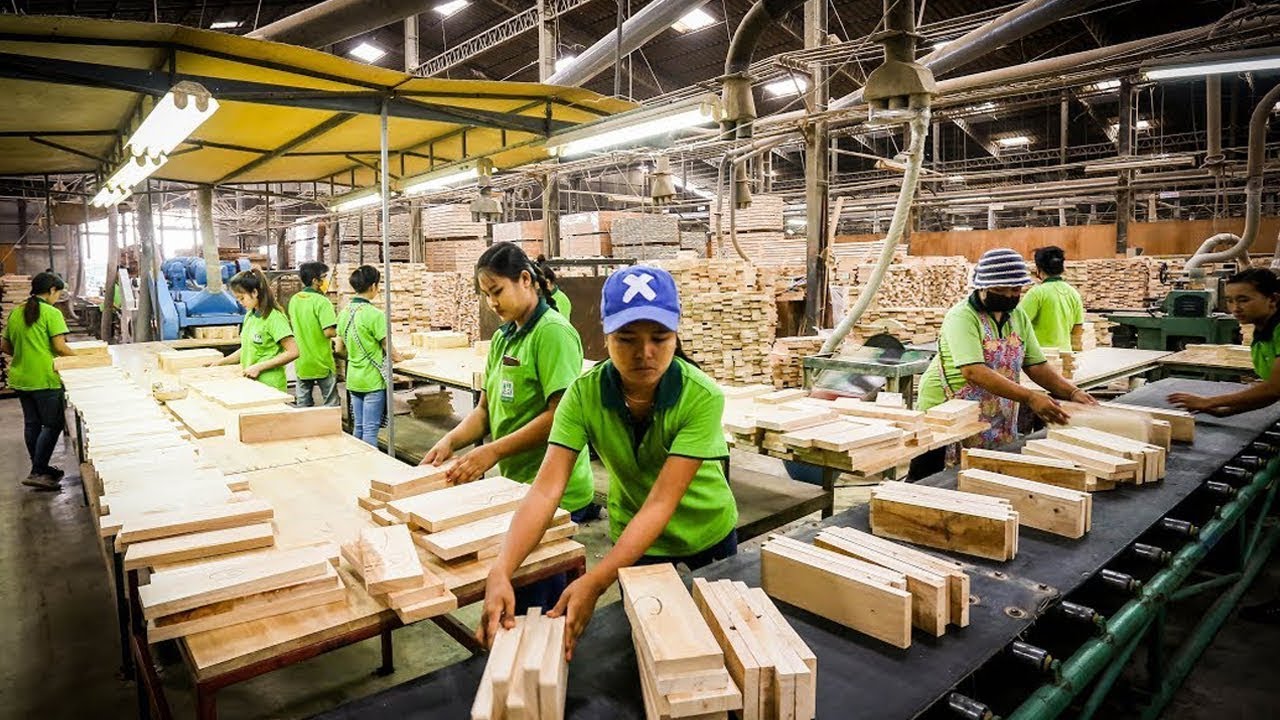
Gemba Walk was originally developed by Toyota. It allows managers to go to the shop floor and gain insight into company processes. This is an important part of any facility improvement project. It allows managers and employees to be more aware of the business processes and make better decision. This helps you to spot potential problems and possible solutions.
Gemba is a Japanese word that refers to "where the work takes place". It is used to describe the factory floor or shop floor, but can refer to any place where a product or service is created. Gemba is the Japanese business philosophy. Gemba's goal is to gain in-depth knowledge about the organization's processes and eliminate waste while improving efficiency.
Companies that want to improve their processes or eliminate waste should consider Gemba walks. They promote collaboration and harmony within an organization. They encourage employees and their families to share ideas. This can increase the quality of any product or service. Managers and executives can benefit from them by better understanding the company's processes.
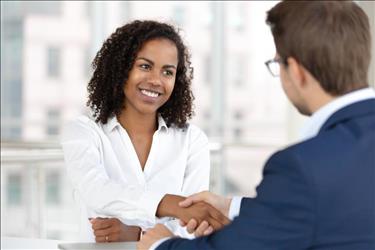
Gemba walks are generally conducted by supervisors or managers. But they can also be done by executives. Gemba walks should not be performed by managers or supervisors. Gemba walks should be done with Sensei or a Lean teacher every week for 45-60 minutes. Because it is easy to observe how workers do their jobs, these walks should not be done during peak hours.
Gemba Walks are designed to help executives and managers understand the process and identify improvements. They can also improve safety in an organization. Safety is the largest waste stream from manufacturing plants. Increasing safety can lead to continuous improvement.
Gemba Walks are an integral part of Lean, but should be used at all levels of the company. They are a great way for executives and leaders to get a fresh view on customers. This will lead to better products and services. Gemba Walks can help an organization achieve its full potential.
Gemba Walks are an integral part of Lean process design and are frequently used by key stakeholders at Kaizen events. Kaizen events bring together key stakeholders to assess activities and make recommendations.
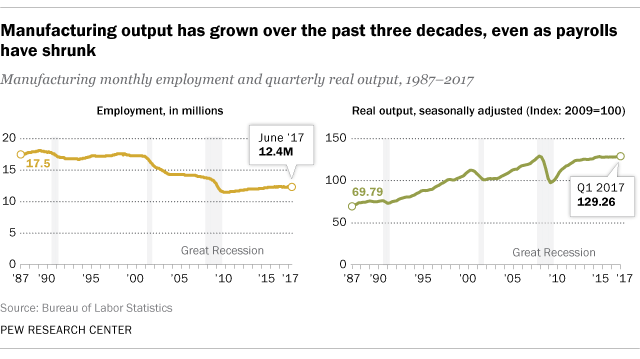
Gemba Walks should always be performed on a daily basis. They can reduce waste and increase productivity if done properly. Because they are the most hectic times of day, they should be performed during shift changes. This will give project managers and executives a fresh outlook on their businesses. These executives and project managers must also note any possible improvements they uncover, such new products or service ideas, as well any suggestions from employees.
FAQ
Can some manufacturing processes be automated?
Yes! Automation has been around since ancient times. The Egyptians invent the wheel thousands of year ago. Robots are now used to assist us in assembly lines.
There are many applications for robotics in manufacturing today. These include:
-
Automated assembly line robots
-
Robot welding
-
Robot painting
-
Robotics inspection
-
Robots that make products
Automation could also be used to improve manufacturing. 3D printing makes it possible to produce custom products in a matter of days or weeks.
How can manufacturing prevent production bottlenecks?
You can avoid bottlenecks in production by making sure that everything runs smoothly throughout the production cycle, from the moment you receive an order to the moment the product is shipped.
This includes planning to meet capacity requirements and quality control.
The best way to do this is to use continuous improvement techniques such as Six Sigma.
Six Sigma is a management system used to improve quality and reduce waste in every aspect of your organization.
It seeks to eliminate variation and create consistency in your work.
How important is automation in manufacturing?
Automating is not just important for manufacturers, but also for service providers. It enables them to provide services faster and more efficiently. It also helps to reduce costs and improve productivity.
What does it take for a logistics enterprise to succeed?
To be a successful businessman in logistics, you will need many skills and knowledge. For clients and suppliers to be successful, you need to have excellent communication skills. It is important to be able to analyse data and draw conclusions. You must be able to work well under pressure and handle stressful situations. To improve efficiency, you must be innovative and creative. You must be a strong leader to motivate others and direct them to achieve organizational goals.
It is also important to be efficient and well organized in order meet deadlines.
Why automate your factory?
Modern warehouses are increasingly dependent on automation. E-commerce has increased the demand for quicker delivery times and more efficient processes.
Warehouses have to be flexible to meet changing requirements. Technology is essential for warehouses to be able to adapt quickly to changing needs. Automation of warehouses offers many benefits. Here are some reasons why it's worth investing in automation:
-
Increases throughput/productivity
-
Reduces errors
-
Improves accuracy
-
Safety Boosts
-
Eliminates bottlenecks
-
Allows companies scale more easily
-
It makes workers more efficient
-
It gives visibility to everything that happens inside the warehouse
-
Enhances customer experience
-
Improves employee satisfaction
-
Reducing downtime and increasing uptime
-
High quality products delivered on-time
-
Human error can be eliminated
-
Assure compliance with regulations
Statistics
- According to a Statista study, U.S. businesses spent $1.63 trillion on logistics in 2019, moving goods from origin to end user through various supply chain network segments. (netsuite.com)
- In the United States, for example, manufacturing makes up 15% of the economic output. (twi-global.com)
- According to the United Nations Industrial Development Organization (UNIDO), China is the top manufacturer worldwide by 2019 output, producing 28.7% of the total global manufacturing output, followed by the United States, Japan, Germany, and India.[52][53] (en.wikipedia.org)
- It's estimated that 10.8% of the U.S. GDP in 2020 was contributed to manufacturing. (investopedia.com)
- Job #1 is delivering the ordered product according to specifications: color, size, brand, and quantity. (netsuite.com)
External Links
How To
How to Use the Just-In-Time Method in Production
Just-in-time is a way to cut costs and increase efficiency in business processes. It is a process where you get the right amount of resources at the right moment when they are needed. This means that you only pay the amount you actually use. Frederick Taylor first coined this term while working in the early 1900s as a foreman. Taylor observed that overtime was paid to workers if they were late in working. He then concluded that if he could ensure that workers had enough time to do their job before starting to work, this would improve productivity.
JIT teaches you to plan ahead and prepare everything so you don’t waste time. The entire project should be looked at from start to finish. You need to ensure you have enough resources to tackle any issues that might arise. If you anticipate that there might be problems, you'll have enough people and equipment to fix them. This will ensure that you don't spend more money on things that aren't necessary.
There are many types of JIT methods.
-
Demand-driven: This JIT is where you place regular orders for the parts/materials that are needed for your project. This will allow you to track how much material you have left over after using it. It will also allow you to predict how long it takes to produce more.
-
Inventory-based: This allows you to store the materials necessary for your projects in advance. This allows you predict the amount you can expect to sell.
-
Project-driven : This is a method where you make sure that enough money is set aside to pay the project's cost. Once you have an idea of how much material you will need, you can purchase the necessary materials.
-
Resource-based JIT: This is the most popular form of JIT. You assign certain resources based off demand. For example, if there is a lot of work coming in, you will have more people assigned to them. You'll have fewer orders if you have fewer.
-
Cost-based : This is similar in concept to resource-based. But here, you aren't concerned about how many people your company has but how much each individual costs.
-
Price-based pricing: This is similar in concept to cost-based but instead you look at how much each worker costs, it looks at the overall company's price.
-
Material-based: This approach is similar to cost-based. However, instead of looking at the total cost for the company, you look at how much you spend on average on raw materials.
-
Time-based JIT: A variation on resource-based JIT. Instead of worrying about how much each worker costs, you can focus on how long the project takes.
-
Quality-based: This is yet another variation of resource-based JIT. Instead of thinking about the cost of each employee or the time it takes to produce something, you focus on how good your product quality.
-
Value-based JIT: One of the most recent forms of JIT. This is where you don't care about how the products perform or whether they meet customers' expectations. Instead, you're focused on how much value you add to the market.
-
Stock-based: This inventory-based approach focuses on how many items are being produced at any one time. It's useful when you want maximum production and minimal inventory.
-
Just-in time (JIT), planning: This is a combination JIT/supply chain management. It is the process of scheduling components' delivery as soon as they have been ordered. It reduces lead times and improves throughput.