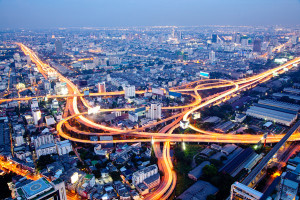
The broad field of industrial technology includes many jobs such as technicians and technologists. There are many industries that employ technicians and technologists. Their salaries can also vary. The salary ranges for industrial technologists can vary depending on their location. They may also be affected depending on the type and employer of their employers.
Technologists and technicians in the industrial engineering field are highly sought after. These professionals can be found working for a wide range of companies, such as government agencies or pharmaceutical companies. These professionals use computer-aided drawing software to create solutions to industry problems. This profession requires professionals with the right education, experience, as well as a strong work ethic.
An Industrial Engineering Technologist salary can vary by location, skill level, and years of experience. Entry-level jobs are less expensive than those that require more education. A bachelor's degree will allow you to make around $53,080 annually. Entry-level jobs pay between $36,550 & $45,040. Your experience can make you earn as high as $86,900 per annum.
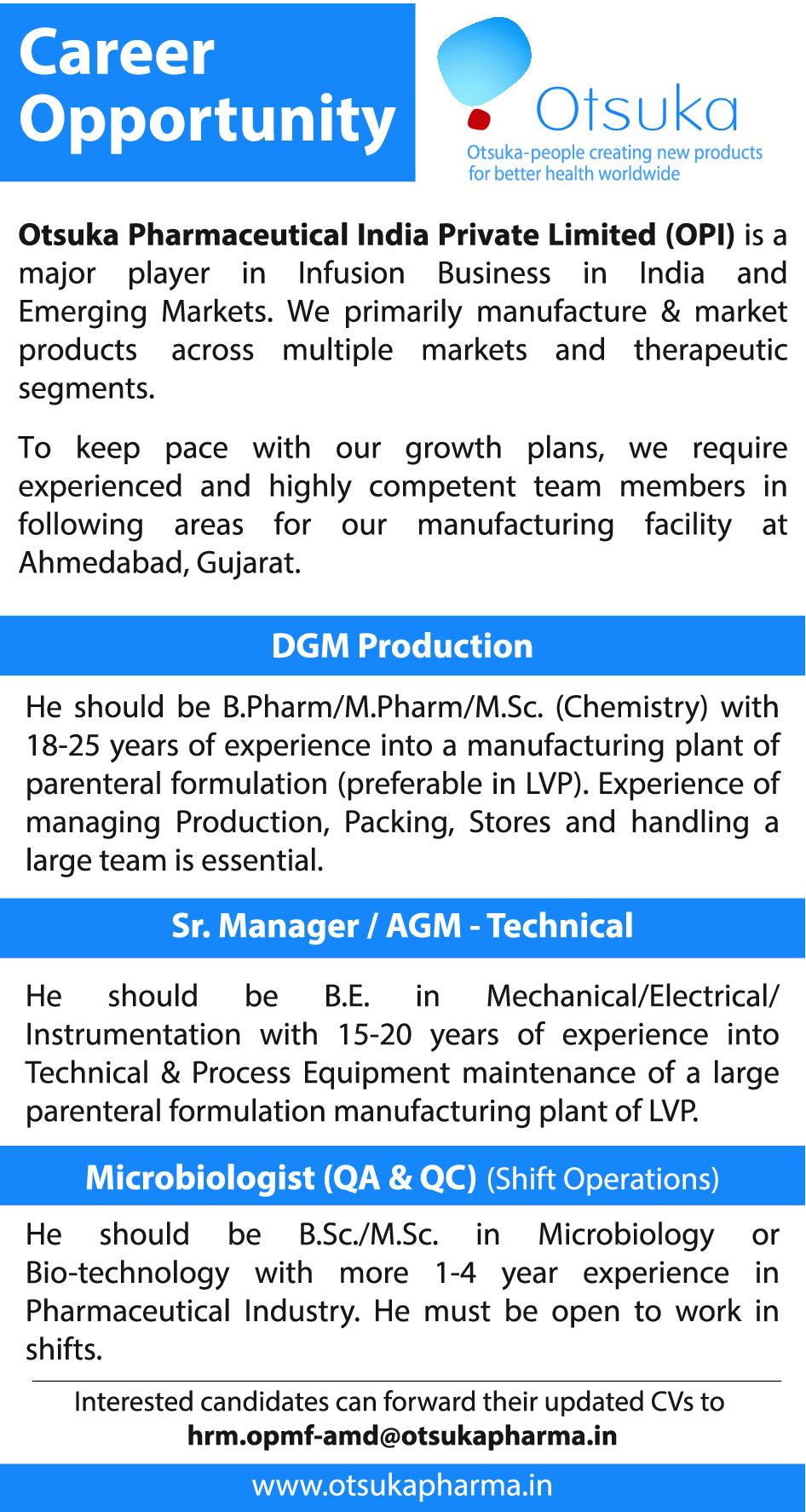
Cost of living in your area is one of the key factors affecting an Industrial Engineering Technician's salary. In some areas, the cost of living can be very low, and that may be a huge advantage. However, some cities have a higher cost of living than others. You can still get a good income in the field if you put in the work.
Industrial engineers receive bonuses quite often. A bonus can increase your salary but it doesn't have to be significant. For example, an average Industrial Engineer bonus is approximately $825. This is approximately 2% your salary. SalaryExpert allows you to find out the potential bonuses that are available.
With the right knowledge and skills, industrial technologists and technicians can find a job in a variety of industries. Manufacturing, healthcare and utilities are the most common positions for industrial technicians and technologists. These professionals report high job satisfaction which helps explain the high demand.
The demand for this career is expected to rise over the next decade. It is estimated that there will be approximately 2,100 additional jobs annually. Many of these openings are due to the retirement of workers. The employment of Industrial Engineering Technologists & Technicians is expected to increase by 3 percent between 2021 and 31.
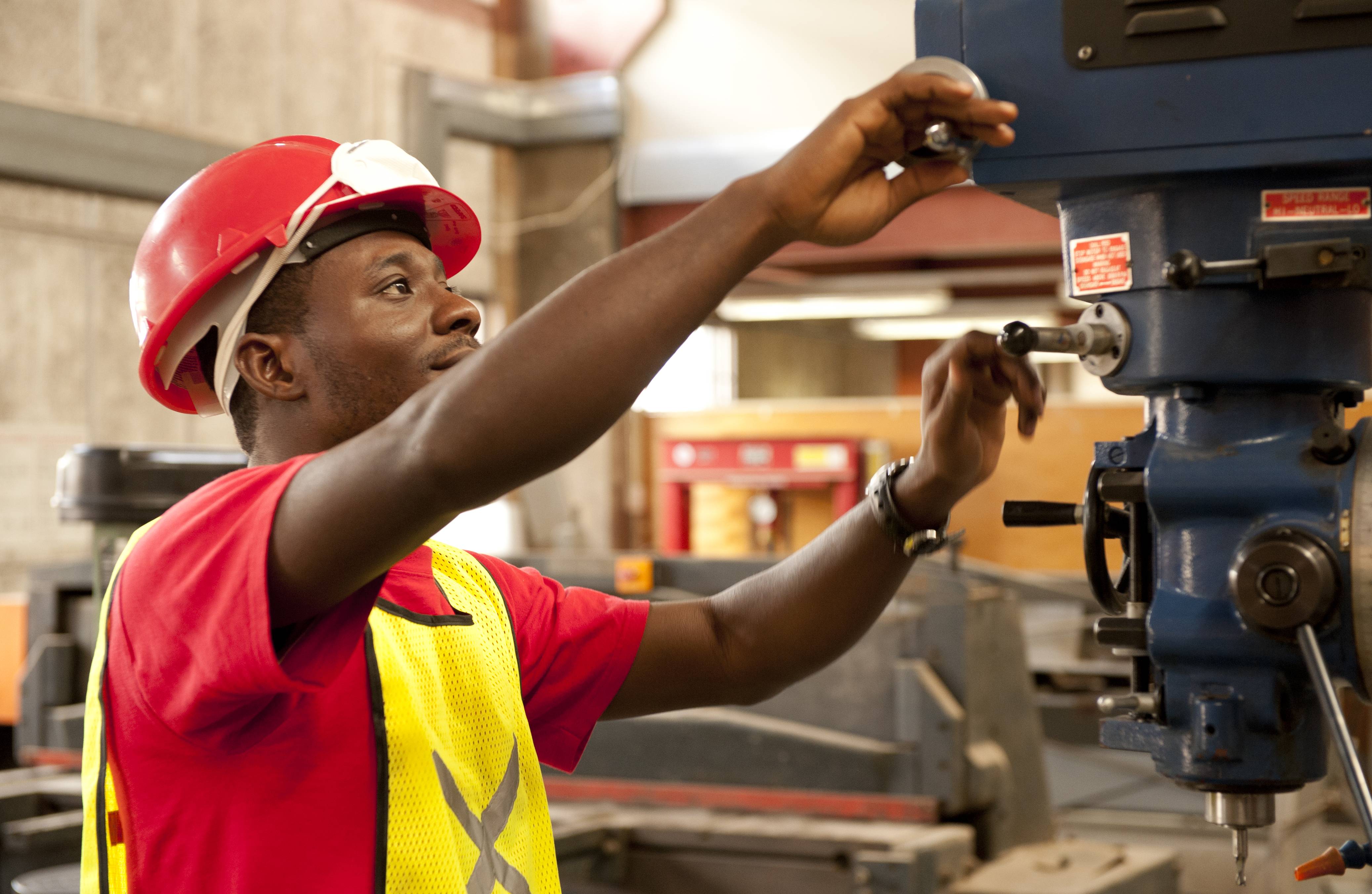
Average Industrial Engineering Technologist salaries are $75,648 This is $2,234 higher than the national average. Chicago area workers can expect to make $77882 per year.
A large proportion of industrial technologist and technician jobs have been filled by government agencies, manufacturing businesses, and pharmaceutical corporations. The average hourly wage for an industrial engineer technologist or technician in the United States is around $26.
FAQ
What is the job of a manufacturer manager?
A manufacturing manager must make sure that all manufacturing processes run smoothly and effectively. They must also be alert to any potential problems and take appropriate action.
They should also be able and comfortable communicating with other departments like sales and marketing.
They must also keep up-to-date with the latest trends in their field and be able use this information to improve productivity and efficiency.
What skills is required for a production planner?
Production planners must be flexible, organized, and able handle multiple tasks. Also, you must be able and willing to communicate with clients and coworkers.
What are the jobs in logistics?
Logistics can offer many different jobs. These are some of the jobs available in logistics:
-
Warehouse workers - They load and unload trucks and pallets.
-
Transportation drivers - They drive trucks and trailers to deliver goods and carry out pick-ups.
-
Freight handlers – They sort and package freight at warehouses.
-
Inventory managers - They oversee the inventory of goods in warehouses.
-
Sales representatives - They sell products to customers.
-
Logistics coordinators – They plan and coordinate logistics operations.
-
Purchasing agents - They buy goods and services that are necessary for company operations.
-
Customer service representatives - Answer calls and email from customers.
-
Ship clerks - They issue bills and process shipping orders.
-
Order fillers - These people fill orders based on what has been ordered.
-
Quality control inspectors: They inspect outgoing and incoming products for any defects.
-
Others – There are many other types available in logistics. They include transport supervisors, cargo specialists and others.
What are the differences between these four types?
Manufacturing is the process of transforming raw materials into useful products using machines and processes. It can involve many activities like designing, manufacturing, testing packaging, shipping, selling and servicing.
How does a production planner differ from a project manager?
The major difference between a Production Planner and a Project Manager is that a Project Manager is often the person responsible for organizing and planning the entire project. While a Production Planner is involved mainly in the planning stage,
Why should you automate your warehouse?
Automation has become increasingly important in modern warehousing. The rise of e-commerce has led to increased demand for faster delivery times and more efficient processes.
Warehouses must be able to quickly adapt to changing demands. They must invest heavily in technology to do this. Automation warehouses can bring many benefits. These are some of the benefits that automation can bring to warehouses:
-
Increases throughput/productivity
-
Reduces errors
-
Increases accuracy
-
Safety is boosted
-
Eliminates bottlenecks
-
This allows companies to scale easily
-
Increases efficiency of workers
-
It gives visibility to everything that happens inside the warehouse
-
Enhances customer experience
-
Improves employee satisfaction
-
Reducing downtime and increasing uptime
-
This ensures that quality products are delivered promptly
-
Removing human error
-
This helps to ensure compliance with regulations
Statistics
- According to a Statista study, U.S. businesses spent $1.63 trillion on logistics in 2019, moving goods from origin to end user through various supply chain network segments. (netsuite.com)
- In 2021, an estimated 12.1 million Americans work in the manufacturing sector.6 (investopedia.com)
- It's estimated that 10.8% of the U.S. GDP in 2020 was contributed to manufacturing. (investopedia.com)
- In the United States, for example, manufacturing makes up 15% of the economic output. (twi-global.com)
- According to the United Nations Industrial Development Organization (UNIDO), China is the top manufacturer worldwide by 2019 output, producing 28.7% of the total global manufacturing output, followed by the United States, Japan, Germany, and India.[52][53] (en.wikipedia.org)
External Links
How To
How to use lean manufacturing in the production of goods
Lean manufacturing is a management style that aims to increase efficiency and reduce waste through continuous improvement. It was developed by Taiichi Okono in Japan, during the 1970s & 1980s. TPS founder Kanji Takoda awarded him the Toyota Production System Award (TPS). Michael L. Watkins published the "The Machine That Changed the World", the first book about lean manufacturing. It was published in 1990.
Lean manufacturing is often described as a set if principles that help improve the quality and speed of products and services. It is about eliminating defects and waste from all stages of the value stream. Lean manufacturing can be described as just-in–time (JIT), total productive maintenance, zero defect (TPM), or even 5S. Lean manufacturing seeks to eliminate non-value added activities, such as inspection, work, waiting, and rework.
Lean manufacturing improves product quality and costs. It also helps companies reach their goals quicker and decreases employee turnover. Lean manufacturing is a great way to manage the entire value chain including customers, suppliers, distributors and retailers as well as employees. Lean manufacturing practices are widespread in many industries. Toyota's philosophy is a great example of this. It has helped to create success in automobiles as well electronics, appliances and healthcare.
Five fundamental principles underlie lean manufacturing.
-
Define Value - Determine the value that your business brings to society. Also, identify what sets you apart from your competitors.
-
Reduce Waste - Eliminate any activity that doesn't add value along the supply chain.
-
Create Flow. Ensure that your work is uninterrupted and flows seamlessly.
-
Standardize & simplify - Make processes consistent and repeatable.
-
Building Relationships – Establish personal relationships with both external and internal stakeholders.
Although lean manufacturing isn't a new concept in business, it has gained popularity due to renewed interest in the economy after the 2008 global financial crisis. Many businesses have adopted lean manufacturing techniques to help them become more competitive. Many economists believe lean manufacturing will play a major role in economic recovery.
Lean manufacturing has many benefits in the automotive sector. These include higher customer satisfaction levels, reduced inventory levels as well as lower operating costs.
Lean manufacturing can be applied to almost every aspect of an organization. It is especially useful for the production aspect of an organization, as it ensures that every step in the value chain is efficient and effective.
There are three types principally of lean manufacturing:
-
Just-in Time Manufacturing: This lean manufacturing method is commonly called "pull systems." JIT is a process in which components can be assembled at the point they are needed, instead of being made ahead of time. This strategy aims to decrease lead times, increase availability of parts and reduce inventory.
-
Zero Defects Manufacturing, (ZDM): ZDM is focused on ensuring that no defective products leave the manufacturing facility. Repairing a part that is damaged during assembly should be done, not scrapping. This also applies to finished products that need minor repairs before being shipped.
-
Continuous Improvement (CI: Continuous improvement aims to increase the efficiency of operations by constantly identifying and making improvements to reduce or eliminate waste. Continuous Improvement involves continuous improvement of processes.