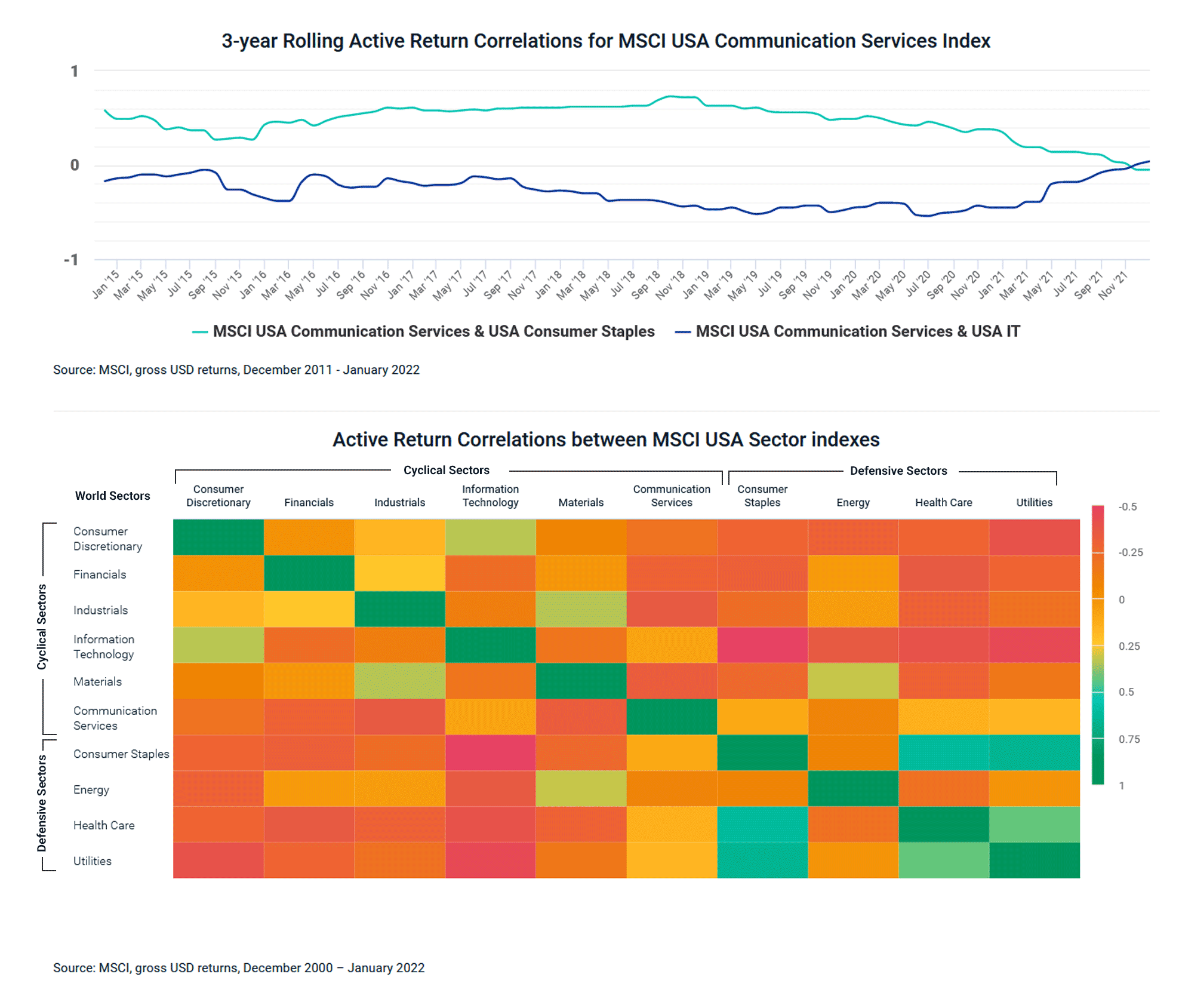
The job director of job manufacturing is similar to the job of a production associate. This article will explain the qualifications required to be a job director in manufacturing. This job requires a highly skilled workforce to complete various operations. It is important to have an irregular workflow. This will make it easier to manage projects, track development, and help with project management. This production line requires a highly skilled workforce. Employees must be able maintain pace and deliver quality products at the right time.
Job director for manufacturing
Job directors of manufacturing are responsible for overseeing the daily operations of a unit of manufacturing. They ensure that products are finished on time and at a high quality standard. For a product to be created, a director for manufacturing must work closely alongside engineers and designers. Before the product enters large-scale production they must assess its feasibility, market suitability, and impact upon processes and quality. They must have leadership abilities as a director for manufacturing. They should be able supervise workers and implement process and equipment improvements.
Typically, directors of manufacturing hold a bachelor's degree or higher. Employers prefer to hire people with advanced degrees. Directors of manufacturing should have at minimum five years' experience working in management. Candidates should be able and willing to learn quickly.
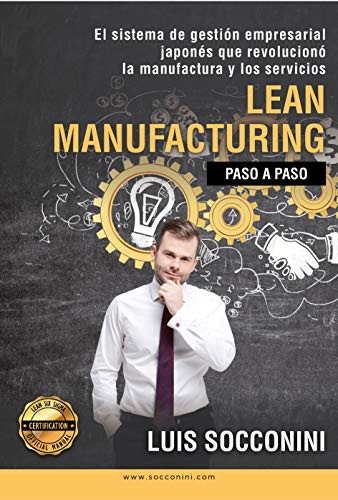
Duties of a manufacturing associate
While the duties of a Manufacturing Associate can vary, they typically involve repetitive motions as well as assembly line work. To avoid injury, associates should exercise proper body mechanics and stay in good physical condition. They may also have to lift heavy materials or stand for long periods of time.
As a manufacturing associate, your duties could include reading engineering drawings and executing production documents. They need to coordinate with others on the team and produce reports. They should be organized, detail-oriented with good communication skills, and have previous manufacturing experience.
Quality control of manufactured products is another important responsibility. They should be familiar with the manufacturing process and be able determine if products meet company standards. They should also be able to inspect the finished product and spot any potential defects.
Qualifications for a job as a director of manufacturing
Director of manufacturing is a job that requires you to manage all aspects of manufacturing operations, including scheduling and product production. In this role, you will need to maintain high standards of quality, as well as implementing and evaluating new ideas and techniques to cut costs. You will also have to evaluate the performance of your staff. For a job as a director in manufacturing, you will need to demonstrate leadership, organizational skills and problem solving.
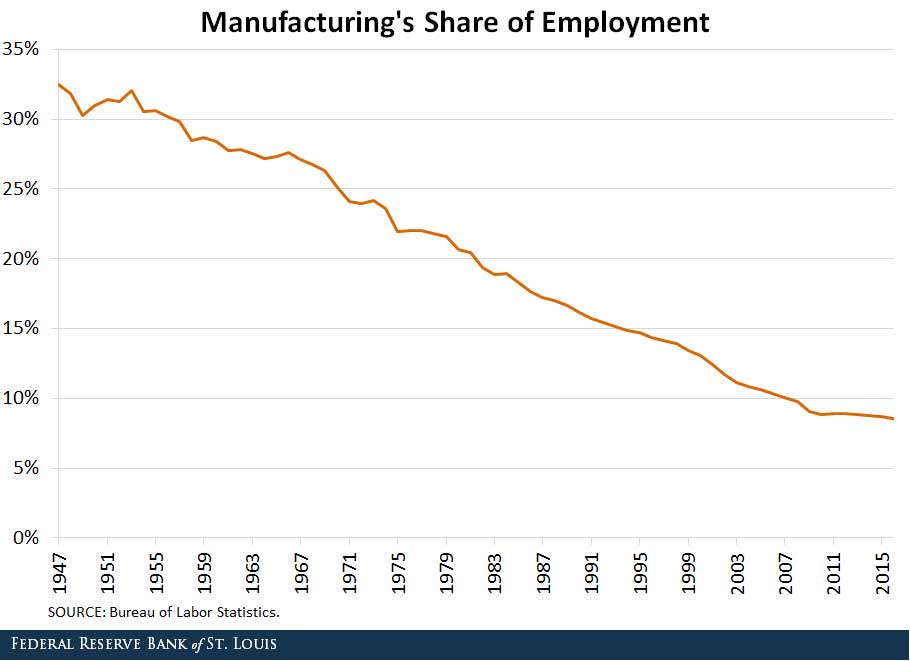
You will be a manufacturing director and work closely with engineers and designers to create products and services. To ensure everyone understands their roles and is on the same page, you will need excellent communication skills. Your ability to communicate effectively is key to your ability to oversee the entire business. As a director for manufacturing, you will need to mentor and coach employees. For example, you will need to provide training to employees on safety protocols, risk mitigation, and new equipment.
FAQ
What are the responsibilities for a manufacturing manager
The manufacturing manager should ensure that every manufacturing process is efficient and effective. They should also be aware of any problems within the company and act accordingly.
They should also be able and comfortable communicating with other departments like sales and marketing.
They should be up to date on the latest trends and be able apply this knowledge to increase productivity and efficiency.
What kind of jobs are there in logistics?
Logistics can offer many different jobs. Some examples are:
-
Warehouse workers - They load trucks and pallets.
-
Transportation drivers: They drive trucks and trailers and deliver goods and make pick-ups.
-
Freight handlers – They sort and package freight at warehouses.
-
Inventory managers: They are responsible for the inventory and management of warehouses.
-
Sales representatives - They sell products.
-
Logistics coordinators: They plan and manage logistics operations.
-
Purchasing agents: They are responsible for purchasing goods and services to support company operations.
-
Customer service representatives - They answer calls and emails from customers.
-
Ship clerks - They issue bills and process shipping orders.
-
Order fillers: They fill orders based off what has been ordered and shipped.
-
Quality control inspectors – They inspect incoming and outgoing products to ensure that there are no defects.
-
Other - Logistics has many other job opportunities, including transportation supervisors, logistics specialists, and cargo specialists.
What is production planning?
Production planning is the process of creating a plan that covers all aspects of production. This includes scheduling, budgeting and crew, location, equipment, props, and more. It is important to have everything ready and planned before you start shooting. This document should include information about how to achieve the best results on-set. It should include information about shooting locations, casting lists, crew details, equipment requirements, and shooting schedules.
It is important to first outline the type of film you would like to make. You may have already decided where you would like to shoot, or maybe there are specific locations or sets that you want to use. Once you have determined your scenes and locations, it is time to start figuring out the elements that you will need for each scene. Perhaps you have decided that you need to buy a car but aren't sure which model. To narrow your options, you can search online for available models.
After you have selected the car you want, you can begin to think about additional features. What about additional seating? Or perhaps you need someone walking around the back of the car? Maybe you want to change the interior color from black to white? These questions will help determine the look and feel you want for your car. Also, think about what kind of shots you would like to capture. You will be filming close-ups and wide angles. Maybe you want the engine or the steering wheels to be shown. These details will help identify the exact car you wish to film.
Once you've determined the above, it is time to start creating a calendar. You will know when you should start and when you should finish shooting. The schedule will show you when to get there, what time to leave, and when to return home. This way, everyone knows what they need to do and when. It is possible to make arrangements in advance for additional staff if you are looking to hire. There is no point in hiring someone who won't turn up because you didn't let him know.
It is important to calculate the amount of filming days when you are creating your schedule. Some projects take only a few days while others can last several weeks. While creating your schedule, it is important to remember whether you will require more than one shot per day. Multiple takes of the same location will lead to higher costs and take more time. If you aren't sure whether you need multiple shots, it is best to take fewer photos than you would like.
Another important aspect of production planning is setting budgets. It is important to set a realistic budget so you can work within your budget. It is possible to reduce the budget at any time if you experience unexpected problems. But, don't underestimate how much money you'll spend. You'll end up with less money after paying for other things if the cost is underestimated.
Planning production is a tedious process. Once you have a good understanding of how everything works together, planning future projects becomes easy.
What is the responsibility of a logistics manager?
Logistics managers are responsible for ensuring that all goods arrive in perfect condition and on time. This is achieved by using their knowledge and experience with the products of the company. He/she should make sure that enough stock is on hand to meet the demands.
What does manufacturing mean?
Manufacturing Industries refers to businesses that manufacture products. The people who buy these products are called consumers. This is accomplished by using a variety of processes, including production, distribution and retailing. These companies produce goods using raw materials and other equipment. This includes all types if manufactured goods.
Statistics
- According to the United Nations Industrial Development Organization (UNIDO), China is the top manufacturer worldwide by 2019 output, producing 28.7% of the total global manufacturing output, followed by the United States, Japan, Germany, and India.[52][53] (en.wikipedia.org)
- Job #1 is delivering the ordered product according to specifications: color, size, brand, and quantity. (netsuite.com)
- Many factories witnessed a 30% increase in output due to the shift to electric motors. (en.wikipedia.org)
- You can multiply the result by 100 to get the total percent of monthly overhead. (investopedia.com)
- [54][55] These are the top 50 countries by the total value of manufacturing output in US dollars for its noted year according to World Bank.[56] (en.wikipedia.org)
External Links
How To
Six Sigma in Manufacturing
Six Sigma refers to "the application and control of statistical processes (SPC) techniques in order to achieve continuous improvement." Motorola's Quality Improvement Department developed it at their Tokyo plant in Japan in 1986. Six Sigma's basic concept is to improve quality and eliminate defects through standardization. In recent years, many companies have adopted this method because they believe there is no such thing as perfect products or services. Six Sigma's main objective is to reduce variations from the production average. It is possible to measure the performance of your product against an average and find the percentage of time that it differs from the norm. If this deviation is too big, you know something needs fixing.
Understanding how variability works in your company is the first step to Six Sigma. Once you have a good understanding of the basics, you can identify potential sources of variation. It is important to identify whether the variations are random or systemic. Random variations occur when people do mistakes. Symmetrical variations are caused due to factors beyond the process. If you make widgets and some of them end up on the assembly line, then those are considered random variations. You might notice that your widgets always fall apart at the same place every time you put them together.
Once you've identified where the problems lie, you'll want to design solutions to eliminate those problems. It might mean changing the way you do business or redesigning it entirely. Test them again once you've implemented the changes. If they don't work, you will need to go back to the drawing boards and create a new plan.