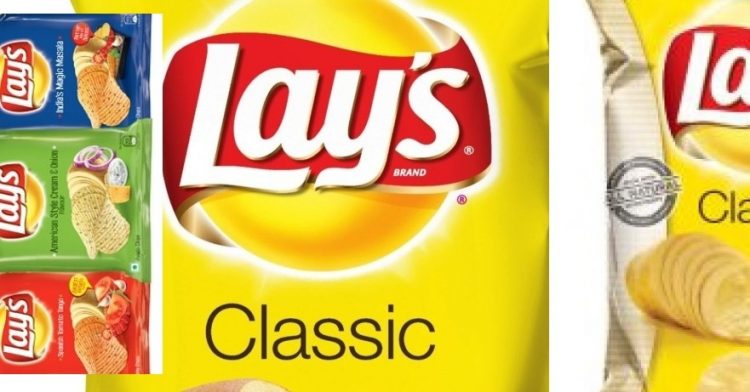
Many skills are needed to work in railway logistics. Some jobs are very easy to learn while others require extensive classroom training and years of experience. These types of jobs require a high degree of computer proficiency and product knowledge. Other jobs may require considerable overseas travel.
Transport logistics specialists are experts in coordinating and managing the movement of people or materials. The specialist may assess the efficiency of the process and find solutions to specific problems. This might include performing a mechanical inspection or determining the best route for a particular cargo.
Rail logistics managers are responsible for ensuring trains and other transport vehicles run on schedule and are properly equipped. They must also ensure that trains follow safety rules and regulations. This job involves delivering freight and moving from one place or another. However, this is only a small part of the job.
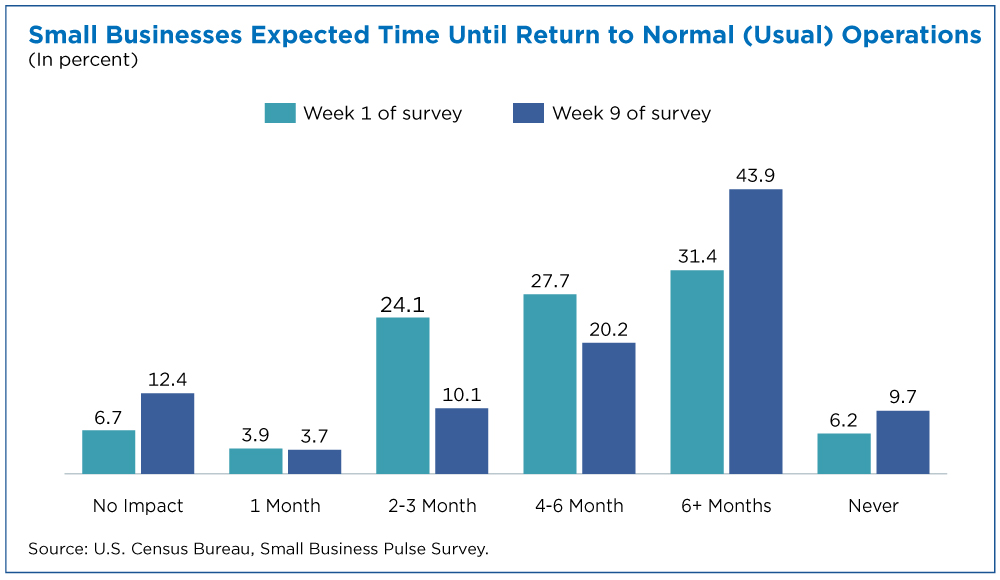
Intermodal dispatcher is another entry level job in the industry. This person coordinates the schedules of several drivers and a shipping firm. This person communicates with the shipping company to notify them of any changes in routes and assigns the shipments to drivers. It is not unusual for administrative duties to be included in this position.
A railway logistics manager may also choose to work in a private firm or a government agency. These roles pay well and offer opportunities for career growth. Generally speaking, you can expect to earn about $45,000 per year. These jobs don't require a bachelor’s degree. Despite the high wages, the average rail salary remains quite low.
Typical logistics titles include logistics manager, logistics analyst and logistics coordinator. These are all crucial positions in the field. Each of these positions has its own merits. However there are good chances that you'll be more successful in one role than the other.
Logistics managers must be able and willing to negotiate the best rates or terms for their clients' transportation needs. This involves analyzing the availability of equipment and services, negotiating with other parties, and analyzing service levels. A basic understanding of transportation management principles is required to help improve the efficiency of a company's logistics process.
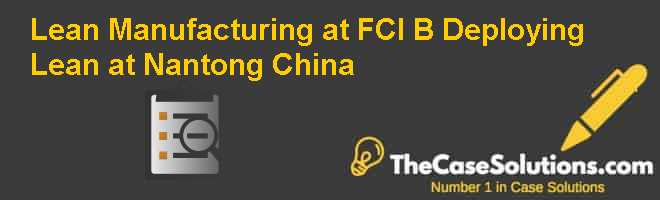
A rail logistics manager could also oversee the implementation and maintenance of a tracking system that tracks shipments and ensures timely delivery. A tracking system will often alert customers to the exact location of a shipment.
Rail logistics managers may be asked to advise how to maximize efficiency in the transportation process. This will enable them to achieve faster results for their clients.
Many of these positions can be learned by doing on-the-job training and experience. For example, a rail logistics coordinator requires a bachelor's degree along with years of experience in a related field.
FAQ
Why is logistics important for manufacturing?
Logistics are an essential part of any business. They help you achieve great results by helping you manage all aspects of product flow, from raw materials to finished goods.
Logistics also play a major role in reducing costs and increasing efficiency.
What are my options for learning more about manufacturing
You can learn the most about manufacturing by getting involved in it. You can also read educational videos or take classes if this isn't possible.
How can manufacturing overproduction be reduced?
The key to reducing overproduction lies in developing better ways to manage inventory. This would reduce the amount of time spent on unnecessary activities such as purchasing, storing, and maintaining excess stock. By doing this, we could free up resources for other productive tasks.
This can be done by using a Kanban system. A Kanbanboard is a visual tool that allows you to keep track of the work being done. In a Kanban system, work items move through a sequence of states until they reach their final destination. Each state represents an individual priority level.
As an example, if work is progressing from one stage of the process to another, then the current task is complete and can be transferred to the next. A task that is still in the initial stages of a process will be considered complete until it moves on to the next stage.
This allows work to move forward and ensures that no work is missed. With a Kanban board, managers can see exactly how much work is being done at any given moment. This information allows managers to adjust their workflow based off real-time data.
Lean manufacturing is another option to control inventory levels. Lean manufacturing is about eliminating waste from all stages of the production process. Anything that does not contribute to the product's value is considered waste. These are some of the most common types.
-
Overproduction
-
Inventory
-
Unnecessary packaging
-
Exceed materials
Manufacturers can reduce their costs and improve their efficiency by using these ideas.
Statistics
- Many factories witnessed a 30% increase in output due to the shift to electric motors. (en.wikipedia.org)
- (2:04) MTO is a production technique wherein products are customized according to customer specifications, and production only starts after an order is received. (oracle.com)
- It's estimated that 10.8% of the U.S. GDP in 2020 was contributed to manufacturing. (investopedia.com)
- In 2021, an estimated 12.1 million Americans work in the manufacturing sector.6 (investopedia.com)
- According to a Statista study, U.S. businesses spent $1.63 trillion on logistics in 2019, moving goods from origin to end user through various supply chain network segments. (netsuite.com)
External Links
How To
How to Use Lean Manufacturing in the Production of Goods
Lean manufacturing is a management style that aims to increase efficiency and reduce waste through continuous improvement. It was first developed in Japan in the 1970s/80s by Taiichi Ahno, who was awarded the Toyota Production System (TPS), award from KanjiToyoda, the founder of TPS. Michael L. Watkins published the original book on lean manufacturing, "The Machine That Changed the World," in 1990.
Lean manufacturing is often defined as a set of principles used to improve the quality, speed, and cost of products and services. It emphasizes eliminating waste and defects throughout the value stream. Lean manufacturing is also known as just in time (JIT), zero defect total productive maintenance(TPM), and five-star (S). Lean manufacturing emphasizes reducing non-value-added activities like inspection, rework and waiting.
Lean manufacturing is a way for companies to achieve their goals faster, improve product quality, and lower costs. Lean Manufacturing is one of the most efficient ways to manage the entire value chains, including suppliers and customers as well distributors and retailers. Lean manufacturing is widely used in many industries. Toyota's philosophy has been a key driver of success in many industries, including automobiles and electronics.
Five fundamental principles underlie lean manufacturing.
-
Define Value: Identify the social value of your business and what sets you apart.
-
Reduce waste - Get rid of any activity that does not add value to the supply chain.
-
Create Flow – Ensure that work flows smoothly throughout the process.
-
Standardize and simplify – Make processes as repeatable and consistent as possible.
-
Develop Relationships: Establish personal relationships both with internal and external stakeholders.
Lean manufacturing isn’t new, but it has seen a renewed interest since 2008 due to the global financial crisis. Many businesses are now using lean manufacturing to improve their competitiveness. Some economists even believe that lean manufacturing can be a key factor in economic recovery.
Lean manufacturing, which has many benefits, is now a standard practice in the automotive industry. These benefits include increased customer satisfaction, reduced inventory levels and lower operating costs.
The principles of lean manufacturing can be applied in almost any area of an organization. It is especially useful for the production aspect of an organization, as it ensures that every step in the value chain is efficient and effective.
There are three types principally of lean manufacturing:
-
Just-in Time Manufacturing: This lean manufacturing method is commonly called "pull systems." JIT is a process in which components can be assembled at the point they are needed, instead of being made ahead of time. This method reduces lead times, increases availability, and decreases inventory.
-
Zero Defects Manufacturing: ZDM ensures that no defective units leave the manufacturing plant. You should repair any part that needs to be repaired during an assembly line. This applies to finished products, which may need minor repairs before they are shipped.
-
Continuous Improvement (CI),: Continuous improvement aims improve the efficiency and effectiveness of operations by continuously identifying issues and making changes to reduce waste. Continuous improvement refers to continuous improvement of processes as well people and tools.