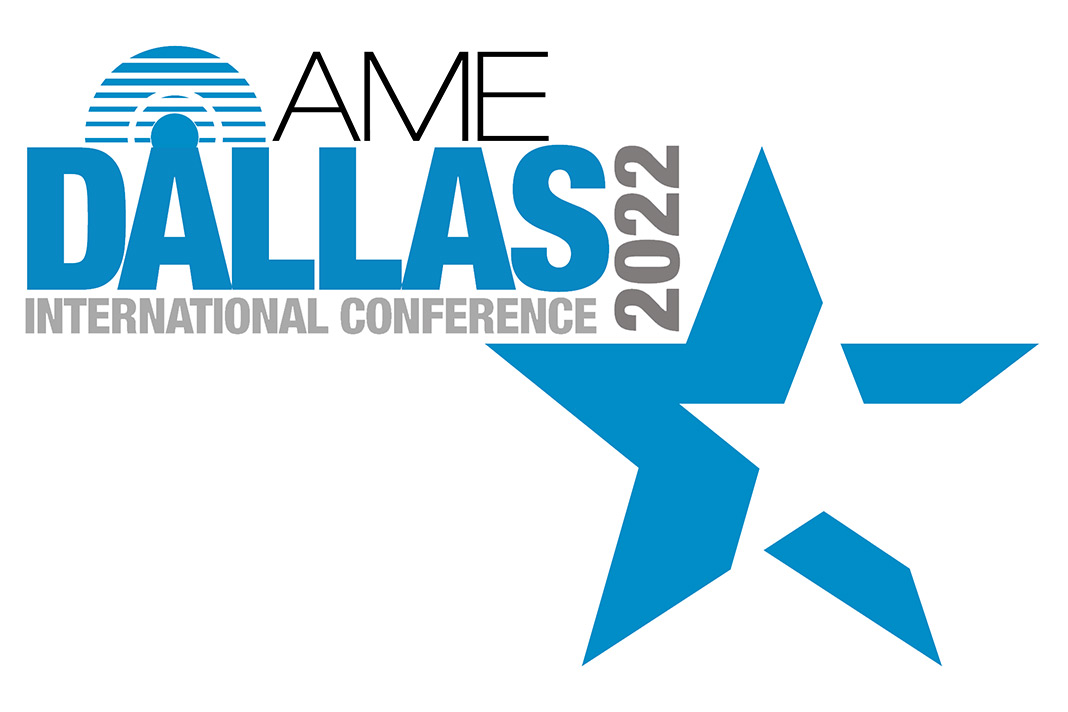
San Diego, whether you're new in the city or just looking to switch careers, is home to some the best logistics jobs nationwide. The jobs available in San Diego range from entry levels to directorships that pay well above $100,000 a yearly.
Logistics jobs are an important part of any company's supply chain. They help move goods from manufacturers to clients. This includes jobs that are involved in inventory management, distribution, warehousing/storage and other duties.
Some of the largest companies in the United States have logistics departments. General Dynamics and BAE Systems are just a few of the companies that have a logistics department.
You can work anywhere in the globe with a career in logistics. The logistics industry offers many career opportunities, especially for those who like organization and structure.
Entry-level logistic jobs are available in many industries and do not require a degree. You might want to get a college degree if your goal is to run a supply chain, or any other department.
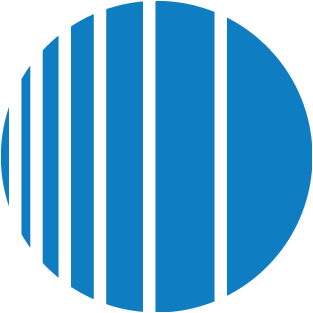
Many logistics jobs are available in San Diego. These positions involve analyzing transport data and using the information to determine which routes are most efficient for products. These jobs will help you to advance your career and build a resume.
Other logistics careers are trucking and shipping. You will be delivering packages or freight to various destinations. You'll need to have a driver's license to qualify for these jobs, and you should be able to pass a background check.
A warehouse manager is another option for anyone interested in a job in logistics. It can be a well-paying position and you can work with large quantities of equipment and inventory.
In San Diego there are many logistics companies that provide various services. These include warehousing, transportation, and more. These companies are a great option to ensure that your supplies arrive at your warehouse in good condition and on time.
Some of the most popular San Diego logistics companies include Omni Logistics, WWEX, and Worldwide Express. These businesses offer a variety freight services including domestic transportation and international shipping.
San Diego companies choose them because of their excellent customer service. They'll go beyond the call of duty to make sure that your shipments reach you on time, and in perfect shape.
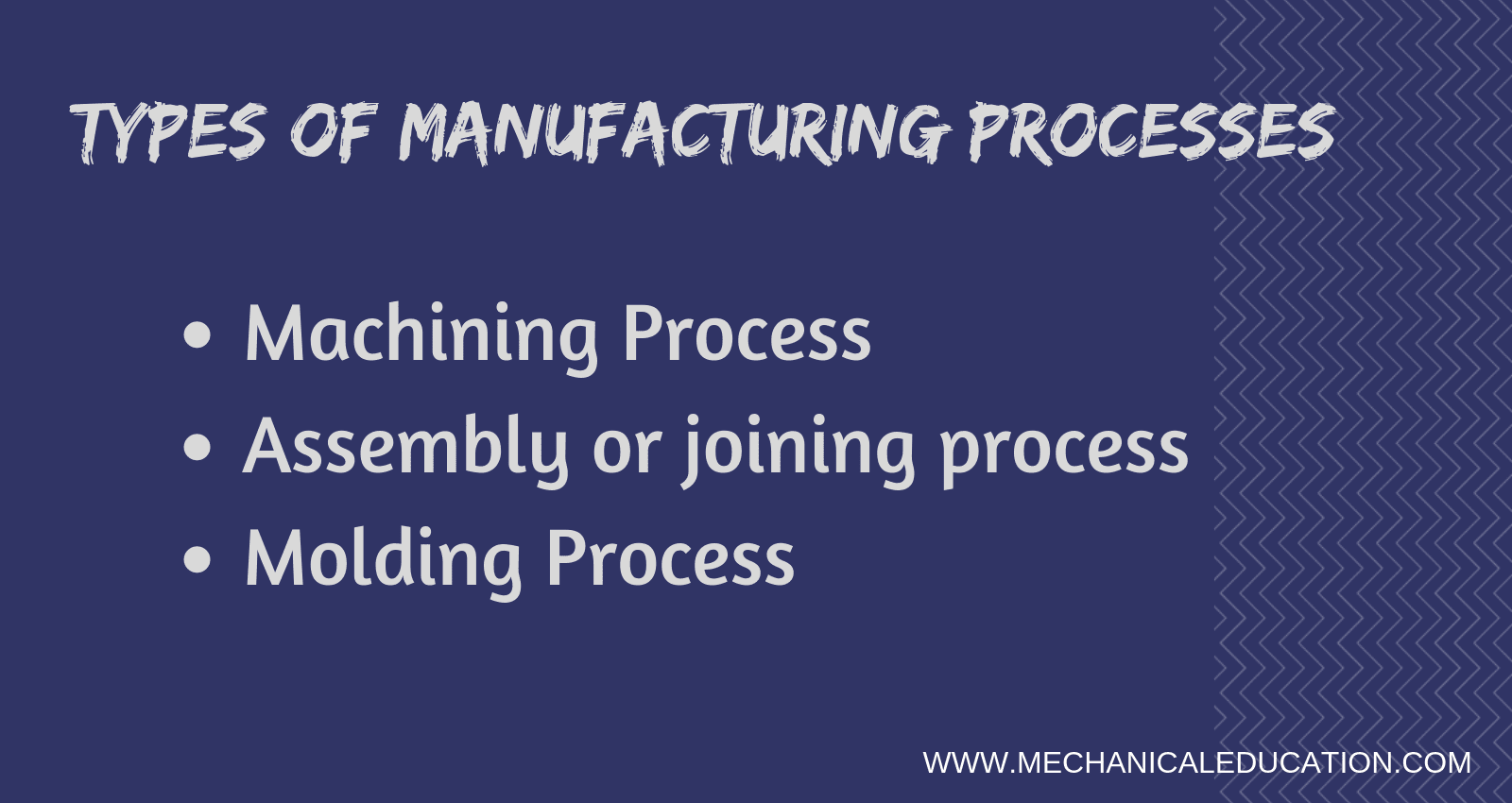
Zion Transport, a freight shipping firm in San Diego, offers a superior service and competitive rates. The company offers shipping and trucking solutions to a wide range of companies, including small startups as well as large corporations.
These services can be difficult to manage and are often a vital part of any company. The services can be both time-consuming as well as costly. That's why it's important to work with a shipping firm that is reliable and can help you cut costs.
Salary Tools allows you to find out how much you will earn in San Diego. These details can help you decide whether this is the career for you.
FAQ
What are the products and services of logistics?
Logistics involves the transportation of goods from point A and point B.
They encompass all aspects transport, including packaging and loading, transporting, storage, unloading.
Logisticians ensure that the product is delivered to the correct place, at the right time, and under safe conditions. They help companies manage their supply chain efficiency by providing information on demand forecasts, stock levels, production schedules, and availability of raw materials.
They monitor shipments in transit, ensure quality standards, manage inventories, replenish orders, coordinate with suppliers and other vendors, and offer support services for sales, marketing, and customer service.
How is a production manager different from a producer planner?
The major difference between a Production Planner and a Project Manager is that a Project Manager is often the person responsible for organizing and planning the entire project. While a Production Planner is involved mainly in the planning stage,
Why is logistics important for manufacturing?
Logistics are an integral part any business. Logistics can help you achieve amazing results by helping to manage product flow from raw materials to finished products.
Logistics play an important role in reducing costs as well as increasing efficiency.
What are the responsibilities for a manufacturing manager
A manufacturing manager has to ensure that all manufacturing processes work efficiently and effectively. They should also be aware of any problems within the company and act accordingly.
They must also be able to communicate with sales and marketing departments.
They should be informed about industry trends and be able make use of this information to improve their productivity and efficiency.
Statistics
- Job #1 is delivering the ordered product according to specifications: color, size, brand, and quantity. (netsuite.com)
- In 2021, an estimated 12.1 million Americans work in the manufacturing sector.6 (investopedia.com)
- According to a Statista study, U.S. businesses spent $1.63 trillion on logistics in 2019, moving goods from origin to end user through various supply chain network segments. (netsuite.com)
- You can multiply the result by 100 to get the total percent of monthly overhead. (investopedia.com)
- [54][55] These are the top 50 countries by the total value of manufacturing output in US dollars for its noted year according to World Bank.[56] (en.wikipedia.org)
External Links
How To
Six Sigma and Manufacturing
Six Sigma can be described as "the use of statistical process control (SPC), techniques to achieve continuous improvement." Motorola's Quality Improvement Department in Tokyo, Japan developed Six Sigma in 1986. The basic idea behind Six Sigma is to improve quality by improving processes through standardization and eliminating defects. This method has been adopted by many companies in recent years as they believe there are no perfect products or services. Six Sigma aims to reduce variation in the production's mean value. You can calculate the percentage of deviation from the norm by taking a sample of your product and comparing it to the average. If it is too large, it means that there are problems.
The first step toward implementing Six Sigma is understanding how variability works in your business. Once you understand this, you can then identify the causes of variation. This will allow you to decide if these variations are random and systematic. Random variations happen when people make errors; systematic variations are caused externally. Random variations would include, for example, the failure of some widgets to fall from the assembly line. You might notice that your widgets always fall apart at the same place every time you put them together.
Once you've identified where the problems lie, you'll want to design solutions to eliminate those problems. This could mean changing your approach or redesigning the entire process. You should then test the changes again after they have been implemented. If they don’t work, you’ll need to go back and rework the plan.