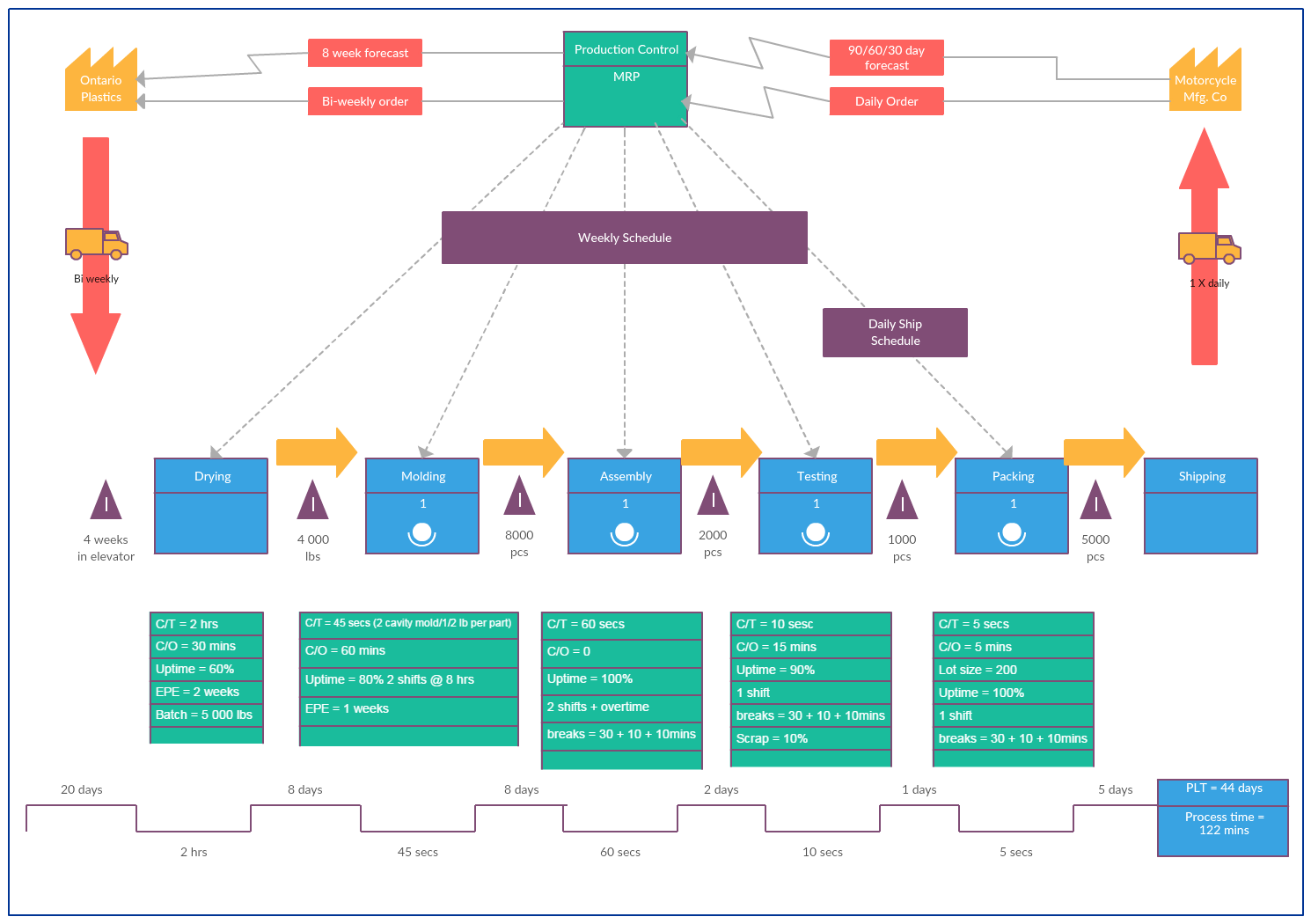
Despite the many benefits of lean manufacturing, there have been some challenges for companies trying to implement this strategy. Companies should develop a comprehensive plan that addresses these issues. Companies that have implemented Lean have found that there are three main issues that are responsible for limiting the success of the initiative.
Whatever the company's size, it is essential that they are committed to lean manufacturing. While there is no hard and fast rule to determine how committed a company is to the implementation of lean, it is important that management acquaints staff with the changes in the corporate culture.
Also, it is important to make sure that resources are properly allocated. Many public organisations have reported that they waste allocated budgets by purchasing unnecessary items. According to some reports, managers also purchase equipment that's not necessary in order to maximize their budget. This can cause operational bottlenecks that lead to inefficient lean manufacturing.
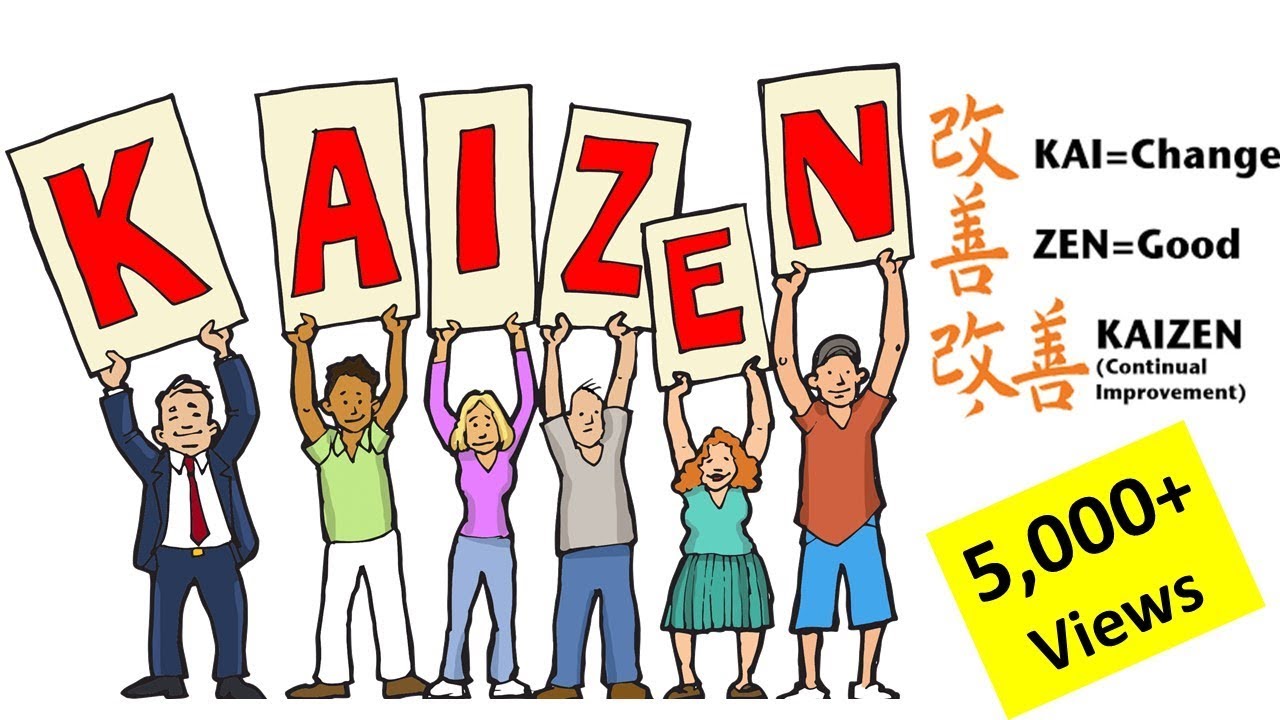
Resistance to cultural changes is one of the biggest obstacles in lean manufacturing. Employees, especially those who have worked for the company for many years, aren’t used to change. Some employees will wait for the majority to speak up and convince them to move in a new direction. To break down resistance, managers must clearly communicate the benefits and justify the need for change.
A lack of a strategy for transformation is another major problem. While companies usually transform several business operations at once, it is important to maintain a long-term strategy. Companies can use this strategy to mentor and identify future leaders, improve their operations, and ensure that they remain competitive in the face technological advances. It helps identify operational bottlenecks and addresses growth opportunities.
To overcome resistance, it is important to have training. Training is essential to help workers understand their roles and expectations. The training also helps workers to develop multi-skills, which can be used to do more work independently. Workers also learn problem solving skills through training, which can help them maintain Lean through performance improvements.
To overcome resistance, management needs to engage with workers frequently. Managers can use pressure to get workers comply with their instructions, but managers must also take the time to explain why they are changing. Managers have been accused of giving incorrect instructions to employees, leading sometimes to ineffective implementation.
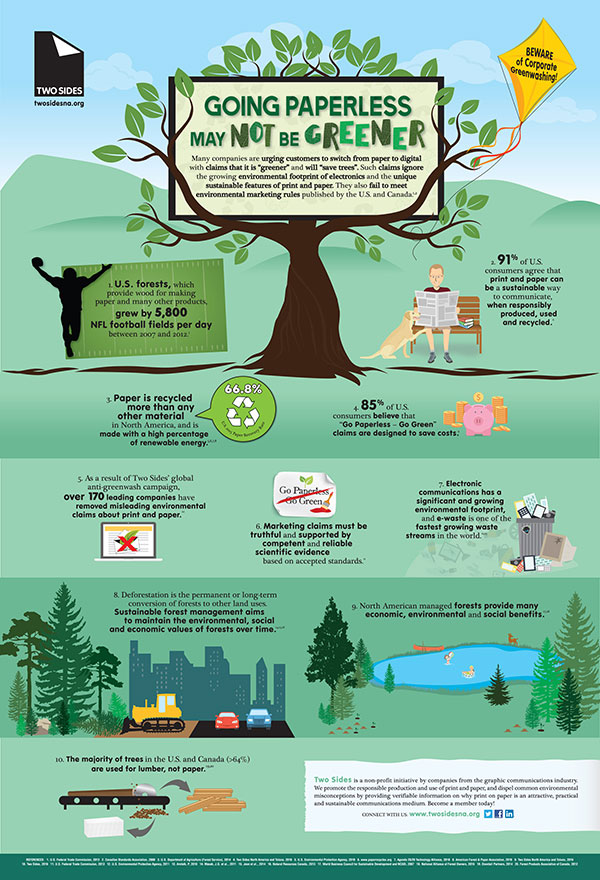
No matter the company's size, managers need to be present on the shop floor in order to identify areas that can be improved. Managers must also develop training modules and familiarize staff with new digital tools. These tools, such 5S, can improve visual management.
It is crucial to communicate and develop a clear vision of how lean manufacturing will be implemented. This vision should outline the responsibilities of employees and include a schedule to implement lean. It also includes a method for measuring success.
FAQ
What does it take for a logistics enterprise to succeed?
To run a successful logistics company, you need a lot knowledge and skills. Good communication skills are essential to effectively communicate with your suppliers and clients. You will need to know how to interpret data and draw conclusions. You must be able manage stress and pressure under pressure. To improve efficiency, you must be innovative and creative. Strong leadership qualities are essential to motivate your team and help them achieve their organizational goals.
You must be organized to meet tight deadlines.
How can manufacturing overproduction be reduced?
In order to reduce excess production, you need to develop better inventory management methods. This would reduce time spent on activities such as purchasing, stocking, and maintaining excess stock. This will allow us to free up resources for more productive tasks.
You can do this by adopting a Kanban method. A Kanban board is a visual display used to track work in progress. A Kanban system allows work items to move through several states before reaching their final destination. Each state is assigned a different priority.
When work is completed, it can be transferred to the next stage. But if a task remains in the beginning stages it will stay that way until it reaches its end.
This allows you to keep work moving along while making sure that no work gets neglected. Managers can view the Kanban board to see how much work they have done. This data allows them adjust their workflow based upon real-time data.
Lean manufacturing is another way to manage inventory levels. Lean manufacturing is about eliminating waste from all stages of the production process. Anything that doesn't add value to the product is considered waste. There are several types of waste that you might encounter:
-
Overproduction
-
Inventory
-
Unnecessary packaging
-
Exceed materials
Manufacturers can increase efficiency and decrease costs by implementing these ideas.
What are the responsibilities of a logistic manager?
A logistics manager ensures that all goods are delivered on time and without damage. This is done using his/her knowledge of the company's products. He/she should also ensure enough stock is available to meet demand.
What are the goods of logistics?
Logistics are the activities involved in moving goods from point A to point B.
They encompass all aspects transport, including packaging and loading, transporting, storage, unloading.
Logisticians ensure that the right product reaches the right place at the right time and under safe conditions. They assist companies with their supply chain efficiency through information on demand forecasts. Stock levels, production times, and availability.
They also keep track of shipments in transit, monitor quality standards, perform inventories and order replenishment, coordinate with suppliers and vendors, and provide support services for sales and marketing.
What are manufacturing and logistics?
Manufacturing refers to the process of making goods using raw materials and machines. Logistics manages all aspects of the supply chain, including procurement, production planning and distribution, inventory control, transportation, customer service, and transport. Manufacturing and logistics can often be grouped together to describe a larger term that covers both the creation of products, and the delivery of them to customers.
Statistics
- (2:04) MTO is a production technique wherein products are customized according to customer specifications, and production only starts after an order is received. (oracle.com)
- According to a Statista study, U.S. businesses spent $1.63 trillion on logistics in 2019, moving goods from origin to end user through various supply chain network segments. (netsuite.com)
- You can multiply the result by 100 to get the total percent of monthly overhead. (investopedia.com)
- In 2021, an estimated 12.1 million Americans work in the manufacturing sector.6 (investopedia.com)
- In the United States, for example, manufacturing makes up 15% of the economic output. (twi-global.com)
External Links
How To
How to Use the 5S to Increase Productivity In Manufacturing
5S stands for "Sort", "Set In Order", "Standardize", "Separate" and "Store". The 5S methodology was developed at Toyota Motor Corporation in 1954. It improves the work environment and helps companies to achieve greater efficiency.
The idea behind standardizing production processes is to make them repeatable and measurable. It means tasks like cleaning, sorting or packing, labeling, and storing are done every day. Because workers know what they can expect, this helps them perform their jobs more efficiently.
There are five steps that you need to follow in order to implement 5S. Each step requires a different action, which increases efficiency. By sorting, for example, you make it easy to find the items later. When you set items in an order, you put items together. Once you have separated your inventory into groups and organized them, you will store these groups in easily accessible containers. Labeling your containers will ensure that everything is correctly labeled.
This requires employees to critically evaluate how they work. Employees must be able to see why they do what they do and find a way to achieve them without having to rely on their old methods. To implement the 5S system, employees must acquire new skills and techniques.
The 5S method not only increases efficiency but also boosts morale and teamwork. They are more motivated to achieve higher efficiency levels as they start to see improvement.