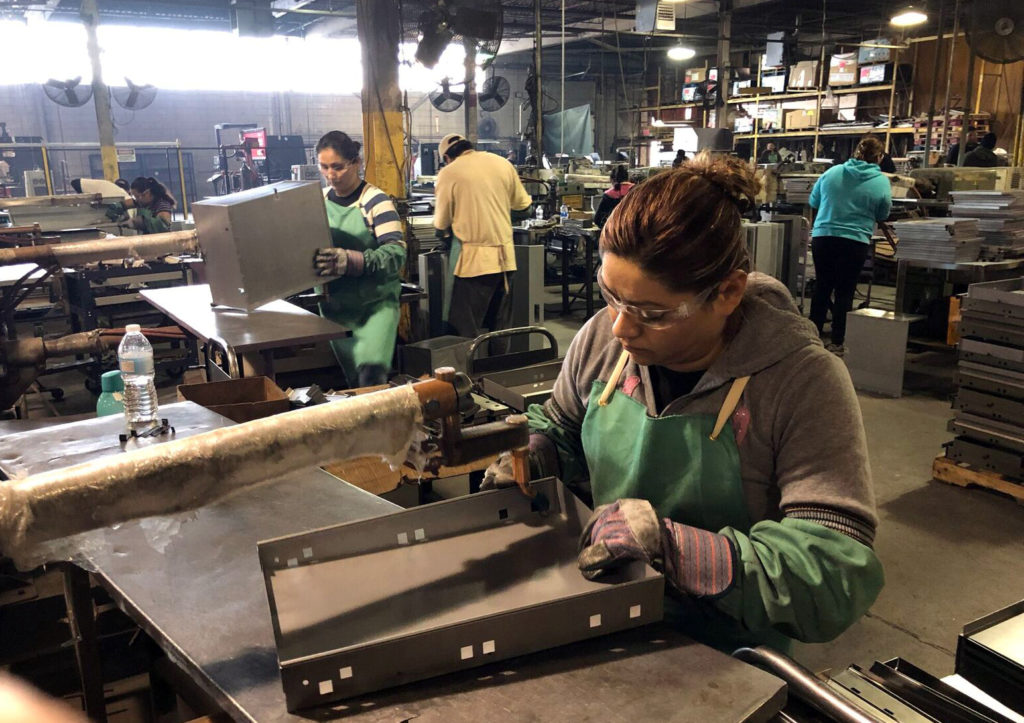
Here's the latest news about manufacturing. Fusion 360 community members share updates about manufacturing innovation and recap the week's events. Fusion 360 covers all aspects of the industry, including Alexandria Industries and Festo's expansion plans. Fusion 360 covers many topics, including news on additive manufacturing and product launches. Here are some articles that have been published recently about manufacturing innovation. Continue reading to find out more.
Alexandria Industries
Alexandria Industries has announced plans to expand their operation in Douglas County. Their current workforce is 480, but they plan to invest several millions in the new facility. Alexandria Industries' growth has been faster than their revenue and employment levels before the recession. However, they are still struggling to find qualified candidates for 50 new positions. These positions have a starting salary of $15- $30 per hour and include benefits. Alexandria Industries offers a great career opportunity for those who are interested in a change.
Alexandria Industries recently appointed new management to aid their growth. Jonathan D. Olson, Alexandria Industries' former CFO, will now take over as the company's CFO. He is committed to investing and supporting the company's employees. He joined the company in the role of CFO. His plans include improving the working conditions of employees as well as investing in training programs. Alexandria Plastics, Inc., the manufacturer of plastic injections and foam-molded components, will be incorporated into the new acquisition, which will allow the company to expand its capabilities.
Festo U.S. expansion plans
Festo Corp. just announced expansion plans for North American manufacturing operations. The company will increase its presence in Mason by three times and create 350 additional jobs. The expansion will add 350 jobs over five years and cost $90 million. In addition to manufacturing, Festo will provide industrial training solutions and support services. A new Didactic Learning Centre will be added to the expansion, which will serve colleges and manufacturing companies throughout the Tristate region.
The expansion will create a new facility in Mason, Ohio, dedicated to manufacturing automation components. It will house both a Research and Development Center and Global Production Center. Each facility will have more than 1000 employees when it is completed. In addition to creating new jobs, the company plans to establish a new research and development center to enhance automation systems. This expansion is part an overall plan to concentrate on the U.S.
Additive Manufacturing
Manufacturers are beginning to recognize the advantages of additive manufacturing in their manufacturing processes, thanks to technological advancements. In order to expand their reach in the global market, a variety of companies have entered into partnerships. Some of these partnerships involve Voxeljet and AGC Ceramic, a glass and ceramic company. Voxeljet will introduce Brightorb ceramic material and the VX1000 to be used for 3D printing ceramic powder. AGC Ceramic also plans to partner with Voxeljet. Other partnerships include Stratasys, which has partnered with Tata Technologies to promote additive manufacturing technologies in India.
New technologies for additive manufacturing are also being developed in conjunction with existing collaboration agreements. Optimus 3D purchased a fourth Renishaw metal additive production system. The company has also increased its 3D printing machine inventory to include metal powder. With these developments, additive manufacture is poised to be an essential component of advanced PLM. The company will become more IoT-oriented as well as integrated. These new developments will lead to the rapid growth of a wide variety of industries.
Collaborative Manufacturing
What is collaborative Manufacturing? Collaborative manufacturing involves input directly from plant floor systems. This information is a significant piece of the management process. This also requires interaction between the manufacturing and design teams. Collaborative manufacturing is a way to increase productivity and improve quality. It also reduces the number of people needed for each production step. But what are the real benefits of collaborative production? Let's take a look at some examples. How can collaborative manufacturing increase plant performance? Learn more.
Many industries are now adopting collaborative manufacturing. It can be used to improve product design, reduce costs, increase product development, and sync inventory with the supply chain. Collaborative manufacturing also helps reduce time to market and volume. It can also cut down on the manufacturing cycle time between designated suppliers. It is important for companies to realize that collaborative manufacturing offers significant benefits for everyone. This isn't for every company. Before adopting collaborative manufacturing, consider the benefits.
FAQ
What are the 7 Rs of logistics?
The acronym 7R's of Logistic is an acronym that stands for seven fundamental principles of logistics management. It was developed and published by the International Association of Business Logisticians in 2004 as part of the "Seven Principles of Logistics Management".
The acronym is composed of the following letters.
-
Responsible - to ensure that all actions are within the legal requirements and are not detrimental to others.
-
Reliable – have faith in your ability and capability to keep promises.
-
Reasonable - make sure you use your resources well and don't waste them.
-
Realistic - Take into consideration all aspects of operations including cost-effectiveness, environmental impact, and other factors.
-
Respectful - treat people fairly and equitably.
-
You are resourceful and look for ways to save money while increasing productivity.
-
Recognizable: Provide customers with value-added service
What is the role of a production manager?
A production planner ensures all aspects of the project are delivered on time, within budget, and within scope. They also ensure that the product/service meets the client’s needs.
Can we automate some parts of manufacturing?
Yes! Automation has been around since ancient times. The wheel was invented by the Egyptians thousands of years ago. We now use robots to help us with assembly lines.
There are many applications for robotics in manufacturing today. These include:
-
Robots for assembly line
-
Robot welding
-
Robot painting
-
Robotics inspection
-
Robots that create products
Manufacturing can also be automated in many other ways. 3D printing, for example, allows us to create custom products without waiting for them to be made.
What does it take to run a logistics business?
It takes a lot of skills and knowledge to run a successful logistics business. Good communication skills are essential to effectively communicate with your suppliers and clients. You will need to know how to interpret data and draw conclusions. You must be able manage stress and pressure under pressure. To increase efficiency and creativity, you need to be creative. Strong leadership qualities are essential to motivate your team and help them achieve their organizational goals.
You must be organized to meet tight deadlines.
Statistics
- In 2021, an estimated 12.1 million Americans work in the manufacturing sector.6 (investopedia.com)
- In the United States, for example, manufacturing makes up 15% of the economic output. (twi-global.com)
- You can multiply the result by 100 to get the total percent of monthly overhead. (investopedia.com)
- [54][55] These are the top 50 countries by the total value of manufacturing output in US dollars for its noted year according to World Bank.[56] (en.wikipedia.org)
- It's estimated that 10.8% of the U.S. GDP in 2020 was contributed to manufacturing. (investopedia.com)
External Links
How To
Six Sigma and Manufacturing
Six Sigma is defined as "the application of statistical process control (SPC) techniques to achieve continuous improvement." It was developed by Motorola's Quality Improvement Department at their plant in Tokyo, Japan, in 1986. Six Sigma's core idea is to improve the quality of processes by standardizing and eliminating defects. Since there are no perfect products, or services, this approach has been adopted by many companies over the years. Six Sigma seeks to reduce variation between the mean production value. You can calculate the percentage of deviation from the norm by taking a sample of your product and comparing it to the average. If the deviation is excessive, it's likely that something needs to be fixed.
Understanding the nature of variability in your business is the first step to Six Sigma. Once you have a good understanding of the basics, you can identify potential sources of variation. It is important to identify whether the variations are random or systemic. Random variations occur when people make mistakes; systematic ones are caused by factors outside the process itself. These are, for instance, random variations that occur when widgets are made and some fall off the production line. It would be considered a systematic problem if every widget that you build falls apart at the same location each time.
After identifying the problem areas, you will need to devise solutions. It might mean changing the way you do business or redesigning it entirely. Once you have implemented the changes, it is important to test them again to ensure they work. If they don't work, you will need to go back to the drawing boards and create a new plan.