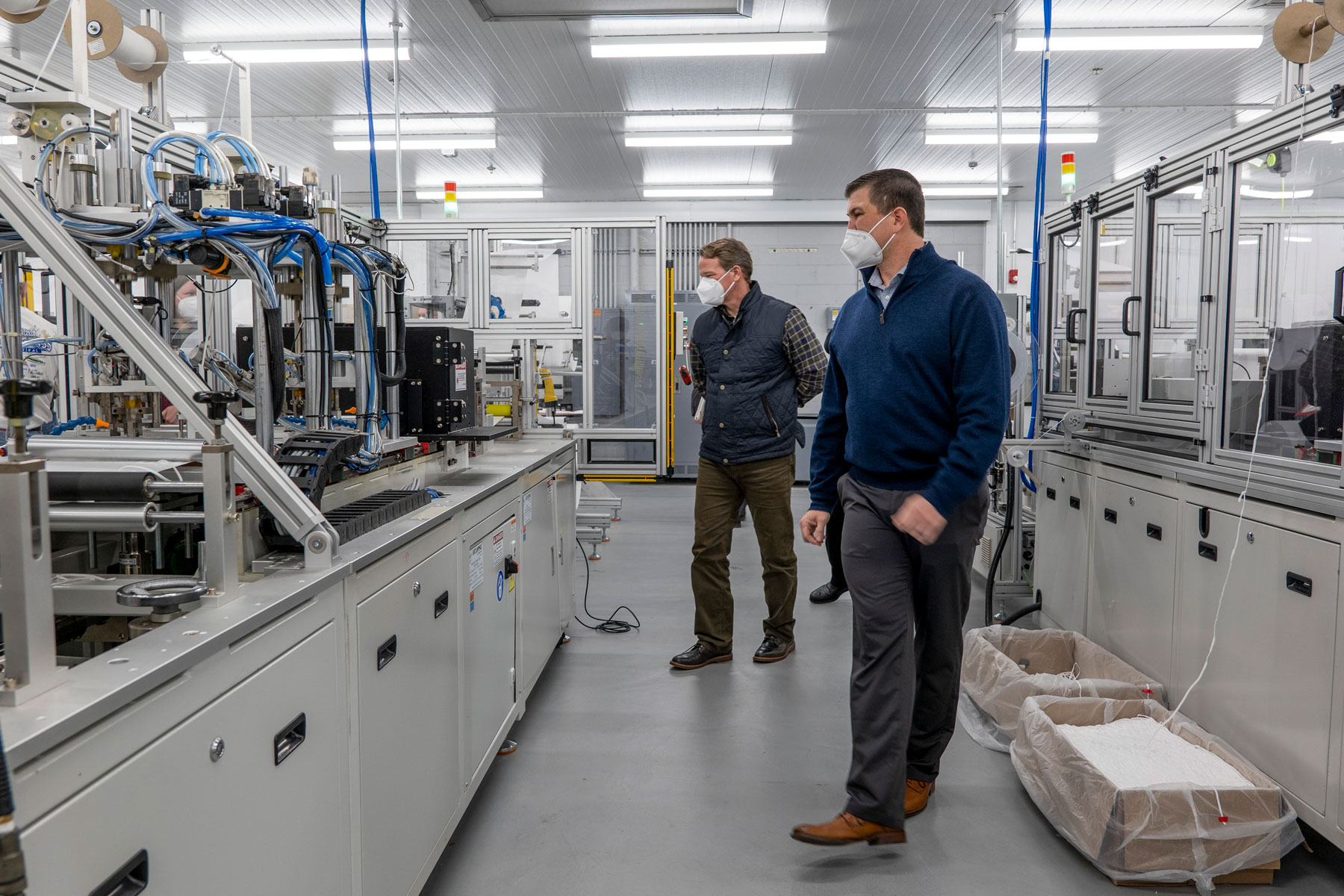
Non value added activities are actions that don't add value to the finished product. It might be necessary and useful, but it does nothing to directly increase the final product's worth. Sharpening the saw is necessary for cutting lumber to the proper size. However, the finished product is still worth less if the saw has been sharpened.
First, define value to understand non-value added activities. Value is defined as what customers are willing to pay for a product or service. This value can vary depending upon the product or service offered. Adding value to a product or service is important for business success. Businesses that don't add value to their products and services will not survive long. In addition, a business will lose customers.
Ask yourself, "Does this action add value to my product or service?" There are three ways to answer. The first way is to assess how the actions relate to the product's final value. Another way is to evaluate how the action contributes to customer satisfaction. Last, ask yourself the question "Does it contribute to customer satisfaction?"
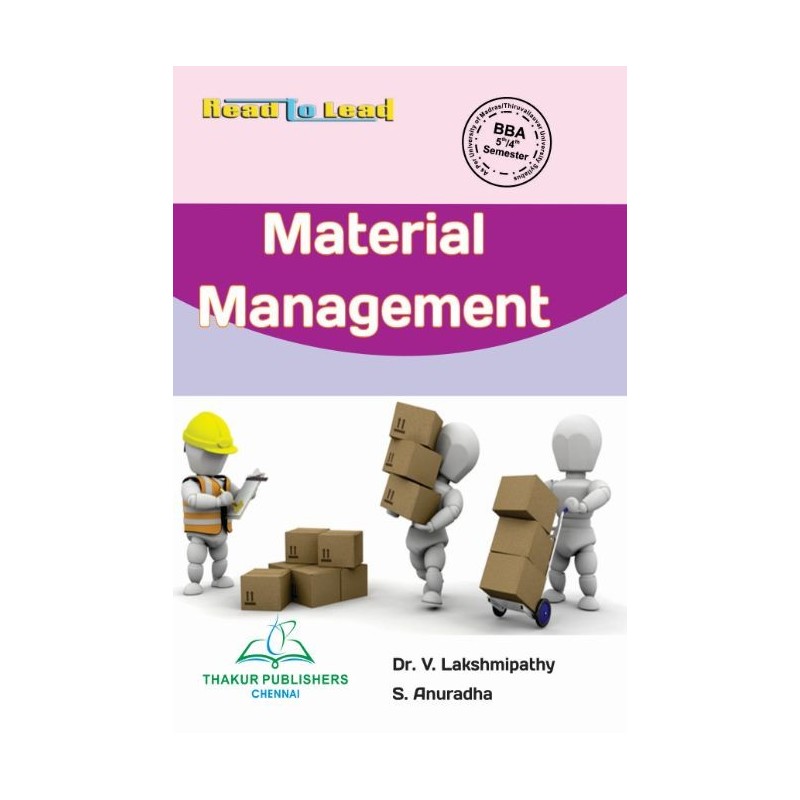
A value-added enterprise is one that generates a positive return. Selling merchandise is an example of a value-added activities. Selling merchandise is an attractive activity as it can generate a profit for the company. Selling merchandise is a profitable activity, as it helps to recoup manufacturing costs.
It is important to identify a value-added activity, but this does not guarantee success. The process that produces the value-added activity must be designed to meet customer expectations. The correct process will ensure that your product or service is delivered on-time and of high quality. You can't afford to make mistakes that could lead to quality or delays.
In order to identify a value-added activity, you must understand what a non-valued activity is. Non-valued tasks are those that don't change the product or its function. Checking, inspecting, billing, and processing are all examples of non-valued tasks.
Non-valued tasks are those that do not serve the customer's interests or provide satisfaction. They can also be costly and consume resources. Your process's wastes can be identified and corrected to increase speed, quality, or service levels. You will increase your cash flow and be more competitive by taking steps to eliminate waste.

The most common mistake is to waste time on activities that are not value added. Some examples of non-valued activities are waiting, performing inspections, and repairing defective items. Other activities that are not valuable to the finished product include copying documents, moving material, and filing paperwork.
Creating a list of processes that add value to the product or service will allow you to determine if your current process is maximizing your potential. It can help you save time and money by breaking down the process.
FAQ
What does it take for a logistics enterprise to succeed?
It takes a lot of skills and knowledge to run a successful logistics business. You must have good communication skills to interact effectively with your clients and suppliers. You will need to know how to interpret data and draw conclusions. You will need to be able handle pressure well and work in stressful situations. You must be creative and innovative to develop new ideas to improve efficiency. Strong leadership qualities are essential to motivate your team and help them achieve their organizational goals.
To meet tight deadlines, you must also be efficient and organized.
Can we automate some parts of manufacturing?
Yes! Since ancient times, automation has been in existence. The Egyptians discovered the wheel thousands and years ago. To help us build assembly lines, we now have robots.
Actually, robotics can be used in manufacturing for many purposes. These include:
-
Automated assembly line robots
-
Robot welding
-
Robot painting
-
Robotics inspection
-
Robots that make products
Manufacturing can also be automated in many other ways. For example, 3D printing allows us to make custom products without having to wait for weeks or months to get them manufactured.
How important is automation in manufacturing?
Not only is automation important for manufacturers, but it's also vital for service providers. It allows them to offer services faster and more efficiently. It reduces human errors and improves productivity, which in turn helps them lower their costs.
What are the goods of logistics?
Logistics are the activities involved in moving goods from point A to point B.
They include all aspects associated with transport including packaging, loading transporting, unloading storage, warehousing inventory management customer service, distribution returns and recycling.
Logisticians ensure that the right product reaches the right place at the right time and under safe conditions. Logisticians help companies improve their supply chain efficiency by providing information about demand forecasts and stock levels, production schedules, as well as availability of raw materials.
They keep track and monitor the transit of shipments, maintain quality standards, order replenishment and inventories, coordinate with suppliers, vendors, and provide support for sales and marketing.
Statistics
- Many factories witnessed a 30% increase in output due to the shift to electric motors. (en.wikipedia.org)
- Job #1 is delivering the ordered product according to specifications: color, size, brand, and quantity. (netsuite.com)
- It's estimated that 10.8% of the U.S. GDP in 2020 was contributed to manufacturing. (investopedia.com)
- According to the United Nations Industrial Development Organization (UNIDO), China is the top manufacturer worldwide by 2019 output, producing 28.7% of the total global manufacturing output, followed by the United States, Japan, Germany, and India.[52][53] (en.wikipedia.org)
- In the United States, for example, manufacturing makes up 15% of the economic output. (twi-global.com)
External Links
How To
How to use lean manufacturing in the production of goods
Lean manufacturing is a management style that aims to increase efficiency and reduce waste through continuous improvement. It was created in Japan by Taiichi Ohno during the 1970s and 80s. He received the Toyota Production System award (TPS), from Kanji Toyoda, founder of TPS. Michael L. Watkins published the "The Machine That Changed the World", the first book about lean manufacturing. It was published in 1990.
Lean manufacturing can be described as a set or principles that are used to improve quality, speed and cost of products or services. It emphasizes the elimination of defects and waste throughout the value stream. The five-steps of Lean Manufacturing are just-in time (JIT), zero defect and total productive maintenance (TPM), as well as 5S. Lean manufacturing focuses on eliminating non-value-added activities such as rework, inspection, and waiting.
Lean manufacturing is a way for companies to achieve their goals faster, improve product quality, and lower costs. Lean Manufacturing is one of the most efficient ways to manage the entire value chains, including suppliers and customers as well distributors and retailers. Many industries worldwide use lean manufacturing. Toyota's philosophy is a great example of this. It has helped to create success in automobiles as well electronics, appliances and healthcare.
Five fundamental principles underlie lean manufacturing.
-
Define Value: Identify the social value of your business and what sets you apart.
-
Reduce waste - Get rid of any activity that does not add value to the supply chain.
-
Create Flow. Ensure that your work is uninterrupted and flows seamlessly.
-
Standardize & Simplify - Make processes as consistent and repeatable as possible.
-
Building Relationships – Establish personal relationships with both external and internal stakeholders.
Although lean manufacturing isn't a new concept in business, it has gained popularity due to renewed interest in the economy after the 2008 global financial crisis. Many businesses have adopted lean manufacturing techniques to help them become more competitive. In fact, some economists believe that lean manufacturing will be an important factor in economic recovery.
With many benefits, lean manufacturing is becoming more common in the automotive industry. These include better customer satisfaction and lower inventory levels. They also result in lower operating costs.
The principles of lean manufacturing can be applied in almost any area of an organization. It is especially useful for the production aspect of an organization, as it ensures that every step in the value chain is efficient and effective.
There are three types principally of lean manufacturing:
-
Just-in-Time Manufacturing: Also known as "pull systems", this type of lean manufacturing uses just-in-time manufacturing (JIT). JIT means that components are assembled at the time of use and not manufactured in advance. This approach reduces lead time, increases availability and reduces inventory.
-
Zero Defects Manufacturing (ZDM): ZDM focuses on ensuring that no defective units leave the manufacturing facility. It is better to repair a part than have it removed from the production line if it needs to be fixed. This applies to finished goods that may require minor repairs before shipment.
-
Continuous Improvement: Continuous Improvement aims to improve efficiency by continually identifying problems and making adjustments to eliminate or minimize waste. It involves continuous improvement of processes, people, and tools.