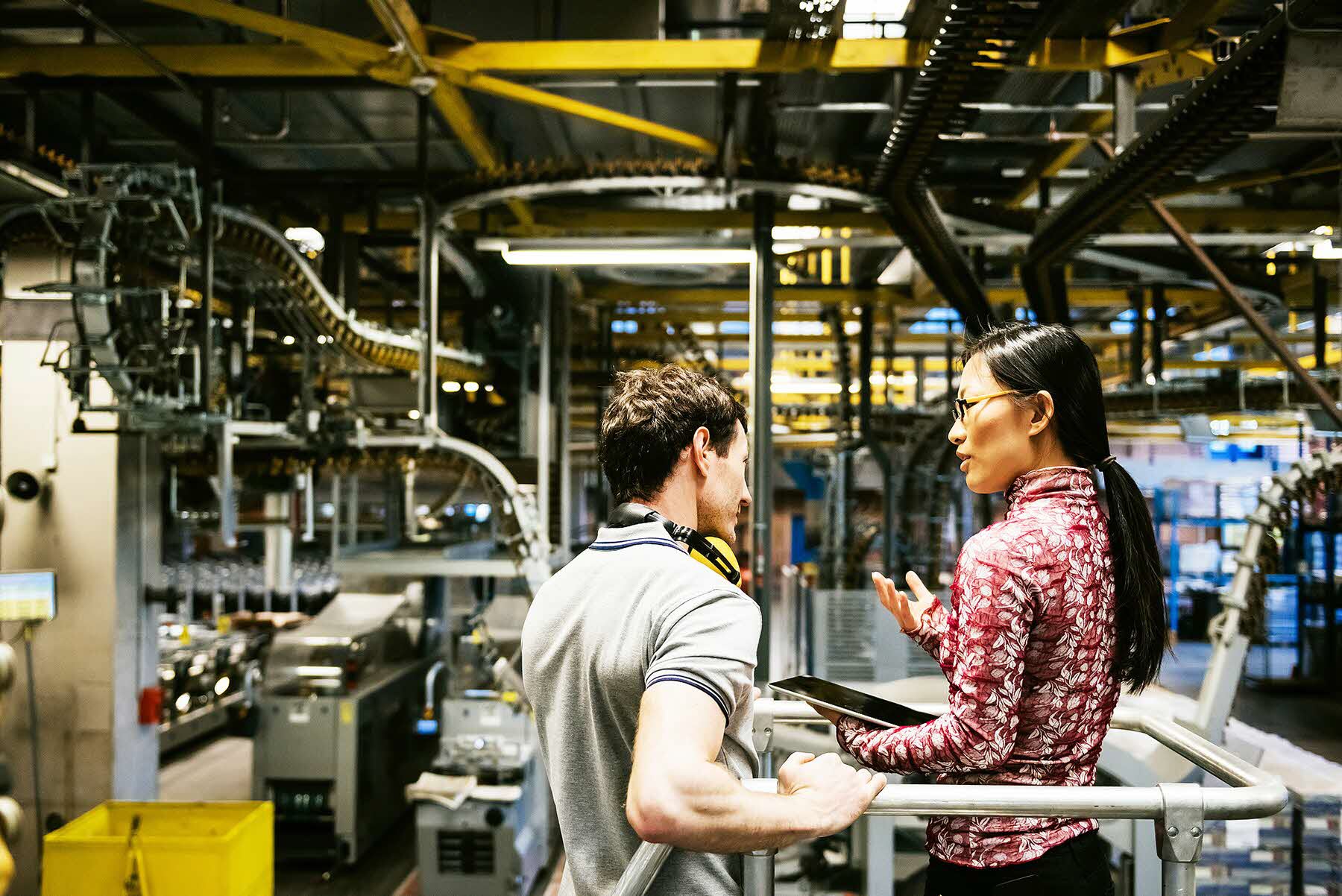
Louisville, Kentucky, is a growing business and manufacturing center. It has a population close to 770,557 people and is home a number of famous brands. KFC, Maker's Mark or Louisville Slugger are some examples. Louisville is known for being one of America's most prominent cities when it comes to moving goods.
Louisville, KY has many logistics professionals who can handle a wide variety tasks. This is to ensure that the industry remains competitive. They are responsible to ensure products are delivered on time. This career involves shipping, handling, distribution, or both. It requires a strong understanding of business operations and the ability to deliver high quality.
You can find a variety jobs in logistics from entry-level positions to executives. You can search the Monster job listings if you are interested in this career. After finding the right job, they can apply. They can set up a profile for free and receive custom job alerts as well as expert advice.
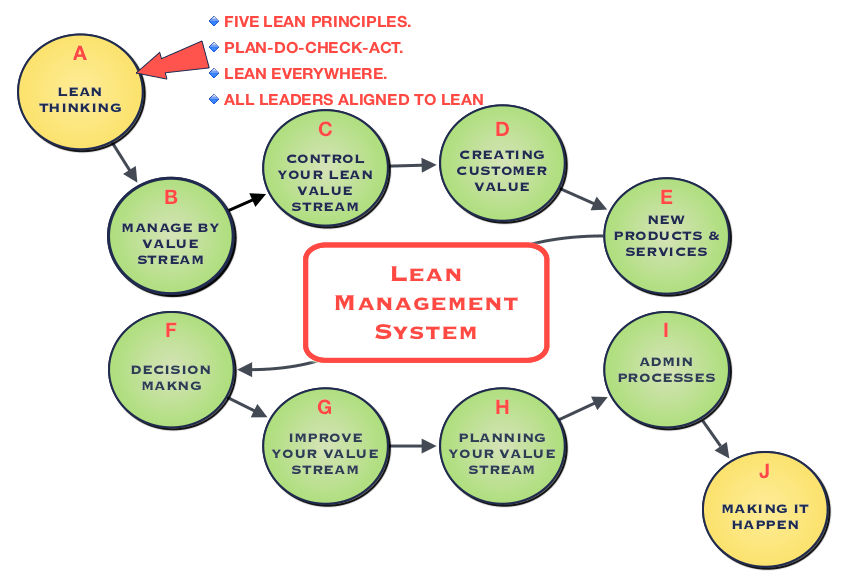
The Logistics and Distribution Institute is a multidisciplinary organization dedicated to improving the efficiency of delivery processes. They conduct research and offer training on impactful efficiencies in the shipping industry.
A&R Global Logistics is a logistics company that arranges bulk shipments of dry plastic pallets for chemical companies. They have a fleet of 800 trucks and operate 10 warehouses in the U.S. Additionally, they provide packaging services. They offer ground and air freight forwarding services as well as reverse logistics.
SEKO is a global third-party logistics provider that offers a full range of supply chain services. These include contract logistics, air freight forwarding and asset management. They also offer reverse logistics, DC bypass shipping, customs brokerage and more. They currently have offices in more than 40 countries.
Similarly, Palisades Logistics is a top third-party logistics firm that provides storage, warehousing, and fulfillment services. They are easily located and have a professional manager. They are also well-known for providing excellent customer service as well as reliable delivery.
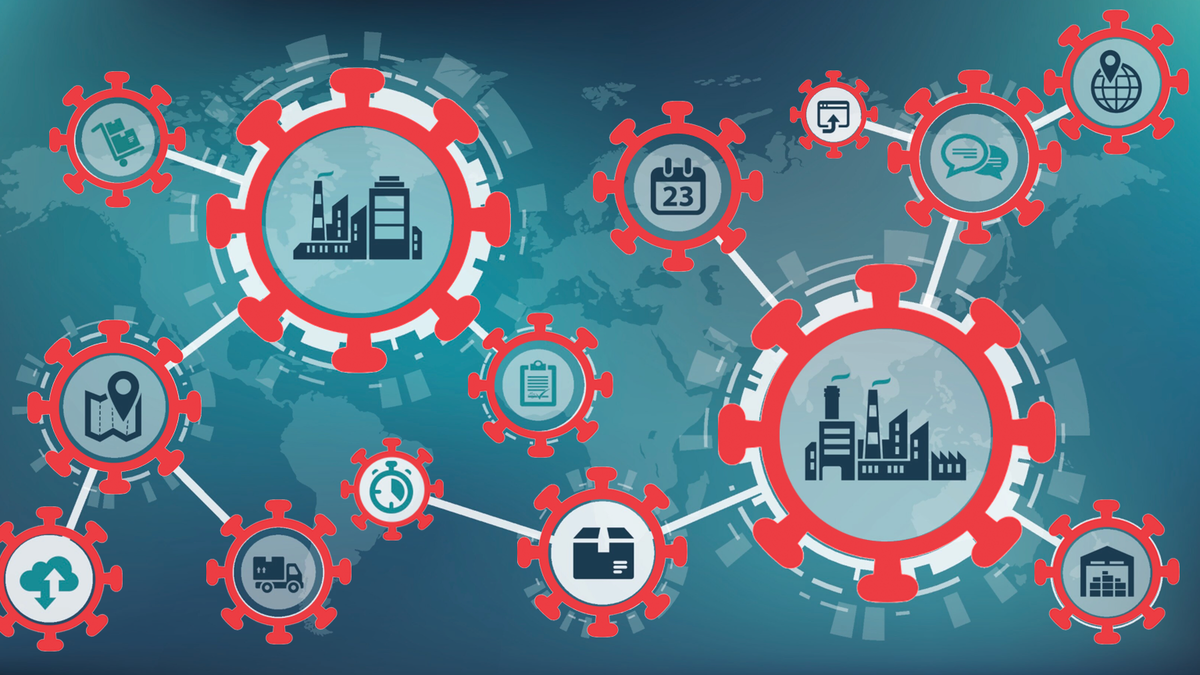
Worldport is one the largest logistics companies with an annual payroll exceeding $2.5 billion. It also employs 62,000 people in indirect and direct roles.
For entry-level jobs in logistics, Louisville, KY, the median annual salary is $41,522. However, this salary can vary depending on the specific skills and experience you bring to the table. A freight sales and carrier negotiation background are required for an Account Manager. The Supply Chain Coordinator oversees logistics and ensures that inventory is correctly stored, shipped, and delivered.
If you're looking for a career in the logistics industry, you can start by browsing the job listings on Monster. Internships are also available to help bridge the gap between schoolworkplace and the real world. Internships allow you to experience a work environment firsthand and decide whether you want to continue to pursue a career in this field.
FAQ
Can certain manufacturing steps be automated?
Yes! Yes. The wheel was invented by the Egyptians thousands of years ago. Nowadays, we use robots for assembly lines.
Actually, robotics can be used in manufacturing for many purposes. They include:
-
Assembly line robots
-
Robot welding
-
Robot painting
-
Robotics inspection
-
Robots that create products
Manufacturing can also be automated in many other ways. 3D printing makes it possible to produce custom products in a matter of days or weeks.
What is production planning?
Production planning is the process of creating a plan that covers all aspects of production. This includes scheduling, budgeting and crew, location, equipment, props, and more. This document aims to ensure that everything is planned and ready when you are ready to shoot. This document should also include information on how to get the best result on set. This includes shooting schedules, locations, cast lists, crew details, and equipment requirements.
The first step is to outline what you want to film. You may have already decided where you would like to shoot, or maybe there are specific locations or sets that you want to use. Once you have determined your scenes and locations, it is time to start figuring out the elements that you will need for each scene. Perhaps you have decided that you need to buy a car but aren't sure which model. This is where you can look up car models online and narrow down your options by choosing from different makes and models.
After you have selected the car you want, you can begin to think about additional features. Are you looking for people to sit in the front seats? You might also need someone to help you get around the back. You might want to change your interior color from black and white. These questions will help you determine the exact look and feel of your car. Another thing you can do is think about what type of shots are desired. You will be filming close-ups and wide angles. Perhaps you want to show the engine or the steering wheel? These factors will help you determine which car style you want to film.
Once you've determined the above, it is time to start creating a calendar. A schedule will tell you when you need to start shooting and when you need to finish. Every day will have a time for you to arrive at the location, leave when you are leaving and return home when you are done. It will help everyone know exactly what they have to do and when. It is possible to make arrangements in advance for additional staff if you are looking to hire. It's not worth paying someone to show up if you haven't told him.
You will need to factor in the days that you have to film when creating your schedule. Some projects are quick and easy, while others take weeks. When creating your schedule, be aware of whether you need more shots per day. Multiple takes at the same place will result in higher costs and longer completion times. You can't be certain if you will need multiple takes so it is better not to shoot too many.
Budget setting is another important aspect in production planning. A realistic budget will help you work within your means. Remember that you can always reduce the budget later on if you run into unforeseen problems. However, it is important not to overestimate the amount that you will spend. You will end up spending less money if you underestimate the cost of something.
Production planning is a detailed process. But, once you understand the workings of everything, it becomes easier for future projects to be planned.
What are the responsibilities for a manufacturing manager
The manufacturing manager should ensure that every manufacturing process is efficient and effective. They must also be alert to any potential problems and take appropriate action.
They should also be able communicate with other departments, such as sales or marketing.
They must also keep up-to-date with the latest trends in their field and be able use this information to improve productivity and efficiency.
How does a production planner differ from a project manager?
The difference between a product planner and project manager is that a planer is typically the one who organizes and plans the entire project. A production planner, however, is mostly involved in the planning stages.
How can efficiency in manufacturing be improved?
First, identify the factors that affect production time. We then need to figure out how to improve these variables. If you don’t know how to start, look at which factors have the greatest impact upon production time. Once you have identified the factors, then try to find solutions.
What does manufacturing mean?
Manufacturing Industries are those businesses that make products for sale. Consumers are people who purchase these goods. These companies use a variety processes such as distribution, retailing and management to accomplish their purpose. They manufacture goods from raw materials using machines and other equipment. This includes all types of manufactured goods, including food items, clothing, building supplies, furniture, toys, electronics, tools, machinery, vehicles, pharmaceuticals, medical devices, chemicals, and many others.
Statistics
- Many factories witnessed a 30% increase in output due to the shift to electric motors. (en.wikipedia.org)
- According to the United Nations Industrial Development Organization (UNIDO), China is the top manufacturer worldwide by 2019 output, producing 28.7% of the total global manufacturing output, followed by the United States, Japan, Germany, and India.[52][53] (en.wikipedia.org)
- In the United States, for example, manufacturing makes up 15% of the economic output. (twi-global.com)
- You can multiply the result by 100 to get the total percent of monthly overhead. (investopedia.com)
- Job #1 is delivering the ordered product according to specifications: color, size, brand, and quantity. (netsuite.com)
External Links
How To
How to use lean manufacturing in the production of goods
Lean manufacturing (or lean manufacturing) is a style of management that aims to increase efficiency, reduce waste and improve performance through continuous improvement. It was developed in Japan between 1970 and 1980 by Taiichi Ohno. TPS founder Kanji Tyoda gave him the Toyota Production System, or TPS award. Michael L. Watkins published the first book on lean manufacturing in 1990.
Lean manufacturing is often defined as a set of principles used to improve the quality, speed, and cost of products and services. It emphasizes eliminating waste and defects throughout the value stream. The five-steps of Lean Manufacturing are just-in time (JIT), zero defect and total productive maintenance (TPM), as well as 5S. Lean manufacturing eliminates non-value-added tasks like inspection, rework, waiting.
In addition to improving product quality and reducing costs, lean manufacturing helps companies achieve their goals faster and reduces employee turnover. Lean manufacturing is considered one of the most effective ways to manage the entire value chain, including suppliers, customers, distributors, retailers, and employees. Lean manufacturing is widely used in many industries. For example, Toyota's philosophy underpins its success in automobiles, electronics, appliances, healthcare, chemical engineering, aerospace, paper, food, etc.
Lean manufacturing includes five basic principles:
-
Define Value - Identify the value your business adds to society and what makes you different from competitors.
-
Reduce Waste - Eliminate any activity that doesn't add value along the supply chain.
-
Create Flow. Ensure that your work is uninterrupted and flows seamlessly.
-
Standardize and Simplify – Make processes as consistent, repeatable, and as simple as possible.
-
Develop Relationships: Establish personal relationships both with internal and external stakeholders.
Although lean manufacturing has always been around, it is gaining popularity in recent years because of a renewed interest for the economy after 2008's global financial crisis. Many businesses have adopted lean production techniques to make them more competitive. Some economists even believe that lean manufacturing can be a key factor in economic recovery.
With many benefits, lean manufacturing is becoming more common in the automotive industry. These include higher customer satisfaction levels, reduced inventory levels as well as lower operating costs.
It can be applied to any aspect of an organisation. Because it makes sure that all value chains are efficient and effectively managed, Lean Manufacturing is particularly helpful for organizations.
There are three main types in lean manufacturing
-
Just-in-Time Manufacturing (JIT): This type of lean manufacturing is commonly referred to as "pull systems." JIT is a process in which components can be assembled at the point they are needed, instead of being made ahead of time. This approach is designed to reduce lead times and increase the availability of components. It also reduces inventory.
-
Zero Defects Manufacturing (ZDM),: ZDM is a system that ensures no defective units are left the manufacturing facility. If a part is required to be repaired on the assembly line, it should not be scrapped. This applies to finished products, which may need minor repairs before they are shipped.
-
Continuous Improvement: Continuous Improvement aims to improve efficiency by continually identifying problems and making adjustments to eliminate or minimize waste. Continuous improvement involves continuous improvement of processes and people as well as tools.