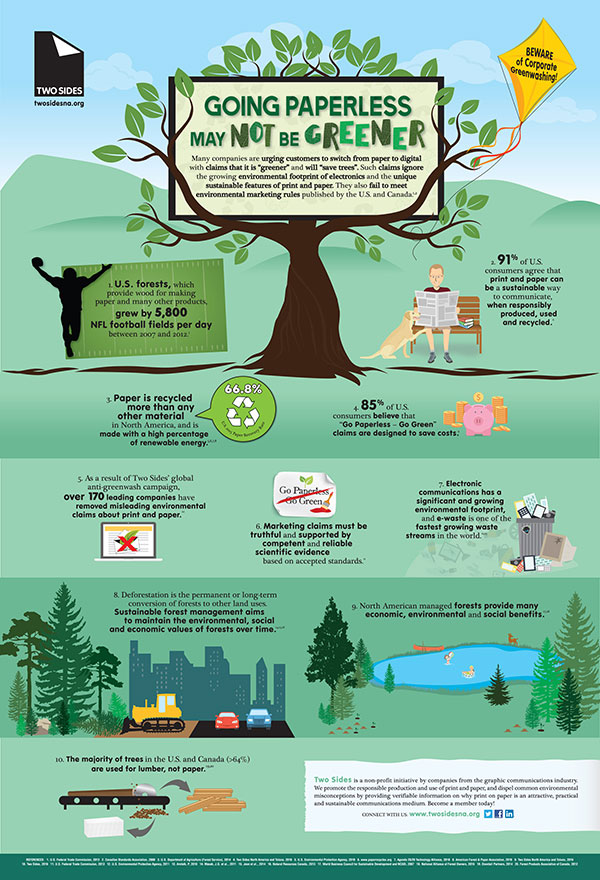
Production workers have a key role to play in the manufacturing industry. They are responsible for getting products to customers. These employees do everything from operating machinery to working at warehouses. They ensure that all the components of a product, including packaging and shipping, are made correctly.
The average manufacturing wage exceeds that of many other industries. In general, the wage premium ranges from 10 percent up to more than 15% (Langdon & Lehrman 2012). The compensation premium is lower than in previous years. This means that those who want to expand the manufacturing sector can't take this advantage for granted.
Paying Production Workers by Level of Experience
As a production worker, you are likely to earn a higher salary than other workers in the same field, as long as you have a strong skill set and a good track record of success. You can increase the earning potential of your career by changing employers, getting more experience or moving into a role with greater management responsibilities.
Developing Effective Workplace Strategies
As a manufacturing worker, you should consider how to make your workplace as efficient as possible without sacrificing quality. It is important to identify areas of production that are slow and find a solution for the whole line. It also involves collaborating with supervisors and other team members to introduce these efficiency enhancements and measure their efficacy.
Safety at Work. It is important to keep all equipment clean and prevent accidents.
Maintaining Production Standards. As a production worker you have the responsibility of producing high quality products that meet strict standards in manufacturing and quality. You must operate machines with consistency and accuracy, and you should monitor equipment for defects.
Cleaning the Workplace. It is important to do this in order to avoid contamination and create a productive work environment.
Monitoring Product Quality: As a production worker, you conduct daily inspections to ensure that the quality of your output is meeting the company's specifications. This includes checking your production report for any defects and recording them.
Use New Technologies to Increase Productivity. As a factory worker, you can apply innovative and new processes in the factory. You may decide to adopt a different way of assembling products or develop an alternative system for packaging.
These improvements are able to increase the efficiency of the factory, and therefore your earnings as an employee. These improvements could include robotics, automation or better human interaction.
Wages of Manufacturing Workers
As a manufacturer, you must be aware of how much other workers in your industry earn. This will help you to set a competitive wage. This may include seeking out positions at different companies, obtaining advanced certificates or degrees, and managing experience in order to qualify for promotion.
FAQ
Are there any Manufacturing Processes that we should know before we can learn about Logistics?
No. No. But, being familiar with manufacturing processes will give you a better understanding about how logistics works.
What is the difference between Production Planning and Scheduling?
Production Planning (PP), is the process of deciding what production needs to take place at any given time. This is accomplished by forecasting the demand and identifying production resources.
Scheduling refers to the process of allocating specific dates to tasks in order that they can be completed within a specified timeframe.
How can we improve manufacturing efficiency?
The first step is to identify the most important factors affecting production time. Then we need to find ways to improve these factors. If you don’t know how to start, look at which factors have the greatest impact upon production time. Once you identify them, look for solutions.
What do you mean by warehouse?
A warehouse is an area where goods are stored before being sold. It can be an indoor space or an outdoor area. In some cases, it may be a combination of both.
What are the 7 Rs of logistics.
The acronym "7R's" of Logistics stands for seven principles that underpin logistics management. It was developed by the International Association of Business Logisticians (IABL) and published in 2004 as part of its "Seven Principles of Logistics Management" series.
The acronym is composed of the following letters.
-
Responsible - to ensure that all actions are within the legal requirements and are not detrimental to others.
-
Reliable - You can have confidence that you will fulfill your promises.
-
It is reasonable to use resources efficiently and not waste them.
-
Realistic - Consider all aspects of operations, including environmental impact and cost effectiveness.
-
Respectful - treat people fairly and equitably.
-
Be resourceful: Look for opportunities to save money or increase productivity.
-
Recognizable - provide customers with value-added services.
Statistics
- You can multiply the result by 100 to get the total percent of monthly overhead. (investopedia.com)
- It's estimated that 10.8% of the U.S. GDP in 2020 was contributed to manufacturing. (investopedia.com)
- Many factories witnessed a 30% increase in output due to the shift to electric motors. (en.wikipedia.org)
- Job #1 is delivering the ordered product according to specifications: color, size, brand, and quantity. (netsuite.com)
- [54][55] These are the top 50 countries by the total value of manufacturing output in US dollars for its noted year according to World Bank.[56] (en.wikipedia.org)
External Links
How To
How to Use the 5S to Increase Productivity In Manufacturing
5S stands to stand for "Sort", “Set In Order", “Standardize", and "Store". Toyota Motor Corporation invented the 5S strategy in 1954. It assists companies in improving their work environments and achieving higher efficiency.
This method has the basic goal of standardizing production processes to make them repeatable. This means that tasks such as cleaning, sorting, storing, packing, and labeling are performed daily. Because workers know what they can expect, this helps them perform their jobs more efficiently.
There are five steps to implementing 5S, including Sort, Set In Order, Standardize, Separate and Store. Each step requires a different action to increase efficiency. By sorting, for example, you make it easy to find the items later. You arrange items by placing them in an order. Once you have separated your inventory into groups and organized them, you will store these groups in easily accessible containers. Labeling your containers will ensure that everything is correctly labeled.
This process requires employees to think critically about how they do their job. Employees must understand why they do certain tasks and decide if there's another way to accomplish them without relying on the old ways of doing things. In order to use the 5S system effectively, they must be able to learn new skills.
In addition to improving efficiency, the 5S system also increases morale and teamwork among employees. They will feel motivated to strive for higher levels of efficiency once they start to see results.