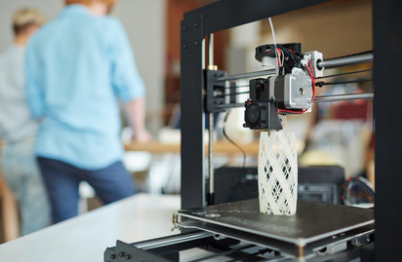
OEE stands for Overall Equipment Efficiency. It is a metric for assessing the performance of equipment. This article will discuss the definition of OEE as well as how to calculate it. It is a best-practice metric that measures availability, performance, and quality. OEE is used by manufacturers to increase production and reduce downtime. It helps manufacturers save money.
OEE is a labor efficiency metric
OEE is a measure of overall production quality. It measures the interaction between availability, quality, performance. OEE represents the loss of time due to inconsistent production. These include the time down, rate fluctuations in process, scrap, and any rework that is generated during operative modes.
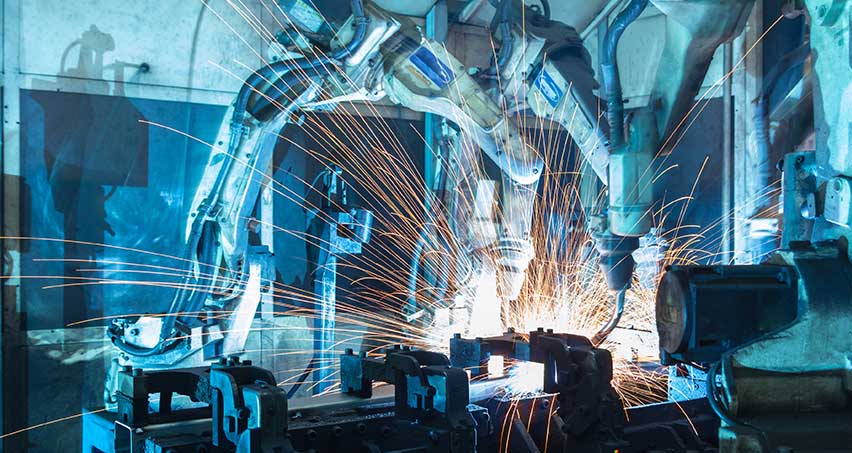
It is based on Availability, Performance and Quality
OEE is an OPM methodology for production management that emphasizes the importance and performance of quality, availability, and performance. The time a product or service is made available for sale or use is called availability. It may also be defined as the period between the delivery of a product or service to a customer and its recovery, or the interval between scrapping and repair. Performance is directly related to the quality of a business. An effective way to measure performance is to hire a professional company that can assess your business processes and provide recommendations for improvement.
It is a best practices metric
OEE can be used to improve and measure your operation. This metric gives you different levels to analyze your operation, helping you to reduce waste and improve efficiency. It is important to remember that this metric cannot be used as the ultimate metric. You should pilot any OEE improvement program before you start it.
It is a directional measure
OEE, in addition to being a directional measure that allows you to compare the performance across similar types of machines within a company, is also defined. Companies can track the efficiency of their machines by measuring it consistently across all machines.
It is the TPM metric.
An important tool to analyze production efficiency is the overall equipment effectiveness (OEE). It measures production inefficiencies and losses in three key areas: availability and performance. This metric can be used for monitoring and identifying areas that need improvement.
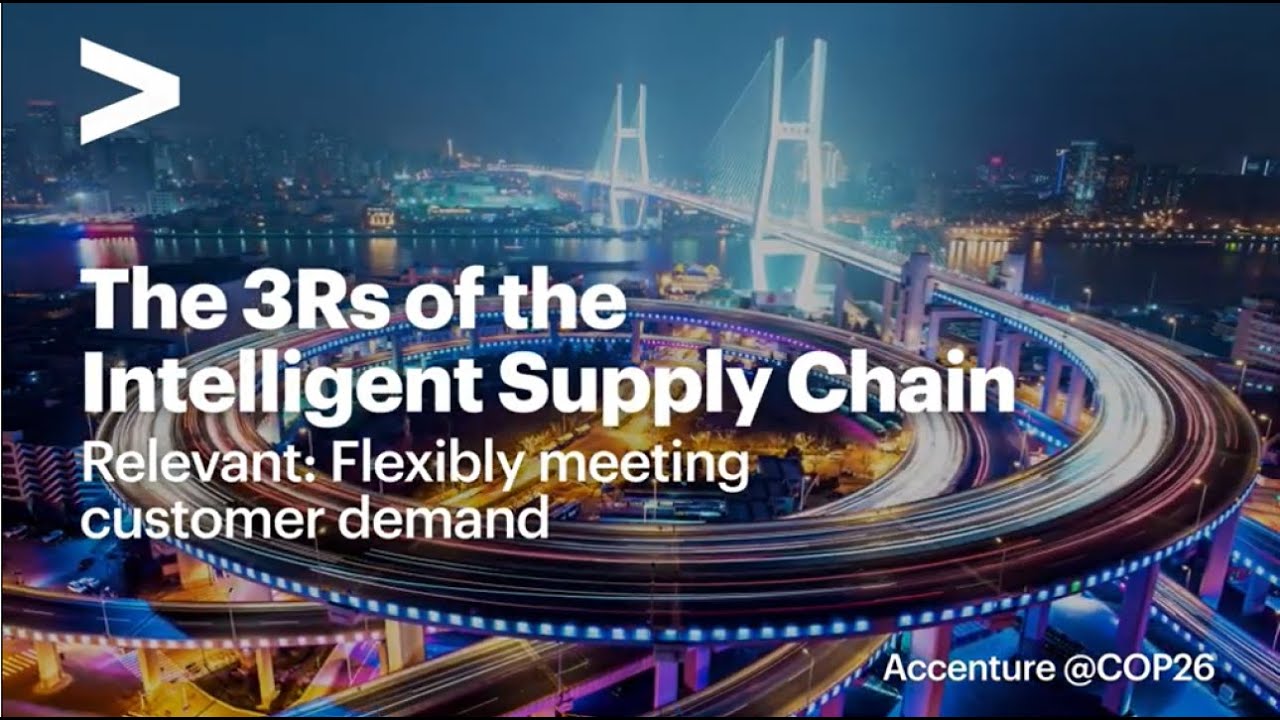
It is a manufacturing best practise
OEE stands to indicate overall equipment effectiveness. It is the ratio of how much a machine or cell can produce in a given time period to the actual time it takes to make that product. It is important to minimize downtime and maximize OEE. Manufacturing operations can also improve quality and reduce cost.
FAQ
How does a production planner differ from a project manager?
The primary difference between a producer planner and a manager of a project is that the manager usually plans and organizes the whole project, while a production planner is only involved in the planning stage.
What's the difference between Production Planning & Scheduling?
Production Planning (PP) is the process of determining what needs to be produced at any given point in time. This is done through forecasting demand and identifying production capacities.
Scheduling refers the process by which tasks are assigned dates so that they can all be completed within the given timeframe.
What do you mean by warehouse?
A warehouse or storage facility is where goods are stored before they are sold. You can have it indoors or outdoors. It could be one or both.
What is it like to manage a logistics company?
It takes a lot of skills and knowledge to run a successful logistics business. To communicate effectively with clients and suppliers, you must be able to communicate well. You must be able analyze data and draw out conclusions. You must be able manage stress and pressure under pressure. To improve efficiency, you must be innovative and creative. To motivate and guide your team towards reaching organizational goals, you must have strong leadership skills.
It is also important to be efficient and well organized in order meet deadlines.
How can we improve manufacturing efficiency?
The first step is to identify the most important factors affecting production time. Next, we must find ways to improve those factors. If you aren't sure where to begin, think about the factors that have the greatest impact on production time. Once you've identified them all, find solutions to each one.
What are the 7 Rs of logistics?
The acronym 7Rs of Logistics refers to the seven core principles of logistics management. It was created by the International Association of Business Logisticians and published in 2004 under its "Seven Principles of Logistics Management".
The following letters make up the acronym:
-
Responsible - to ensure that all actions are within the legal requirements and are not detrimental to others.
-
Reliable - have confidence in the ability to deliver on commitments made.
-
Reasonable - use resources efficiently and don't waste them.
-
Realistic – consider all aspects of operations, from cost-effectiveness to environmental impact.
-
Respectful - show respect and treat others fairly and fairly
-
Reliable - Find ways to save money and increase your productivity.
-
Recognizable - Provide value-added services to customers
How can I find out more about manufacturing?
You can learn the most about manufacturing by getting involved in it. If that is not possible, you could always read books or view educational videos.
Statistics
- According to a Statista study, U.S. businesses spent $1.63 trillion on logistics in 2019, moving goods from origin to end user through various supply chain network segments. (netsuite.com)
- Many factories witnessed a 30% increase in output due to the shift to electric motors. (en.wikipedia.org)
- According to the United Nations Industrial Development Organization (UNIDO), China is the top manufacturer worldwide by 2019 output, producing 28.7% of the total global manufacturing output, followed by the United States, Japan, Germany, and India.[52][53] (en.wikipedia.org)
- It's estimated that 10.8% of the U.S. GDP in 2020 was contributed to manufacturing. (investopedia.com)
- You can multiply the result by 100 to get the total percent of monthly overhead. (investopedia.com)
External Links
How To
How to Use Lean Manufacturing in the Production of Goods
Lean manufacturing (or lean manufacturing) is a style of management that aims to increase efficiency, reduce waste and improve performance through continuous improvement. It was first developed in Japan in the 1970s/80s by Taiichi Ahno, who was awarded the Toyota Production System (TPS), award from KanjiToyoda, the founder of TPS. Michael L. Watkins published the original book on lean manufacturing, "The Machine That Changed the World," in 1990.
Lean manufacturing is often defined as a set of principles used to improve the quality, speed, and cost of products and services. It is about eliminating defects and waste from all stages of the value stream. Lean manufacturing can be described as just-in–time (JIT), total productive maintenance, zero defect (TPM), or even 5S. Lean manufacturing seeks to eliminate non-value added activities, such as inspection, work, waiting, and rework.
Lean manufacturing improves product quality and costs. It also helps companies reach their goals quicker and decreases employee turnover. Lean manufacturing is considered one of the most effective ways to manage the entire value chain, including suppliers, customers, distributors, retailers, and employees. Lean manufacturing is widely used in many industries. Toyota's philosophy has been a key driver of success in many industries, including automobiles and electronics.
Lean manufacturing includes five basic principles:
-
Define Value: Identify the social value of your business and what sets you apart.
-
Reduce waste - Get rid of any activity that does not add value to the supply chain.
-
Create Flow. Ensure that your work is uninterrupted and flows seamlessly.
-
Standardize and simplify – Make processes as repeatable and consistent as possible.
-
Build Relationships- Develop personal relationships with both internal as well as external stakeholders.
Lean manufacturing isn’t new, but it has seen a renewed interest since 2008 due to the global financial crisis. Many businesses have adopted lean production techniques to make them more competitive. Some economists even believe that lean manufacturing can be a key factor in economic recovery.
With many benefits, lean manufacturing is becoming more common in the automotive industry. These include improved customer satisfaction, reduced inventory levels, lower operating costs, increased productivity, and better overall safety.
It can be applied to any aspect of an organisation. However, it is particularly useful when applied to the production side of an organization because it ensures that all steps in the value chain are efficient and effective.
There are three main types:
-
Just-in-Time Manufacturing: Also known as "pull systems", this type of lean manufacturing uses just-in-time manufacturing (JIT). JIT refers to a system in which components are assembled at the point of use instead of being produced ahead of time. This approach aims to reduce lead times, increase the availability of parts, and reduce inventory.
-
Zero Defects Manufacturing (ZDM): ZDM focuses on ensuring that no defective units leave the manufacturing facility. If a part needs to be fixed during the assembly line, it should be repaired rather than scrapped. This applies to finished goods that may require minor repairs before shipment.
-
Continuous Improvement (CI): CI aims to improve the efficiency of operations by continuously identifying problems and making changes in order to eliminate or minimize waste. Continuous improvement involves continuous improvement of processes and people as well as tools.