, for example, is what has enabled it to be successful in electronics, automobiles, medical devices, healthcare and chemical engineering as well as paper and food.
Five principles are the basis of lean manufacturing:
-
Define value - Find out what your business contributes to society, and what makes it different from other competitors.
-
Reduce Waste - Eliminate any activity that doesn't add value along the supply chain.
-
Create Flow - Make sure work runs smoothly without interruptions.
-
Standardize & Simplify - Make processes as consistent and repeatable as possible.
-
Build Relationships - Establish personal relationships with both internal and external stakeholders.
Lean manufacturing, although not new, has seen renewed interest in the economic sector since 2008. Many businesses are now using lean manufacturing to improve their competitiveness. In fact, some economists believe that lean manufacturing will be an important factor in economic recovery.
Lean manufacturing is now becoming a common practice in the automotive industry, with many benefits. These benefits include increased customer satisfaction, reduced inventory levels and lower operating costs.
Any aspect of an enterprise can benefit from Lean manufacturing. Because it makes sure that all value chains are efficient and effectively managed, Lean Manufacturing is particularly helpful for organizations.
There are three types of lean manufacturing.
-
Just-in Time Manufacturing: This lean manufacturing method is commonly called "pull systems." JIT means that components are assembled at the time of use and not manufactured in advance. This approach reduces lead time, increases availability and reduces inventory.
-
Zero Defects Manufacturing (ZDM): ZDM focuses on ensuring that no defective units leave the manufacturing facility. If a part is required to be repaired on the assembly line, it should not be scrapped. This is true even for finished products that only require minor repairs prior to shipping.
-
Continuous Improvement (CI),: Continuous improvement aims improve the efficiency and effectiveness of operations by continuously identifying issues and making changes to reduce waste. It involves continuous improvement of processes, people, and tools.