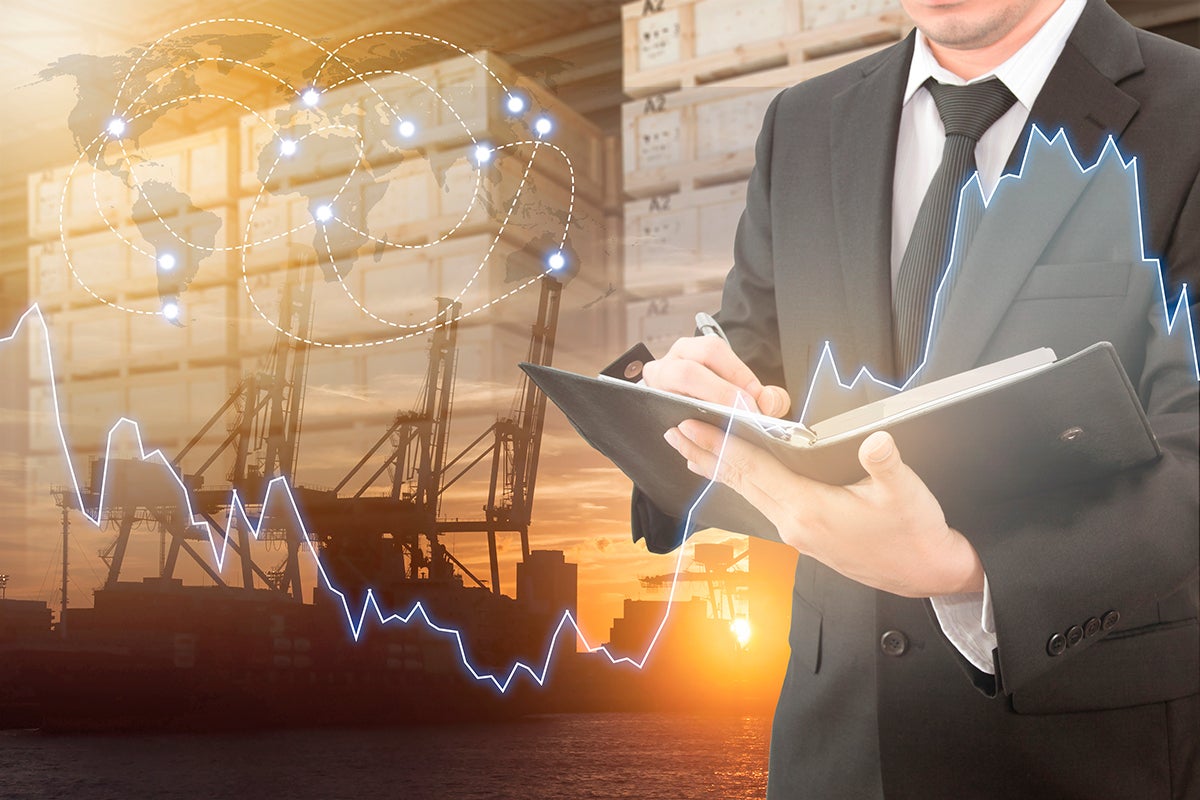
Integrated supply chain management can be described as a process that allows a company monitor and optimize its supply chain performance. This creates a responsive, streamlined production network. Your supply chain will be more efficient the more it is streamlined and responsive. Integrated supply chain management will increase profits and reduce waste. This allows you to produce products that are better quality, reliable, and cheaper.
Integrated supply chain management can increase the reliability and predictability of your orders. Your production schedule and inventory levels will be better managed, which will allow you to be more responsive. Also, your delivery schedule will work more efficiently. Integrated supply chains are also better at managing risk. It can also lower greenhouse gases emissions. This helps you to meet environmental goals.
First, you need to create a contract for integration with your vendors. These agreements must be tailored to the needs of your company. It should include information about your production schedule, the materials you require, and the costs involved. It should also include information about your production schedule, the materials you require, and how they will benefit your company. Purchasing a larger volume of goods or services can also lead to cheaper prices.
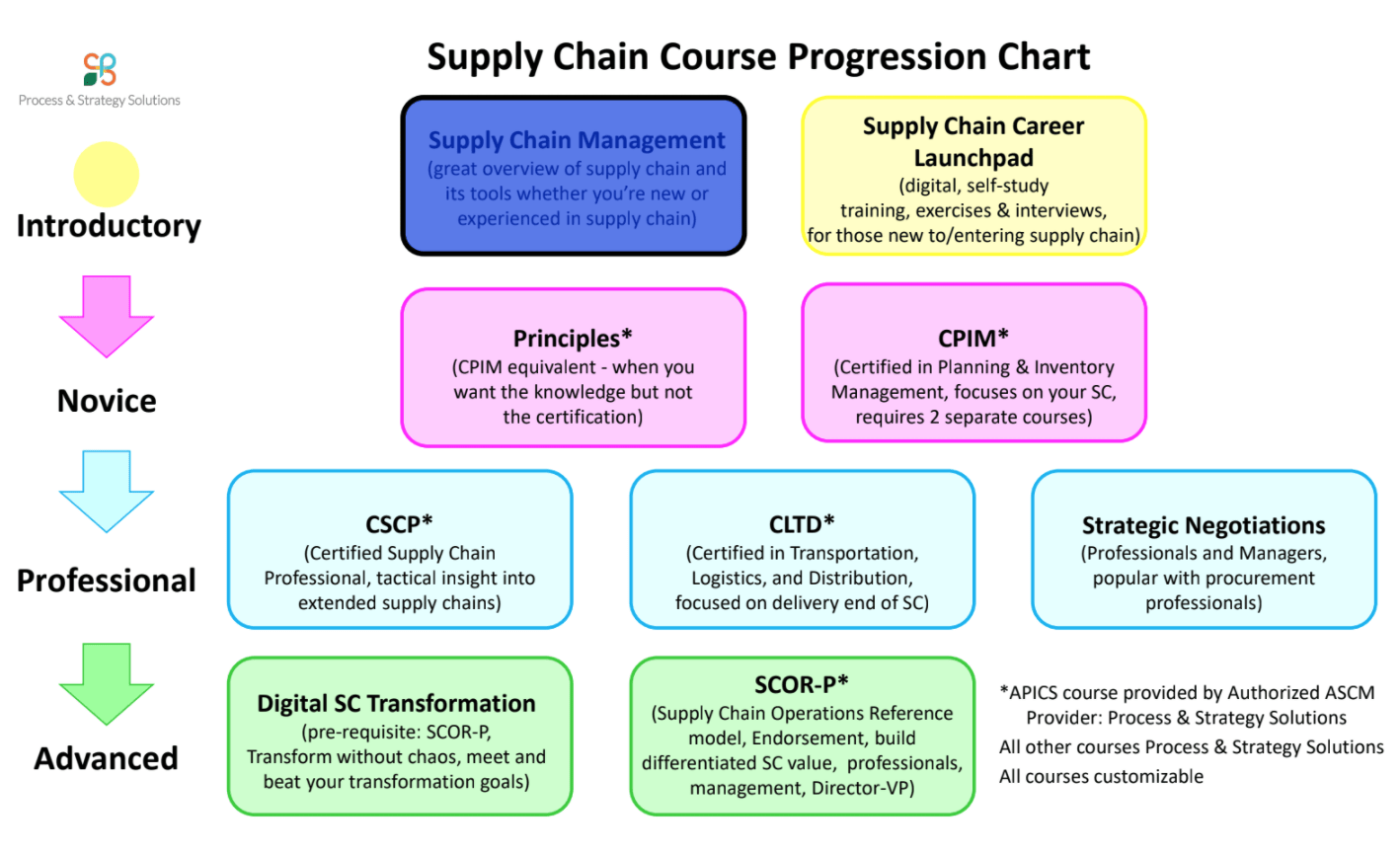
A solid understanding of your relationships and how they impact your business is an essential component of integrated supply chain management. This helps to identify any opportunities for improved performance and avoid mistakes. Also, you need a complete end-to–end plan in place to meet all of your needs. It should be flexible enough that it can accommodate production changes. This will avoid any delays.
Just-in time distribution is an example of an integrated supply system. This strategy lowers warehouse space and operational costs. This strategy can also be used to forecast accurately. It is essential to use an integrated supply network in order to reduce greenhouse gas emissions. This can be achieved by reducing the use of large fixed assets.
Vertical integration is when you have all the necessary elements for a specific product. This includes a manufacturer and vendor. This could result in a higher share of profits for the manufacturer. A widget manufacturer or firm that produces widgets might be a good option. This will allow you to take control of your competitors' businesses and ensure you get a fair price for widgets.
Another example is a container management plan. This allows for you to monitor inventory levels and make adjustments as necessary to your container pulling strategies. You can also make changes to the production schedule right away.
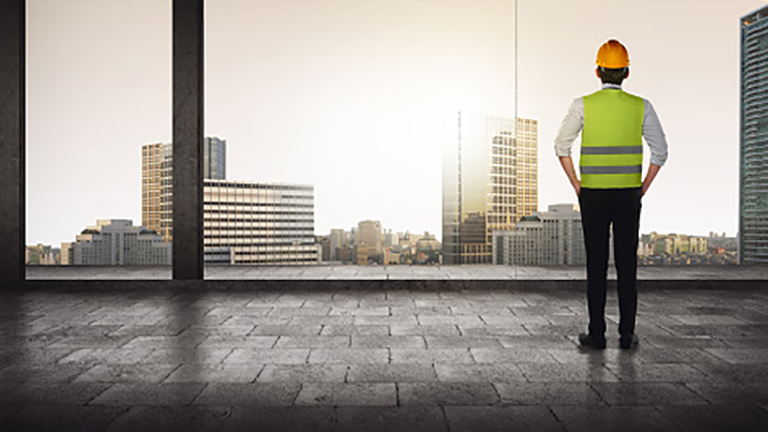
A supply chain management strategy that is clearly defined will make it more effective. The main objective of an integrated supply chain is to optimize performance and provide the best possible products for your customers. You can reduce plastic waste by using an integrated supply network. This can improve your profit margins as well as reduce greenhouse gas emissions.
FAQ
What skills does a production planner need?
Being a production planner is not easy. You need to be organized and flexible. It is also important to be able communicate with colleagues and clients.
What does it mean to be a manufacturer?
Manufacturing Industries are companies that manufacture products. The people who buy these products are called consumers. To accomplish this goal, these companies employ a range of processes including distribution, sales, management, and production. They produce goods from raw materials by using machines and other machinery. This covers all types of manufactured goods including clothing, food, building supplies and furniture, as well as electronics, tools, machinery, vehicles and pharmaceuticals.
What are the responsibilities of a logistic manager?
A logistics manager makes sure that all goods are delivered on-time and in good condition. This is done through his/her expertise and knowledge about the company's product range. He/she should make sure that enough stock is on hand to meet the demands.
Statistics
- In the United States, for example, manufacturing makes up 15% of the economic output. (twi-global.com)
- (2:04) MTO is a production technique wherein products are customized according to customer specifications, and production only starts after an order is received. (oracle.com)
- According to a Statista study, U.S. businesses spent $1.63 trillion on logistics in 2019, moving goods from origin to end user through various supply chain network segments. (netsuite.com)
- You can multiply the result by 100 to get the total percent of monthly overhead. (investopedia.com)
- Job #1 is delivering the ordered product according to specifications: color, size, brand, and quantity. (netsuite.com)
External Links
How To
How to use lean manufacturing in the production of goods
Lean manufacturing (or lean manufacturing) is a style of management that aims to increase efficiency, reduce waste and improve performance through continuous improvement. It was developed by Taiichi Okono in Japan, during the 1970s & 1980s. TPS founder Kanji Takoda awarded him the Toyota Production System Award (TPS). The first book published on lean manufacturing was titled "The Machine That Changed the World" written by Michael L. Watkins and published in 1990.
Lean manufacturing is often described as a set if principles that help improve the quality and speed of products and services. It is about eliminating defects and waste from all stages of the value stream. Lean manufacturing can be described as just-in–time (JIT), total productive maintenance, zero defect (TPM), or even 5S. Lean manufacturing focuses on eliminating non-value-added activities such as rework, inspection, and waiting.
Lean manufacturing can help companies improve their product quality and reduce costs. Additionally, it helps them achieve their goals more quickly and reduces employee turnover. Lean manufacturing is a great way to manage the entire value chain including customers, suppliers, distributors and retailers as well as employees. Lean manufacturing can be found in many industries. Toyota's philosophy, for example, is what has enabled it to be successful in electronics, automobiles, medical devices, healthcare and chemical engineering as well as paper and food.
Lean manufacturing is based on five principles:
-
Define value - Find out what your business contributes to society, and what makes it different from other competitors.
-
Reduce Waste - Eliminate any activity that doesn't add value along the supply chain.
-
Create Flow. Ensure that your work is uninterrupted and flows seamlessly.
-
Standardize & Simplify - Make processes as consistent and repeatable as possible.
-
Develop Relationships: Establish personal relationships both with internal and external stakeholders.
Although lean manufacturing has always been around, it is gaining popularity in recent years because of a renewed interest for the economy after 2008's global financial crisis. Many companies have adopted lean manufacturing methods to increase their marketability. According to some economists, lean manufacturing could be a significant factor in the economic recovery.
Lean manufacturing is now becoming a common practice in the automotive industry, with many benefits. These include higher customer satisfaction levels, reduced inventory levels as well as lower operating costs.
Any aspect of an enterprise can benefit from Lean manufacturing. This is because it ensures efficiency and effectiveness in all stages of the value chain.
There are three main types in lean manufacturing
-
Just-in Time Manufacturing (JIT), also known as "pull system": This form of lean manufacturing is often referred to simply as "pull". JIT stands for a system where components are assembled on the spot rather than being made in advance. This strategy aims to decrease lead times, increase availability of parts and reduce inventory.
-
Zero Defects Manufacturing: ZDM ensures that no defective units leave the manufacturing plant. You should repair any part that needs to be repaired during an assembly line. This applies to finished products, which may need minor repairs before they are shipped.
-
Continuous Improvement (CI), also known as Continuous Improvement, aims at improving the efficiency of operations through continuous identification and improvement to minimize or eliminate waste. Continuous Improvement involves continuous improvement of processes.