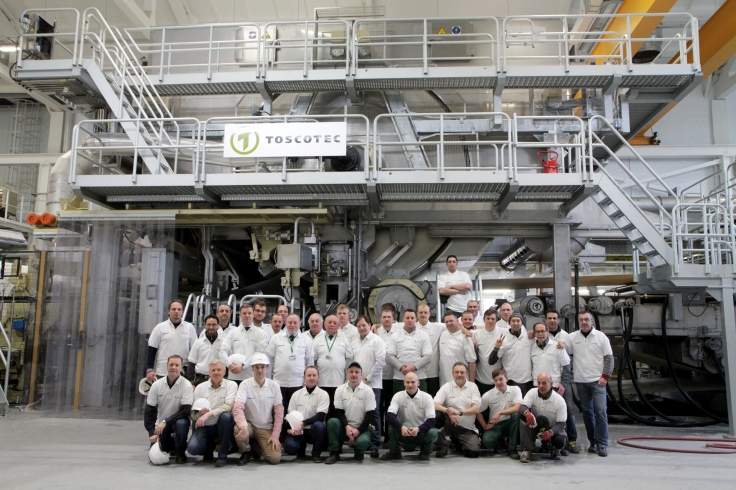
There have been several factors that have led to a severe shortage in chips in recent years. Manufacturing and transport problems are two of the main reasons for the chip shortage. In addition, there have been numerous disasters that have led to the shutdown of some chip plants. This has had a negative impact on consumer devices like gaming consoles, data centers, and healthcare devices. The Chinese government is trying to promote semiconductor manufacturing. The government has even introduced an investment fund to help chip makers.
China's chip manufacturing industry has made great strides over the past few decades as a result. According to IC Insights the growth in chip production in China is expected to be 19.4% by 2025. However, the industry still has a long way to go before it reaches its former levels. Despite all these developments, there are still only a few domestic chip companies. Many of these companies do not yet have their own independent business.
Huawei, Oppo and Midea are some of China's most well-known chip manufacturers. Chinese companies also have a significant market share of the mobile processor sector. They are also creating their own chips, which allows them to increase their chip making capabilities. This has helped them become more competitive in this industry.
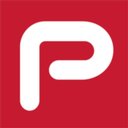
China is developing rapidly as a chip manufacturing hub. However, there are still limitations. Chinese companies lack the resources necessary to mass-produce high-end microchips. These chips are used in smartphones and other wearable devices as well as servers. Additionally, the country cannot yet produce its own raw materials for chip manufacturing. These include enriched and tantalum isotopes, neon, and tantalum. These raw materials can be refined by chemical processes.
The Chinese government is also keen to decrease its dependence upon imported chips. China will produce 70% of its chips in China by 2025, according to the country. But this will take many years. China has 32 registered chip firms, while many others are still waiting to be IPO'd. The government is also actively marketing its industrial policy. The government hopes to encourage more chip production in the country. This is a major challenge considering the resources available.
The US semiconductor sector is currently facing an unprecedented shortage for tech talent. Washington also recently adopted new rules to limit the US's ability to support chip production.
TSMC is one of the most important chipmakers in the world. However, it has not made any announcements yet about a new plant in Europe. It hasn't ruled out the possibility of building an older-generation chip factory there. It has also partnered up with European automakers in order to buy less-advanced chip technology. The idea has been resisted by most European auto companies. Adding a plant in Europe would add to the supply chain, which means chips would have to be shipped back to Asia for back-end processing. This could add several years to the chip's lifespan.
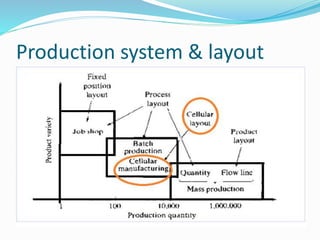
According to the US Commerce Department report, the chip shortage is expected to worsen in 2021. This has resulted to lengthy delays for consumers. The shortage has also affected transportation, healthcare, and gaming consoles. However, the government's investments in reshoring chip production will help create hundreds of thousands of jobs in the US, and ensure a more resilient chip supply chain.
FAQ
What can I do to learn more about manufacturing?
Practical experience is the best way of learning about manufacturing. You can also read educational videos or take classes if this isn't possible.
Why should you automate your warehouse?
Automation has become increasingly important in modern warehousing. E-commerce has brought increased demand for more efficient and quicker delivery times.
Warehouses must adapt quickly to meet changing customer needs. They must invest heavily in technology to do this. Automating warehouses has many benefits. These are some of the benefits that automation can bring to warehouses:
-
Increases throughput/productivity
-
Reduces errors
-
Improves accuracy
-
Safety enhancements
-
Eliminates bottlenecks
-
Companies can scale up more easily
-
Makes workers more efficient
-
Gives you visibility into all that is happening in your warehouse
-
Enhances customer experience
-
Improves employee satisfaction
-
Reduces downtime and improves uptime
-
Ensures quality products are delivered on time
-
Eliminates human error
-
Helps ensure compliance with regulations
What are the 4 types of manufacturing?
Manufacturing refers to the transformation of raw materials into useful products by using machines and processes. It includes many different activities like designing, building and testing, packaging, shipping and selling, as well as servicing.
Statistics
- [54][55] These are the top 50 countries by the total value of manufacturing output in US dollars for its noted year according to World Bank.[56] (en.wikipedia.org)
- You can multiply the result by 100 to get the total percent of monthly overhead. (investopedia.com)
- According to a Statista study, U.S. businesses spent $1.63 trillion on logistics in 2019, moving goods from origin to end user through various supply chain network segments. (netsuite.com)
- It's estimated that 10.8% of the U.S. GDP in 2020 was contributed to manufacturing. (investopedia.com)
- In the United States, for example, manufacturing makes up 15% of the economic output. (twi-global.com)
External Links
How To
How to Use lean manufacturing in the Production of Goods
Lean manufacturing is a management system that aims at increasing efficiency and reducing waste. It was developed by Taiichi Okono in Japan, during the 1970s & 1980s. TPS founder Kanji Takoda awarded him the Toyota Production System Award (TPS). Michael L. Watkins published the book "The Machine That Changed the World", which was the first to be published about lean manufacturing.
Lean manufacturing refers to a set of principles that improve the quality, speed and costs of products and services. It is about eliminating defects and waste from all stages of the value stream. Just-in-time (JIT), zero defect (TPM), and 5S are all examples of lean manufacturing. Lean manufacturing eliminates non-value-added tasks like inspection, rework, waiting.
Lean manufacturing improves product quality and costs. It also helps companies reach their goals quicker and decreases employee turnover. Lean manufacturing can be used to manage all aspects of the value chain. Customers, suppliers, distributors, retailers and employees are all included. Many industries worldwide use lean manufacturing. Toyota's philosophy is a great example of this. It has helped to create success in automobiles as well electronics, appliances and healthcare.
Lean manufacturing includes five basic principles:
-
Define Value - Determine the value that your business brings to society. Also, identify what sets you apart from your competitors.
-
Reduce waste - Stop any activity that isn't adding value to the supply chains.
-
Create Flow - Make sure work runs smoothly without interruptions.
-
Standardize & Simplify - Make processes as consistent and repeatable as possible.
-
Develop Relationships: Establish personal relationships both with internal and external stakeholders.
Although lean manufacturing isn't a new concept in business, it has gained popularity due to renewed interest in the economy after the 2008 global financial crisis. Many businesses are now using lean manufacturing to improve their competitiveness. According to some economists, lean manufacturing could be a significant factor in the economic recovery.
Lean manufacturing is now becoming a common practice in the automotive industry, with many benefits. These include improved customer satisfaction, reduced inventory levels, lower operating costs, increased productivity, and better overall safety.
Lean manufacturing can be applied to almost every aspect of an organization. It is especially useful for the production aspect of an organization, as it ensures that every step in the value chain is efficient and effective.
There are three main types:
-
Just-in-Time Manufacturing (JIT): This type of lean manufacturing is commonly referred to as "pull systems." JIT refers to a system in which components are assembled at the point of use instead of being produced ahead of time. This approach is designed to reduce lead times and increase the availability of components. It also reduces inventory.
-
Zero Defects Manufacturing, (ZDM): ZDM is focused on ensuring that no defective products leave the manufacturing facility. Repairing a part that is damaged during assembly should be done, not scrapping. This is also true for finished products that require minor repairs before shipping.
-
Continuous Improvement (CI): CI aims to improve the efficiency of operations by continuously identifying problems and making changes in order to eliminate or minimize waste. Continuous improvement involves continuous improvement of processes and people as well as tools.