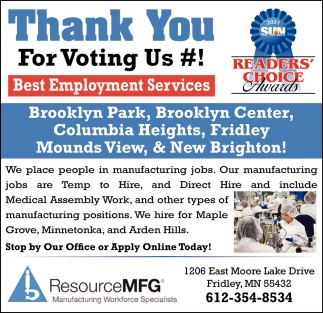
The largest steel companies in usa have been an integral part of the United States' economic development. The steel companies are responsible for providing metals used in vehicles, construction, homes and industrial plants. These companies provide a variety specialized metal fabrications services including cutting and bending, stamping and welding.
Steel companies in the USA: The biggest steel producers
Steel industry size is affected by many factors. These include raw materials prices, availability of raw materials and the number of smelting facilities and casting plants. The top five US-based steel companies produce a total of over 87 million tons of steel annually.
Nucor is the biggest US steelmaker in terms of exports to other countries. In Q3 of 2019, it shipped 3.6 millions tons of steel, down from 3.9million tons in the same period last year.
The company has many operations including smelting steel, manufacturing, mining and oil. The company also holds a majority share in a coal fired power plant.
Commercial Metals (CMC) is the third-largest steelmaker based on steel shipments, with 2.1 million tons of steel shipped in Q4 2018. It is a vertically integred company that also manufactures stainless, aluminum, and expandable metal in various thicknesses, sizes, and alloys.
The company has invested heavily in its iron-ore mines within the Great Lakes region. It is also expanding its flat-rolling capacity at its Baytown plate and pipe plant in Texas. It also plans a second phase of expansion at its Ohio Flat-Roll mill.
It is a diversified steelmaker with major operations in Europe, the United States, and Asia. It is also a major producer of specialty and high-performance steels, including advanced corrosion-resistant and non-corrosive grades.
ArcelorMittal is another major player in the global steel industry. It produces over half the world's total steel. It operates plants in the United States, Canada, Brazil, and Europe and serves markets around the globe. Its global reach is a major competitive advantage for the company in a highly-competitive market.
It is also worth mentioning that China has grown to be the largest producer of steel in the world, with more than two thirds of all the supply on the planet. This country also has a rich history of steel production innovation.
While cyclical, the industry is still crucial for the development of the US economy. There is a need for massive construction projects to replace the aging infrastructure. New buildings, roads and bridges are also in high demand.
A key driver of the steel market in the US is the federal government's $1.2 trillion infrastructure spending bill passed in 2021. This is the largest construction project in US history and will help boost the domestic economy and create jobs. It is expected to boost the nation's GDP by $1.3 trillion in 2021, as well as boosting demand for steel.
FAQ
What is the importance of automation in manufacturing?
Not only is automation important for manufacturers, but it's also vital for service providers. They can provide services more quickly and efficiently thanks to automation. It helps them to lower costs by reducing human errors, and improving productivity.
What does it mean to be a manufacturer?
Manufacturing Industries refers to businesses that manufacture products. The people who buy these products are called consumers. These companies employ many processes to achieve this purpose, such as production and distribution, retailing, management and so on. They create goods from raw materials, using machines and various other equipment. This includes all types of manufactured goods, including food items, clothing, building supplies, furniture, toys, electronics, tools, machinery, vehicles, pharmaceuticals, medical devices, chemicals, and many others.
What is production planning?
Production Planning involves developing a plan for all aspects of the production, including scheduling, budgeting, casting, crew, location, equipment, props, etc. This document will ensure everything is in order and ready to go when you need it. It should also contain information on achieving the best results on set. This information includes locations, crew details and equipment requirements.
The first step in filming is to define what you want. You may have already chosen the location you want, or there are locations or sets you prefer. Once you have determined your scenes and locations, it is time to start figuring out the elements that you will need for each scene. One example is if you are unsure of the exact model you want but decide that you require a car. In this case, you could start looking up cars online to find out what models are available and then narrow your choices by choosing between different makes and models.
After you have selected the car you want, you can begin to think about additional features. Are you looking for people to sit in the front seats? Or maybe you just need someone to push the car around. Maybe you want to change the interior color from black to white? These questions will help you determine the exact look and feel of your car. You can also think about the type of shots you want to get. What type of shots will you choose? Perhaps you want to show the engine or the steering wheel? These things will help you to identify the car that you are looking for.
Once you have established all the details, you can create a schedule. You can create a schedule that will outline when you must start and finish your shoots. Each day will include the time when you need to arrive at the location, when you need to leave and when you need to return home. It will help everyone know exactly what they have to do and when. Book extra staff ahead of time if you need them. You should not hire anyone who doesn't show up because of your inaction.
When creating your schedule, you will also need to consider the number of days you need to film. Some projects can be completed in a matter of days or weeks. Others may take several days. You should consider whether you will need more than one shot per week when creating your schedule. Multiple takes of the same location will lead to higher costs and take more time. If you are unsure if you need multiple takes, it is better to err on the side of caution and shoot fewer takes rather than risk wasting money.
Budgeting is another crucial aspect of production plan. You will be able to manage your resources if you have a realistic budget. Remember that you can always reduce the budget later on if you run into unforeseen problems. However, you shouldn't overestimate the amount of money you will spend. Underestimating the cost will result in less money after you have paid for other items.
Production planning is a detailed process. But, once you understand the workings of everything, it becomes easier for future projects to be planned.
What does it mean to warehouse?
Warehouses and storage facilities are where goods are kept before being sold. You can have it indoors or outdoors. In some cases, it may be a combination of both.
Statistics
- It's estimated that 10.8% of the U.S. GDP in 2020 was contributed to manufacturing. (investopedia.com)
- Job #1 is delivering the ordered product according to specifications: color, size, brand, and quantity. (netsuite.com)
- You can multiply the result by 100 to get the total percent of monthly overhead. (investopedia.com)
- (2:04) MTO is a production technique wherein products are customized according to customer specifications, and production only starts after an order is received. (oracle.com)
- [54][55] These are the top 50 countries by the total value of manufacturing output in US dollars for its noted year according to World Bank.[56] (en.wikipedia.org)
External Links
How To
How to Use the Just-In-Time Method in Production
Just-in time (JIT), is a process that reduces costs and increases efficiency in business operations. It is a process where you get the right amount of resources at the right moment when they are needed. This means that you only pay the amount you actually use. Frederick Taylor was the first to coin this term. He developed it while working as a foreman during the early 1900s. He noticed that workers were often paid overtime when they had to work late. He realized that workers should have enough time to complete their jobs before they begin work. This would help increase productivity.
JIT teaches you to plan ahead and prepare everything so you don’t waste time. You should also look at the entire project from start to finish and make sure that you have sufficient resources available to deal with any problems that arise during the course of your project. You will have the resources and people to solve any problems you anticipate. This will prevent you from spending extra money on unnecessary things.
There are many types of JIT methods.
-
Demand-driven: This is a type of JIT where you order the parts/materials needed for your project regularly. This will enable you to keep track of how much material is left after you use it. This will let you know how long it will be to produce more.
-
Inventory-based: This type allows you to stock the materials needed for your projects ahead of time. This allows you predict the amount you can expect to sell.
-
Project-driven: This is an approach where you set aside enough funds to cover the cost of your project. If you know the amount you require, you can buy the materials you need.
-
Resource-based JIT: This type of JIT is most commonly used. You allocate resources based on the demand. If you have many orders, you will assign more people to manage them. If you don't receive many orders, then you'll assign fewer employees to handle the load.
-
Cost-based: This is a similar approach to resource-based but you are not only concerned with how many people you have, but also how much each one costs.
-
Price-based: This approach is very similar to the cost-based method except that you don't look at individual workers costs but the total cost of the company.
-
Material-based - This is a variant of cost-based. But instead of looking at the total company cost, you focus on how much raw material you spend per year.
-
Time-based: This is another variation of resource-based JIT. Instead of worrying about how much each worker costs, you can focus on how long the project takes.
-
Quality-based JIT is another variant of resource-based JIT. Instead of worrying about the costs of each employee or how long it takes for something to be made, you should think about how quality your product is.
-
Value-based JIT: This is the latest form of JIT. In this instance, you are not concerned about the product's performance or meeting customer expectations. Instead, you're focused on how much value you add to the market.
-
Stock-based. This method is inventory-based and focuses only on the actual production at any given point. This method is useful when you want to increase production while decreasing inventory.
-
Just-in-time planning (JIT): This is a combination JIT and supply-chain management. It's the process of scheduling delivery of components immediately after they are ordered. It reduces lead times and improves throughput.