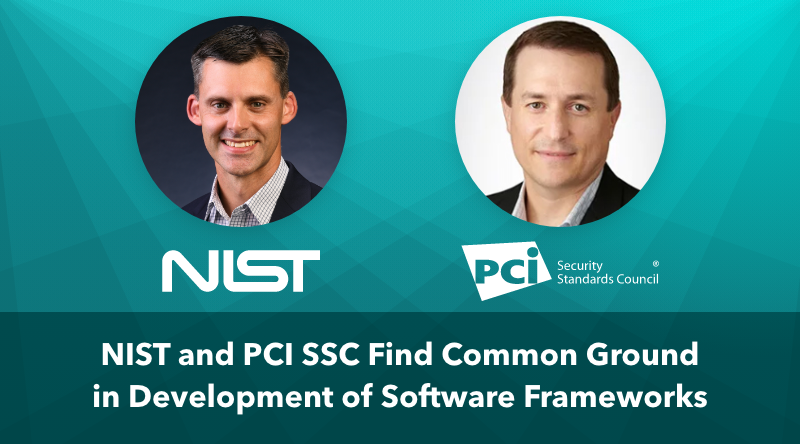
Railroad logistics jobs require many skills. Some jobs are very easy to learn while others require extensive classroom training and years of experience. These types of jobs require a high degree of computer proficiency and product knowledge. Other jobs might involve extensive travel overseas.
A transport logistics specialist tries to make sense of the logistics world, coordinating the transportation of materials or people. He or she might also help to solve problems or assess the efficiency. This might include performing a mechanical inspection or determining the best route for a particular cargo.
The role of the rail logistic manager is to ensure trains and other transport means run on time and are properly maintained. They also have to ensure that trains comply with safety regulations. Freight delivery is often part of the job. However, this job is only part.
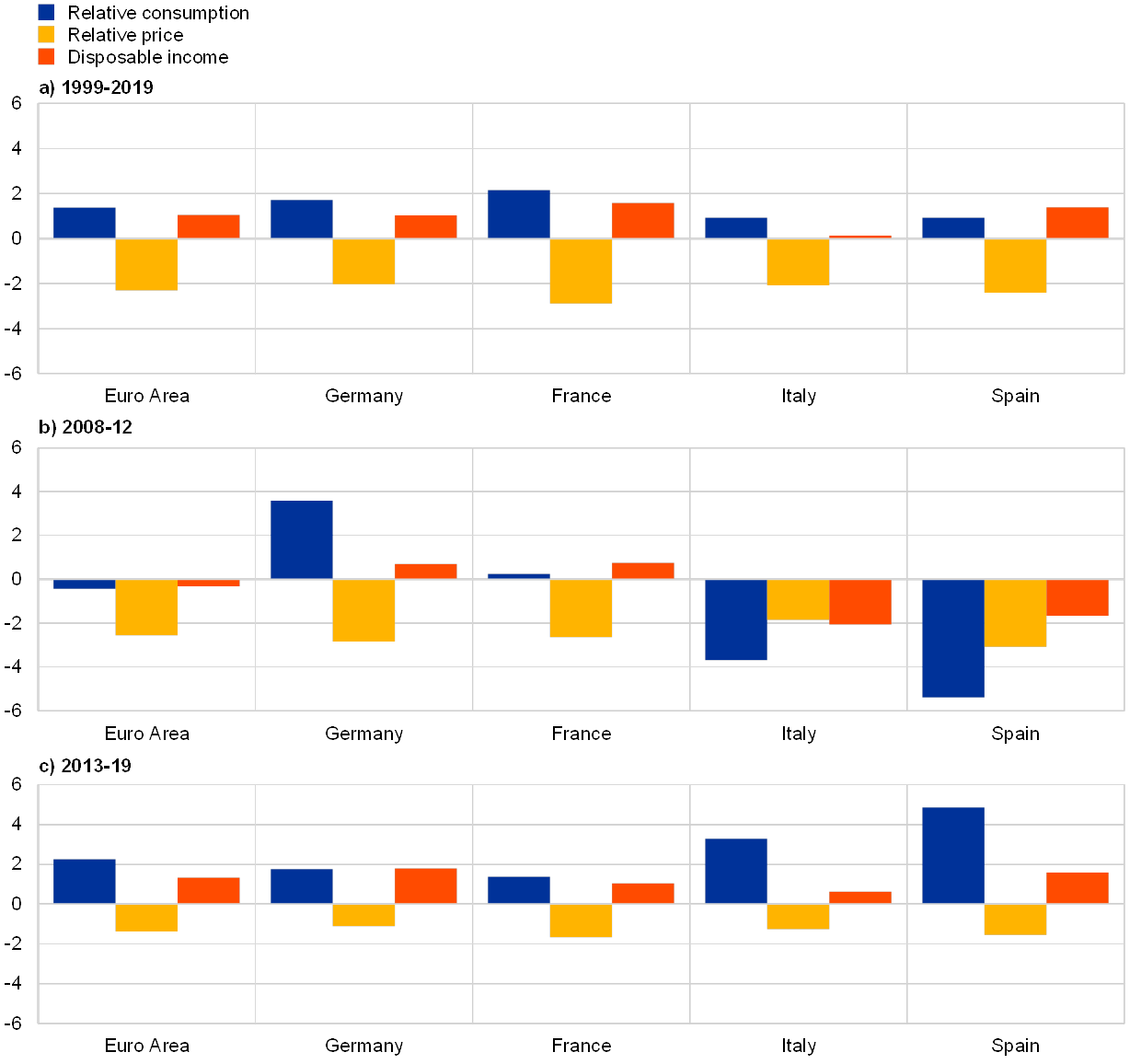
Intermodal dispatcher, another entry-level job in this industry, is also available. This person coordinates schedules for a group drivers and a shipping business. He or she contacts the shipping center to inform them about changes in routes and assigns shipments for the drivers. It is not uncommon for this position also to include administrative duties.
A railway logistics manager may also choose to work in a private firm or a government agency. These positions are generally well-paid and provide excellent career opportunities. You can expect to make approximately $45,000 annually. Many of these jobs do not require a bachelor's level degree. Despite the high salary, however, the average rail salary is a bit on the low side.
Typical logistics titles include logistics manager, logistics analyst and logistics coordinator. These are all very important roles in the field. Each role is unique, but you may find that your skills will be more effective in one than in the others.
Logistics managers must be able and willing to negotiate the best rates or terms for their clients' transportation needs. This includes analyzing equipment availability and negotiating with other parties. It also involves analyzing service levels and analyzing costs. In order to increase efficiency in their company's logistics operations, they will need to be able use basic transportation management concepts.
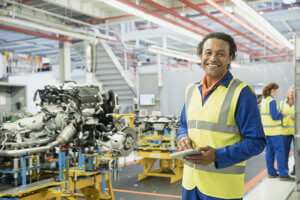
A rail logistics manager might also oversee the implementation of a state-of-the-art tracking system to track shipments and ensure the timely delivery of goods. A tracking system may be used to alert customers about the current location of a shipment.
An expert in rail logistics may be called upon to offer advice about how to optimize the transport process. If he or she can do that, they will be able to help their company achieve better results in a shorter period of time.
You can learn many of these jobs through job training and experience. For example, a rail logistics coordinator requires a bachelor's degree along with years of experience in a related field.
FAQ
Why automate your warehouse
Modern warehouses are increasingly dependent on automation. Increased demand for efficient and faster delivery has resulted in a rise in e-commerce.
Warehouses must be able to quickly adapt to changing demands. Technology is essential for warehouses to be able to adapt quickly to changing needs. Automating warehouses has many benefits. These are just a few reasons to invest in automation.
-
Increases throughput/productivity
-
Reduces errors
-
Increases accuracy
-
Safety is boosted
-
Eliminates bottlenecks
-
Companies can scale more easily
-
Increases efficiency of workers
-
Provides visibility into everything that happens in the warehouse
-
Enhances customer experience
-
Improves employee satisfaction
-
Reducing downtime and increasing uptime
-
This ensures that quality products are delivered promptly
-
Human error can be eliminated
-
It helps ensure compliance with regulations
What are the goods of logistics?
Logistics is the process of moving goods from one point to another.
They include all aspects of transport, including packaging, loading, transporting, unloading, storing, warehousing, inventory management, customer service, distribution, returns, and recycling.
Logisticians ensure the product reaches its destination in the most efficient manner. They help companies manage their supply chain efficiency by providing information on demand forecasts, stock levels, production schedules, and availability of raw materials.
They keep track and monitor the transit of shipments, maintain quality standards, order replenishment and inventories, coordinate with suppliers, vendors, and provide support for sales and marketing.
What are manufacturing and logistic?
Manufacturing refers to the process of making goods using raw materials and machines. Logistics includes all aspects related to supply chain management, such as procurement, distribution planning, inventory control and transportation. Sometimes manufacturing and logistics are combined to refer to a wider term that includes both the process of creating products as well as their delivery to customers.
What is production plan?
Production Planning is the creation of a plan to cover all aspects, such as scheduling, budgeting. Location, crew, equipment, props and other details. It is important to have everything ready and planned before you start shooting. This document should include information about how to achieve the best results on-set. It should include information about shooting locations, casting lists, crew details, equipment requirements, and shooting schedules.
First, you need to plan what you want to film. You might have an idea of where you want to film, or you may have specific locations or sets in mind. Once you've identified the locations and scenes you want to use, you can begin to plan what elements you need for each scene. Perhaps you have decided that you need to buy a car but aren't sure which model. In this case, you could start looking up cars online to find out what models are available and then narrow your choices by choosing between different makes and models.
After you have chosen the right car, you will be able to begin thinking about accessories. What about additional seating? You might also need someone to help you get around the back. Maybe you want to change the interior color from black to white? These questions will help to determine the style and feel of your car. You can also think about the type of shots you want to get. You will be filming close-ups and wide angles. Maybe you want to show your engine or the steering wheel. These details will help identify the exact car you wish to film.
Once you have determined all of the above, you can move on to creating a schedule. You will know when you should start and when you should finish shooting. A schedule for each day will detail when you should arrive at the location and when you need leave. It will help everyone know exactly what they have to do and when. If you need to hire extra staff, you can make sure you book them in advance. It is not worth hiring someone who won’t show up because you didn’t tell him.
Also, consider how many days you will be filming your schedule. Some projects can be completed in a matter of days or weeks. Others may take several days. While creating your schedule, it is important to remember whether you will require more than one shot per day. Multiple takes at the same place will result in higher costs and longer completion times. If you aren't sure whether you need multiple shots, it is best to take fewer photos than you would like.
Budget setting is another important aspect in production planning. As it will allow you and your team to work within your financial means, setting a realistic budget is crucial. It is possible to reduce the budget at any time if you experience unexpected problems. However, it is important not to overestimate the amount that you will spend. You'll end up with less money after paying for other things if the cost is underestimated.
Production planning is a very detailed process, but once you understand how everything works together, it becomes easier to plan future projects.
How can I find out more about manufacturing?
Experience is the best way for you to learn about manufacturing. You can also read educational videos or take classes if this isn't possible.
What is the difference between Production Planning and Scheduling?
Production Planning (PP), or production planning, is the process by which you determine what products are needed at any given time. This is accomplished by forecasting the demand and identifying production resources.
Scheduling is the process that assigns dates to tasks so they can get completed within a given timeframe.
Are there ways to automate parts of manufacturing?
Yes! Automation has been around since ancient times. The Egyptians invented the wheel thousands of years ago. Nowadays, we use robots for assembly lines.
In fact, there are several applications of robotics in manufacturing today. These include:
-
Assembly line robots
-
Robot welding
-
Robot painting
-
Robotics inspection
-
Robots that produce products
Automation could also be used to improve manufacturing. For instance, 3D printing allows us make custom products and not have to wait for months or even weeks to get them made.
Statistics
- According to a Statista study, U.S. businesses spent $1.63 trillion on logistics in 2019, moving goods from origin to end user through various supply chain network segments. (netsuite.com)
- [54][55] These are the top 50 countries by the total value of manufacturing output in US dollars for its noted year according to World Bank.[56] (en.wikipedia.org)
- Job #1 is delivering the ordered product according to specifications: color, size, brand, and quantity. (netsuite.com)
- Many factories witnessed a 30% increase in output due to the shift to electric motors. (en.wikipedia.org)
- In 2021, an estimated 12.1 million Americans work in the manufacturing sector.6 (investopedia.com)
External Links
How To
Six Sigma in Manufacturing
Six Sigma can be described as "the use of statistical process control (SPC), techniques to achieve continuous improvement." Motorola's Quality Improvement Department created Six Sigma at their Tokyo plant, Japan in 1986. Six Sigma's core idea is to improve the quality of processes by standardizing and eliminating defects. Many companies have adopted this method in recent years. They believe there is no such thing a perfect product or service. The main goal of Six Sigma is to reduce variation from the mean value of production. You can calculate the percentage of deviation from the norm by taking a sample of your product and comparing it to the average. If it is too large, it means that there are problems.
Understanding how variability works in your company is the first step to Six Sigma. Once you understand this, you can then identify the causes of variation. It is important to identify whether the variations are random or systemic. Random variations are caused when people make mistakes. While systematic variations are caused outside of the process, they can occur. Random variations would include, for example, the failure of some widgets to fall from the assembly line. If however, you notice that each time you assemble a widget it falls apart in exactly the same spot, that is a problem.
After identifying the problem areas, you will need to devise solutions. You might need to change the way you work or completely redesign the process. Once you have implemented the changes, it is important to test them again to ensure they work. If they don't work you need to rework them and come up a better plan.