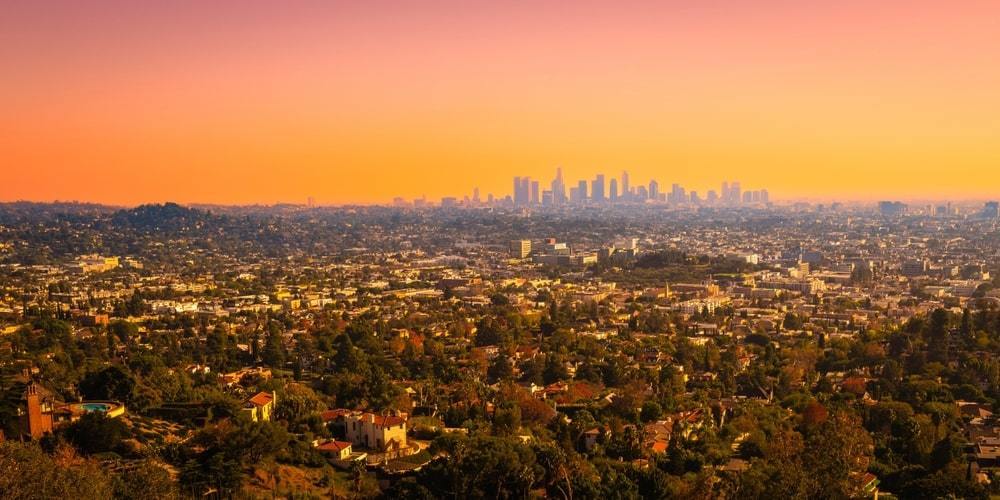
SIPOC Diagram is a visual aid that can be used to identify the inputs as well as outputs in a process. It is also a great way for team members to identify improvements or gaps in the business.
The sipoc diagram is often a part of the DMAIC process improvement cycle, which is a framework used for creating a business process that can be improved through analysis and continuous improvement. The sipoc diagram helps teams and sponsors to agree on project scope and boundaries, as well Key Process Input Variables.
What Is SIPOC?
The SIPOC diagram is a simple and easy-to-follow visual representation of the inputs and outputs of a specific business process. Its primary purpose is to help the team understand and analyze the business process at a high level, providing a clear picture of the steps that are needed to transform inputs into desired outputs.
What is the origin of the Sipoc Diagram?
The sipoc Diagram can be traced all the way back to late 1980s. This was part of Total Quality Management (TQM), a model of business process improvement based on Six Sigma. The sipoc diagram has been used in lean production and business improvement programs for many years. It's a great tool to streamline processes, identify potential improvements and improve communication between stakeholders.
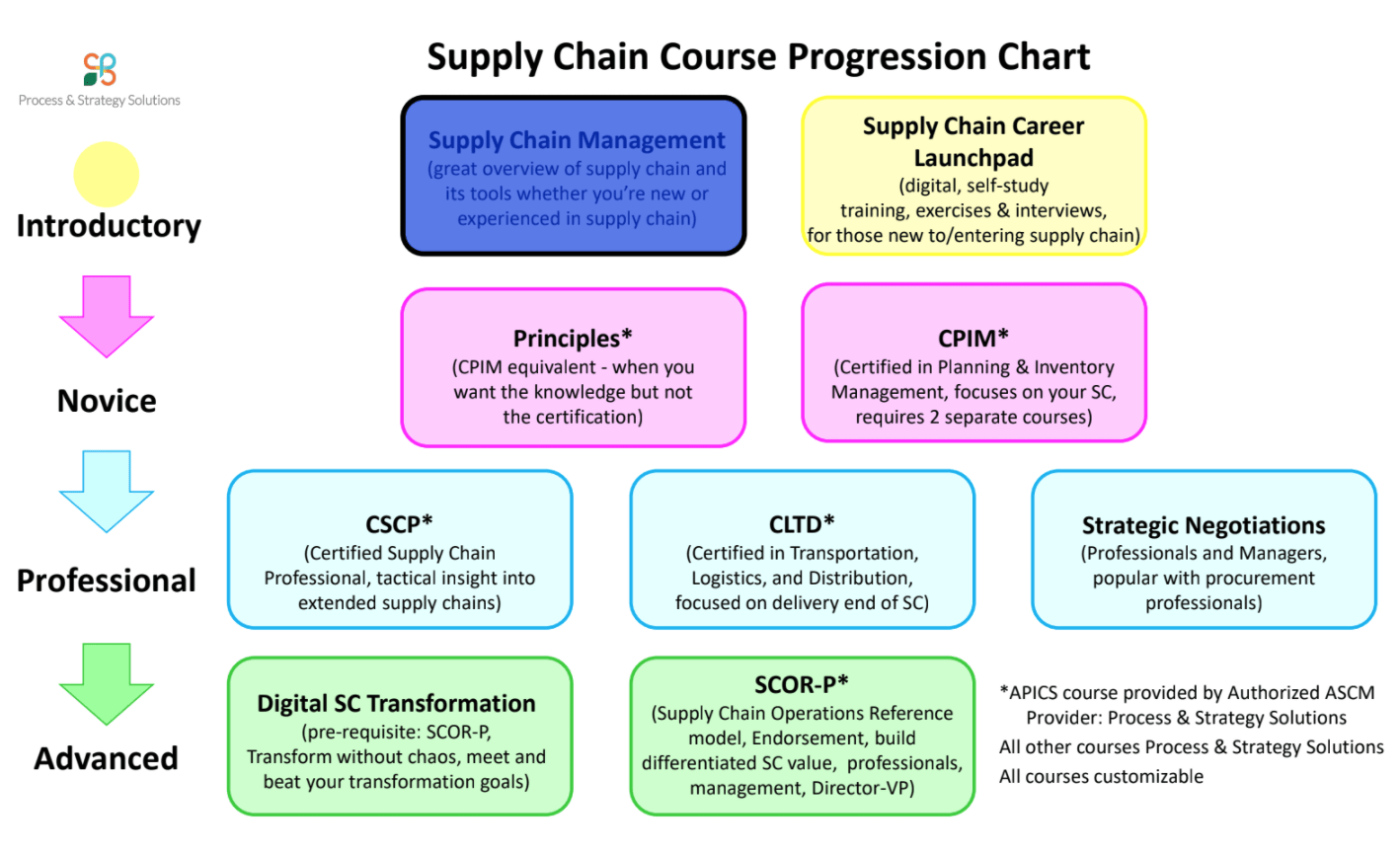
How do you make a SIPOC?
To begin, you must first choose the process that you want to analyze. This will ensure that you and your staff focus on only the most important aspects and don't miss any details.
The next step is to determine what inputs are required for the process to work, and who provides them. List the contact information of each supplier along with their raw materials.
You can also list both internal clients and external clients that will be receiving the outputs. It can be a good way to check if the company offers high-quality goods and services.
Inputs This is the very first section on a SIPOC and it contains all the requirements for material or information. Material can be a physical good, like a product, but it can also be information, like a report.
Outputs is the second part of a SIPOC Diagram. It is usually a list that includes the products, services or actions completed as a result. The outputs need to reflect the value the customer expects from the process and meet their needs.

Customers: This final section of the SIPOC diagram identifies customers, both inside and outside the organization. This could include the maintenance staff, line operators, or other internal and/or external clients.
A SIPOC diagram is a powerful visual tool that can be used to improve business processes and improve overall communication between all stakeholders. It is simple to create and a good way to ensure that team members are aware of the business processes under consideration. It's best to use templates that include all key diagram components such as inputs or outputs. A template will save you time and effort as it allows you to quickly draw the diagram.
FAQ
What does it mean to be a manufacturer?
Manufacturing Industries are companies that manufacture products. Consumers are the people who purchase these products. These companies employ many processes to achieve this purpose, such as production and distribution, retailing, management and so on. These companies produce goods using raw materials and other equipment. This includes all types if manufactured goods.
What are manufacturing and logistic?
Manufacturing is the act of producing goods from raw materials using machines and processes. Logistics manages all aspects of the supply chain, including procurement, production planning and distribution, inventory control, transportation, customer service, and transport. Manufacturing and logistics are often considered together as a broader term that encompasses both the process of creating products and delivering them to customers.
What is the difference between Production Planning, Scheduling and Production Planning?
Production Planning (PP), also known as forecasting and identifying production capacities, is the process that determines what product needs to be produced at any particular time. This is accomplished by forecasting the demand and identifying production resources.
Scheduling refers the process by which tasks are assigned dates so that they can all be completed within the given timeframe.
Statistics
- According to a Statista study, U.S. businesses spent $1.63 trillion on logistics in 2019, moving goods from origin to end user through various supply chain network segments. (netsuite.com)
- In the United States, for example, manufacturing makes up 15% of the economic output. (twi-global.com)
- According to the United Nations Industrial Development Organization (UNIDO), China is the top manufacturer worldwide by 2019 output, producing 28.7% of the total global manufacturing output, followed by the United States, Japan, Germany, and India.[52][53] (en.wikipedia.org)
- Job #1 is delivering the ordered product according to specifications: color, size, brand, and quantity. (netsuite.com)
- You can multiply the result by 100 to get the total percent of monthly overhead. (investopedia.com)
External Links
How To
How to Use Lean Manufacturing in the Production of Goods
Lean manufacturing is an approach to management that aims for efficiency and waste reduction. It was developed in Japan between 1970 and 1980 by Taiichi Ohno. TPS founder Kanji Tyoda gave him the Toyota Production System, or TPS award. The first book published on lean manufacturing was titled "The Machine That Changed the World" written by Michael L. Watkins and published in 1990.
Lean manufacturing is often defined as a set of principles used to improve the quality, speed, and cost of products and services. It emphasizes eliminating waste and defects throughout the value stream. The five-steps of Lean Manufacturing are just-in time (JIT), zero defect and total productive maintenance (TPM), as well as 5S. Lean manufacturing emphasizes reducing non-value-added activities like inspection, rework and waiting.
In addition to improving product quality and reducing costs, lean manufacturing helps companies achieve their goals faster and reduces employee turnover. Lean manufacturing is considered one of the most effective ways to manage the entire value chain, including suppliers, customers, distributors, retailers, and employees. Lean manufacturing can be found in many industries. Toyota's philosophy is a great example of this. It has helped to create success in automobiles as well electronics, appliances and healthcare.
Five basic principles of Lean Manufacturing are included in lean manufacturing
-
Define Value - Determine the value that your business brings to society. Also, identify what sets you apart from your competitors.
-
Reduce Waste - Remove any activity which doesn't add value to your supply chain.
-
Create Flow - Make sure work runs smoothly without interruptions.
-
Standardize & Simplify - Make processes as consistent and repeatable as possible.
-
Develop Relationships: Establish personal relationships both with internal and external stakeholders.
Lean manufacturing is not a new concept, but it has been gaining popularity over the last few years due to a renewed interest in the economy following the global financial crisis of 2008. To increase their competitiveness, many businesses have turned to lean manufacturing. In fact, some economists believe that lean manufacturing will be an important factor in economic recovery.
Lean manufacturing is now becoming a common practice in the automotive industry, with many benefits. These include higher customer satisfaction, lower inventory levels, lower operating expenses, greater productivity, and improved overall safety.
It can be applied to any aspect of an organisation. Because it makes sure that all value chains are efficient and effectively managed, Lean Manufacturing is particularly helpful for organizations.
There are three types principally of lean manufacturing:
-
Just-in Time Manufacturing, (JIT): This kind of lean manufacturing is also commonly known as "pull-systems." JIT refers to a system in which components are assembled at the point of use instead of being produced ahead of time. This strategy aims to decrease lead times, increase availability of parts and reduce inventory.
-
Zero Defects Manufacturing: ZDM ensures that no defective units leave the manufacturing plant. Repairing a part that is damaged during assembly should be done, not scrapping. This is also true for finished products that require minor repairs before shipping.
-
Continuous Improvement (CI), also known as Continuous Improvement, aims at improving the efficiency of operations through continuous identification and improvement to minimize or eliminate waste. Continuous improvement refers to continuous improvement of processes as well people and tools.