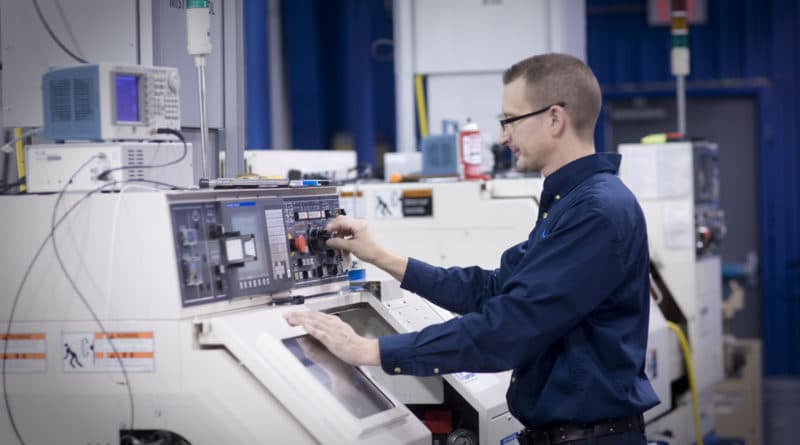
Towson University is a Maryland business school located on the eastern coast. It has been recognized for its outstanding programs. Towson University is one of a few institutions that has been accredited by AACSB International as well as the Association to Advance Collegiate Schools of Business. These certifications let businesses know that students possess the necessary skills to succeed.
Towson's undergraduate business program has been honored as one of the top public universities in the country. U.S. News & World Report ranked this program amongst the top national programs. The business school also received recognition for its high rate of graduation. The College of Business and Economics (CBE) is dedicated to providing students with the skills they need to succeed. It is a top-ranked business program in Maryland.
Students have access to an entrepreneurship course at the business school. This program helps them identify opportunities, plan strategies, and bring new ideas to life. Towson also offers internships. Internships allow students to get valuable experience in the real workplace.
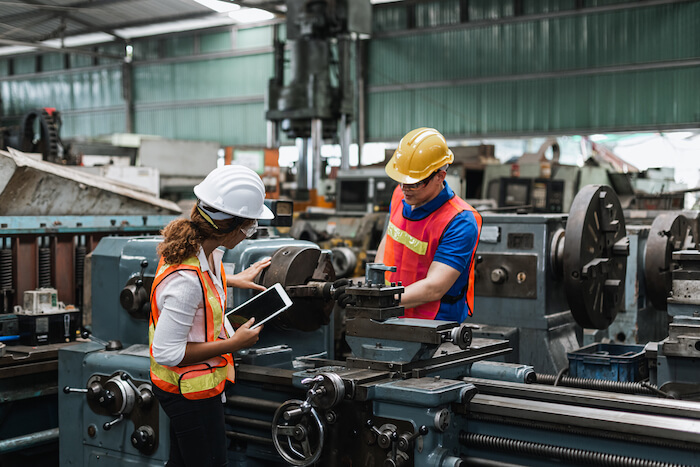
The business school at Towson University offers a bachelor's in business administration. To be eligible, students must have a GPA at least 2.7 in the six required courses. Students who are accepted may take the required courses to complete their major. Students may also pursue a concentrations in leadership and management or entrepreneurship.
Students also have the option to apply for an internship at the business school. Students have the opportunity to work at a variety of companies in the Northeastern region. B-Local Mid-Atlantic partners with the school to allow students to work at local businesses. These internships give students valuable experience as well as the opportunity to apply the knowledge they have gained in the classroom.
International Business Concentration: This concentration requires students take courses in international business, international organizational behavior and multinational management. Students must also complete a capstone course in strategic management that allows them the opportunity to create solutions for real companies.
One of the core components of our business school's curriculum includes the Sellinger Experiential Learning Lab. This lab provides students with data analysis, executive management decision making, research skills, and leadership skills. The lab uses Bloomberg terminals and other technological tools to help students learn about the business world.
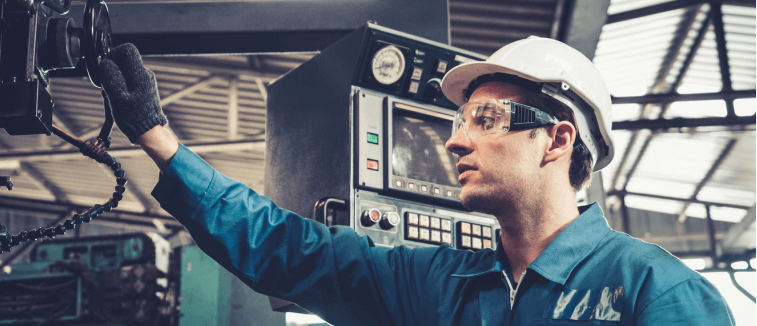
Towson University offers a management curriculum that helps students become an integrator and an analyst. Students will learn how to analyse data, assess trends, and develop strategies through the program. The program prepares students well for careers as managers, financial analysts, and business developers. Students are also encouraged to create new products. Students learn how best to market their products.
Towson University's business school prepares students for management and finance careers. The school's faculty is distinguished scholars who are both active in business research and in academic writing. Faculty can also be mentors or advisers.
FAQ
What skills does a production planner need?
A production planner must be organized, flexible, and able multitask to succeed. Effective communication with clients and colleagues is essential.
What can I do to learn more about manufacturing?
Experience is the best way for you to learn about manufacturing. You can also read educational videos or take classes if this isn't possible.
What is it like to manage a logistics company?
To run a successful logistics company, you need a lot knowledge and skills. Good communication skills are essential to effectively communicate with your suppliers and clients. It is important to be able to analyse data and draw conclusions. You must be able manage stress and pressure under pressure. To improve efficiency, you must be innovative and creative. You will need strong leadership skills to motivate and direct your team members towards achieving their organizational goals.
To meet tight deadlines, you must also be efficient and organized.
What is production management?
Production Planning includes planning for all aspects related to production. It is important to have everything ready and planned before you start shooting. It should also provide information about how best to produce the best results while on set. This includes location information, crew details, equipment specifications, and casting lists.
The first step in filming is to define what you want. You may already know where you want the film to be shot, or perhaps you have specific locations and sets you wish to use. Once you have identified your locations and scenes, you can start working out which elements you require for each scene. If you decide you need a car and don't know what model to choose, this could be an example. In this case, you could start looking up cars online to find out what models are available and then narrow your choices by choosing between different makes and models.
After you have chosen the right car, you will be able to begin thinking about accessories. Do you have people who need to be seated in the front seat? Maybe you need someone to move around in the back. You might want to change your interior color from black and white. These questions can help you decide the right look for your car. Another thing you can do is think about what type of shots are desired. Will you be filming close-ups or wide angles? Perhaps you want to show the engine or the steering wheel? All of these things will help you identify the exact style of car you want to film.
Once you've determined the above, it is time to start creating a calendar. You can create a schedule that will outline when you must start and finish your shoots. Each day will include the time when you need to arrive at the location, when you need to leave and when you need to return home. This way, everyone knows what they need to do and when. It is possible to make arrangements in advance for additional staff if you are looking to hire. You should not hire anyone who doesn't show up because of your inaction.
Your schedule will also have to be adjusted to reflect the number of days required to film. Some projects may only take a couple of days, while others could last for weeks. When you are creating your schedule, you should always keep in mind whether you need more than one shot per day or not. Shooting multiple takes over the same location will increase costs and take longer to complete. If you aren't sure whether you need multiple shots, it is best to take fewer photos than you would like.
Budgeting is another important aspect of production planning. Setting a realistic budget is essential as it will allow you to work within your means. Keep in mind that you can always reduce your budget if you face unexpected difficulties. You shouldn't underestimate the amount you'll spend. You will end up spending less money if you underestimate the cost of something.
Planning production is a tedious process. Once you have a good understanding of how everything works together, planning future projects becomes easy.
How is a production manager different from a producer planner?
The primary difference between a producer planner and a manager of a project is that the manager usually plans and organizes the whole project, while a production planner is only involved in the planning stage.
Statistics
- It's estimated that 10.8% of the U.S. GDP in 2020 was contributed to manufacturing. (investopedia.com)
- You can multiply the result by 100 to get the total percent of monthly overhead. (investopedia.com)
- [54][55] These are the top 50 countries by the total value of manufacturing output in US dollars for its noted year according to World Bank.[56] (en.wikipedia.org)
- Job #1 is delivering the ordered product according to specifications: color, size, brand, and quantity. (netsuite.com)
- In 2021, an estimated 12.1 million Americans work in the manufacturing sector.6 (investopedia.com)
External Links
How To
How to use the Just-In Time Method in Production
Just-in-time (JIT) is a method that is used to reduce costs and maximize efficiency in business processes. It is a process where you get the right amount of resources at the right moment when they are needed. This means that you only pay for what you actually use. Frederick Taylor developed the concept while working as foreman in early 1900s. After observing how workers were paid overtime for late work, he realized that overtime was a common practice. He then concluded that if he could ensure that workers had enough time to do their job before starting to work, this would improve productivity.
JIT teaches you to plan ahead and prepare everything so you don’t waste time. Also, you should look at the whole project from start-to-finish and make sure you have the resources necessary to address any issues. If you expect problems to arise, you will be able to provide the necessary equipment and personnel to address them. You won't have to pay more for unnecessary items.
There are many JIT methods.
-
Demand-driven: This is a type of JIT where you order the parts/materials needed for your project regularly. This will enable you to keep track of how much material is left after you use it. This will allow to you estimate the time it will take for more to be produced.
-
Inventory-based : You can stock the materials you need in advance. This allows one to predict how much they will sell.
-
Project-driven : This is a method where you make sure that enough money is set aside to pay the project's cost. You will be able to purchase the right amount of materials if you know what you need.
-
Resource-based: This is the most common form of JIT. You assign certain resources based off demand. You might assign more people to help with orders if there are many. If you don't receive many orders, then you'll assign fewer employees to handle the load.
-
Cost-based: This is the same as resource-based except that you don't care how many people there are but how much each one of them costs.
-
Price-based: This approach is very similar to the cost-based method except that you don't look at individual workers costs but the total cost of the company.
-
Material-based: This approach is similar to cost-based. However, instead of looking at the total cost for the company, you look at how much you spend on average on raw materials.
-
Time-based: This is another variation of resource-based JIT. Instead of focusing on the cost of each employee, you will focus on the time it takes to complete a project.
-
Quality-based: This is yet another variation of resource-based JIT. Instead of thinking about how much each employee costs or how long it takes to manufacture something, you think about how good the quality of your product is.
-
Value-based JIT is the newest form of JIT. You don't worry about whether the products work or if they meet customer expectations. Instead, you're focused on how much value you add to the market.
-
Stock-based: This stock-based method focuses on the actual quantity of products being made at any given time. This is used to increase production and minimize inventory.
-
Just-intime (JIT), planning is a combination JIT management and supply chain management. It is the process that schedules the delivery of components within a short time of their order. It's important as it reduces leadtimes and increases throughput.