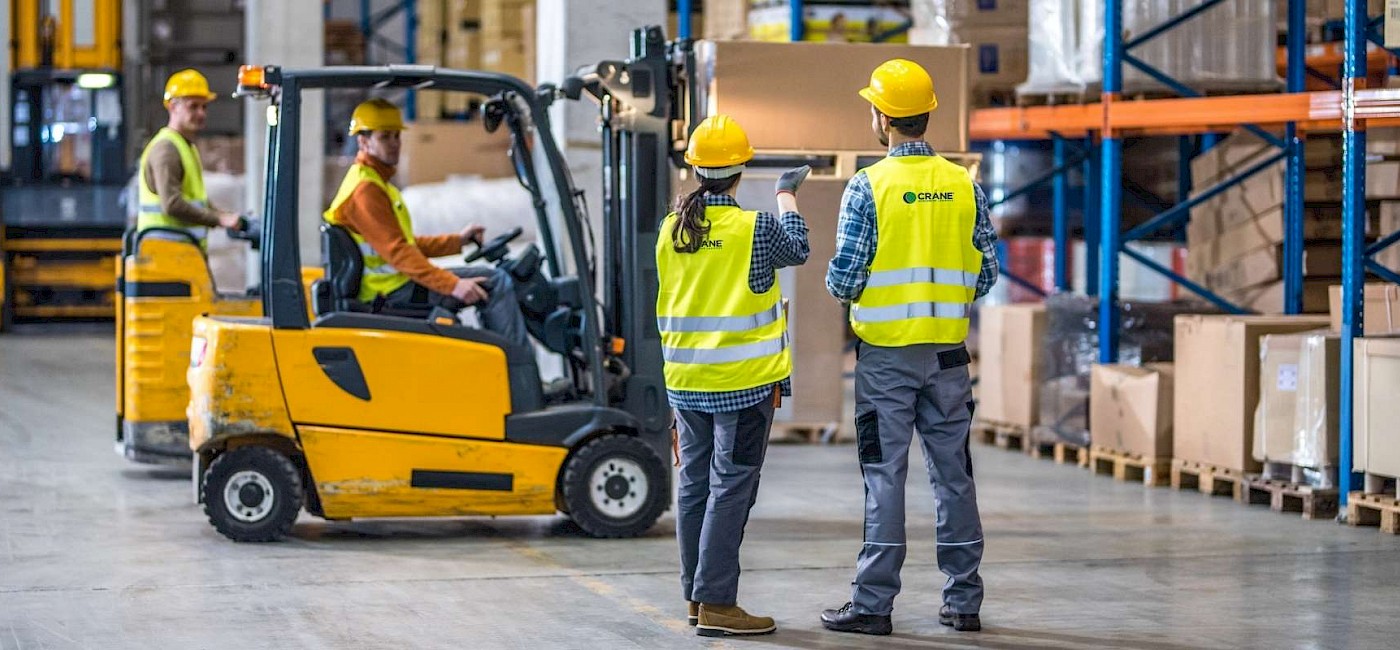
Toyota Motor Manufacturing Indiana Inc. is located in Gibson County Indiana. This plant was the first Toyota plant in America to be completely owned by Toyota. The plant produces Toyota's fullsize pickup trucks, such as the Avalon or the Corolla, and also the Sienna small van. The Toyota RAV4 Hybrid is also produced here, making it the most popular hybrid Toyota has ever made.
The plant was originally planned to manufacture the Toyota Highlander, but instead moved to Gibson County, Indiana. Since 2011, the Toyota RAV4 Hybrid compact SUV is produced at this plant. The plant was worth more than $1.33 Billion in 2017.
Toyota Safety Sense 2.5+ is also manufactured at the plant. It features automatic emergency braking. The plant is currently in the process of preparing all 2018 Camry models. The new model boasts a new transmission with more power and a more stylish look. It will be $25,900.
Toyota's Camry is the most popular car in America. It is currently the best selling midsize sedan in America, and has been for 15 years. Toyota has built 10 million Camrys here in Kentucky. This is the first hybrid model-producing plant in North America.
Toyota Production System is a collection practices and techniques that increase quality and efficiency. This system includes 600 Toyota engineers. It also houses the Toyota Production Engineering and Manufacturing Center. The center will be the first to produce hydrogen fuel cell modules suitable for heavy-duty commercial trucks. The facility can make up to 100,000 vehicles per annum.
Toyota has invested $1.5 Billion in the plant over the past five years. Toyota also added 700 workers. This investment will create 470,100 jobs in the United States by 2020. In addition, Toyota has invested over $147 million in nonprofit partners in Kentucky since 1986.
The Toyota Camry has a reputation for being dependable and fashionable. It has the GA-K platform, and a new transmission. It is also fun to drive. Consumer Reports listed the Toyota Camry as the number one selling car in America in July.
Toyota's production system includes many elements such as continuous improvement, justin-time parts deliveries, and a sophisticated robotic welder system. The Toyota Production Engineering and Manufacturing Center is a good example of how Toyota has made the most of its investment in Kentucky.
A new production hall design allows Toyota to save on construction costs and air conditioning costs. The Visitor Center includes interactive video screens and exhibits about hybrid technology. During the next 10 years, Toyota will produce up to 2 million vehicles in North America. This is the largest Toyota facility other than Japan.
Toyota's New Global Architecture marks a major improvement in the company's production systems. This strategy includes a revamped engine and organization of production. It also includes a module that unifies all vehicle components. The new design preserves Toyota's innovation spirit and reflects Toyota’s traditional values.
FAQ
What are the 4 types of manufacturing?
Manufacturing is the process of transforming raw materials into useful products using machines and processes. It can involve many activities like designing, manufacturing, testing packaging, shipping, selling and servicing.
Why is logistics important for manufacturing?
Logistics is an integral part of every business. They are essential to any business's success.
Logistics play an important role in reducing costs as well as increasing efficiency.
How can manufacturing avoid production bottlenecks
Production bottlenecks can be avoided by ensuring that processes are running smoothly during the entire production process, starting with the receipt of an order and ending when the product ships.
This includes both planning for capacity and quality control.
Continuous improvement techniques such Six Sigma are the best method to accomplish this.
Six Sigma is a management method that helps to improve quality and reduce waste.
It focuses on eliminating variation and creating consistency in your work.
Statistics
- Job #1 is delivering the ordered product according to specifications: color, size, brand, and quantity. (netsuite.com)
- (2:04) MTO is a production technique wherein products are customized according to customer specifications, and production only starts after an order is received. (oracle.com)
- You can multiply the result by 100 to get the total percent of monthly overhead. (investopedia.com)
- Many factories witnessed a 30% increase in output due to the shift to electric motors. (en.wikipedia.org)
- In the United States, for example, manufacturing makes up 15% of the economic output. (twi-global.com)
External Links
How To
How to Use the 5S to Increase Productivity In Manufacturing
5S stands as "Sort", Set In Order", Standardize", Separate" and "Store". Toyota Motor Corporation invented the 5S strategy in 1954. It assists companies in improving their work environments and achieving higher efficiency.
The basic idea behind this method is to standardize production processes, so they become repeatable, measurable, and predictable. This means that every day tasks such cleaning, sorting/storing, packing, and labeling can be performed. Because workers know what they can expect, this helps them perform their jobs more efficiently.
Implementing 5S requires five steps. These are Sort, Set In Order, Standardize. Separate. And Store. Each step requires a different action, which increases efficiency. By sorting, for example, you make it easy to find the items later. Once you have placed items in an ordered fashion, you will put them together. Then, after you separate your inventory into groups, you store those groups in containers that are easy to access. You can also label your containers to ensure everything is properly labeled.
This process requires employees to think critically about how they do their job. Employees need to understand the reasons they do certain jobs and determine if there is a better way. In order to use the 5S system effectively, they must be able to learn new skills.
In addition to increasing efficiency, the 5S method also improves morale and teamwork among employees. As they begin to see improvements, they feel motivated to continue working towards the goal of achieving higher levels of efficiency.