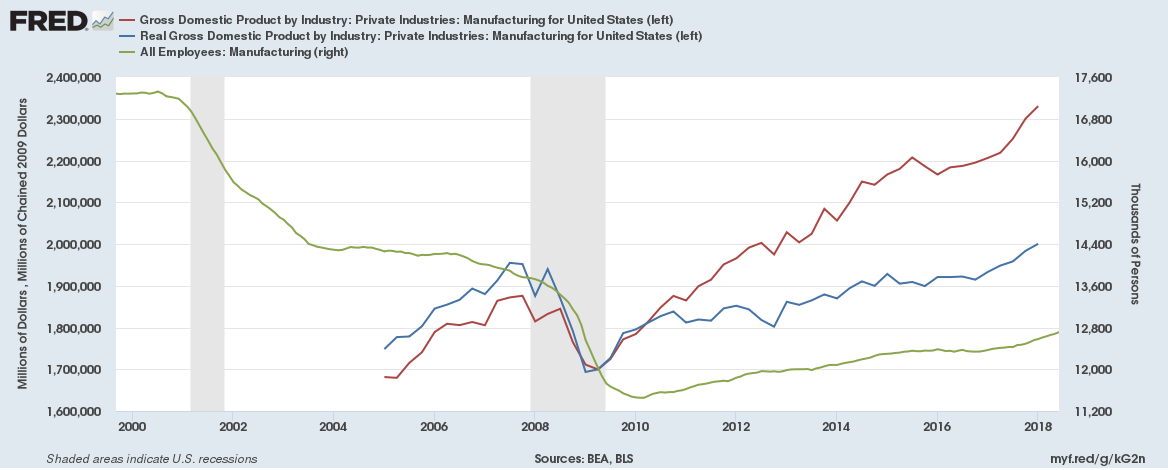
What does an environmental scientist do in mining?
Engineers are vital to the mineral industry because they make it possible for us to collect, refine and transport raw materials. They also design systems which make mining and refining profitable to the companies that mine or sell the material.
How much money does a mine engineer make?
A mining engineer's salary depends on a variety of factors, including the company and position. At the entry level, a mining engineer can earn up to PS22,000 per year, but this can rise to PS50,000 or more with experience. Senior engineers are able to earn PS80,000 per annum or even more.
What subjects is mining engineering concerned with?
To be a mining engineering, you need to have an understanding of several disciplines. These include electrical, mechanical, geological, and civil engineering. They must have the ability to design and operate equipment, manage mining operations, and provide technical support to their fellow engineers.
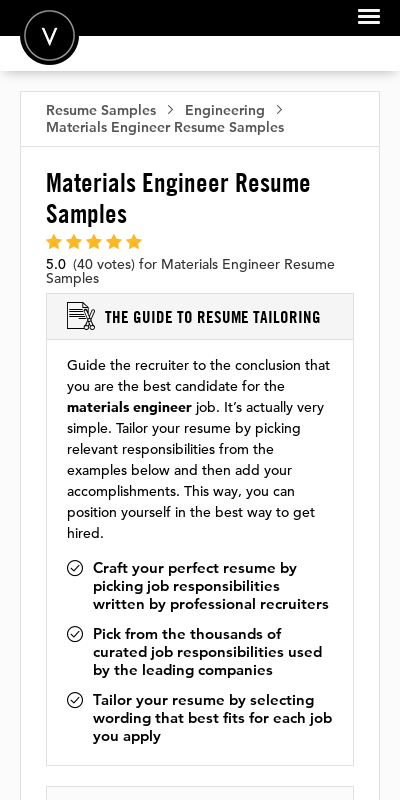
How to get a mining engineer job
The first step in getting a career as a mining engineer is to earn a degree and gain work experience. This will give you the chance to show off your skills and demonstrate to prospective employers that you have the right attitude and qualifications. You can also seek opportunities to do a placement with a mining engineering firm, which will allow you to apply your knowledge in a real-life setting.
How to find mining engineer jobs
There are many mining engineering positions overseas. Some are available in the UK as well, especially at international companies. Many of these positions involve working on site for long periods and travelling to other parts of the world.
How to select a career path as a mining engineers
The career of a mining engineer is a challenging one, but with plenty of opportunity for progression and professional development. You can progress to the position of lead or senior engineers, then move on to take on more managerial and strategic duties.
How to get a mining job?
To become a mining engineers, you need to hold a bachelor's degree and have relevant work experience. Graduates often begin their careers as trainees, learning from professionals and working under a mentor. It is a good way to expand your knowledge and network.
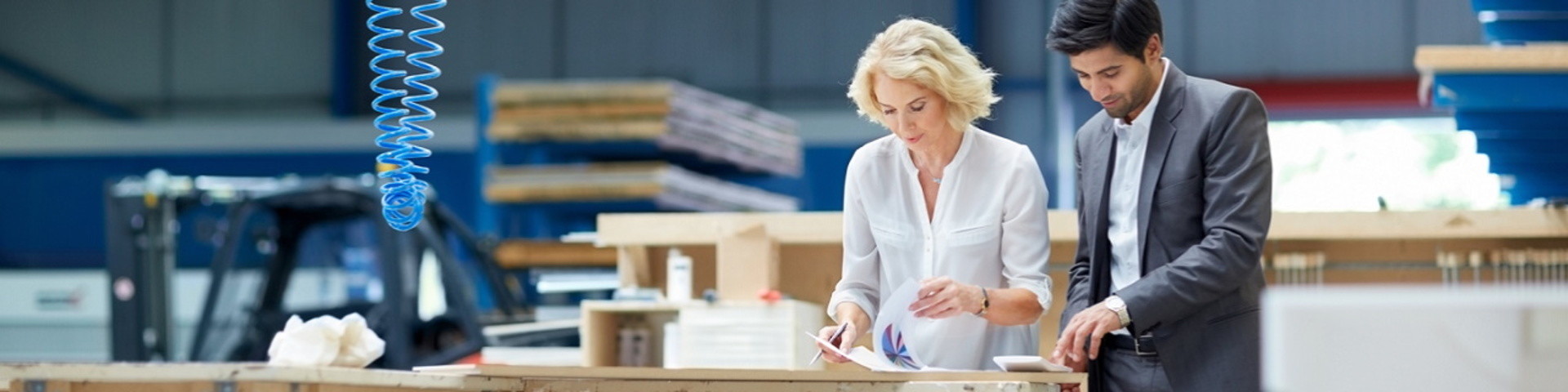
How to get a job as a mining engineering?
These companies are the best places to find jobs in the mining engineering field. You can find vacancies with these firms online, by specialist recruitment agencies and in publications such as targetjobs Engineering, Mining Journal, and InfoMine. You can also search for speculative applications with the Directory of Mines and Quarries produced by the British Geological Survey.
How to get ready for a career as an engineer in the mining industry
You can start a career in mining by earning a bachelor's or master's degree in a geological subject and working towards practical experience in the sector. If you're particularly interested in this subject, you can consider a PhD or a master's program.
FAQ
How does a Production Planner differ from a Project Manager?
The difference between a product planner and project manager is that a planer is typically the one who organizes and plans the entire project. A production planner, however, is mostly involved in the planning stages.
What is the responsibility for a logistics manager
Logistics managers ensure that goods arrive on time and are unharmed. This is done by using his/her experience and knowledge of the company's products. He/she should ensure that sufficient stock is available in order to meet customer demand.
Why is logistics important for manufacturing?
Logistics are an essential component of any business. They help you achieve great results by helping you manage all aspects of product flow, from raw materials to finished goods.
Logistics play a key role in reducing expenses and increasing efficiency.
What are the responsibilities of a manufacturing manager
Manufacturing managers must ensure that manufacturing processes are efficient, effective, and cost-effective. They should be aware of any issues within the company and respond accordingly.
They should also know how to communicate with other departments such as sales and marketing.
They should also be aware of the latest trends in their industry and be able to use this information to help improve productivity and efficiency.
Why automate your warehouse?
Modern warehousing is becoming more automated. Increased demand for efficient and faster delivery has resulted in a rise in e-commerce.
Warehouses need to adapt quickly to meet changing needs. In order to do this, they need to invest in technology. Automating warehouses has many benefits. These are some of the benefits that automation can bring to warehouses:
-
Increases throughput/productivity
-
Reduces errors
-
Improves accuracy
-
Safety is boosted
-
Eliminates bottlenecks
-
This allows companies to scale easily
-
It makes workers more efficient
-
It gives visibility to everything that happens inside the warehouse
-
Enhances customer experience
-
Improves employee satisfaction
-
This reduces downtime while increasing uptime
-
Quality products delivered on time
-
Removing human error
-
Helps ensure compliance with regulations
How can manufacturing excess production be decreased?
The key to reducing overproduction lies in developing better ways to manage inventory. This would decrease the time that is spent on inefficient activities like purchasing, storing, or maintaining excess stock. This will allow us to free up resources for more productive tasks.
A Kanban system is one way to achieve this. A Kanban board can be used to monitor work progress. Kanban systems are where work items travel through a series of states until reaching their final destination. Each state represents a different priority level.
When work is completed, it can be transferred to the next stage. However, if a task is still at the beginning stages, it will remain so until it reaches the end of the process.
This helps to keep work moving forward while ensuring that no work is left behind. Managers can monitor the work being done by Kanban boards to see what is happening at any given time. This information allows managers to adjust their workflow based off real-time data.
Lean manufacturing is another way to manage inventory levels. Lean manufacturing seeks to eliminate waste from every step of the production cycle. Anything that doesn't add value to the product is considered waste. The following are examples of common waste types:
-
Overproduction
-
Inventory
-
Unnecessary packaging
-
Excess materials
Manufacturers can reduce their costs and improve their efficiency by using these ideas.
Statistics
- It's estimated that 10.8% of the U.S. GDP in 2020 was contributed to manufacturing. (investopedia.com)
- In 2021, an estimated 12.1 million Americans work in the manufacturing sector.6 (investopedia.com)
- In the United States, for example, manufacturing makes up 15% of the economic output. (twi-global.com)
- According to the United Nations Industrial Development Organization (UNIDO), China is the top manufacturer worldwide by 2019 output, producing 28.7% of the total global manufacturing output, followed by the United States, Japan, Germany, and India.[52][53] (en.wikipedia.org)
- [54][55] These are the top 50 countries by the total value of manufacturing output in US dollars for its noted year according to World Bank.[56] (en.wikipedia.org)
External Links
How To
How to Use Lean Manufacturing in the Production of Goods
Lean manufacturing (or lean manufacturing) is a style of management that aims to increase efficiency, reduce waste and improve performance through continuous improvement. It was first developed in Japan in the 1970s/80s by Taiichi Ahno, who was awarded the Toyota Production System (TPS), award from KanjiToyoda, the founder of TPS. Michael L. Watkins published the book "The Machine That Changed the World", which was the first to be published about lean manufacturing.
Lean manufacturing can be described as a set or principles that are used to improve quality, speed and cost of products or services. It emphasizes the elimination of defects and waste throughout the value stream. The five-steps of Lean Manufacturing are just-in time (JIT), zero defect and total productive maintenance (TPM), as well as 5S. Lean manufacturing focuses on eliminating non-value-added activities such as rework, inspection, and waiting.
Lean manufacturing improves product quality and costs. It also helps companies reach their goals quicker and decreases employee turnover. Lean manufacturing can be used to manage all aspects of the value chain. Customers, suppliers, distributors, retailers and employees are all included. Many industries worldwide use lean manufacturing. Toyota's philosophy has been a key driver of success in many industries, including automobiles and electronics.
Lean manufacturing is based on five principles:
-
Define Value - Identify the value your business adds to society and what makes you different from competitors.
-
Reduce waste - Get rid of any activity that does not add value to the supply chain.
-
Create Flow - Make sure work runs smoothly without interruptions.
-
Standardize and simplify – Make processes as repeatable and consistent as possible.
-
Building Relationships – Establish personal relationships with both external and internal stakeholders.
Although lean manufacturing isn't a new concept in business, it has gained popularity due to renewed interest in the economy after the 2008 global financial crisis. Many businesses have adopted lean production techniques to make them more competitive. Economists think that lean manufacturing is a crucial factor in economic recovery.
Lean manufacturing is becoming a popular practice in automotive. It has many advantages. These benefits include increased customer satisfaction, reduced inventory levels and lower operating costs.
Any aspect of an enterprise can benefit from Lean manufacturing. Lean manufacturing is most useful in the production sector of an organisation because it ensures that each step in the value-chain is efficient and productive.
There are three types principally of lean manufacturing:
-
Just-in Time Manufacturing (JIT), also known as "pull system": This form of lean manufacturing is often referred to simply as "pull". JIT is a process in which components can be assembled at the point they are needed, instead of being made ahead of time. This strategy aims to decrease lead times, increase availability of parts and reduce inventory.
-
Zero Defects Manufacturing (ZDM): ZDM focuses on ensuring that no defective units leave the manufacturing facility. If a part needs to be fixed during the assembly line, it should be repaired rather than scrapped. This is true even for finished products that only require minor repairs prior to shipping.
-
Continuous Improvement (CI), also known as Continuous Improvement, aims at improving the efficiency of operations through continuous identification and improvement to minimize or eliminate waste. Continuous Improvement involves continuous improvement of processes.