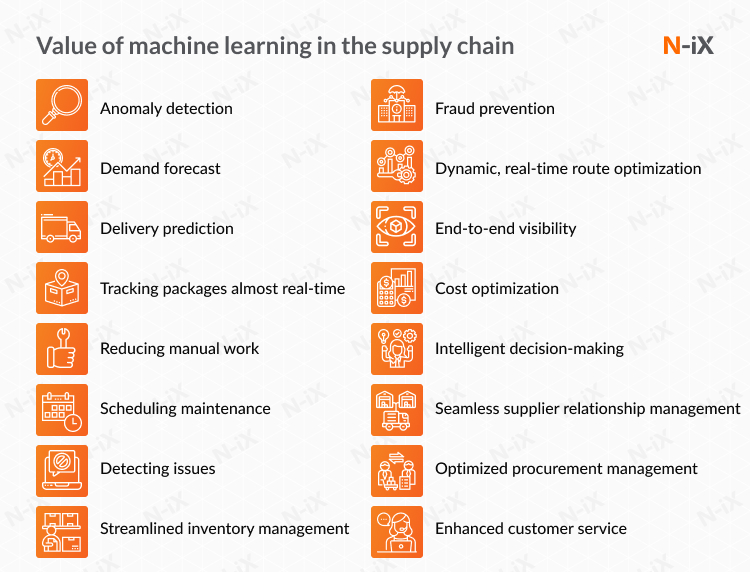
DMAIC, or the DMAIC model, is a process improvement method that includes five steps. Six Sigma professionals commonly use DMAIC to improve the quality of a company. However, it can be used independently as a structured and effective continuous improvement process.
Dmaic, a quality method that reduces defects, costs and rework. It is a proven method to ensure that products are of high quality and are efficient and consistent in performance, thus improving overall customer satisfaction.
DMAIC can be an effective way to resolve issues within a company. It can also be used to improve processes that impact customer satisfaction, quality of products, cost reductions and cycle times. It is a vital part of any program for quality improvement.
The DMAIC is a structured method of problem solving that helps organizations eliminate the root causes behind a particular issue. The DMAIC model is a structured approach to problem-solving that helps an organization eliminate the root causes of a given issue.
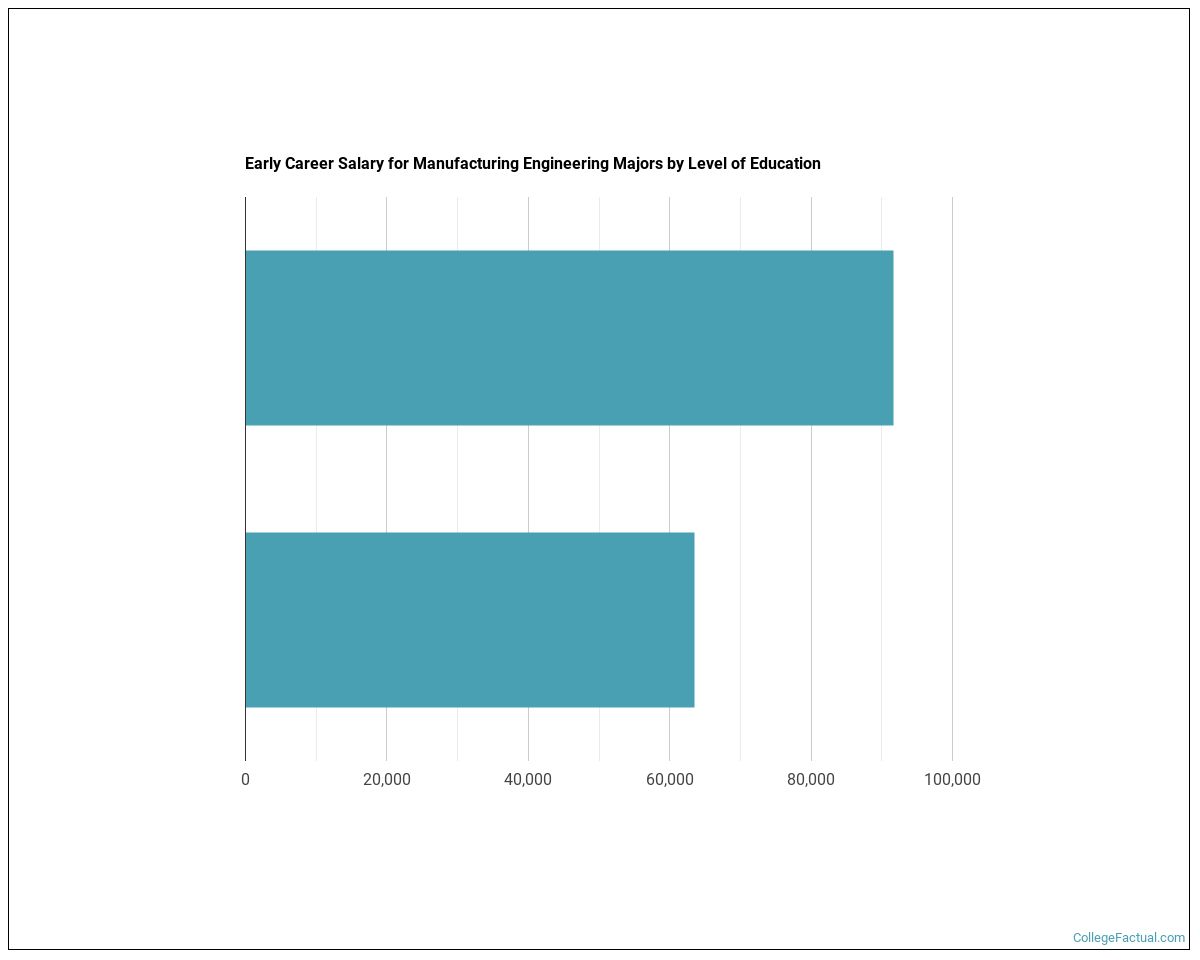
It is a powerful tool in Lean Six Sigma because it gives teams a defined and structured path to follow to find and fix quality problems. This is important, especially for complex problems with unknown causes and the risk of inaction.
Understanding the criteria to be met is essential before choosing a DMAIC. It is also important to know which tools can be used during the process, such as fishbone diagrams and Pareto charts.
When you have chosen a DMAIC-qualified project, you should identify its goals and objectives. The best projects to choose are those that relate to the current status of the business, and also meet the DMAIC requirements.
DMAIC's Define phase involves defining clearly the problem and scope of the improvements. This can either be a formal charter for the project or it can also take a more informal form. It specifies the CTQ (critical-to-quality) issues, as well as the core processes and scope of the project.
This step is crucial in the DMAIC method because it helps teams understand what issues they need to address first, how long they will have to work and which metrics they can use to measure their success. It allows teams to determine their project champions and create the foundation for a successful DMAIC process.
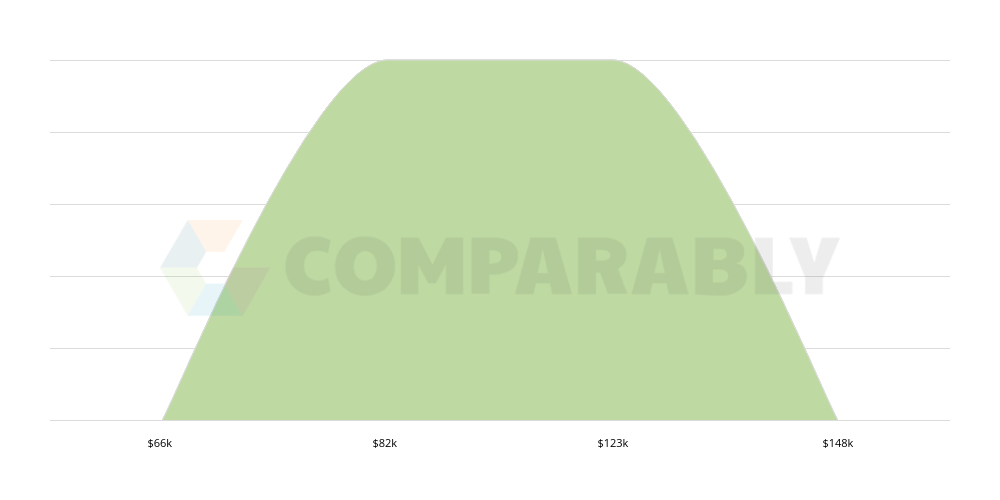
In the Measurement Phase, teams collect current data and compare them to the target state. They then use this information to determine gaps between the two states and identify opportunities for improvement. You can do this by using a number of tools such as scatterplots and frequency plots.
After analyzing the data, teams identify potential solutions to the problem and test them to make sure they are working. They then implement these solutions and verify the results.
FAQ
What does manufacturing industry mean?
Manufacturing Industries are businesses that produce products for sale. The people who buy these products are called consumers. These companies use various processes such as production, distribution, retailing, management, etc., to fulfill this purpose. They produce goods from raw materials by using machines and other machinery. This includes all types manufactured goods such as clothing, building materials, furniture, electronics, tools and machinery.
How can I learn about manufacturing?
Experience is the best way for you to learn about manufacturing. You can also read educational videos or take classes if this isn't possible.
What are manufacturing & logistics?
Manufacturing is the production of goods using raw materials. Logistics covers all aspects involved in managing supply chains, including procurement and production planning. Manufacturing and logistics are often considered together as a broader term that encompasses both the process of creating products and delivering them to customers.
How can manufacturing prevent production bottlenecks?
You can avoid bottlenecks in production by making sure that everything runs smoothly throughout the production cycle, from the moment you receive an order to the moment the product is shipped.
This includes both planning for capacity and quality control.
Continuous improvement techniques like Six Sigma are the best way to achieve this.
Six Sigma is a management system used to improve quality and reduce waste in every aspect of your organization.
It is focused on creating consistency and eliminating variation in your work.
Statistics
- You can multiply the result by 100 to get the total percent of monthly overhead. (investopedia.com)
- In the United States, for example, manufacturing makes up 15% of the economic output. (twi-global.com)
- According to a Statista study, U.S. businesses spent $1.63 trillion on logistics in 2019, moving goods from origin to end user through various supply chain network segments. (netsuite.com)
- Many factories witnessed a 30% increase in output due to the shift to electric motors. (en.wikipedia.org)
- According to the United Nations Industrial Development Organization (UNIDO), China is the top manufacturer worldwide by 2019 output, producing 28.7% of the total global manufacturing output, followed by the United States, Japan, Germany, and India.[52][53] (en.wikipedia.org)
External Links
How To
Six Sigma: How to Use it in Manufacturing
Six Sigma is defined as "the application of statistical process control (SPC) techniques to achieve continuous improvement." Motorola's Quality Improvement Department, Tokyo, Japan, developed it in 1986. Six Sigma's main goal is to improve process quality by standardizing processes and eliminating defects. This method has been adopted by many companies in recent years as they believe there are no perfect products or services. Six Sigma's primary goal is to reduce variation from the average value of production. You can calculate the percentage of deviation from the norm by taking a sample of your product and comparing it to the average. If you notice a large deviation, then it is time to fix it.
Understanding the dynamics of variability within your business is the first step in Six Sigma. Once you've understood that, you'll want to identify sources of variation. It is important to identify whether the variations are random or systemic. Random variations are caused by human errors. Systematic variations can be caused by outside factors. Random variations would include, for example, the failure of some widgets to fall from the assembly line. It would be considered a systematic problem if every widget that you build falls apart at the same location each time.
After identifying the problem areas, you will need to devise solutions. It might mean changing the way you do business or redesigning it entirely. You should then test the changes again after they have been implemented. If they don’t work, you’ll need to go back and rework the plan.