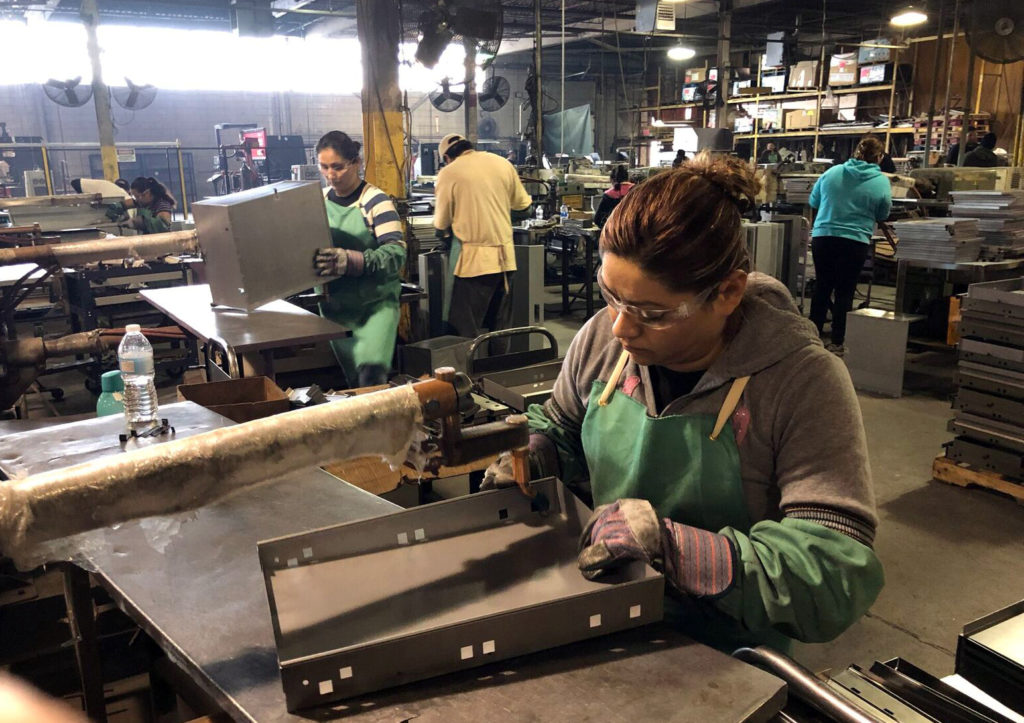
A chemical engineer can be described as a person who has knowledge in the fields of engineering and chemistry. These engineers design and operate processes and equipment that convert raw materials into products. They manage all aspects of production, from the design and operation of equipment to the layouts. A chemical engineering degree is rewarding and lucrative, regardless of your field of interest. Here are some career options within the field of chemical engineering. These professionals are an asset to any industry in which they work, including pharmaceuticals and food.
Aerospace engineering may be the most difficult major.
The aerospace engineering major requires intense discipline. This major doesn't allow for college party culture. You will be expected to spend hours learning and doing course-related work. This subject is also known as rocket science. Aerospace engineering is the design, construction and research of spacecraft and air. It also includes the overlapping branches of astronautical engineering as well as aeronautical. Students will be required to learn heavy mathematics and fluid dynamics.
The easiest major is chemical engineering
To be interested in chemical engineers, your first step should be to obtain a high-grade point average (GPA), in highschool. Colleges expect majors in chemical engineering to do rigorous coursework in highschool. Taking AP courses can help you impress admissions officers. AP classes are a great way to build academic skills. Chemical engineers can expect a well-paying job with an average salary of $96,300 by 2020.
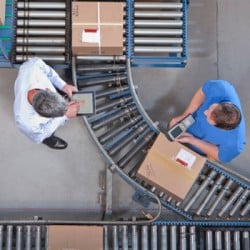
It requires math and physics.
Most undergraduate degree programs in chemical engineering involve 120 to 130 credits and are four years long. Students will learn to create, manufacture, analyze, and process chemical products and equipment. Chemical engineering students take classes in math, physics and chemistry. Students also participate in internships or cooperative learning. Some programs offer doctoral degrees. At least a bachelor's level in chemical engineering is necessary to get a PhD.
It's a safe field
Chemical engineering has many jobs. While most chemical engineers work in an office or laboratory, many spend their time on the site where they oversee operations and solve any problems. While they are able to work long hours to meet deadlines but may also be on-call at certain times, chemical engineers can also be expected to work on weekends. This field requires an in-depth knowledge of many complex topics. To design the best process, a chemical engineer might use computer aided design software.
It pays well
You have many options if you are a recent college grad looking for an entry-level position. If you don't see a position, you can search for internships. ExxonMobil may have positions open at their company. You can find jobs in engineering, finance and operations. You can also concentrate on your areas of expertise, such a geophysics, operations, or information tech.
It is a recent topic.
Chemical engineering is both fascinating and challenging. You will discover many uses of chemical engineering as a student. You will learn how to design and build industrial processes with complex operations. You will study unit operations in chemical plants and the implications of changing the variables in a process. Throughout the history of chemical engineering, innovative approaches have been implemented to improve student understanding and participation.
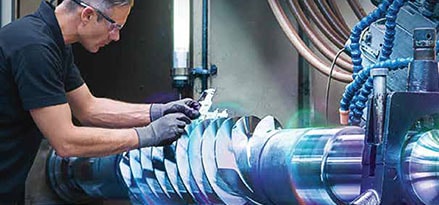
It's a great choice for students who wish to work in the field.
Chemical engineering is a great choice if you're interested in a career within the chemical industry. This field can be combined with other disciplines such electrical engineering to provide specialist knowledge. Chemical engineers have the ability to identify and solve problems in chemical manufacturing, use, transportation and distribution. Today, chemicals are used to produce fuel, drugs, or food. Depending on your interests and expertise, you may choose to concentrate on particular sub-groups of the field such as biotechnology or environmental.
FAQ
What are the requirements to start a logistics business?
You need to have a lot of knowledge and skills to manage a successful logistic business. To communicate effectively with clients and suppliers, you must be able to communicate well. You should be able analyse data and draw inferences. You need to be able work under pressure and manage stressful situations. To increase efficiency and creativity, you need to be creative. Strong leadership qualities are essential to motivate your team and help them achieve their organizational goals.
It is also important to be efficient and well organized in order meet deadlines.
What are the responsibilities for a manufacturing manager
A manufacturing manager has to ensure that all manufacturing processes work efficiently and effectively. They should be aware of any issues within the company and respond accordingly.
They should also be able communicate with other departments, such as sales or marketing.
They must also keep up-to-date with the latest trends in their field and be able use this information to improve productivity and efficiency.
What makes a production planner different from a project manger?
The primary difference between a producer planner and a manager of a project is that the manager usually plans and organizes the whole project, while a production planner is only involved in the planning stage.
What does manufacturing mean?
Manufacturing Industries are companies that manufacture products. Consumers are those who purchase these products. To accomplish this goal, these companies employ a range of processes including distribution, sales, management, and production. They make goods from raw materials with machines and other equipment. This covers all types of manufactured goods including clothing, food, building supplies and furniture, as well as electronics, tools, machinery, vehicles and pharmaceuticals.
What does warehouse mean?
A warehouse is an area where goods are stored before being sold. You can have it indoors or outdoors. Sometimes, it can be both an indoor and outdoor space.
Why is logistics important for manufacturing?
Logistics are an essential part of any business. Logistics can help you achieve amazing results by helping to manage product flow from raw materials to finished products.
Logistics also play a major role in reducing costs and increasing efficiency.
What skills do production planners need?
To become a successful production planner, you need to be organized, flexible, and able to multitask. It is also important to be able communicate with colleagues and clients.
Statistics
- Many factories witnessed a 30% increase in output due to the shift to electric motors. (en.wikipedia.org)
- Job #1 is delivering the ordered product according to specifications: color, size, brand, and quantity. (netsuite.com)
- It's estimated that 10.8% of the U.S. GDP in 2020 was contributed to manufacturing. (investopedia.com)
- In 2021, an estimated 12.1 million Americans work in the manufacturing sector.6 (investopedia.com)
- In the United States, for example, manufacturing makes up 15% of the economic output. (twi-global.com)
External Links
How To
How to Use 5S to Increase Productivity in Manufacturing
5S stands for "Sort", 'Set In Order", 'Standardize', & Separate>. The 5S methodology was developed at Toyota Motor Corporation in 1954. This methodology helps companies improve their work environment to increase efficiency.
The idea behind standardizing production processes is to make them repeatable and measurable. This means that daily tasks such as cleaning and sorting, storage, packing, labeling, and packaging are possible. These actions allow workers to perform their job more efficiently, knowing what to expect.
Implementing 5S involves five steps: Sort, Set in Order, Standardize Separate, Store, and Each step requires a different action, which increases efficiency. If you sort items, it makes them easier to find later. You arrange items by placing them in an order. Then, after you separate your inventory into groups, you store those groups in containers that are easy to access. Make sure everything is correctly labeled when you label your containers.
This requires employees to critically evaluate how they work. Employees must understand why they do certain tasks and decide if there's another way to accomplish them without relying on the old ways of doing things. To be successful in the 5S system, employees will need to acquire new skills and techniques.
The 5S method not only increases efficiency but also boosts morale and teamwork. As they begin to see improvements, they feel motivated to continue working towards the goal of achieving higher levels of efficiency.