
The bill of material (BOM) is an important part in the manufacturing process. This document lists all items necessary to produce end products, including raw materials and assembly procedures. It is essential for any company, no matter if they are selling directly to customers or via retail channels. It assists companies in keeping track of their stock, avoiding waste and reducing production errors. It is also useful for companies to avoid stockouts.
A bill-of-materials is a detailed tabular document that lists all components of an assembly. The document also lists the parts that will be used to construct the assembly. You can purchase the parts and subassemblies from external sources or make them yourself. A unique part number will be required to identify the parts. This allows the assembly staff to easily identify and gather all the materials they require. Note any special requirements that may be required on the bill. These special requirements could lead to delays or even errors during the manufacturing process.
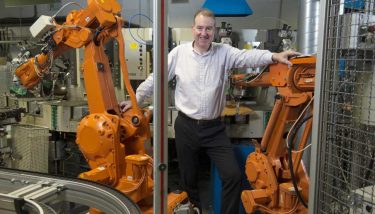
Companies need bills of materials to be able to track the components and the raw materials. They enable more productive production. They are useful in preventing stockouts, and they allow companies to forecast sales. These documents allow companies to keep track of the materials used for production, and avoid over-ordering.
A bill-of-materials is a document listing the materials, components and subassemblies that are required to manufacture a product. The bill also includes the labor and time needed to complete each stage. It is important to remember that the bill should include the supplier(s), for each part. You may also need to include any other information that is essential for the production process. It is crucial to note that the bill of materials may differ from company to company.
To ensure that the final product works properly, bills of materials are used during manufacturing. Companies can use them to plan and order materials and avoid waste. The bill of materials helps manufacturers to identify the raw materials needed to make a product and determine the proper amounts for each piece. It is also important to note that this document is a roadmap for the finished product. It can be difficult to create a bill of materials, especially when a product has many parts. There are software tools that allow you to create a bill.
To reflect the requirements and specifications of a project, a bill of materials is prepared. It can be used as a blueprint for the finished product or as a communication card between manufacturing and supply chain partners. This document is useful for companies in order to avoid over-ordering materials and keep track of all components used in the production process.
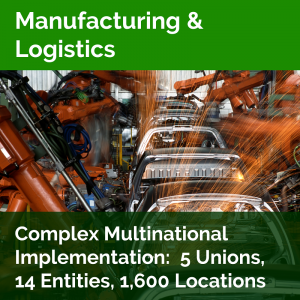
Any company that sells directly to customers or through retail channels needs a bill of materials. Bills allow for higher productivity and greater profits. They help companies to avoid waste, reduce production mistakes, and prevent stockouts.
FAQ
What are the logistics products?
Logistics refers to all activities that involve moving goods from A to B.
They include all aspects of transport, including packaging, loading, transporting, unloading, storing, warehousing, inventory management, customer service, distribution, returns, and recycling.
Logisticians ensure that the product is delivered to the correct place, at the right time, and under safe conditions. Logisticians assist companies in managing their supply chains by providing information such as demand forecasts, stock levels and production schedules.
They monitor shipments in transit, ensure quality standards, manage inventories, replenish orders, coordinate with suppliers and other vendors, and offer support services for sales, marketing, and customer service.
Is automation necessary in manufacturing?
Automation is essential for both manufacturers and service providers. It allows them to offer services faster and more efficiently. It also helps to reduce costs and improve productivity.
What is the job of a logistics manger?
Logistics managers make sure all goods are delivered on schedule and without damage. This is done by using his/her experience and knowledge of the company's products. He/she should make sure that enough stock is on hand to meet the demands.
What is the difference between manufacturing and logistics
Manufacturing is the act of producing goods from raw materials using machines and processes. Logistics encompasses the management of all aspects associated with supply chain activities such as procurement, production planning, distribution and inventory control. It also includes customer service. As a broad term, manufacturing and logistics often refer to both the creation and delivery of products.
What skills should a production planner have?
Being a production planner is not easy. You need to be organized and flexible. Communication skills are essential to ensure that you can communicate effectively with clients, colleagues, and customers.
How can manufacturing avoid production bottlenecks
To avoid production bottlenecks, ensure that all processes run smoothly from the moment you receive your order to the time the product ships.
This includes planning for both capacity requirements and quality control measures.
This can be done by using continuous improvement techniques, such as Six Sigma.
Six Sigma can be used to improve the quality and decrease waste in all areas of your company.
It seeks to eliminate variation and create consistency in your work.
Why is logistics important for manufacturing?
Logistics are an integral part any business. They can help you achieve great success by helping you manage product flow from raw material to finished goods.
Logistics are also important in reducing costs and improving efficiency.
Statistics
- (2:04) MTO is a production technique wherein products are customized according to customer specifications, and production only starts after an order is received. (oracle.com)
- In the United States, for example, manufacturing makes up 15% of the economic output. (twi-global.com)
- It's estimated that 10.8% of the U.S. GDP in 2020 was contributed to manufacturing. (investopedia.com)
- [54][55] These are the top 50 countries by the total value of manufacturing output in US dollars for its noted year according to World Bank.[56] (en.wikipedia.org)
- Many factories witnessed a 30% increase in output due to the shift to electric motors. (en.wikipedia.org)
External Links
How To
How to use lean manufacturing in the production of goods
Lean manufacturing refers to a method of managing that seeks to improve efficiency and decrease waste. It was first developed in Japan in the 1970s/80s by Taiichi Ahno, who was awarded the Toyota Production System (TPS), award from KanjiToyoda, the founder of TPS. The first book published on lean manufacturing was titled "The Machine That Changed the World" written by Michael L. Watkins and published in 1990.
Lean manufacturing is often defined as a set of principles used to improve the quality, speed, and cost of products and services. It is about eliminating defects and waste from all stages of the value stream. The five-steps of Lean Manufacturing are just-in time (JIT), zero defect and total productive maintenance (TPM), as well as 5S. Lean manufacturing eliminates non-value-added tasks like inspection, rework, waiting.
In addition to improving product quality and reducing costs, lean manufacturing helps companies achieve their goals faster and reduces employee turnover. Lean manufacturing has been deemed one of the best ways to manage the entire value-chain, including customers, distributors as well retailers and employees. Lean manufacturing can be found in many industries. Toyota's philosophy has been a key driver of success in many industries, including automobiles and electronics.
Five fundamental principles underlie lean manufacturing.
-
Define Value- Identify the added value your company brings to society. What makes you stand out from your competitors?
-
Reduce Waste – Eliminate all activities that don't add value throughout the supply chain.
-
Create Flow – Ensure that work flows smoothly throughout the process.
-
Standardize and Simplify – Make processes as consistent, repeatable, and as simple as possible.
-
Build relationships - Develop and maintain personal relationships with both your internal and external stakeholders.
Although lean manufacturing has always been around, it is gaining popularity in recent years because of a renewed interest for the economy after 2008's global financial crisis. To increase their competitiveness, many businesses have turned to lean manufacturing. Some economists even believe that lean manufacturing can be a key factor in economic recovery.
Lean manufacturing has many benefits in the automotive sector. These include improved customer satisfaction, reduced inventory levels, lower operating costs, increased productivity, and better overall safety.
Lean manufacturing can be applied to almost every aspect of an organization. However, it is particularly useful when applied to the production side of an organization because it ensures that all steps in the value chain are efficient and effective.
There are three main types of lean manufacturing:
-
Just-in Time Manufacturing: This lean manufacturing method is commonly called "pull systems." JIT refers to a system in which components are assembled at the point of use instead of being produced ahead of time. This strategy aims to decrease lead times, increase availability of parts and reduce inventory.
-
Zero Defects Manufacturing - ZDM: ZDM focuses its efforts on making sure that no defective units leave a manufacturing facility. You should repair any part that needs to be repaired during an assembly line. This applies to finished goods that may require minor repairs before shipment.
-
Continuous Improvement: Continuous Improvement aims to improve efficiency by continually identifying problems and making adjustments to eliminate or minimize waste. Continuous Improvement (CI) involves continuous improvement in processes, people, tools, and infrastructure.