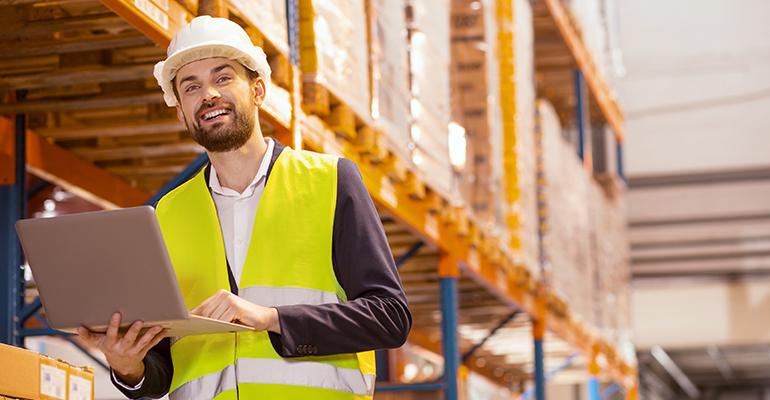
The Jacksonville, Florida area has a growing need for logistic jobs. These positions are crucial in the transportation and distribution of goods from factory floor to customer's doorstep. Jobs in this field can pay a handsome sum, especially if you know what you're doing. Here are some tips and tricks that will help you get your dream job.
To begin, you should create a Monster profile. You'll have access to job alerts and a customized list of related listings. Expert advice is also available. A skilled recruiter can even explain the perks of working for one company to you so you're prepared to face the competition. It's easy to get the job done if you know what your qualifications are and how they relate to the job you are applying for.
If you have the time, think about a paid internship. A paid internship will allow you to experience the professional work environment for as little as $10-15 per hour. Not to mention, you'll gain real-world experience that you can apply to your job search. This is the best kind of training you can get. You'll also be given a bag full of goodies.
It is important to remember that you don’t need to be a logistician to get the job of your dreams. There are many opportunities for entry-level logistics professionals with no frills. Vaco and Penske provide their employees with a traditional working environment. Others offer more flexible options. You'll find a job in Jacksonville regardless of your choice.
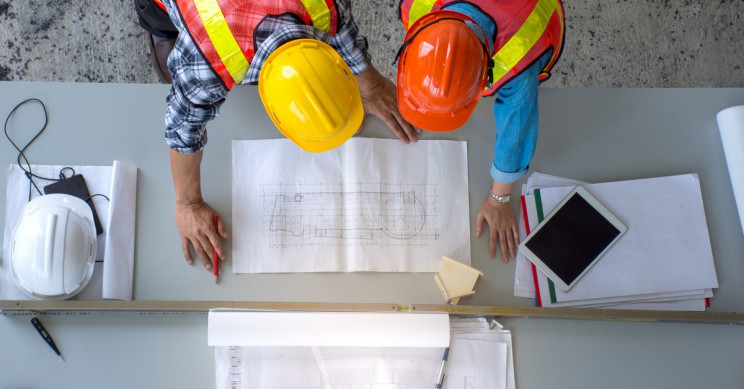
Scott Logistics Corp. and Quaker Transportation are top-rated companies in the area that can help you get started in your career. These companies are both 3PLs (third parties logistics providers) and will provide you with an opportunity to see the working environment at large companies. Then you will be able choose which one suits your needs best. It's not fair to lose out on a lucrative job because you don't know how to find it.
FAQ
What skills do production planners need?
To become a successful production planner, you need to be organized, flexible, and able to multitask. Effective communication with clients and colleagues is essential.
What is the difference in Production Planning and Scheduling, you ask?
Production Planning (PP), is the process of deciding what production needs to take place at any given time. Forecasting and identifying production capacity are two key elements to this process.
Scheduling is the process of assigning specific dates to tasks so they can be completed within the specified timeframe.
What is the role of a production manager?
A production planner makes sure all project elements are delivered on schedule, within budget, as well as within the agreed scope. A production planner ensures that the service and product meet the client's expectations.
What are the 4 types of manufacturing?
Manufacturing is the process of transforming raw materials into useful products using machines and processes. Manufacturing can include many activities such as designing and building, testing, packaging shipping, selling, servicing, and other related activities.
Statistics
- Job #1 is delivering the ordered product according to specifications: color, size, brand, and quantity. (netsuite.com)
- It's estimated that 10.8% of the U.S. GDP in 2020 was contributed to manufacturing. (investopedia.com)
- According to a Statista study, U.S. businesses spent $1.63 trillion on logistics in 2019, moving goods from origin to end user through various supply chain network segments. (netsuite.com)
- (2:04) MTO is a production technique wherein products are customized according to customer specifications, and production only starts after an order is received. (oracle.com)
- In 2021, an estimated 12.1 million Americans work in the manufacturing sector.6 (investopedia.com)
External Links
How To
How to use Lean Manufacturing in the production of goods
Lean manufacturing is a management style that aims to increase efficiency and reduce waste through continuous improvement. It was developed by Taiichi Okono in Japan, during the 1970s & 1980s. TPS founder Kanji Takoda awarded him the Toyota Production System Award (TPS). Michael L. Watkins published the first book on lean manufacturing in 1990.
Lean manufacturing is often described as a set if principles that help improve the quality and speed of products and services. It emphasizes eliminating waste and defects throughout the value stream. Lean manufacturing is called just-in-time (JIT), zero defect, total productive maintenance (TPM), or 5S. Lean manufacturing emphasizes reducing non-value-added activities like inspection, rework and waiting.
Lean manufacturing is a way for companies to achieve their goals faster, improve product quality, and lower costs. Lean manufacturing is considered one of the most effective ways to manage the entire value chain, including suppliers, customers, distributors, retailers, and employees. Many industries worldwide use lean manufacturing. Toyota's philosophy is the foundation of its success in automotives, electronics and appliances, healthcare, chemical engineers, aerospace, paper and food, among other industries.
Lean manufacturing is based on five principles:
-
Define Value - Identify the value your business adds to society and what makes you different from competitors.
-
Reduce Waste - Remove any activity which doesn't add value to your supply chain.
-
Create Flow - Ensure work moves smoothly through the process without interruption.
-
Standardize & Simplify - Make processes as consistent and repeatable as possible.
-
Building Relationships – Establish personal relationships with both external and internal stakeholders.
Lean manufacturing is not a new concept, but it has been gaining popularity over the last few years due to a renewed interest in the economy following the global financial crisis of 2008. To increase their competitiveness, many businesses have turned to lean manufacturing. According to some economists, lean manufacturing could be a significant factor in the economic recovery.
Lean manufacturing is now becoming a common practice in the automotive industry, with many benefits. These include improved customer satisfaction, reduced inventory levels, lower operating costs, increased productivity, and better overall safety.
It can be applied to any aspect of an organisation. This is because it ensures efficiency and effectiveness in all stages of the value chain.
There are three main types:
-
Just-in-Time Manufacturing (JIT): This type of lean manufacturing is commonly referred to as "pull systems." JIT means that components are assembled at the time of use and not manufactured in advance. This approach aims to reduce lead times, increase the availability of parts, and reduce inventory.
-
Zero Defects Manufacturing, (ZDM): ZDM is focused on ensuring that no defective products leave the manufacturing facility. If a part needs to be fixed during the assembly line, it should be repaired rather than scrapped. This applies to finished products, which may need minor repairs before they are shipped.
-
Continuous Improvement (CI),: Continuous improvement aims improve the efficiency and effectiveness of operations by continuously identifying issues and making changes to reduce waste. It involves continuous improvement of processes, people, and tools.