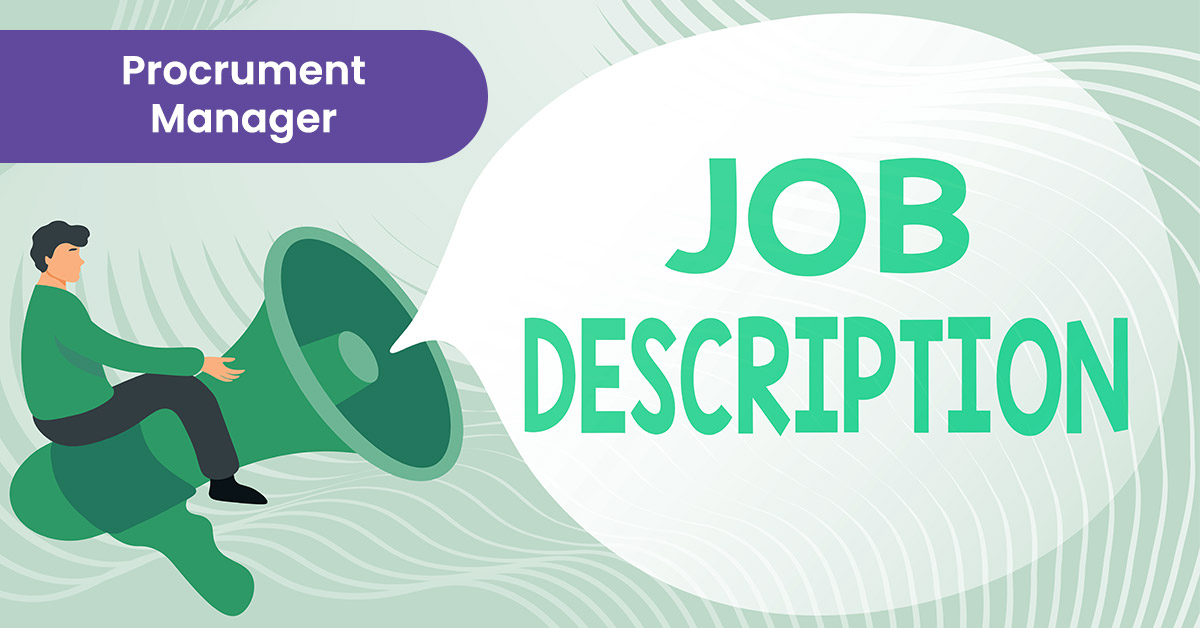
In the United States, chemical manufacturing is a major industry that transforms organic and inorganic raw materials into useful products. It supplies products and materials for industries, ranging from plastics through explosives. There are also many challenges facing the chemical industry. Many workers are at risk for safety and health issues.
Chemical manufacturing is broken down into two main segments: specialty chemicals (common chemicals) and commodity chemicals (spezial chemicals). These two groups share the same infrastructure, utilities, production processes, and other resources. But the products offered by these groups are not identical. Specialty chemicals are usually designed for specific customer uses. Specialty manufacturers produce some of the most costly chemicals. Many of these chemicals are protected by patents.
Some chemicals are manufactured in one location. However, the vast majority of petrochemicals (and commodity chemicals) are produced in large facilities. For example, large-scale chemical plants are located in Texas, Louisiana, and Rotterdam in the Netherlands. Large-scale chemical plant often share utilities and infrastructures, which can lead to economies of size.
The United States is China's second-largest chemical producer. According to Statista, the chemical industry is worth more than $4 trillion annually. About half the industry's revenues are generated by the top 50 US businesses.

Worldwide, the chemical manufacturing industry employs around 20 million workers. The majority of these workers work in large scale facilities. A small number of them are contract or part-time workers. The industry's employment has suffered due to increased competition and technological progress.
The overall U.S. economy drives the demand for chemicals. The chemical industry is highly regulated. The manufacturing process is regulated by the government. Companies are required to practice environmentally sustainable operations. Some chemicals manufacturing raw materials are extremely dangerous to extract.
The industry faces a challenging procurement process. Additionally, raw material costs are very high. Companies are moving their operations to areas with lower overhead in an effort to reduce costs. Finally, some companies merge or shift production to developing nations. This will lead to the loss of jobs.
In 2008, basic chemical manufacturing accounted for 80 percent. This group includes companies that produce pesticides, chemicals, and other materials. Pfizer and Dow are among the top manufacturing companies in this sector. DuPont, Formosa Plastics and Sinopec Group are other major players in this sector.
Large-scale production plants are often clean. Workers are required to wear safety goggles and work in a temperature-controlled environment. Some workers are however replaced by advanced machines that have computerized controls. Most of these workers perform night shifts.
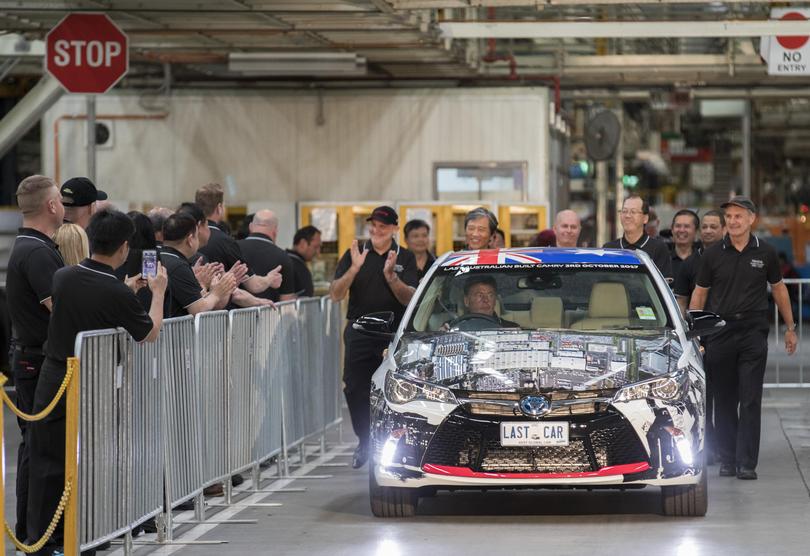
It is possible that chemical manufacturing plants will need to adapt to new production methods. New processes can improve accuracy, and reduce labor costs. Also, the use of nanotechnology will make chemical manufacturing more efficient. Nanotechnology will also help companies conserve energy and reduce waste.
The employment prospects for the chemical manufacturing industry will be affected by increased foreign competition, technological developments, as well as safety and environmental concerns. The industry's overall employment is expected to decline by 13 percent in the next four-years.
FAQ
What jobs are available in logistics?
There are many kinds of jobs available within logistics. Some of them are:
-
Warehouse workers - They load and unload trucks and pallets.
-
Transportation drivers – They drive trucks or trailers to transport goods and perform pick-ups.
-
Freight handlers - They sort and pack freight in warehouses.
-
Inventory managers - These are responsible for overseeing the stock of goods in warehouses.
-
Sales reps - They sell products and services to customers.
-
Logistics coordinators – They plan and coordinate logistics operations.
-
Purchasing agents are those who purchase goods and services for the company.
-
Customer service agents - They answer phone calls and respond to emails.
-
Shipping clerks – They process shipping orders, and issue bills.
-
Order fillers - They fill orders based on what is ordered and shipped.
-
Quality control inspectors - They check incoming and outgoing products for defects.
-
Others – There are many other types available in logistics. They include transport supervisors, cargo specialists and others.
What do you mean by warehouse?
A warehouse, or storage facility, is where goods are stored prior to being sold. It can be an indoor space or an outdoor area. In some cases it could be both indoors and outdoors.
What are the 4 types of manufacturing?
Manufacturing refers to the transformation of raw materials into useful products by using machines and processes. It can involve many activities like designing, manufacturing, testing packaging, shipping, selling and servicing.
How can manufacturing reduce production bottlenecks?
You can avoid bottlenecks in production by making sure that everything runs smoothly throughout the production cycle, from the moment you receive an order to the moment the product is shipped.
This includes both planning for capacity and quality control.
Continuous improvement techniques like Six Sigma are the best way to achieve this.
Six Sigma is a management method that helps to improve quality and reduce waste.
It emphasizes consistency and eliminating variance in your work.
What is the responsibility of a manufacturing manager?
The manufacturing manager should ensure that every manufacturing process is efficient and effective. They should also be aware of any problems within the company and act accordingly.
They should also be able and comfortable communicating with other departments like sales and marketing.
They must also keep up-to-date with the latest trends in their field and be able use this information to improve productivity and efficiency.
What are the 7 Rs of logistics management?
The acronym "7R's" of Logistics stands for seven principles that underpin logistics management. It was developed by the International Association of Business Logisticians (IABL) and published in 2004 as part of its "Seven Principles of Logistics Management" series.
The acronym is made up of the following letters:
-
Responsible - ensure that all actions taken are within legal requirements and are not harmful to others.
-
Reliable - You can have confidence that you will fulfill your promises.
-
It is reasonable to use resources efficiently and not waste them.
-
Realistic – Consider all aspects, including cost-effectiveness as well as environmental impact.
-
Respectful - Treat people fairly and equitably
-
Reliable - Find ways to save money and increase your productivity.
-
Recognizable provides value-added products and services to customers
Statistics
- Many factories witnessed a 30% increase in output due to the shift to electric motors. (en.wikipedia.org)
- In 2021, an estimated 12.1 million Americans work in the manufacturing sector.6 (investopedia.com)
- In the United States, for example, manufacturing makes up 15% of the economic output. (twi-global.com)
- Job #1 is delivering the ordered product according to specifications: color, size, brand, and quantity. (netsuite.com)
- You can multiply the result by 100 to get the total percent of monthly overhead. (investopedia.com)
External Links
How To
How to Use the Just-In-Time Method in Production
Just-intime (JIT), a method used to lower costs and improve efficiency in business processes, is called just-in-time. It allows you to get the right amount resources at the right time. This means you only pay what you use. Frederick Taylor first coined this term while working in the early 1900s as a foreman. He observed how workers were paid overtime if there were delays in their work. He realized that workers should have enough time to complete their jobs before they begin work. This would help increase productivity.
JIT teaches you to plan ahead and prepare everything so you don’t waste time. Look at your entire project, from start to end. Make sure you have enough resources in place to deal with any unexpected problems. You can anticipate problems and have enough equipment and people available to fix them. You won't have to pay more for unnecessary items.
There are many types of JIT methods.
-
Demand-driven JIT: You order the parts and materials you need for your project every other day. This will allow you to track how much material you have left over after using it. It will also allow you to predict how long it takes to produce more.
-
Inventory-based : You can stock the materials you need in advance. This allows you predict the amount you can expect to sell.
-
Project-driven: This method allows you to set aside enough funds for your project. You will be able to purchase the right amount of materials if you know what you need.
-
Resource-based JIT: This is the most popular form of JIT. This is where you assign resources based upon demand. You might assign more people to help with orders if there are many. If there aren't many orders, you will assign fewer people.
-
Cost-based: This is the same as resource-based except that you don't care how many people there are but how much each one of them costs.
-
Price-based pricing: This is similar in concept to cost-based but instead you look at how much each worker costs, it looks at the overall company's price.
-
Material-based: This approach is similar to cost-based. However, instead of looking at the total cost for the company, you look at how much you spend on average on raw materials.
-
Time-based: Another variation of resource-based JIT. Instead of worrying about how much each worker costs, you can focus on how long the project takes.
-
Quality-based JIT: Another variation on resource-based JIT. Instead of thinking about how much each employee costs or how long it takes to manufacture something, you think about how good the quality of your product is.
-
Value-based JIT : This is the newest type of JIT. In this scenario, you're not concerned about how products perform or whether customers expect them to meet their expectations. Instead, you're focused on how much value you add to the market.
-
Stock-based: This stock-based method focuses on the actual quantity of products being made at any given time. This is used to increase production and minimize inventory.
-
Just-intime planning (JIT), is a combination JIT/sales chain management. It is the process that schedules the delivery of components within a short time of their order. It reduces lead times and improves throughput.