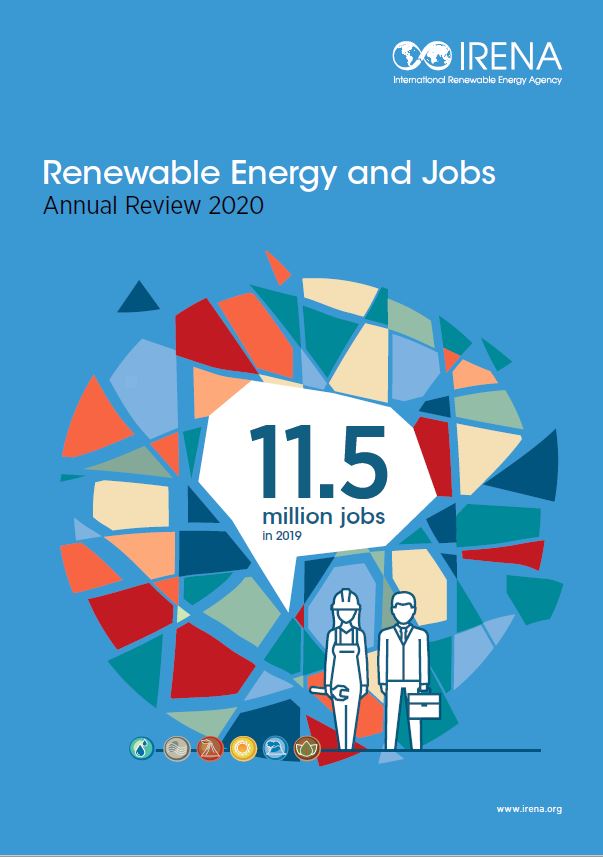
Lean to Agile is a great way for teams to cut waste and increase productivity. It is about prioritizing work and eliminating wasted effort, while empowering teams as well as scrum masters to take care of the rest. Agile teams should be empowered with the ability to act as product owners. They also need to have servant leaders who are committed and dedicated to their projects' success.
Time-to-market
It is the time taken from product ideation to its full release that is most crucial in determining product success. Your company will be able to capture more market share and generate more revenue if it is shorter. To improve this metric, companies need to be aware of their development processes. Companies will then be able to optimize their processes to meet the objectives of their business and to maximize their capabilities to improve their time to market.
To reduce the time to market a new product, outsourcing can be used as a way to cut down on time. Another way to shorten time is to create an ecosystem of reliable supporting partners. This will help you reduce risk and to share your resources.
Iteration
Iteration is a crucial element of agile software development. Iteration is a key element of agile software development. This concept emphasizes the value of small, measured steps that can be evaluated faster than a complete process. The resulting features are better detailed, and the chances of success are higher. This approach can be time-bound. The end product of an iteration should be running and releasable. This requires that the end product be integrated, tested, then deployed on an internal server.
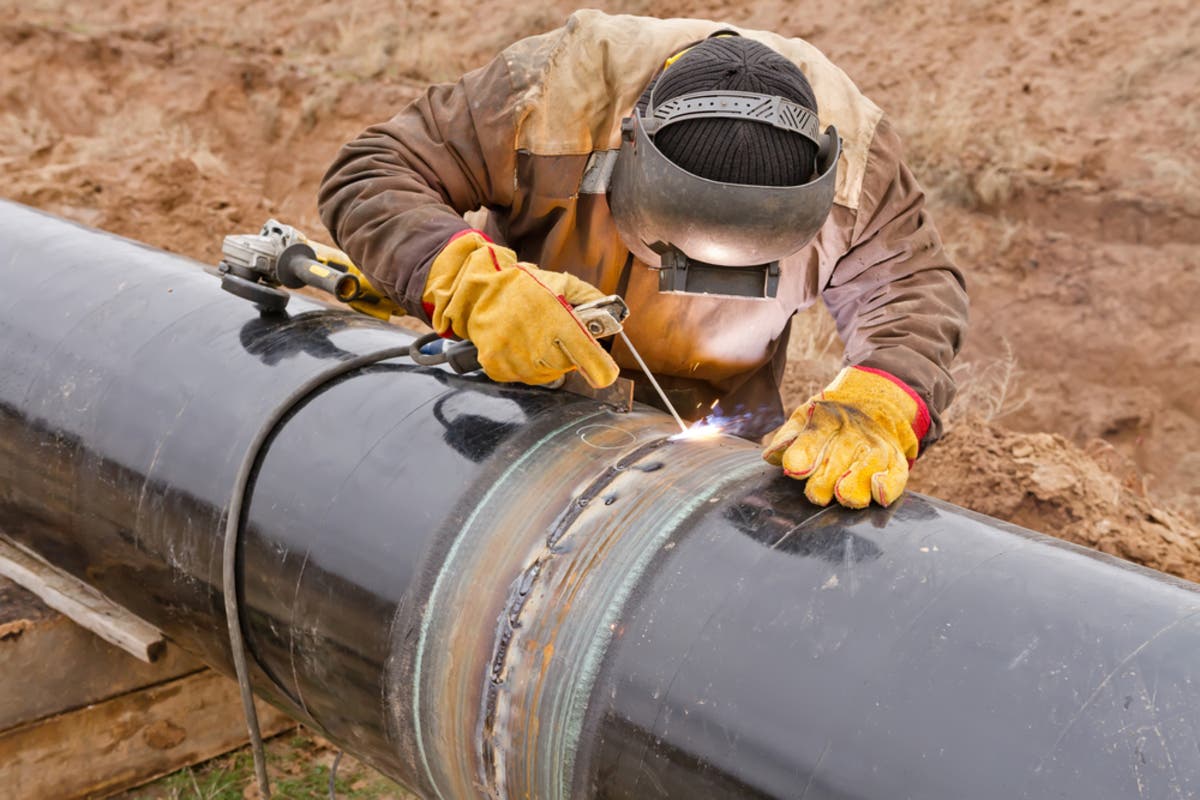
Iterations allow teams to refine their backlog, identify risks and fix them. The aim is to make each iteration better than the one before. Developers might modify or add features to existing functions. This process continues until the product is released.
Collaborative processes
The Agile Manifesto emphasizes the need for collaboration between business stakeholders and developers. This allows teams prioritize work based off business goals. A value stream is also promoted by lean processes. This is the complete list of actions that produces the product or service customers want. These two approaches are very similar, but they have key differences.
Agile is more flexible and adaptable than Lean. Lean UX teams don't use large, rigid tools for project management. Instead, they work as a team, scale up quickly and collaborate to achieve a goal. Agile is a system with small-world networks and deliverables. In addition, it focuses on autonomy, exploration, and collaboration. An agile approach is required for scaling from one project to multiple projects.
User research in agile teams
Agile teams are increasingly incorporating user feedback into their processes. This mindset is becoming increasingly common in product design, but it's also being applied to other areas. Teams are realizing that flexible and rapid research is essential as usability and experience become more important. Agile teams adopt agile thinking to ensure user-centric research is at the forefront. They use this mindset to discover processes that link to the product roadmap.
It is important to simplify and make user research more accessible. This involves creating repeatable templates for user research that non-practitioners could use to run their tests. These templates should include the most important questions as well as cover all stages of product creation. UX platforms offer preloaded templates as well as automated workflows that can ensure consistency in results.
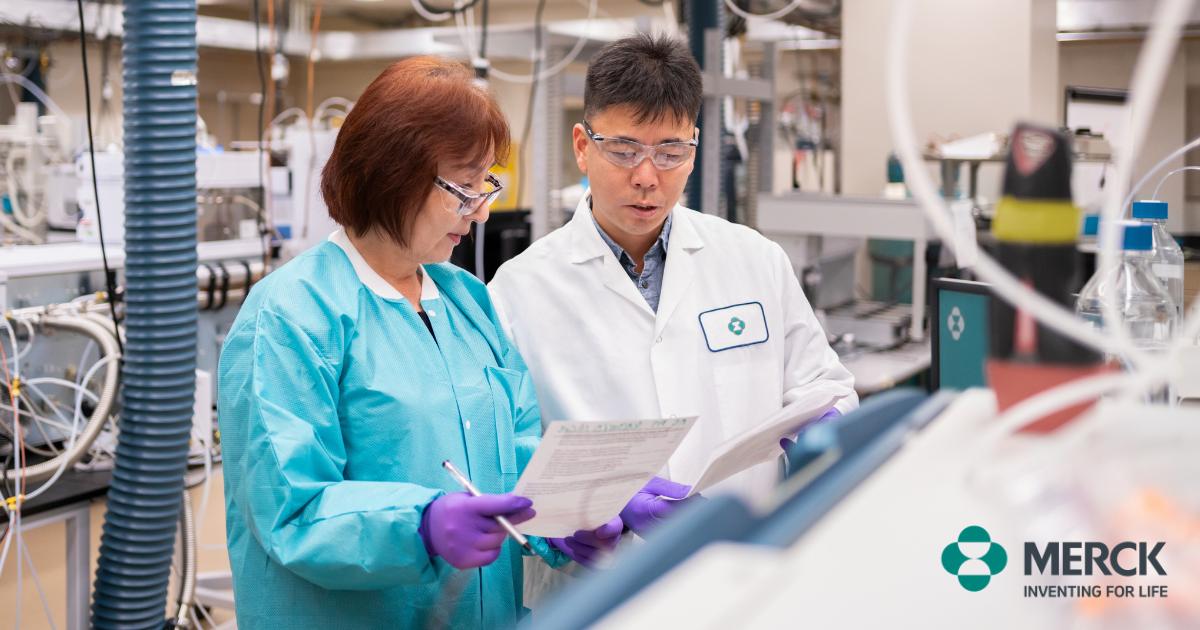
Value creation
The concept of value creation is somewhat odd, even if it makes sense. While creating value can be accomplished with a narrow scope or a larger one, it cannot be entirely binary. In some instances, a narrower scope can result in a low value, while a larger scope can lead to more value. But, it is possible to have a comprehensive scope.
Lean and agile aim to provide a customer with a high-quality, focused product. Combining both these methods can help companies deliver a superior product quicker. They also minimize process overhead by empowering employees to work together and focus on the needs of the customer.
FAQ
What is production planning?
Production planning is the process of creating a plan that covers all aspects of production. This includes scheduling, budgeting and crew, location, equipment, props, and more. This document is designed to make sure everything is ready for when you're ready to shoot. This document should also include information on how to get the best result on set. This includes location information, crew details, equipment specifications, and casting lists.
The first step in filming is to define what you want. You may have decided where to shoot or even specific locations you want to use. Once you have identified your locations and scenes, you can start working out which elements you require for each scene. One example is if you are unsure of the exact model you want but decide that you require a car. This is where you can look up car models online and narrow down your options by choosing from different makes and models.
After you have selected the car you want, you can begin to think about additional features. Do you need people sitting in the front seats? Or maybe you just need someone to push the car around. Maybe you want to change the interior color from black to white? These questions will help determine the look and feel you want for your car. Another thing you can do is think about what type of shots are desired. Will you be filming close-ups or wide angles? Maybe the engine or steering wheel is what you are looking to film. These things will help you to identify the car that you are looking for.
Once you have all the information, you are ready to create a plan. A schedule will tell you when you need to start shooting and when you need to finish. Every day will have a time for you to arrive at the location, leave when you are leaving and return home when you are done. Everyone knows exactly what they should do and when. It is possible to make arrangements in advance for additional staff if you are looking to hire. You should not hire anyone who doesn't show up because of your inaction.
Also, consider how many days you will be filming your schedule. Some projects are quick and easy, while others take weeks. While creating your schedule, it is important to remember whether you will require more than one shot per day. Multiple shots at the same location can increase costs and make it more difficult to complete. If you aren't sure whether you need multiple shots, it is best to take fewer photos than you would like.
Budgeting is another crucial aspect of production plan. It is important to set a realistic budget so you can work within your budget. It is possible to reduce the budget at any time if you experience unexpected problems. However, it is important not to overestimate the amount that you will spend. Underestimating the cost will result in less money after you have paid for other items.
Production planning is a detailed process. But, once you understand the workings of everything, it becomes easier for future projects to be planned.
What is the difference between a production planner and a project manager?
The main difference between a production planner and a project manager is that a project manager is usually the person who plans and organizes the entire project, whereas a production planner is mainly involved in the planning stage of the project.
What are the main products of logistics?
Logistics involves the transportation of goods from point A and point B.
They cover all aspects of transportation, such as packing, loading, transporting and unloading.
Logisticians ensure that the product is delivered to the correct place, at the right time, and under safe conditions. They provide information on demand forecasts as well stock levels, production schedules and availability of raw material.
They keep track and monitor the transit of shipments, maintain quality standards, order replenishment and inventories, coordinate with suppliers, vendors, and provide support for sales and marketing.
How can manufacturing efficiency be improved?
First, identify the factors that affect production time. Next, we must find ways to improve those factors. If you don't know where to start, then think about which factor(s) have the biggest impact on production time. Once you identify them, look for solutions.
Are there any Manufacturing Processes that we should know before we can learn about Logistics?
No. No. Understanding the manufacturing process will allow you to better understand logistics.
Statistics
- Many factories witnessed a 30% increase in output due to the shift to electric motors. (en.wikipedia.org)
- [54][55] These are the top 50 countries by the total value of manufacturing output in US dollars for its noted year according to World Bank.[56] (en.wikipedia.org)
- According to a Statista study, U.S. businesses spent $1.63 trillion on logistics in 2019, moving goods from origin to end user through various supply chain network segments. (netsuite.com)
- You can multiply the result by 100 to get the total percent of monthly overhead. (investopedia.com)
- In 2021, an estimated 12.1 million Americans work in the manufacturing sector.6 (investopedia.com)
External Links
How To
How to Use Lean Manufacturing in the Production of Goods
Lean manufacturing refers to a method of managing that seeks to improve efficiency and decrease waste. It was first developed in Japan in the 1970s/80s by Taiichi Ahno, who was awarded the Toyota Production System (TPS), award from KanjiToyoda, the founder of TPS. Michael L. Watkins published the first book on lean manufacturing in 1990.
Lean manufacturing, often described as a set and practice of principles, is aimed at improving the quality, speed, cost, and efficiency of products, services, and other activities. It emphasizes the elimination and minimization of waste in the value stream. Lean manufacturing is called just-in-time (JIT), zero defect, total productive maintenance (TPM), or 5S. Lean manufacturing eliminates non-value-added tasks like inspection, rework, waiting.
Lean manufacturing can help companies improve their product quality and reduce costs. Additionally, it helps them achieve their goals more quickly and reduces employee turnover. Lean manufacturing is a great way to manage the entire value chain including customers, suppliers, distributors and retailers as well as employees. Lean manufacturing is widely practiced in many industries around the world. Toyota's philosophy is a great example of this. It has helped to create success in automobiles as well electronics, appliances and healthcare.
Five principles are the basis of lean manufacturing:
-
Define Value - Determine the value that your business brings to society. Also, identify what sets you apart from your competitors.
-
Reduce Waste – Eliminate all activities that don't add value throughout the supply chain.
-
Create Flow - Make sure work runs smoothly without interruptions.
-
Standardize and Simplify – Make processes as consistent, repeatable, and as simple as possible.
-
Build Relationships- Develop personal relationships with both internal as well as external stakeholders.
Although lean manufacturing has always been around, it is gaining popularity in recent years because of a renewed interest for the economy after 2008's global financial crisis. Many businesses have adopted lean production techniques to make them more competitive. Some economists even believe that lean manufacturing can be a key factor in economic recovery.
With many benefits, lean manufacturing is becoming more common in the automotive industry. These include better customer satisfaction and lower inventory levels. They also result in lower operating costs.
It can be applied to any aspect of an organisation. However, it is particularly useful when applied to the production side of an organization because it ensures that all steps in the value chain are efficient and effective.
There are three main types:
-
Just-in Time Manufacturing (JIT), also known as "pull system": This form of lean manufacturing is often referred to simply as "pull". JIT is a process in which components can be assembled at the point they are needed, instead of being made ahead of time. This strategy aims to decrease lead times, increase availability of parts and reduce inventory.
-
Zero Defects Manufacturing - ZDM: ZDM focuses its efforts on making sure that no defective units leave a manufacturing facility. It is better to repair a part than have it removed from the production line if it needs to be fixed. This applies to finished goods that may require minor repairs before shipment.
-
Continuous Improvement (CI),: Continuous improvement aims improve the efficiency and effectiveness of operations by continuously identifying issues and making changes to reduce waste. Continuous Improvement involves continuous improvement of processes.