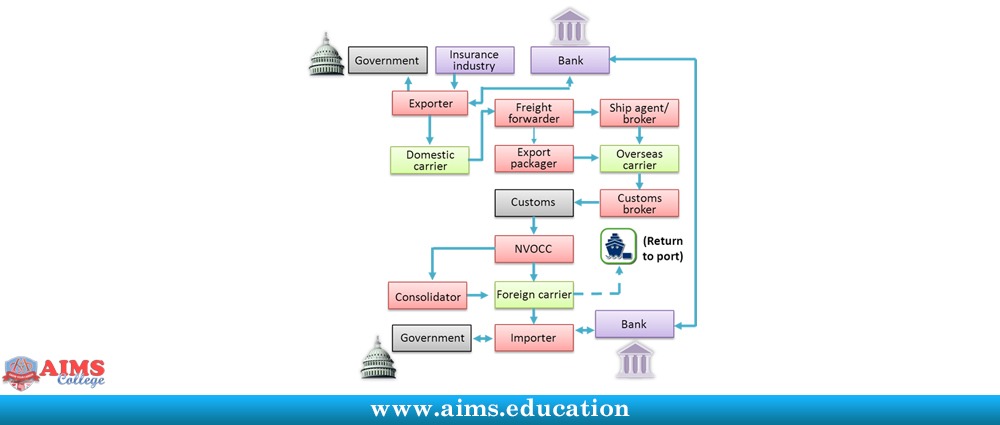
Additive manufacturing uses digital files to create whole systems, parts, and objects. This allows companies to produce complicated machinery or other devices at a very low cost. It also reduces manufacturing costs and increases time to market. Casting, forging, and any other traditional production methods are not required.
These benefits extend to communities and beyond suppliers and manufacturers. Innovators can also benefit from them. Numerous Fortune 500 companies are using 3D printing technology. Biden Administration is launching a new initiative that will help manufacturing companies of all sizes to adopt additive manufacturing.
AM Forward is a public-private initiative that aims to encourage the use of additive manufacturing by developing standards and common practices, establishing an open-market for additive-manufactured parts, and addressing supply chain issues. It is led by five large U.S. manufacturers: General Electric Aviation, Honeywell, Lockheed Martin, Raytheon, and Siemens Energy. These firms are partnering with the DOE Manufacturing Demonstration Facility at Oak Ridge National Laboratory, which is a national facility that provides access to a range of additive-manufacturing technologies.
OEMs will work with other firms to create standard specifications and develop technical solutions for industry challenges. They will also offer technical assistance to U.S. suppliers through the AM Forward Pact. Other large corporations are expected join the initiative over the next few years.
One of the major players involved in AM Forward is the NEO Additive Manufacturing Cluster of Ohio, which works to accelerate the adoption of additive-manufacturing technologies. Ohio has a solid base of skilled engineers and scientists making it an ideal place for additive manufacturing businesses.
The America Makes national accelerator is another important player. This program partners with academia, industry, economic development resources, and workforce training programs to encourage the adoption of additive-manufacturing by a wide range of sectors. Many university programs now exist for additive-manufacturing.
The Manufacturing Extension Partnership is one of many government programs that supports the adoption and use of additive manufacturing. Programs offered by the Department of Labor to support small manufacturers include technical support, financing, and even financial assistance.
These programs can help to overcome common market failures. Many of these programs help overcome common market failures. Similarly, some customers may not be willing to commit to purchasing from companies that invest in additive-manufacturing technologies.
Some of the most innovative additive-manufacturing firms in the country are located in Ohio. Desktop Metal is an industrial additive-manufacturing company that offers metal 3-D printing and machining services to manufacturers and designers. Jonco Industries, Inc. offers many fabrication services, including rapid prototyping, design-for-prototyping, high volume surface finishing, and design for prototyping. PostPro3D specializes in automated surface finishing.
Besides collaborating with the Federal Government, other industry organizations are working to increase the adoption of additive-manufacturing. The Fraunhofer Institute is a leading institution for the development of additive-manufacturing technology.
FAQ
How can excess manufacturing production be reduced?
Better inventory management is key to reducing excess production. This would decrease the time that is spent on inefficient activities like purchasing, storing, or maintaining excess stock. This could help us free up our time for other productive tasks.
You can do this by adopting a Kanban method. A Kanban board, a visual display to show the progress of work, is called a Kanban board. Work items are moved through various states to reach their destination in a Kanban system. Each state has a different priority level.
When work is completed, it can be transferred to the next stage. But if a task remains in the beginning stages it will stay that way until it reaches its end.
This allows you to keep work moving along while making sure that no work gets neglected. A Kanban board allows managers to monitor how much work is being completed at any given moment. This allows them to adjust their workflows based on real-time information.
Lean manufacturing, another method to control inventory levels, is also an option. Lean manufacturing focuses on eliminating waste throughout the entire production chain. Anything that does nothing to add value to a product is waste. Some common types of waste include:
-
Overproduction
-
Inventory
-
Unnecessary packaging
-
Overstock materials
By implementing these ideas, manufacturers can improve efficiency and cut costs.
What is the role of a logistics manager
Logistics managers are responsible for ensuring that all goods arrive in perfect condition and on time. This is done using his/her knowledge of the company's products. He/she should make sure that enough stock is on hand to meet the demands.
What kind of jobs are there in logistics?
Logistics can offer many different jobs. These are some of the jobs available in logistics:
-
Warehouse workers - They load and unload trucks and pallets.
-
Transportation drivers: They drive trucks and trailers and deliver goods and make pick-ups.
-
Freight handlers - They sort and pack freight in warehouses.
-
Inventory managers – These people oversee inventory at warehouses.
-
Sales representatives - They sell products to customers.
-
Logistics coordinators - They organize and plan logistics operations.
-
Purchasing agents are those who purchase goods and services for the company.
-
Customer service agents - They answer phone calls and respond to emails.
-
Shippers clerks - They process shipping order and issue bills.
-
Order fillers: They fill orders based off what has been ordered and shipped.
-
Quality control inspectors - They check incoming and outgoing products for defects.
-
Others - There are many types of jobs in logistics such as transport supervisors and cargo specialists.
How important is automation in manufacturing?
Automating is not just important for manufacturers, but also for service providers. It enables them to provide services faster and more efficiently. In addition, it helps them reduce costs by reducing human errors and improving productivity.
What are the responsibilities for a manufacturing manager
A manufacturing manager must make sure that all manufacturing processes run smoothly and effectively. They must also be alert to any potential problems and take appropriate action.
They should also learn how to communicate effectively with other departments, including sales and marketing.
They should be up to date on the latest trends and be able apply this knowledge to increase productivity and efficiency.
What is the difference in Production Planning and Scheduling, you ask?
Production Planning (PP) refers to the process of determining how much production is needed at any given moment. This can be done by forecasting demand and identifying production capabilities.
Scheduling refers the process by which tasks are assigned dates so that they can all be completed within the given timeframe.
Statistics
- According to the United Nations Industrial Development Organization (UNIDO), China is the top manufacturer worldwide by 2019 output, producing 28.7% of the total global manufacturing output, followed by the United States, Japan, Germany, and India.[52][53] (en.wikipedia.org)
- It's estimated that 10.8% of the U.S. GDP in 2020 was contributed to manufacturing. (investopedia.com)
- In 2021, an estimated 12.1 million Americans work in the manufacturing sector.6 (investopedia.com)
- Many factories witnessed a 30% increase in output due to the shift to electric motors. (en.wikipedia.org)
- You can multiply the result by 100 to get the total percent of monthly overhead. (investopedia.com)
External Links
How To
How to use Lean Manufacturing in the production of goods
Lean manufacturing (or lean manufacturing) is a style of management that aims to increase efficiency, reduce waste and improve performance through continuous improvement. It was developed in Japan between 1970 and 1980 by Taiichi Ohno. TPS founder Kanji Tyoda gave him the Toyota Production System, or TPS award. Michael L. Watkins published the "The Machine That Changed the World", the first book about lean manufacturing. It was published in 1990.
Lean manufacturing refers to a set of principles that improve the quality, speed and costs of products and services. It emphasizes reducing defects and eliminating waste throughout the value chain. Just-in-time (JIT), zero defect (TPM), and 5S are all examples of lean manufacturing. Lean manufacturing emphasizes reducing non-value-added activities like inspection, rework and waiting.
Lean manufacturing not only improves product quality but also reduces costs. Companies can also achieve their goals faster by reducing employee turnover. Lean manufacturing is a great way to manage the entire value chain including customers, suppliers, distributors and retailers as well as employees. Lean manufacturing can be found in many industries. Toyota's philosophy, for example, is what has enabled it to be successful in electronics, automobiles, medical devices, healthcare and chemical engineering as well as paper and food.
Five fundamental principles underlie lean manufacturing.
-
Define Value - Identify the value your business adds to society and what makes you different from competitors.
-
Reduce Waste – Eliminate all activities that don't add value throughout the supply chain.
-
Create Flow: Ensure that the work process flows without interruptions.
-
Standardize and simplify - Make your processes as consistent as possible.
-
Build Relationships- Develop personal relationships with both internal as well as external stakeholders.
Lean manufacturing isn’t new, but it has seen a renewed interest since 2008 due to the global financial crisis. Many companies have adopted lean manufacturing methods to increase their marketability. Some economists even believe that lean manufacturing can be a key factor in economic recovery.
Lean manufacturing is becoming a popular practice in automotive. It has many advantages. These include higher customer satisfaction, lower inventory levels, lower operating expenses, greater productivity, and improved overall safety.
It can be applied to any aspect of an organisation. This is because it ensures efficiency and effectiveness in all stages of the value chain.
There are three types of lean manufacturing.
-
Just-in Time Manufacturing, (JIT): This kind of lean manufacturing is also commonly known as "pull-systems." JIT is a process in which components can be assembled at the point they are needed, instead of being made ahead of time. This method reduces lead times, increases availability, and decreases inventory.
-
Zero Defects Manufacturing: ZDM ensures that no defective units leave the manufacturing plant. If a part needs to be fixed during the assembly line, it should be repaired rather than scrapped. This applies to finished products, which may need minor repairs before they are shipped.
-
Continuous Improvement (CI), also known as Continuous Improvement, aims at improving the efficiency of operations through continuous identification and improvement to minimize or eliminate waste. Continuous Improvement (CI) involves continuous improvement in processes, people, tools, and infrastructure.