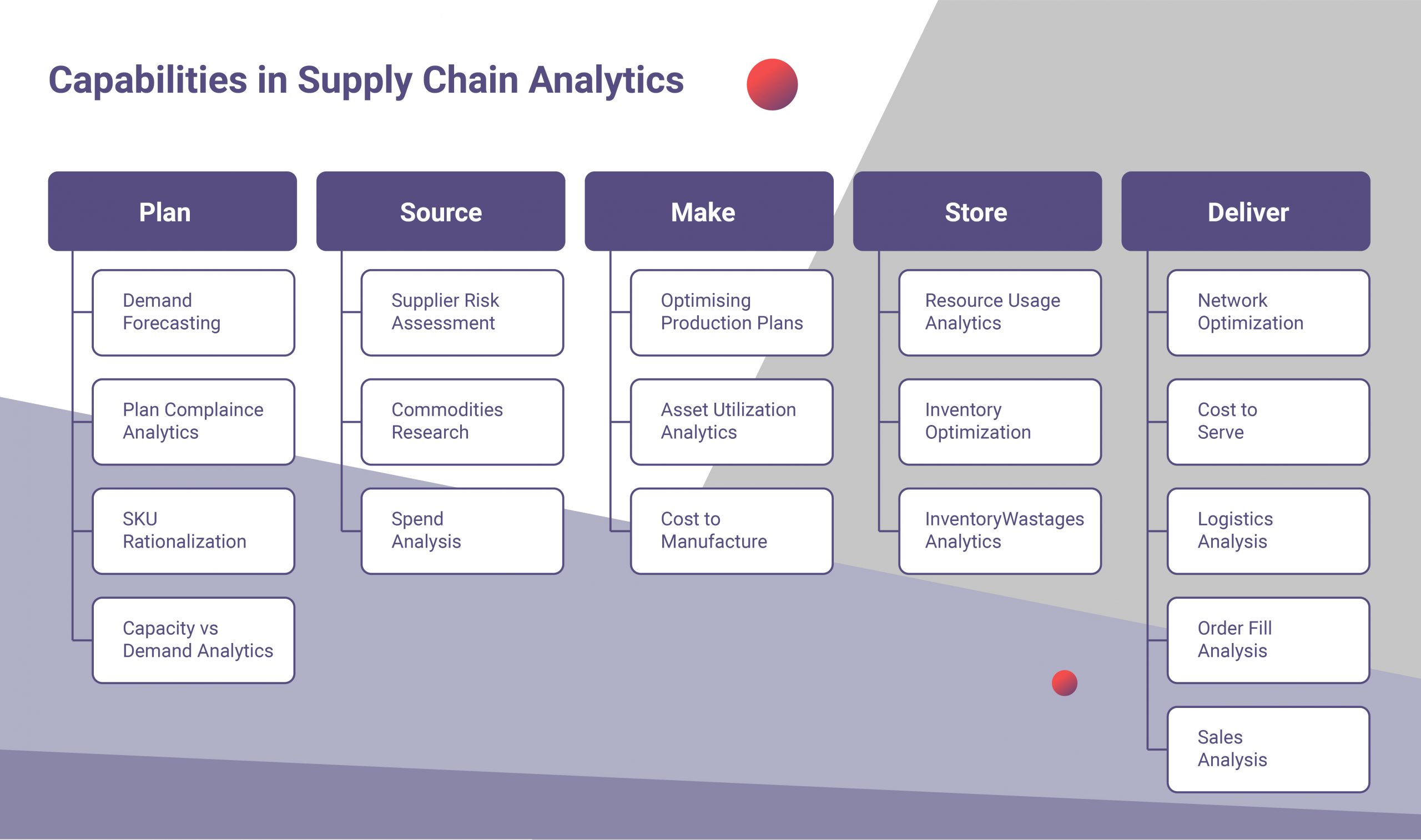
Advanced manufacturing is where companies use innovative technologies to produce better products and processes. These technologies are often referred to as cutting-edge, innovative, and advanced. Companies are increasingly incorporating these technologies into their business operations. Robotics are, Material deposition and Additive Manufacturing are just some examples. These technologies are available for more information.
Additive manufacturing
Many businesses see additive manufacturing as the future of manufacturing. This type of manufacturing uses additive manufacturing technologies (also known as 3D printing). This type of manufacturing offers several benefits, such as increased flexibility and reduced inventory costs. It also reduces the need to import labor-intensive components and parts.
The speed and flexibility of manufacturing has been greatly improved by advances in additive manufacturing technology. Businesses can respond quickly to supply-chain disruptions thanks to them. They can manufacture custom parts in as little as a few hours, sometimes even in days. This is especially helpful in industries that are experiencing supply-chain disruptions. In fact, advanced manufacturing can produce parts with complex geometries.
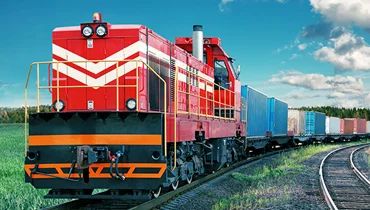
Manufacturers can also produce very small quantities. This can be used, for example, to create custom dental appliances. It also makes it possible to manufacture complex structures, like internal heat pipes. Advanced manufacturing using additive manufacturing also reduces the need for inventory and specialized components. It can reduce materials costs by ninety-five percent and energy consumption by half.
Robotics
Many industrial producers recognize the potential of advanced robotics and plan to implement them within their plants. They aren't satisfied with the current performance and progress made in their implementation. Many of them point out the limitations and high cost of current technology as barriers that prevent wider deployment. They lack key enablers that will allow them to fully deploy advanced robots in their factories.
Advanced robotics integration requires that manufacturers evaluate their system architecture. These systems must include infrastructure, analytics, and data and workflow management. Once these capabilities are in place, companies can choose strategic robotics suppliers. These partners will be able to help the company choose which processes and technologies are most suitable for their business. Simulation models can help with robotics.
The use of advanced robotics is rapidly evolving across numerous industries. Robotic automation can be applied in many areas, such as aerospace, medical and automotive manufacturing. This technology has made manufacturing more efficient. Robotic automation can reduce human labor costs and save energy. It works 24 hours per day without the need to turn on lights.
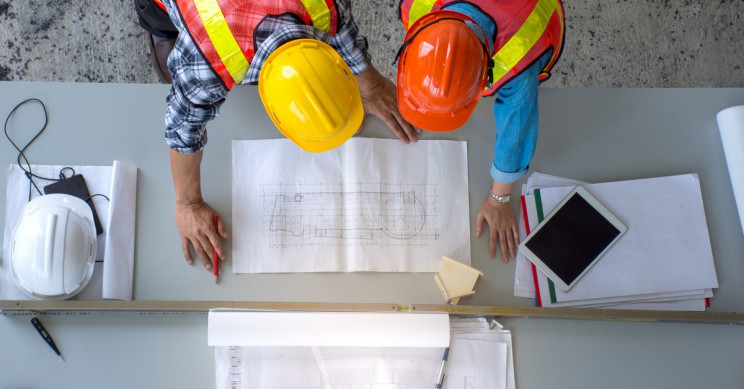
Material deposition
Material deposition plays an important role in advanced manufacturing. This involves the use of both arc plasma energy sources and laser beam to deposit thin film of a substance on a target. A substrate is usually made up of wire or powder. The deposition takes place in an inert or vacuum. Other energy sources could also be utilized.
Plasma metal deposition is one promising technique for direct-energy deposition. This involves using a plasma source to deposit the metals. The process can be used with wire, powder, and both as a feedstock. It can also produce large, complex components. This process allows for a shorter lead time and reduces the amount of machine work.
This process can be used on ceramics, metals, and polymers. Metals can be used as wire or in powder form.
FAQ
What can I do to learn more about manufacturing?
Experience is the best way for you to learn about manufacturing. If that is not possible, you could always read books or view educational videos.
What do we need to know about Manufacturing Processes in order to learn more about Logistics?
No. It doesn't matter if you don't know anything about manufacturing before you learn about logistics. Knowing about manufacturing processes will help you understand how logistics works.
What is the responsibility of a manufacturing manager?
A manufacturing manager must ensure that all manufacturing processes are efficient and effective. They should be aware of any issues within the company and respond accordingly.
They should also learn how to communicate effectively with other departments, including sales and marketing.
They should be informed about industry trends and be able make use of this information to improve their productivity and efficiency.
Why is logistics important in manufacturing?
Logistics are an essential part of any business. They are essential to any business's success.
Logistics are also important in reducing costs and improving efficiency.
Statistics
- (2:04) MTO is a production technique wherein products are customized according to customer specifications, and production only starts after an order is received. (oracle.com)
- You can multiply the result by 100 to get the total percent of monthly overhead. (investopedia.com)
- Job #1 is delivering the ordered product according to specifications: color, size, brand, and quantity. (netsuite.com)
- Many factories witnessed a 30% increase in output due to the shift to electric motors. (en.wikipedia.org)
- According to a Statista study, U.S. businesses spent $1.63 trillion on logistics in 2019, moving goods from origin to end user through various supply chain network segments. (netsuite.com)
External Links
How To
How to use 5S to increase Productivity in Manufacturing
5S stands for "Sort", "Set In Order", "Standardize", "Separate" and "Store". Toyota Motor Corporation created the 5S methodology in 1954. This methodology helps companies improve their work environment to increase efficiency.
The basic idea behind this method is to standardize production processes, so they become repeatable, measurable, and predictable. It means tasks like cleaning, sorting or packing, labeling, and storing are done every day. This knowledge allows workers to be more efficient in their work because they are aware of what to expect.
Implementing 5S involves five steps: Sort, Set in Order, Standardize Separate, Store, and Each step has a different action and leads to higher efficiency. If you sort items, it makes them easier to find later. When you arrange items, you place them together. Once you have separated your inventory into groups and organized them, you will store these groups in easily accessible containers. You can also label your containers to ensure everything is properly labeled.
Employees need to reflect on how they do their jobs. Employees need to understand the reasons they do certain jobs and determine if there is a better way. To be successful in the 5S system, employees will need to acquire new skills and techniques.
The 5S method not only increases efficiency but also boosts morale and teamwork. Once they start to notice improvements, they are motivated to keep working towards their goal of increasing efficiency.