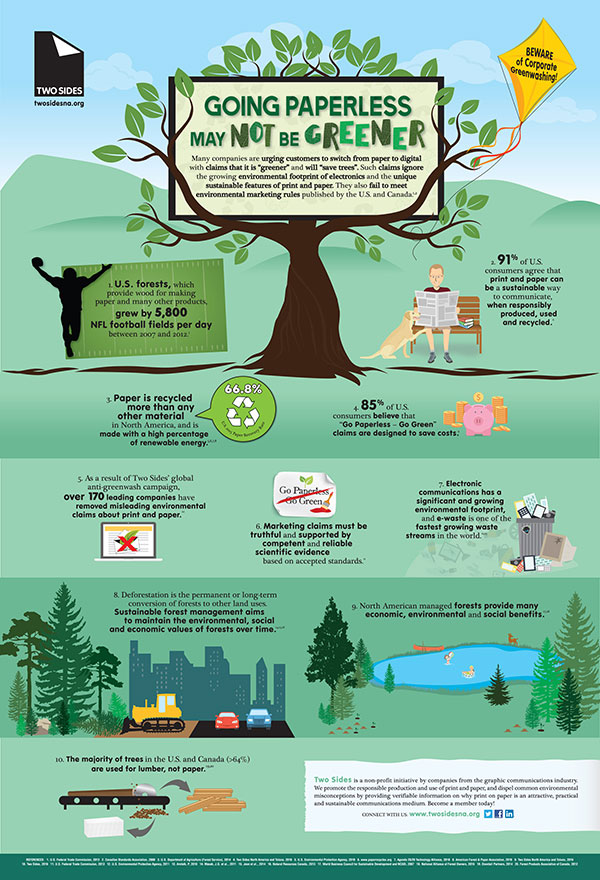
Amazon is seeking Supply Chain Managements with proven track records and senior leadership experience to oversee strategic cross-functional operations. These positions will be responsible for overseeing projects that support new products or operations and working closely with business teams across the globe. They will lead large-scale, cross-functional projects in multiple companies and create cross-functional team members.
Purchasing and supply chain manager
An Amazon Purchasing and supply chain manager has a variety of duties and responsibilities, including driving cost savings, optimizing processes, mitigating risk, and establishing consistent service offerings across the globe. These duties require strong negotiation and analytical skills.
The ideal candidate is self-motivated, with strong communication skills, and attention to details. The ideal candidate should be able and able to work independently, meet deadlines, and manage her own workload.
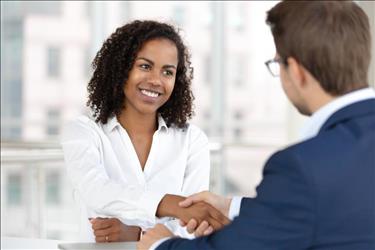
Cost analyst
Amazon's supply chain is an integral part of the company's success. It covers fulfillment, transportation, as well forecasting. This job requires an analytical person who is passionate about details. The person will use data analysis to help understand the company's operation. The analyst will work with global stakeholders, interpreting data and drawing conclusions. For their analysis they might use MS Excel or SQL.
The Amazon supply chain is one of the most innovative in the world. Amazon invests in warehouse technology, trucking capabilities and many other areas. Amazon is also investing heavily into drones and cargo planes.
Program manager
Amazon program manager supply chain jobs require extensive knowledge in areas such as supply chain planning, manufacturing and logistics. A successful candidate will also be able integrate within a team and make data-driven decision. The successful candidate will also need to develop and maintain systems and processes for scale and quality control as well as risk management.
The salary of a Supply Chain Program Management Manager will vary depending on the place where they are located. Some earn over $168,000 a year, while others earn as little as $52,500. On average, Program managers earn between $87,500 and $127,500 annually. However, salaries can vary by nearly $40,000 depending on the region in which they work and the amount of experience they have.
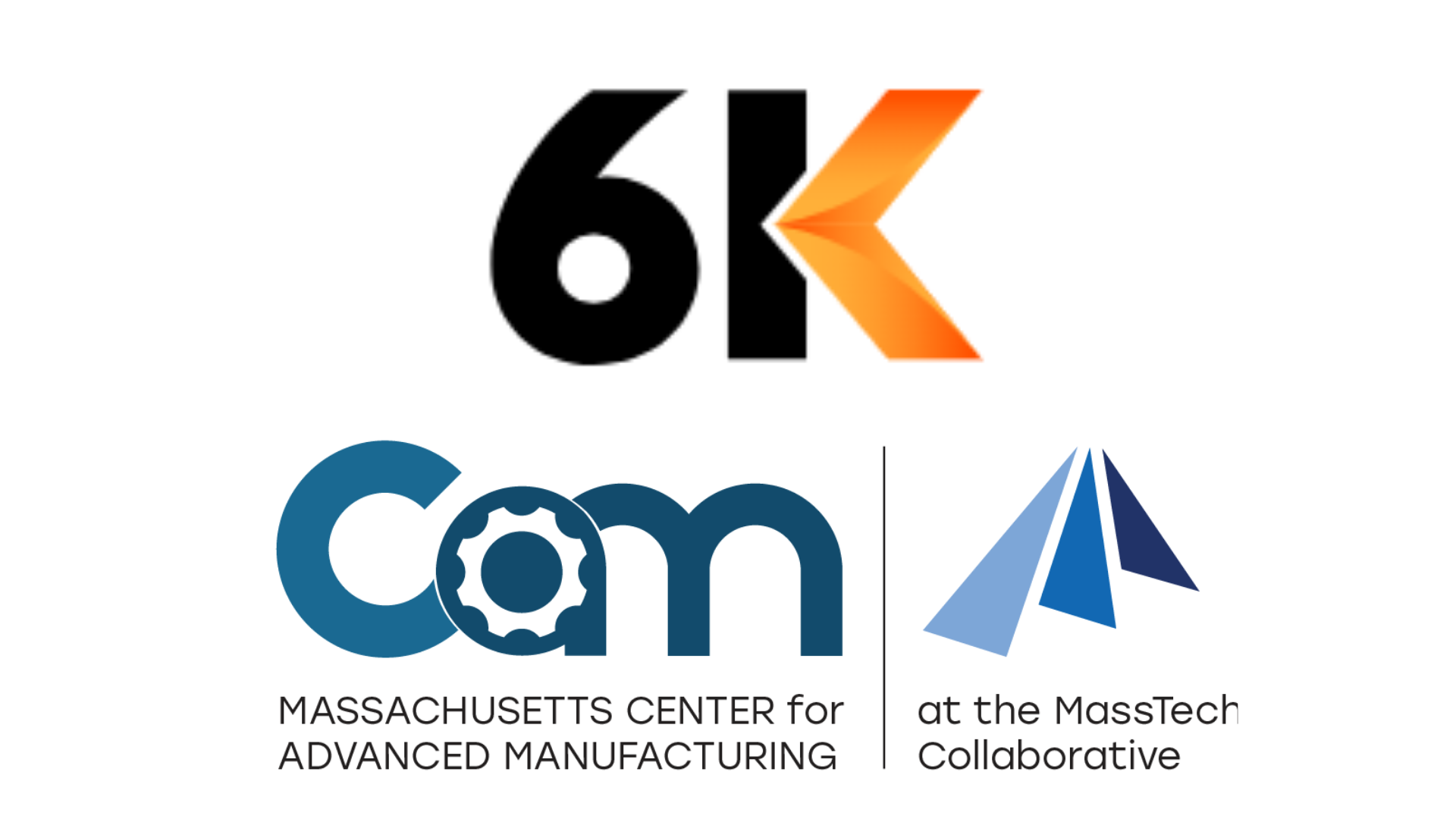
Warehouse manager
Warehouse management jobs are highly sought-after, and the demand for them is growing. Although there are no requirements for warehouse managers, most employers prefer employees with experience. However, a bachelor's is an advantage for this job.
Warehouse managers have a broad range of tasks to perform, including inventory management and customer service. These managers also have an important impact on the experience and performance of operators as well as shippers. These people are responsible for ensuring the success of the entire supply chain. They also develop efficiency-enhancing initiatives. In addition, they have a chance to work with multiple teams within Amazon and get broad exposure to their operations.
FAQ
What does the term manufacturing industries mean?
Manufacturing Industries refers to businesses that manufacture products. These products are sold to consumers. These companies use various processes such as production, distribution, retailing, management, etc., to fulfill this purpose. They make goods from raw materials with machines and other equipment. This includes all types manufactured goods such as clothing, building materials, furniture, electronics, tools and machinery.
What skills is required for a production planner?
Being a production planner is not easy. You need to be organized and flexible. Effective communication with clients and colleagues is essential.
What is the responsibility of a production planner?
Production planners make sure that every aspect of the project is delivered on-time, within budget, and within schedule. They also ensure the quality of the product and service meets the client's requirements.
What is production planning?
Production Planning includes planning for all aspects related to production. This document ensures that everything is prepared and available when you are ready for shooting. You should also have information to ensure the best possible results on set. This includes shooting schedules, locations, cast lists, crew details, and equipment requirements.
The first step is to decide what you want. You may have already decided where you would like to shoot, or maybe there are specific locations or sets that you want to use. Once you have identified the scenes and locations, you can start to determine which elements are required for each scene. One example is if you are unsure of the exact model you want but decide that you require a car. To narrow your options, you can search online for available models.
After you have chosen the right car, you will be able to begin thinking about accessories. Do you have people who need to be seated in the front seat? Or perhaps you need someone walking around the back of the car? Maybe you want to change the interior color from black to white? These questions can help you decide the right look for your car. You can also think about the type of shots you want to get. Are you going to be shooting close-ups? Or wide angles? Maybe you want the engine or the steering wheels to be shown. These details will help identify the exact car you wish to film.
Once you have made all the necessary decisions, you can start to create a schedule. You can create a schedule that will outline when you must start and finish your shoots. You will need to know when you have to be there, what time you have to leave and when your return home. So everyone is clear about what they need to do. If you need to hire extra staff, you can make sure you book them in advance. It's not worth paying someone to show up if you haven't told him.
Your schedule will also have to be adjusted to reflect the number of days required to film. Some projects may only take a couple of days, while others could last for weeks. When creating your schedule, be aware of whether you need more shots per day. Shooting multiple takes over the same location will increase costs and take longer to complete. You can't be certain if you will need multiple takes so it is better not to shoot too many.
Budgeting is another crucial aspect of production plan. You will be able to manage your resources if you have a realistic budget. It is possible to reduce the budget at any time if you experience unexpected problems. However, it is important not to overestimate the amount that you will spend. If you underestimate how much something costs, you'll have less money to pay for other items.
Production planning is a detailed process. But, once you understand the workings of everything, it becomes easier for future projects to be planned.
What's the difference between Production Planning & Scheduling?
Production Planning (PP) is the process of determining what needs to be produced at any given point in time. Forecasting demand is one way to do this.
Scheduling involves the assignment of dates and times to tasks in order to complete them within the timeframe.
What is the job of a manufacturer manager?
A manufacturing manager has to ensure that all manufacturing processes work efficiently and effectively. They must also be alert to any potential problems and take appropriate action.
They should also be able and comfortable communicating with other departments like sales and marketing.
They should be informed about industry trends and be able make use of this information to improve their productivity and efficiency.
Statistics
- According to the United Nations Industrial Development Organization (UNIDO), China is the top manufacturer worldwide by 2019 output, producing 28.7% of the total global manufacturing output, followed by the United States, Japan, Germany, and India.[52][53] (en.wikipedia.org)
- In the United States, for example, manufacturing makes up 15% of the economic output. (twi-global.com)
- (2:04) MTO is a production technique wherein products are customized according to customer specifications, and production only starts after an order is received. (oracle.com)
- Many factories witnessed a 30% increase in output due to the shift to electric motors. (en.wikipedia.org)
- According to a Statista study, U.S. businesses spent $1.63 trillion on logistics in 2019, moving goods from origin to end user through various supply chain network segments. (netsuite.com)
External Links
How To
Six Sigma and Manufacturing
Six Sigma can be described as "the use of statistical process control (SPC), techniques to achieve continuous improvement." Motorola's Quality Improvement Department in Tokyo, Japan developed Six Sigma in 1986. Six Sigma's main goal is to improve process quality by standardizing processes and eliminating defects. Many companies have adopted Six Sigma in recent years because they believe that there are no perfect products and services. Six Sigma seeks to reduce variation between the mean production value. You can calculate the percentage of deviation from the norm by taking a sample of your product and comparing it to the average. If it is too large, it means that there are problems.
Understanding the nature of variability in your business is the first step to Six Sigma. Once you understand this, you can then identify the causes of variation. This will allow you to decide if these variations are random and systematic. Random variations are caused by human errors. Systematic variations can be caused by outside factors. If you make widgets and some of them end up on the assembly line, then those are considered random variations. If however, you notice that each time you assemble a widget it falls apart in exactly the same spot, that is a problem.
After identifying the problem areas, you will need to devise solutions. That solution might involve changing the way you do things or redesigning the process altogether. You should then test the changes again after they have been implemented. If they didn't work, then you'll need to go back to the drawing board and come up with another plan.