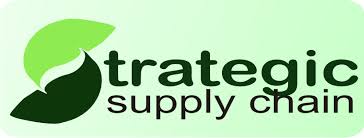
Tennessee offers an economy that is diverse and career options for all. Tennessee has a wide range of career opportunities, whether you want to work in manufacturing or another industry.
Manufacturing Jobs in Tennessee
MNI's data indicates that there are over 6109 factories in the state, employing 408,131 people. These companies produce a variety of goods, including automotive parts, industrial machinery and fabricated metal products.
Transportation Equipment Manufacturing: This is the biggest industrial sector in the State. This industry produces commercial and military airplane parts, as well as trucks and other vehicles. In recent years, these firms have added many workers as Nissan expanded production at its Smyrna plant and Volkswagen increased production at Chattanooga.
Industrial Machinery - Second only to transport equipment in size, industrial machinery manufactures parts for industries like agriculture, energy, defense, and defense. DENSO Manufacturing Tennessee and Maremont Exhaust Products are among the manufacturers who work in this sector.
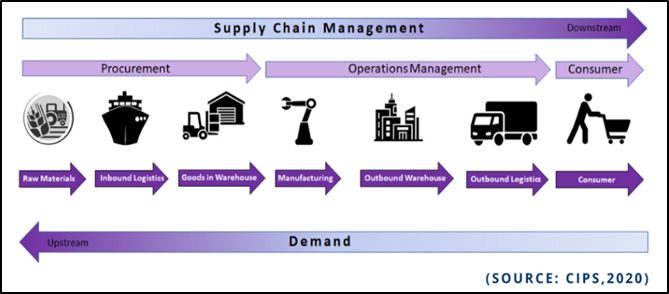
Food Processing: This is the third most important industrial sector. Producers of food such as Little Debbie snackcakes and Drake's Devil Dogs are included. These companies employ many people, such as production staff, packaging specialists, and warehouse employees.
Advanced Manufacturing - The fourth most important industry in the state, advanced manufacture is an essential sector for the economy. More than 32,000 jobs are currently being added to this field. Eastman Chemicals and Consolidated Nuclear Security are some of the leading employers in this sector.
Take a look at the factory jobs in Tennessee.
It is best to start your manufacturing career by completing an apprenticeship or training course. These programs give you the chance to get hands-on training in specific areas of manufacturing. These courses usually focus on one skill, such a welding or electrical works, and are customized to meet your specific interests and qualifications.
Some programs cover a broader area such as manufacturing or quality management. These programs are usually taught by community colleges or other providers of training.
Those who are interested in pursuing a career in manufacturing can also look for manufacturing jobs through online job boards and classified ads. These sites offer a wealth of information about a range of companies and allow you to submit applications without having to speak to hiring managers.
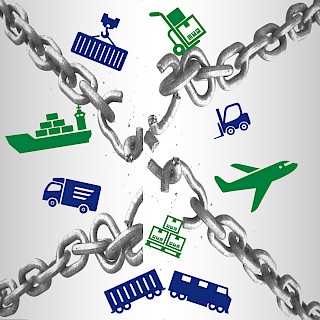
You can start your search for a job within the manufacturing sector by visiting the careers pages of local or national employers. The site will usually give you an overview of the business and list any current positions.
You can also find jobs in manufacturing by attending job fairs. These often give you the opportunity to interview for several different companies. These events are difficult to locate and may not include all of the manufacturing jobs available in your locality.
FAQ
How can we improve manufacturing efficiency?
The first step is to determine the key factors that impact production time. We then need to figure out how to improve these variables. If you don't know where to start, then think about which factor(s) have the biggest impact on production time. Once you have identified them, it is time to identify solutions.
What do you mean by warehouse?
A warehouse is a place where goods are stored until they are sold. It can be an outdoor or indoor area. It may also be an indoor space or an outdoor area.
What is production management?
Production Planning refers to the development of a plan for every aspect of production. This document aims to ensure that everything is planned and ready when you are ready to shoot. This document should also include information on how to get the best result on set. This information includes locations, crew details and equipment requirements.
The first step is to decide what you want. You may have already chosen the location you want, or there are locations or sets you prefer. Once you've identified the locations and scenes you want to use, you can begin to plan what elements you need for each scene. Perhaps you have decided that you need to buy a car but aren't sure which model. In this case, you could start looking up cars online to find out what models are available and then narrow your choices by choosing between different makes and models.
After you have chosen the right car, you will be able to begin thinking about accessories. Do you need people sitting in the front seats? Maybe you need someone to move around in the back. You may want to change the interior's color from black or white. These questions will help determine the look and feel you want for your car. Another thing you can do is think about what type of shots are desired. What type of shots will you choose? Perhaps you want to show the engine or the steering wheel? All of these things will help you identify the exact style of car you want to film.
Once you have established all the details, you can create a schedule. You can use a schedule to determine when and where you need it to be shot. A schedule for each day will detail when you should arrive at the location and when you need leave. This way, everyone knows what they need to do and when. You can also make sure to book extra staff in advance if you have to hire them. It is not worth hiring someone who won’t show up because you didn’t tell him.
Your schedule will also have to be adjusted to reflect the number of days required to film. Some projects can be completed in a matter of days or weeks. Others may take several days. You should consider whether you will need more than one shot per week when creating your schedule. Multiple takes of the same location will lead to higher costs and take more time. It's better to be safe than sorry and shoot less takes if you're not certain whether you need more takes.
Budgeting is another crucial aspect of production plan. You will be able to manage your resources if you have a realistic budget. It is possible to reduce the budget at any time if you experience unexpected problems. However, you shouldn't overestimate the amount of money you will spend. If you underestimate the cost of something, you will have less money left after paying for other items.
Production planning is a very detailed process, but once you understand how everything works together, it becomes easier to plan future projects.
Can certain manufacturing steps be automated?
Yes! Since ancient times, automation has been in existence. The Egyptians invent the wheel thousands of year ago. To help us build assembly lines, we now have robots.
Robotics is used in many manufacturing processes today. They include:
-
Robots for assembly line
-
Robot welding
-
Robot painting
-
Robotics inspection
-
Robots that create products
Automation can be applied to manufacturing in many other ways. For example, 3D printing allows us to make custom products without having to wait for weeks or months to get them manufactured.
What is the difference between manufacturing and logistics
Manufacturing is the act of producing goods from raw materials using machines and processes. Logistics encompasses the management of all aspects associated with supply chain activities such as procurement, production planning, distribution and inventory control. It also includes customer service. Manufacturing and logistics are often considered together as a broader term that encompasses both the process of creating products and delivering them to customers.
What is the importance of automation in manufacturing?
Not only are service providers and manufacturers important, but so is automation. Automation allows them to deliver services quicker and more efficiently. In addition, it helps them reduce costs by reducing human errors and improving productivity.
Statistics
- According to a Statista study, U.S. businesses spent $1.63 trillion on logistics in 2019, moving goods from origin to end user through various supply chain network segments. (netsuite.com)
- It's estimated that 10.8% of the U.S. GDP in 2020 was contributed to manufacturing. (investopedia.com)
- You can multiply the result by 100 to get the total percent of monthly overhead. (investopedia.com)
- In the United States, for example, manufacturing makes up 15% of the economic output. (twi-global.com)
- Many factories witnessed a 30% increase in output due to the shift to electric motors. (en.wikipedia.org)
External Links
How To
How to Use the Just In Time Method in Production
Just-in-time is a way to cut costs and increase efficiency in business processes. It allows you to get the right amount resources at the right time. This means you only pay what you use. The term was first coined by Frederick Taylor, who developed his theory while working as a foreman in the early 1900s. Taylor observed that overtime was paid to workers if they were late in working. He then concluded that if he could ensure that workers had enough time to do their job before starting to work, this would improve productivity.
The idea behind JIT is that you should plan ahead and have everything ready so you don't waste money. It is important to look at your entire project from beginning to end and ensure that you have enough resources to handle any issues that may arise. You'll be prepared to handle any potential problems if you know in advance. You won't have to pay more for unnecessary items.
There are different types of JIT methods:
-
Demand-driven: This type of JIT allows you to order the parts/materials required for your project on a regular basis. This will enable you to keep track of how much material is left after you use it. This will allow you to calculate how long it will take to make more.
-
Inventory-based: This allows you to store the materials necessary for your projects in advance. This allows for you to anticipate how much you can sell.
-
Project-driven: This means that you have enough money to pay for your project. When you know how much you need, you'll purchase the appropriate amount of materials.
-
Resource-based JIT: This type of JIT is most commonly used. You assign certain resources based off demand. For example, if there is a lot of work coming in, you will have more people assigned to them. If you don’t have many orders you will assign less people to the work.
-
Cost-based: This is the same as resource-based except that you don't care how many people there are but how much each one of them costs.
-
Price-based: This approach is very similar to the cost-based method except that you don't look at individual workers costs but the total cost of the company.
-
Material-based: This is quite similar to cost-based, but instead of looking at the total cost of the company, you're concerned with how much raw materials you spend on average.
-
Time-based JIT is another form of resource-based JIT. Instead of focusing on the cost of each employee, you will focus on the time it takes to complete a project.
-
Quality-based JIT: Another variation on resource-based JIT. Instead of worrying about the costs of each employee or how long it takes for something to be made, you should think about how quality your product is.
-
Value-based: This is one of the newest forms of JIT. You don't worry about whether the products work or if they meet customer expectations. Instead, you're focused on how much value you add to the market.
-
Stock-based: This inventory-based approach focuses on how many items are being produced at any one time. It's useful when you want maximum production and minimal inventory.
-
Just-in time (JIT), planning: This is a combination JIT/supply chain management. It refers to the process of scheduling the delivery of components as soon as they are ordered. It reduces lead times and improves throughput.