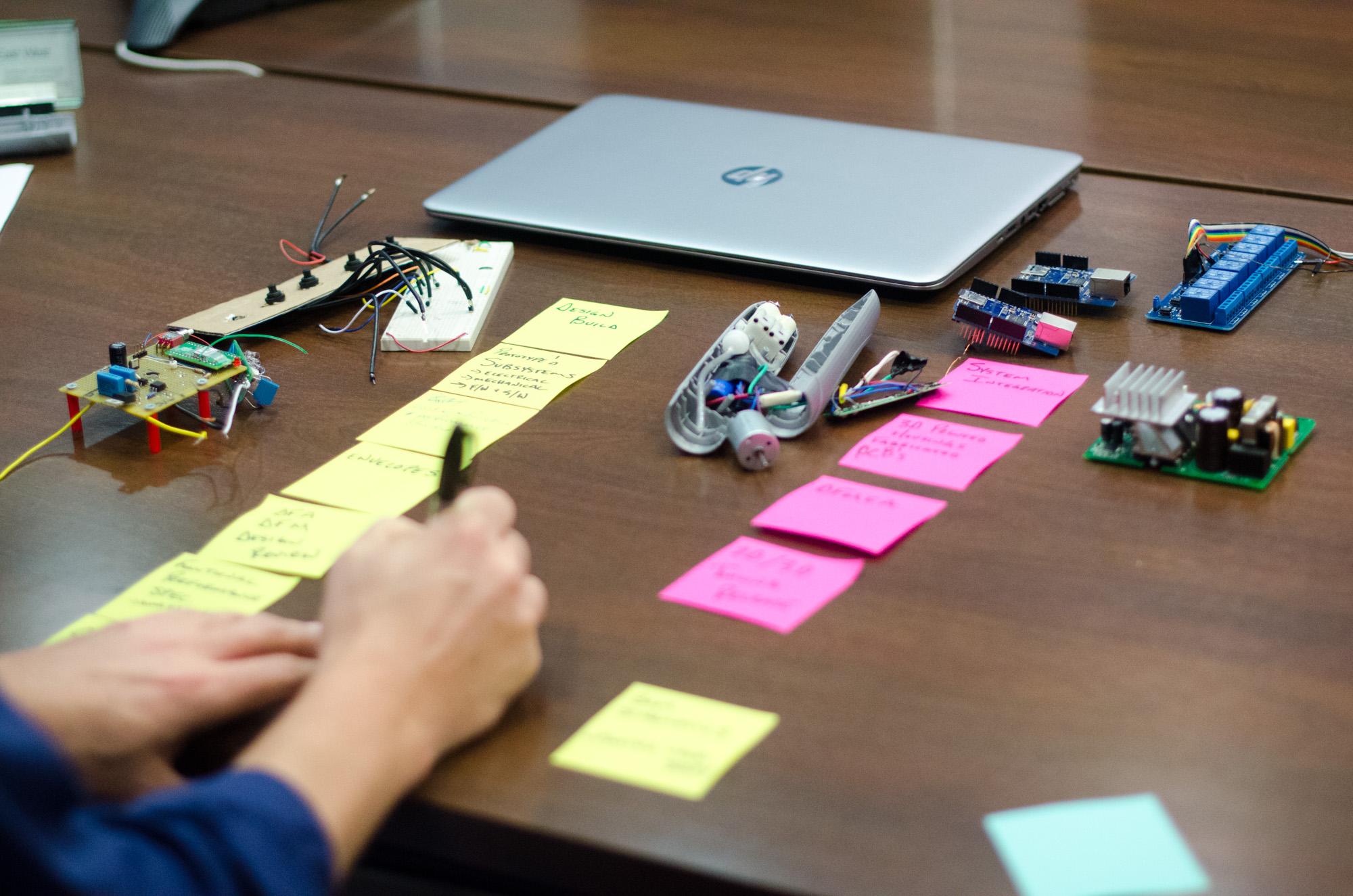
The HEROES PROGRAM provides affordable housing for military families and homeowners who want to save money. It works with radio stations, web networks, and community groups all across the country in order to recognize bravery of our servicemen. In addition, it connects military families with legal experts who specialize in military law and child support issues.
Heroes to Heroes is a non-profit organization with 501(c), which provides peer support and suicide prevention for combat veterans. Their programs include a 12-month curriculum focusing on emotional strength, a 10-day trip to Israel, and spiritual healing. Heroes To Heroes also assists those who have suffered Moral Injuries. It also provides suicide prevention training and peer support to veterans who have experienced PTSD and combat injuries.
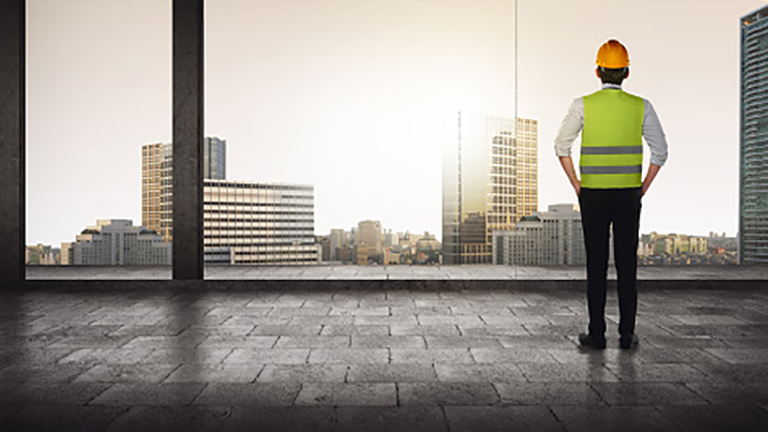
Hiring Our Heroes seeks to identify job opportunities for our veterans. The program helps to identify people from all backgrounds including veterans, active-duty military families, as well as other members the military community. It also assists veterans in finding jobs and provides guidance for military families, especially those with children. In addition, the organization offers a scholarship for children of veterans, as well as other forms of assistance.
Heroes MAKE America helps veterans identify and place them in jobs. It also offers career readiness training, certification and career readiness preparation. The program has placed graduates with 250 companies in 42 states. They work with local technical college and organizations to help veterans find jobs. The program has expanded since COVID-19, and will soon launch a training site in Georgia. Fort Riley is also home to many of its programs. The program has placed 136 graduates in different military occupational specialties. This program is an invaluable resource for veterans looking to work in the manufacturing industry.
Fort Riley will continue to expand its Heroes MAKE America program and will introduce new features for 2021. They will feature virtual reality simulations. These virtual training programs allow transitioning service personnel to participate even if they don't have a computer. They will be able connect with other veterans who participated in the program. The program will grow after COVID-19 and will help veterans find work in the manufacturing industry.
The HEROES Leadership project brings together a diverse group of people who share their experience and talents to create a positive community for youth. The group also helps create an environment where youth can feel safe and supported. It is part of the Re-Envisioning Foster Care in America Movement. Members contribute their experiences, talents, and voice to help create a more supportive environment for youth.
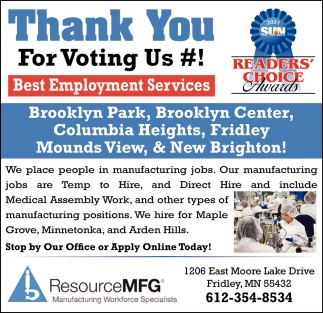
Homes for Heroes also offers discounts for real estate agent commissions, and home inspection fees. The program has been very successful, and has taken off nationally. The program offers discounts to active or former military members, teachers, and health care professionals. On average, a Hero saves about $2400.
FAQ
What is the role and responsibility of a Production Planner?
Production planners make sure that every aspect of the project is delivered on-time, within budget, and within schedule. They make sure that the product and services meet client expectations.
What is the difference in Production Planning and Scheduling, you ask?
Production Planning (PP) is the process of determining what needs to be produced at any given point in time. This can be done by forecasting demand and identifying production capabilities.
Scheduling is the process that assigns dates to tasks so they can get completed within a given timeframe.
What is production planning?
Production Planning involves developing a plan for all aspects of the production, including scheduling, budgeting, casting, crew, location, equipment, props, etc. This document aims to ensure that everything is planned and ready when you are ready to shoot. It should also contain information on achieving the best results on set. This information includes locations, crew details and equipment requirements.
The first step in filming is to define what you want. You might have an idea of where you want to film, or you may have specific locations or sets in mind. Once you have identified the scenes and locations, you can start to determine which elements are required for each scene. You might decide you need a car, but not sure what make or model. In this case, you could start looking up cars online to find out what models are available and then narrow your choices by choosing between different makes and models.
After you've found the perfect car, it's time to start thinking about adding extras. Do you have people who need to be seated in the front seat? Or maybe you just need someone to push the car around. Maybe you want to change the interior color from black to white? These questions will help guide you in determining the ideal look and feel for your car. Another thing you can do is think about what type of shots are desired. Do you want to film close-ups, or wider angles? Perhaps you want to show the engine or the steering wheel? All of these things will help you identify the exact style of car you want to film.
Once you have established all the details, you can create a schedule. You can create a schedule that will outline when you must start and finish your shoots. Every day will have a time for you to arrive at the location, leave when you are leaving and return home when you are done. Everyone knows exactly what they should do and when. You can also make sure to book extra staff in advance if you have to hire them. It's not worth paying someone to show up if you haven't told him.
It is important to calculate the amount of filming days when you are creating your schedule. Some projects only take one or two days, while others may last weeks. When creating your schedule, be aware of whether you need more shots per day. Multiplying takes in the same area will result both in increased costs and a longer time. It's better to be safe than sorry and shoot less takes if you're not certain whether you need more takes.
Budgeting is another crucial aspect of production plan. You will be able to manage your resources if you have a realistic budget. If you have to reduce your budget due to unexpected circumstances, you can always lower it later. It is important to not overestimate how much you will spend. You'll end up with less money after paying for other things if the cost is underestimated.
Production planning is a detailed process. But, once you understand the workings of everything, it becomes easier for future projects to be planned.
Statistics
- According to a Statista study, U.S. businesses spent $1.63 trillion on logistics in 2019, moving goods from origin to end user through various supply chain network segments. (netsuite.com)
- In 2021, an estimated 12.1 million Americans work in the manufacturing sector.6 (investopedia.com)
- It's estimated that 10.8% of the U.S. GDP in 2020 was contributed to manufacturing. (investopedia.com)
- Job #1 is delivering the ordered product according to specifications: color, size, brand, and quantity. (netsuite.com)
- (2:04) MTO is a production technique wherein products are customized according to customer specifications, and production only starts after an order is received. (oracle.com)
External Links
How To
Six Sigma and Manufacturing
Six Sigma refers to "the application and control of statistical processes (SPC) techniques in order to achieve continuous improvement." It was developed by Motorola's Quality Improvement Department at their plant in Tokyo, Japan, in 1986. Six Sigma's core idea is to improve the quality of processes by standardizing and eliminating defects. This method has been adopted by many companies in recent years as they believe there are no perfect products or services. Six Sigma's primary goal is to reduce variation from the average value of production. If you take a sample and compare it with the average, you will be able to determine how much of the production process is different from the norm. If it is too large, it means that there are problems.
The first step toward implementing Six Sigma is understanding how variability works in your business. Once you have this understanding, you will need to identify sources and causes of variation. You'll also want to determine whether these variations are random or systematic. Random variations are caused by human errors. Systematic variations can be caused by outside factors. For example, if you're making widgets, and some of them fall off the assembly line, those would be considered random variations. If however, you notice that each time you assemble a widget it falls apart in exactly the same spot, that is a problem.
Once you've identified where the problems lie, you'll want to design solutions to eliminate those problems. It might mean changing the way you do business or redesigning it entirely. You should then test the changes again after they have been implemented. If they don't work you need to rework them and come up a better plan.