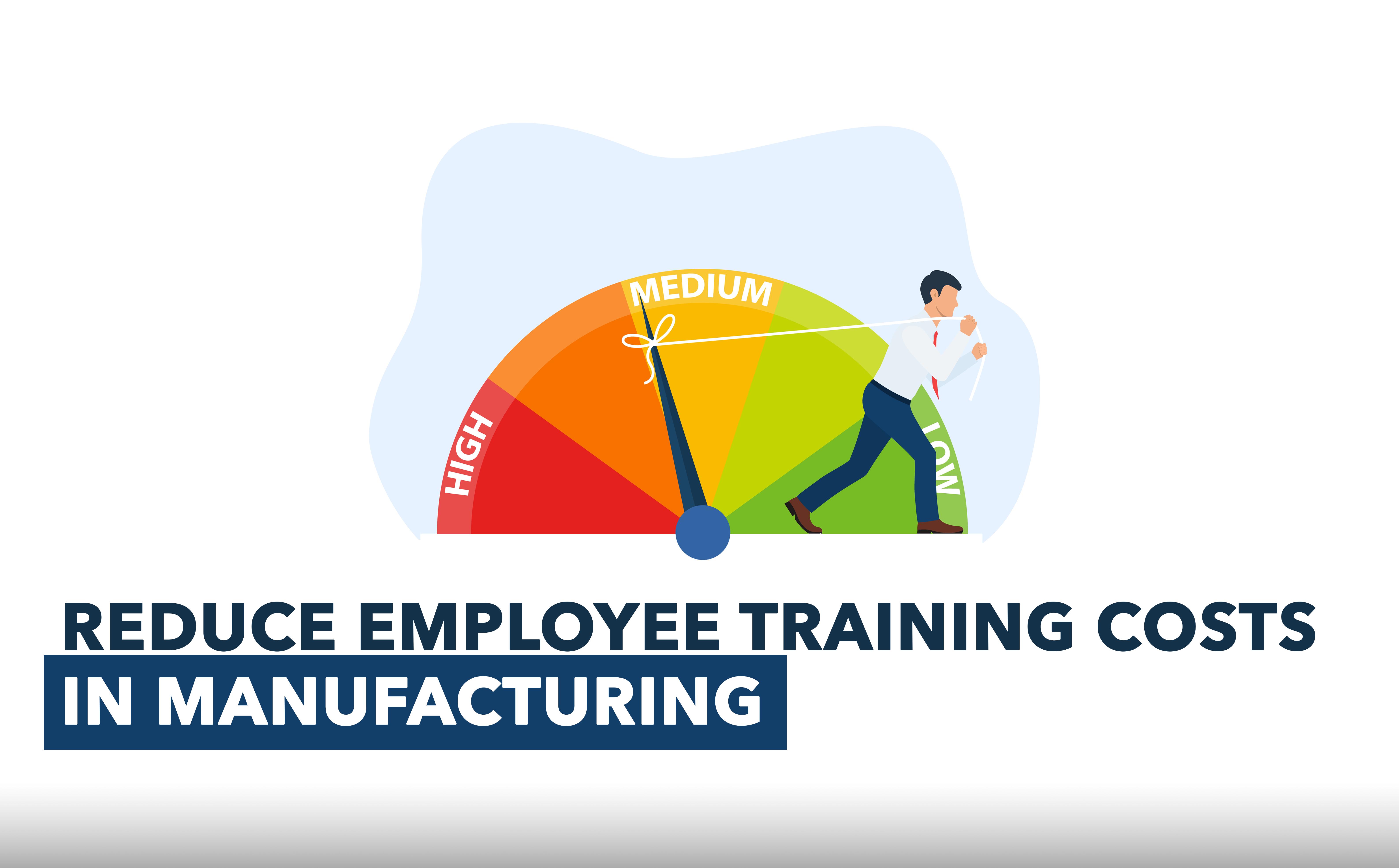
Lean thinking can be used to improve the performance of your organization. It's about eliminating wastes and unvalued tasks from your process. It can also be used to establish a lean culture in your company. A lean cultural is a set if values, principles, or practices that are designed to increase employee morale as well as quality and productivity. It creates a more sustainable environment for employees.
The first step in implementing lean thinking is to identify value for your customer. This includes understanding the entire value-chain and the needs your customers. Once you have this information, you can then identify the steps in your current processes. By identifying the steps within different processes, you can determine if your current process is inefficient. To see how your business is operating, you can also use value streaming mapping. The value stream map depicts the flow of your business and how it works. It also shows the value created by each step.
Lean thinking is all about flow. It is the ability of switching quickly between activities. This is critical when responding rapidly to customer demand. It also reduces the need for inventory and backlogs. It also makes it possible for workers to quickly switch jobs.
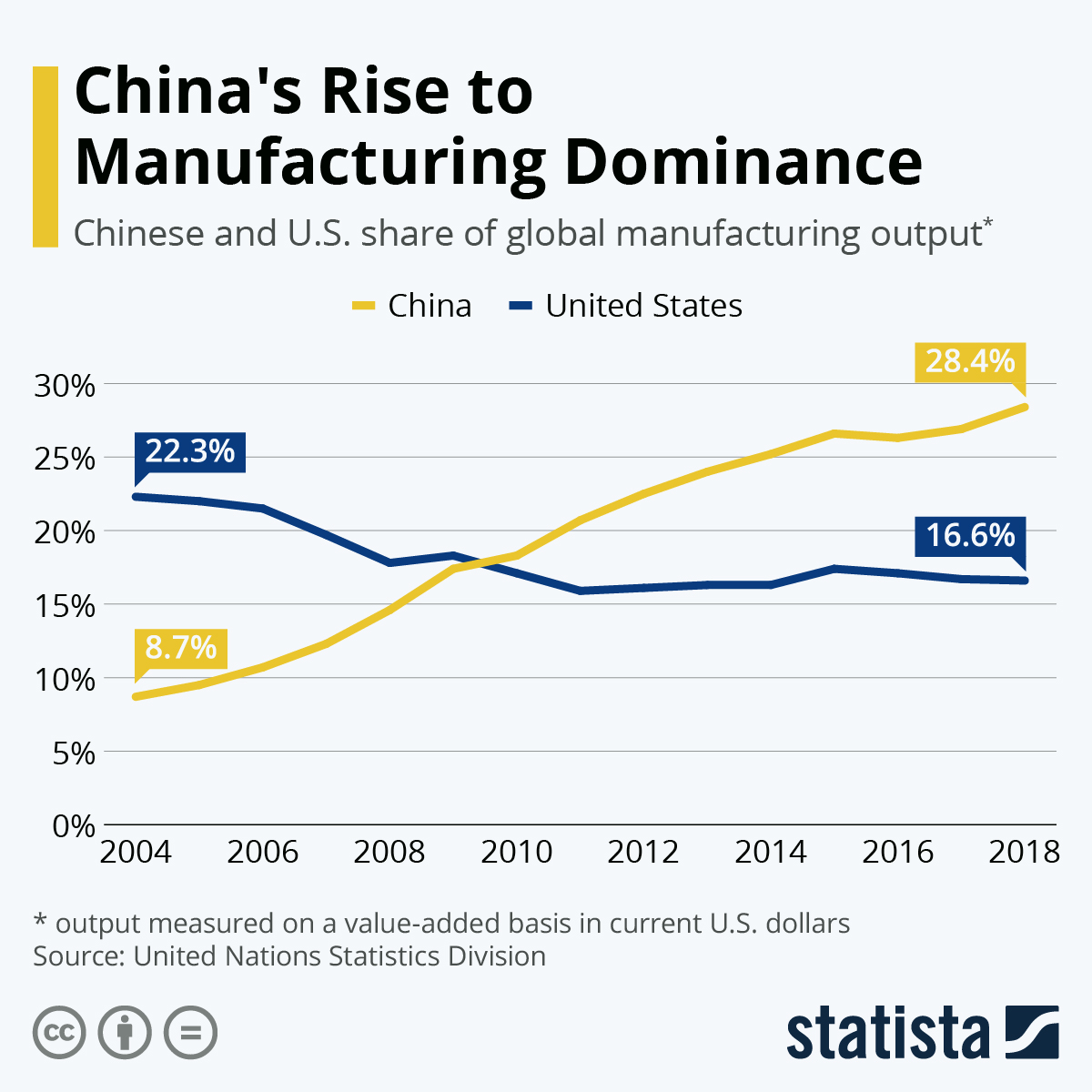
Lean organizations employ a collaborative approach to managing output. They also encourage clear communication and collaboration. They encourage quality assurance, and celebrate the successes. They also reduce unnecessary over-costs to suppliers or customers.
Lean thinking is a continuous process. It can be applied to any type or work. It can help to reduce environmental damage, reduce the waste, and improve employee motivation. Lean thinking is often applied to manufacturing companies, but it can be used in any area of business.
In order to implement lean production methods, it is important to create a culture that promotes lean thinking. The culture must be defined clearly and include constant improvement, employee motivation, and a clear definition about value. It also must be willing to take small steps forward on a regular basis. This is called kaizen.
Lean thinking is a continuous improvement process that requires a kaizen spirit. To improve the quality of your product you have to be open to small improvements each day. You can do this by making changes in the company or using standardized work. Standardized work is a visual representation of the flow of work. It is easy to find everything. It also allows people to see how obstacles can be overcome to make their work smoother.
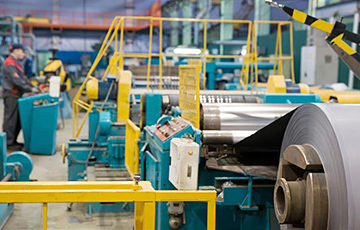
It is also important to consider other production metrics when implementing lean production practices. This ratio shows how often an item is available for production. It also shows how often planned maintenance is required. The ratio of quality materials is an indicator of how well a supplier delivers high-quality products.
The "Just-In Time" principle has risks. This principle ensures supplies are delivered on time. It helps focus and concentrate the mind to the task at hand. However, it can lead to problems in the industry.
FAQ
What types of jobs can you find in logistics
There are different kinds of jobs available in logistics. Some of them are:
-
Warehouse workers - They load and unload trucks and pallets.
-
Transportation drivers – They drive trucks or trailers to transport goods and perform pick-ups.
-
Freight handlers – They sort and package freight at warehouses.
-
Inventory managers: They are responsible for the inventory and management of warehouses.
-
Sales representatives: They sell products to customers.
-
Logistics coordinators - They plan and organize logistics operations.
-
Purchasing agents – They buy goods or services necessary to run a company.
-
Customer service agents - They answer phone calls and respond to emails.
-
Shipping clerks: They process shipping requests and issue bills.
-
Order fillers – They fill orders based upon what was ordered and shipped.
-
Quality control inspectors (QCI) - They inspect all incoming and departing products for potential defects.
-
Others - There are many types of jobs in logistics such as transport supervisors and cargo specialists.
What skills is required for a production planner?
To become a successful production planner, you need to be organized, flexible, and able to multitask. Communication skills are essential to ensure that you can communicate effectively with clients, colleagues, and customers.
What are the 7 Rs of logistics management?
The acronym 7Rs of Logistics refers to the seven core principles of logistics management. It was published in 2004 by the International Association of Business Logisticians as part of their "Seven Principles of Logistics Management" series.
The acronym is composed of the following letters.
-
Responsible - ensure that actions are in compliance with legal requirements and do not cause harm to others.
-
Reliable - You can have confidence that you will fulfill your promises.
-
Be responsible - Use resources efficiently and avoid wasting them.
-
Realistic – Consider all aspects, including cost-effectiveness as well as environmental impact.
-
Respectful - show respect and treat others fairly and fairly
-
Reliable - Find ways to save money and increase your productivity.
-
Recognizable is a company that provides customers with value-added solutions.
Statistics
- According to a Statista study, U.S. businesses spent $1.63 trillion on logistics in 2019, moving goods from origin to end user through various supply chain network segments. (netsuite.com)
- You can multiply the result by 100 to get the total percent of monthly overhead. (investopedia.com)
- According to the United Nations Industrial Development Organization (UNIDO), China is the top manufacturer worldwide by 2019 output, producing 28.7% of the total global manufacturing output, followed by the United States, Japan, Germany, and India.[52][53] (en.wikipedia.org)
- Job #1 is delivering the ordered product according to specifications: color, size, brand, and quantity. (netsuite.com)
- It's estimated that 10.8% of the U.S. GDP in 2020 was contributed to manufacturing. (investopedia.com)
External Links
How To
How to Use 5S for Increasing Productivity in Manufacturing
5S stands for "Sort", "Set In Order", "Standardize", "Separate" and "Store". Toyota Motor Corporation created the 5S methodology in 1954. It allows companies to improve their work environment, thereby achieving greater efficiency.
The idea behind standardizing production processes is to make them repeatable and measurable. This means that every day tasks such cleaning, sorting/storing, packing, and labeling can be performed. Through these actions, workers can perform their jobs more efficiently because they know what to expect from them.
There are five steps to implementing 5S, including Sort, Set In Order, Standardize, Separate and Store. Each step requires a different action, which increases efficiency. You can make it easy for people to find things later by sorting them. Once you have placed items in an ordered fashion, you will put them together. After you have divided your inventory into groups you can store them in easy-to-reach containers. You can also label your containers to ensure everything is properly labeled.
This process requires employees to think critically about how they do their job. Employees need to understand the reasons they do certain jobs and determine if there is a better way. They must learn new skills and techniques in order to implement the 5S system.
The 5S Method not only improves efficiency, but it also helps employees to be more productive and happier. They feel more motivated to work towards achieving greater efficiency as they see the results.