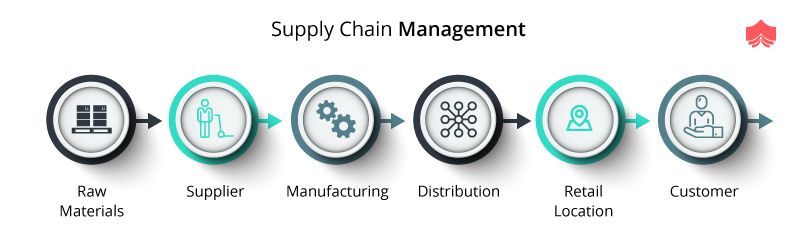
Lean system management reduces waste at the workplace. The belief is that each activity or process within a company must add value to a product or service provided for the customer. It can be done by eliminating activities that don't add value, and working to create more.
A lean management is designed to increase the performance of an organization. It helps employees to understand their purpose and goals.
The first step in lean system management is to identify what value is. The first step is to identify what the customer wants, and then create a solution which provides this value. It is possible to achieve this by making everything, from the production process through to customer service efficient and consistent.
You can reduce costs and improve efficiency by applying lean manufacturing principles when making products. But, your staff must be on board. The results of the program could be disastrous if the staff is not committed.
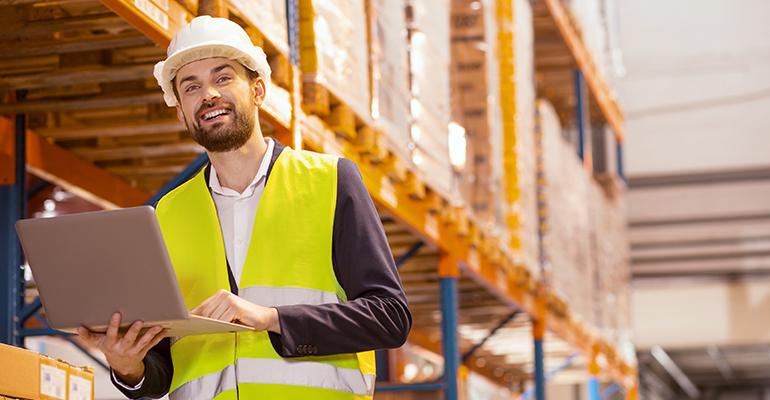
You must also ensure that the supply chain of your company is healthy. The majority of lean projects require the supply chain be retooled to work properly.
To achieve this, you should make sure that your staff receives proper training on lean methods. It is important that your staff understands what waste is, and why it should be removed from the production process.
The importance of teamwork should be taken into consideration when implementing the lean system. It may be hard to achieve but is an important aspect of the lean system.
Your team will be able to create better products and services, and your bottom line will increase over time. You can encourage this by giving them a chance to meet with each other regularly and discuss ways to get rid of wastes in their work.
Lean managers will help you reach this goal by ensuring workers are trained properly and have the knowledge to implement these techniques. They can also help to keep your production processes running smoothly and efficiently by keeping the team informed of any potential issues.
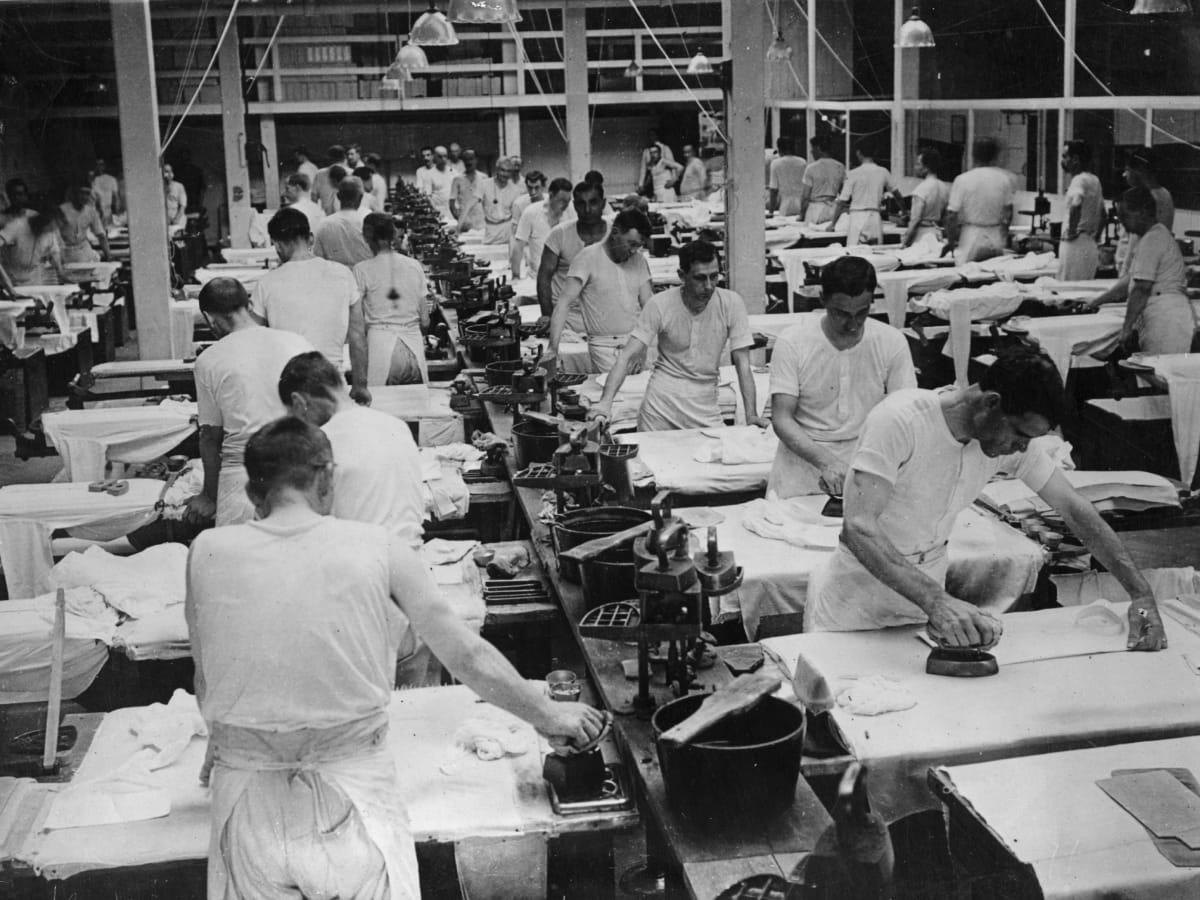
The final stage in lean management is to evaluate and improve the implementation of each procedure. You can do this by tracking each project's progress and making sure that all necessary changes are made.
According to your organization’s size, you might need to hire a manager to oversee lean operations. Searching for lean management positions or job boards can help you find candidates.
FAQ
What do we need to know about Manufacturing Processes in order to learn more about Logistics?
No. It doesn't matter if you don't know anything about manufacturing before you learn about logistics. It is important to know about the manufacturing processes in order to understand how logistics works.
What are the 7 Rs of logistics.
The 7R's of Logistics is an acronym for the seven basic principles of logistics management. It was created by the International Association of Business Logisticians and published in 2004 under its "Seven Principles of Logistics Management".
The acronym consists of the following letters:
-
Responsible - ensure that all actions taken are within legal requirements and are not harmful to others.
-
Reliable - You can have confidence that you will fulfill your promises.
-
It is reasonable to use resources efficiently and not waste them.
-
Realistic - Consider all aspects of operations, including environmental impact and cost effectiveness.
-
Respectful: Treat others with fairness and equity
-
Resourceful - look for opportunities to save money and increase productivity.
-
Recognizable - Provide value-added services to customers
How can manufacturing efficiency be improved?
First, determine which factors have the greatest impact on production time. We must then find ways that we can improve these factors. If you aren't sure where to begin, think about the factors that have the greatest impact on production time. Once you identify them, look for solutions.
How can manufacturing excess production be decreased?
The key to reducing overproduction lies in developing better ways to manage inventory. This would reduce the time spent on unproductive activities like purchasing, storing and maintaining excess stock. By doing this, we could free up resources for other productive tasks.
You can do this by adopting a Kanban method. A Kanban board, a visual display to show the progress of work, is called a Kanban board. In a Kanban system, work items move through a sequence of states until they reach their final destination. Each state represents a different priority.
To illustrate, work can move from one stage or another when it is complete enough for it to be moved to a new stage. If a task is still in its beginning stages, it will continue to be so until it reaches the end.
This helps to keep work moving forward while ensuring that no work is left behind. A Kanban board allows managers to monitor how much work is being completed at any given moment. This allows them the ability to adjust their workflow using real-time data.
Lean manufacturing is another way to manage inventory levels. Lean manufacturing is about eliminating waste from all stages of the production process. Any product that isn't adding value can be considered waste. Here are some examples of common types.
-
Overproduction
-
Inventory
-
Unnecessary packaging
-
Excess materials
By implementing these ideas, manufacturers can improve efficiency and cut costs.
What's the difference between Production Planning & Scheduling?
Production Planning (PP) is the process of determining what needs to be produced at any given point in time. This is accomplished by forecasting the demand and identifying production resources.
Scheduling is the process of assigning specific dates to tasks so they can be completed within the specified timeframe.
What is manufacturing and logistics?
Manufacturing refers to the process of making goods using raw materials and machines. Logistics is the management of all aspects of supply chain activities, including procurement, production planning, distribution, warehousing, inventory control, transportation, and customer service. Logistics and manufacturing are often referred to as one thing. It encompasses both the creation of products and their delivery to customers.
What are the responsibilities for a manufacturing manager
The manufacturing manager should ensure that every manufacturing process is efficient and effective. They should also be aware and responsive to any company problems.
They should also be able communicate with other departments, such as sales or marketing.
They should be up to date on the latest trends and be able apply this knowledge to increase productivity and efficiency.
Statistics
- Job #1 is delivering the ordered product according to specifications: color, size, brand, and quantity. (netsuite.com)
- In 2021, an estimated 12.1 million Americans work in the manufacturing sector.6 (investopedia.com)
- Many factories witnessed a 30% increase in output due to the shift to electric motors. (en.wikipedia.org)
- (2:04) MTO is a production technique wherein products are customized according to customer specifications, and production only starts after an order is received. (oracle.com)
- You can multiply the result by 100 to get the total percent of monthly overhead. (investopedia.com)
External Links
How To
How to Use lean manufacturing in the Production of Goods
Lean manufacturing refers to a method of managing that seeks to improve efficiency and decrease waste. It was first developed in Japan in the 1970s/80s by Taiichi Ahno, who was awarded the Toyota Production System (TPS), award from KanjiToyoda, the founder of TPS. The first book published on lean manufacturing was titled "The Machine That Changed the World" written by Michael L. Watkins and published in 1990.
Lean manufacturing, often described as a set and practice of principles, is aimed at improving the quality, speed, cost, and efficiency of products, services, and other activities. It emphasizes the elimination and minimization of waste in the value stream. Lean manufacturing is called just-in-time (JIT), zero defect, total productive maintenance (TPM), or 5S. Lean manufacturing eliminates non-value-added tasks like inspection, rework, waiting.
Lean manufacturing is a way for companies to achieve their goals faster, improve product quality, and lower costs. Lean manufacturing is considered one of the most effective ways to manage the entire value chain, including suppliers, customers, distributors, retailers, and employees. Lean manufacturing is widely used in many industries. Toyota's philosophy is the foundation of its success in automotives, electronics and appliances, healthcare, chemical engineers, aerospace, paper and food, among other industries.
Five basic principles of Lean Manufacturing are included in lean manufacturing
-
Define Value- Identify the added value your company brings to society. What makes you stand out from your competitors?
-
Reduce waste - Get rid of any activity that does not add value to the supply chain.
-
Create Flow - Make sure work runs smoothly without interruptions.
-
Standardize and Simplify – Make processes as consistent, repeatable, and as simple as possible.
-
Build Relationships - Establish personal relationships with both internal and external stakeholders.
Although lean manufacturing has always been around, it is gaining popularity in recent years because of a renewed interest for the economy after 2008's global financial crisis. Many businesses are now using lean manufacturing to improve their competitiveness. In fact, some economists believe that lean manufacturing will be an important factor in economic recovery.
Lean manufacturing is now becoming a common practice in the automotive industry, with many benefits. These include improved customer satisfaction, reduced inventory levels, lower operating costs, increased productivity, and better overall safety.
Lean manufacturing can be applied to almost every aspect of an organization. It is especially useful for the production aspect of an organization, as it ensures that every step in the value chain is efficient and effective.
There are three main types of lean manufacturing:
-
Just-in-Time Manufacturing: Also known as "pull systems", this type of lean manufacturing uses just-in-time manufacturing (JIT). JIT refers to a system in which components are assembled at the point of use instead of being produced ahead of time. This approach is designed to reduce lead times and increase the availability of components. It also reduces inventory.
-
Zero Defects Manufacturing (ZDM),: ZDM is a system that ensures no defective units are left the manufacturing facility. If a part needs to be fixed during the assembly line, it should be repaired rather than scrapped. This applies to finished products, which may need minor repairs before they are shipped.
-
Continuous Improvement: Continuous Improvement aims to improve efficiency by continually identifying problems and making adjustments to eliminate or minimize waste. Continuous Improvement involves continuous improvement of processes.