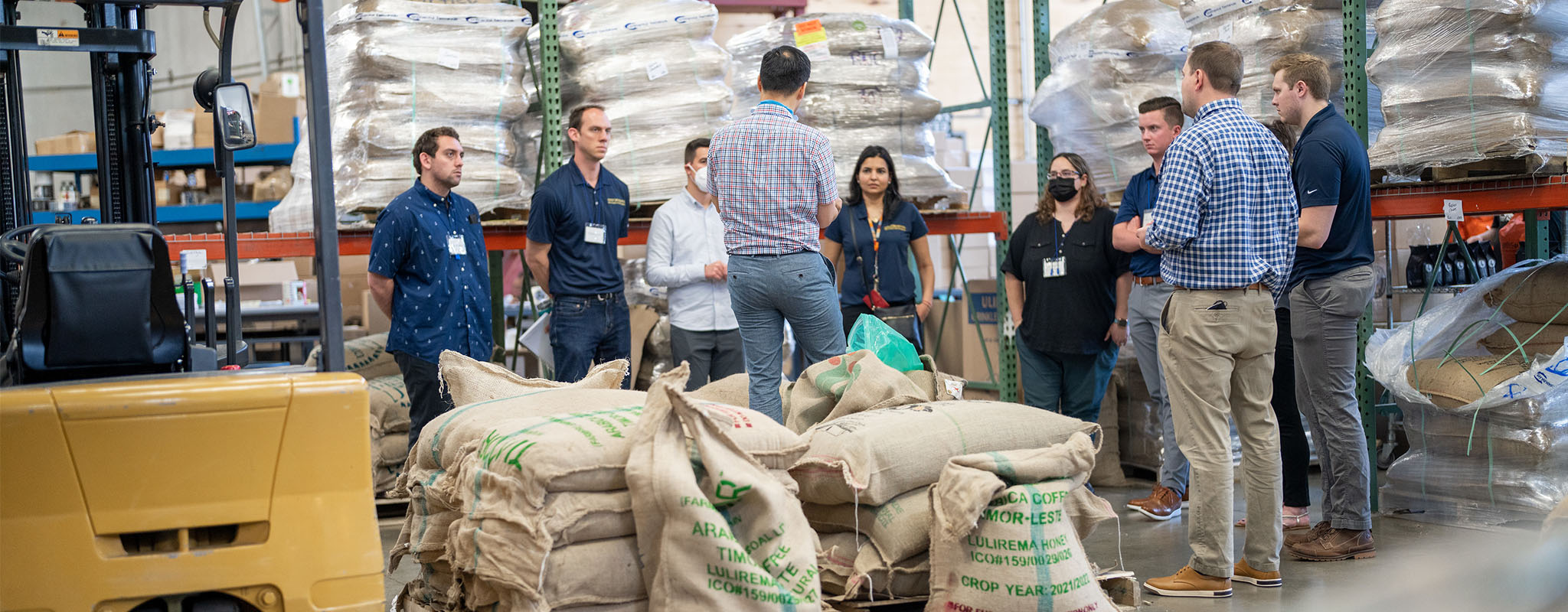
Industrial engineers are able to use math and science to increase efficiency in production. They can identify and fix flaws in systems, and create solutions that increase productivity and performance. They also have the ability to create new processes that use fewer resources. This is an attractive career choice for those who enjoy working in teams and being independent. It allows you to progress in your career and make the transition into management.
An industrial engineer may work in many different industries. Some of their duties include working in hazardous materials, or at very high temperatures. They might be required travel to other places in order to accomplish their work. They will also need to be able to communicate with clients via telephone, email and face to face. They should be able to comprehend workplace safety laws.
Industrial engineers are highly respected for their ability and creativity in solving problems. Many industrial engineers love solving problems that improve productivity. They may be tasked with redesigning assembly lines to reduce costs and improve production. Sometimes, they may have to work overtime in order to meet deadlines. They might have the opportunity to collaborate with other engineers to create new production processes.
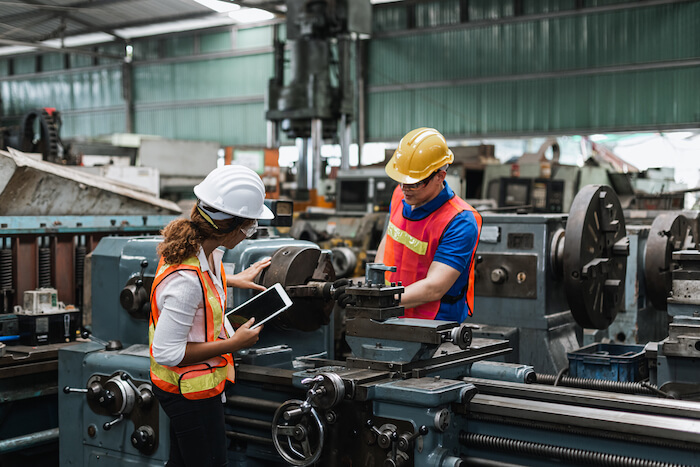
Industrial engineers are expected to have strong interpersonal skills, including the ability to listen and understand what others are saying. They also have to be able to work effectively with supervisors and colleagues. They must also be able to use their critical thinking skills to identify and assess alternative solutions to a problem. They can predict changes and take action to increase their prospects.
Industrial engineers might be required to travel, work long hours, or work in noisy environments depending on their job duties. It may be difficult for them to balance their work and personal lives. This can be difficult to manage, but it is possible to find ways to adjust to the demands of their work.
Industrial engineers usually have a bachelor's degree. They then have the opportunity to earn a master's or doctorate degree. It can take anywhere from two to seven years for this degree program. It is important to select a degree program that is suited for your needs. Many universities offer online degrees in industrial engineer. These programs allow students to finish their studies quickly and without paying high tuition fees. These programs also allow for flexibility in terms of study time.
Industrial engineers may find joining professional organizations like the Institute of Industrial and Systems Engineers helpful. This organization hosts conferences, publishes case studies and white papers, and supports professionals in industrial engineering. Graduates can also apply for fellowships. They also have the option to obtain MOOCs certifications. They may also participate in fellowships from the American Society for Engineering Education.

Industrial engineers can also find employment with government agencies. They may need to be licensed. Some large companies may provide formal training. These employers value the amount of experience that industrial engineers have.
FAQ
What is the role of a production manager?
Production planners ensure all aspects of the project are delivered within time and budget. They also ensure that the product/service meets the client’s needs.
How can we improve manufacturing efficiency?
The first step is to determine the key factors that impact production time. The next step is to identify the most important factors that affect production time. If you don’t know where to begin, consider which factors have the largest impact on production times. Once you have identified the factors, then try to find solutions.
How can manufacturing prevent production bottlenecks?
Production bottlenecks can be avoided by ensuring that processes are running smoothly during the entire production process, starting with the receipt of an order and ending when the product ships.
This includes both quality control and capacity planning.
Continuous improvement techniques such Six Sigma can help you achieve this.
Six Sigma is a management system used to improve quality and reduce waste in every aspect of your organization.
It's all about eliminating variation and creating consistency in work.
Statistics
- (2:04) MTO is a production technique wherein products are customized according to customer specifications, and production only starts after an order is received. (oracle.com)
- In 2021, an estimated 12.1 million Americans work in the manufacturing sector.6 (investopedia.com)
- In the United States, for example, manufacturing makes up 15% of the economic output. (twi-global.com)
- Job #1 is delivering the ordered product according to specifications: color, size, brand, and quantity. (netsuite.com)
- Many factories witnessed a 30% increase in output due to the shift to electric motors. (en.wikipedia.org)
External Links
How To
How to Use lean manufacturing in the Production of Goods
Lean manufacturing refers to a method of managing that seeks to improve efficiency and decrease waste. It was developed in Japan between 1970 and 1980 by Taiichi Ohno. TPS founder Kanji Tyoda gave him the Toyota Production System, or TPS award. The first book published on lean manufacturing was titled "The Machine That Changed the World" written by Michael L. Watkins and published in 1990.
Lean manufacturing refers to a set of principles that improve the quality, speed and costs of products and services. It emphasizes the elimination and minimization of waste in the value stream. Just-in-time (JIT), zero defect (TPM), and 5S are all examples of lean manufacturing. Lean manufacturing emphasizes reducing non-value-added activities like inspection, rework and waiting.
Lean manufacturing not only improves product quality but also reduces costs. Companies can also achieve their goals faster by reducing employee turnover. Lean manufacturing is a great way to manage the entire value chain including customers, suppliers, distributors and retailers as well as employees. Lean manufacturing can be found in many industries. For example, Toyota's philosophy underpins its success in automobiles, electronics, appliances, healthcare, chemical engineering, aerospace, paper, food, etc.
Five principles are the basis of lean manufacturing:
-
Define Value - Determine the value that your business brings to society. Also, identify what sets you apart from your competitors.
-
Reduce Waste – Eliminate all activities that don't add value throughout the supply chain.
-
Create Flow: Ensure that the work process flows without interruptions.
-
Standardize & simplify - Make processes consistent and repeatable.
-
Develop Relationships: Establish personal relationships both with internal and external stakeholders.
Lean manufacturing is not a new concept, but it has been gaining popularity over the last few years due to a renewed interest in the economy following the global financial crisis of 2008. Many businesses have adopted lean manufacturing techniques to help them become more competitive. Some economists even believe that lean manufacturing can be a key factor in economic recovery.
Lean manufacturing is now becoming a common practice in the automotive industry, with many benefits. These include higher customer satisfaction, lower inventory levels, lower operating expenses, greater productivity, and improved overall safety.
Any aspect of an enterprise can benefit from Lean manufacturing. It is especially useful for the production aspect of an organization, as it ensures that every step in the value chain is efficient and effective.
There are three types of lean manufacturing.
-
Just-in Time Manufacturing, (JIT): This kind of lean manufacturing is also commonly known as "pull-systems." JIT means that components are assembled at the time of use and not manufactured in advance. This approach is designed to reduce lead times and increase the availability of components. It also reduces inventory.
-
Zero Defects Manufacturing - ZDM: ZDM focuses its efforts on making sure that no defective units leave a manufacturing facility. You should repair any part that needs to be repaired during an assembly line. This applies to finished products, which may need minor repairs before they are shipped.
-
Continuous Improvement (CI): CI aims to improve the efficiency of operations by continuously identifying problems and making changes in order to eliminate or minimize waste. It involves continuous improvement of processes, people, and tools.