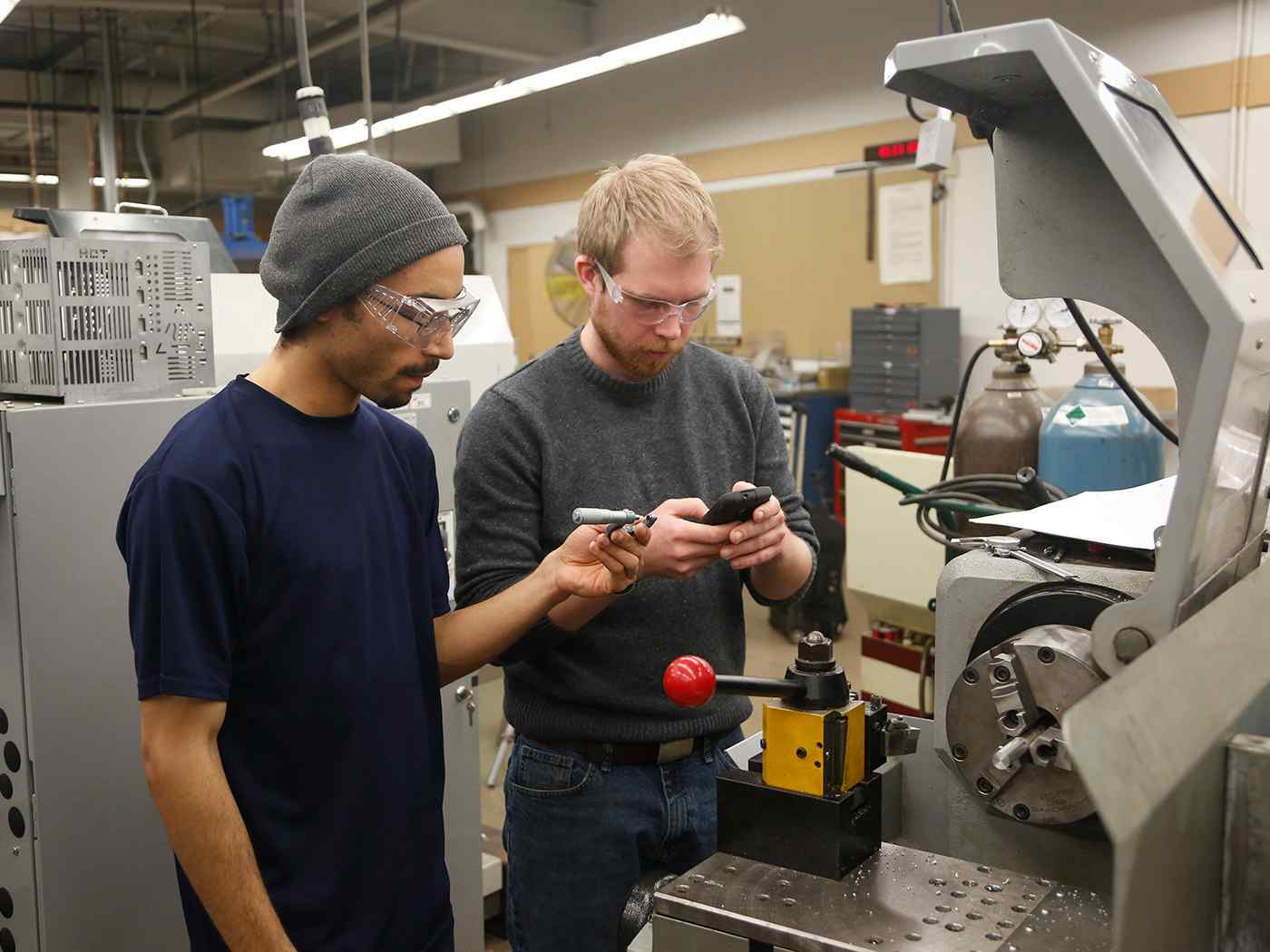
Besides earning a decent salary, train engineers have many other perks to look forward to. Actually, the average salary for a train engineer exceeds what most people make over their lifetime. The demand for railroad transportation positions is expected to rise by around one percent. The salary of a train engineer varies depending on where you live and how many years of experience. After many years in the industry, train engineers can earn well above $100,000 per annum.
Train engineers are not easy jobs. You must first complete federal licensing. Before you can start working on your own, you will need to obtain your federal license. For your certification, you will need to pass a test. This usually includes a vision and eye test. If you pass, your eligibility to work at federal railroads and other transportation agencies will be granted.
It is not uncommon for train engineers to work long hours without a home. You may work weekends or nights. Additionally, your schedule may be irregular, such that you work on holidays or in mornings. You'll also be exposed to different types of weather. Driving electric trains can present a challenge in certain cases.
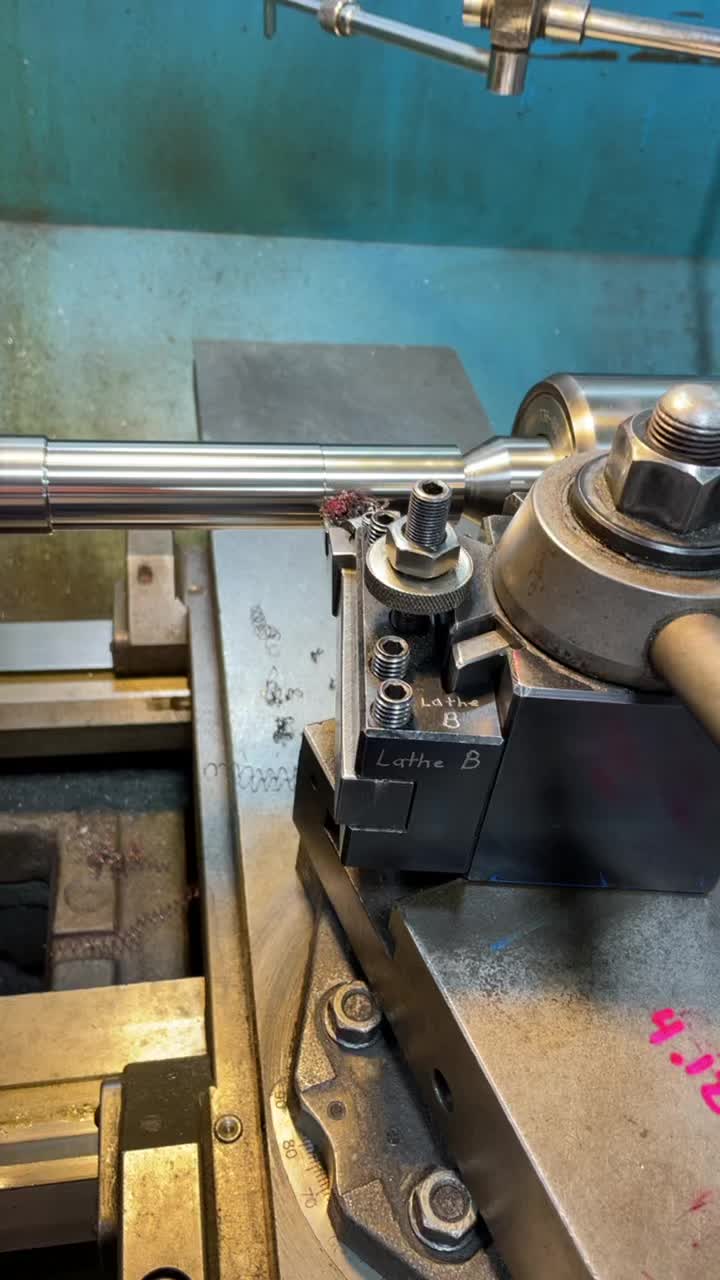
Additionally, you'll need to pass an aptitude test for mechanical engineering. The general requirements for locomotive engineers are to have good vision and hand-eye co-ordination, be able and able to follow a program and operate controls efficiently. In some cases, you may drive freight trains, which may require you to work evenings and nights.
Depending on your location, you may have to work in the dark, or you may have to be on call twenty-four hours a day. It's a great job that can bring in a lot of money, as long as your ability to do the job. These large rail companies pay the best wages for train engineers. They have their own training programs, but if you want to work for a smaller railroad, you can get certified through a trade school.
You'll also need a good high school diploma and a clean criminal record. Although it's not required, having a degree in train engineering can help you get noticed by employers. You can also earn certification through a community college or trade school that will enable you to get a job as train engineer.
Average train engineer salaries are $5,254 per month. It is possible to earn a different salary depending on where you are located, your experience, as well as your employer. For train engineers, most companies pay $75,000 to $80,000 per year. The top earners make up to $186,000 each year. If you're willing to search, you might be able to earn a higher average salary. You'll also want to keep an eye out for job openings.
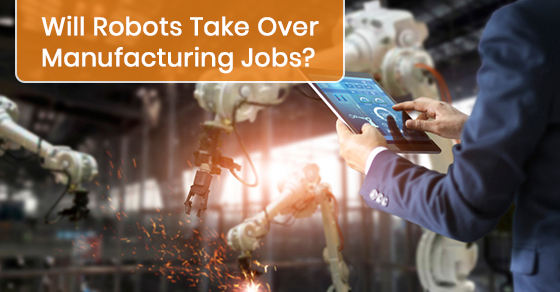
An advanced degree can help you get a better salary. Some locomotive engineers may go on as train trainers or railroad schedulers. Train engineers often find they love their work and will continue it for many years.
FAQ
What is the responsibility of a production planner?
Production planners make sure that every aspect of the project is delivered on-time, within budget, and within schedule. They also ensure that the product/service meets the client’s needs.
How can manufacturing efficiency improved?
First, determine which factors have the greatest impact on production time. The next step is to identify the most important factors that affect production time. You can start by identifying the most important factors that impact production time. Once you've identified them all, find solutions to each one.
What are the goods of logistics?
Logistics refers to all activities that involve moving goods from A to B.
They cover all aspects of transportation, such as packing, loading, transporting and unloading.
Logisticians ensure that the right product reaches the right place at the right time and under safe conditions. They help companies manage their supply chain efficiency by providing information on demand forecasts, stock levels, production schedules, and availability of raw materials.
They can also track shipments in transit and monitor quality standards.
Is automation necessary in manufacturing?
Not only are service providers and manufacturers important, but so is automation. They can provide services more quickly and efficiently thanks to automation. They can also reduce their costs by reducing human error and improving productivity.
Statistics
- Job #1 is delivering the ordered product according to specifications: color, size, brand, and quantity. (netsuite.com)
- Many factories witnessed a 30% increase in output due to the shift to electric motors. (en.wikipedia.org)
- According to a Statista study, U.S. businesses spent $1.63 trillion on logistics in 2019, moving goods from origin to end user through various supply chain network segments. (netsuite.com)
- [54][55] These are the top 50 countries by the total value of manufacturing output in US dollars for its noted year according to World Bank.[56] (en.wikipedia.org)
- It's estimated that 10.8% of the U.S. GDP in 2020 was contributed to manufacturing. (investopedia.com)
External Links
How To
How to use lean manufacturing in the production of goods
Lean manufacturing is an approach to management that aims for efficiency and waste reduction. It was developed in Japan during the 1970s and 1980s by Taiichi Ohno, who received the Toyota Production System (TPS) award from TPS founder Kanji Toyoda. Michael L. Watkins published the first book on lean manufacturing in 1990.
Lean manufacturing refers to a set of principles that improve the quality, speed and costs of products and services. It emphasizes reducing defects and eliminating waste throughout the value chain. Just-in-time (JIT), zero defect (TPM), and 5S are all examples of lean manufacturing. Lean manufacturing is about eliminating activities that do not add value, such as inspection, rework, and waiting.
Lean manufacturing not only improves product quality but also reduces costs. Companies can also achieve their goals faster by reducing employee turnover. Lean manufacturing is a great way to manage the entire value chain including customers, suppliers, distributors and retailers as well as employees. Lean manufacturing practices are widespread in many industries. Toyota's philosophy is a great example of this. It has helped to create success in automobiles as well electronics, appliances and healthcare.
Lean manufacturing includes five basic principles:
-
Define Value - Determine the value that your business brings to society. Also, identify what sets you apart from your competitors.
-
Reduce Waste - Eliminate any activity that doesn't add value along the supply chain.
-
Create Flow - Make sure work runs smoothly without interruptions.
-
Standardize & simplify - Make processes consistent and repeatable.
-
Build relationships - Develop and maintain personal relationships with both your internal and external stakeholders.
Although lean manufacturing has always been around, it is gaining popularity in recent years because of a renewed interest for the economy after 2008's global financial crisis. To increase their competitiveness, many businesses have turned to lean manufacturing. Economists think that lean manufacturing is a crucial factor in economic recovery.
With many benefits, lean manufacturing is becoming more common in the automotive industry. These include improved customer satisfaction, reduced inventory levels, lower operating costs, increased productivity, and better overall safety.
It can be applied to any aspect of an organisation. It is especially useful for the production aspect of an organization, as it ensures that every step in the value chain is efficient and effective.
There are three types of lean manufacturing.
-
Just-in Time Manufacturing, (JIT): This kind of lean manufacturing is also commonly known as "pull-systems." JIT is a process in which components can be assembled at the point they are needed, instead of being made ahead of time. This approach reduces lead time, increases availability and reduces inventory.
-
Zero Defects Manufacturing (ZDM): ZDM focuses on ensuring that no defective units leave the manufacturing facility. It is better to repair a part than have it removed from the production line if it needs to be fixed. This applies to finished goods that may require minor repairs before shipment.
-
Continuous Improvement: Continuous Improvement aims to improve efficiency by continually identifying problems and making adjustments to eliminate or minimize waste. Continuous improvement refers to continuous improvement of processes as well people and tools.